An EXAMPLE Startup of the thickener may occur under two sets of very different circumstances: After a major plant shutdown or the initial plant start-up, when the thickener is completely empty OR/AND After a shutdown whereby the thickener has been left full of pulp, and rakes and underflow pumps have been inoperative (such as after a power failure).

In the case that the thickener is empty, the thickener must be filled with barren solution or water prior to restarting any part of the process. No attempt should be made to put pulp into an empty thickener. The underflow lines must be clean.
- Ensure that the density controller is in MANUAL mode. When the thickener is about half full of solution, raise the rakes slightly, start them, and then lower them to the lowest part of their travel.
- Start the Grinding Circuit. Cyclone overflow will now feed the thickener. Allow the Grinding Circuit to run for at least 6 hours before starting the thickener underflow pumps. This time delay should be sufficient to allow the solids in the thickener to form a bed below the rakes.
- Start the underflow pump and trash screen. Put the underflow on recycle by adjusting the appropriate plug valves located in the recycle box. Set the output of the controller to 10% (pump will run at its minimum speed) .
- Leave the thickener on recycle until the underflow density approaches 60%. Place the setpoint at 60%, and switch the controller to AUTO when the setpoint matches the input. As the pulp approaches 60%, start flocculant flow to the thickener. Care must be taken that not too much flocculant is added or the underflow will become a “jelly-like” mass. Monitor the overflow for solids and base flocculant addition on the increase or decrease in solids.
- Make sure that the clarification circuit is operating downstream from the pregnant tanks.
- Take the thickener out of recycle by opening the plug valves in the recycle box to the leach tanks and closing the recycle plug valve.
If the thickener has been left full of pulp but without operating pumps or rake mechanism, there is a serious danger of sanding, particularly after a number of hours of in operation.
- If the rakes are in the pulp, raise them slowly out of the pulp to their highest position by the manual lifting device.
- Check that all associated equipment is operable, and that the density controller is in MANUAL mode, and that the output is set to 0%.
- Turn the gland seal water to the thickener underflow pump.
- Apply water to the thickener discharge cone by the appropriate water line connections.
- Start the trash screen and adjust recycle box valves for recycling thickener underflow back to the thickener.
- Start the appropriate thickener underflow pump. Set the density controller output to 50% (pump will be running at half speed).
- Once the underflow pump is successfully recirculating slurry, attempt to start the fake drive if high thickener torque has not initiated the stopping of the rakes. If a high torque situation prevails, do not start the rake drive until some of the solids have been removed.
- With the rake mechanism rotating. Lower the rakes slightly and allow rakes to make at least one full revolution. Pay close attention to the torque indicator and lift rakes if torque rises above 40%. Repeat this procedure, lowering the rakes and waiting for one revolution, until the rakes are lowered to their desired operating level without activating the high torque alarm.
- Adjust the recycle box valves to discontinue recycle and begin feed to leach circuit.
Preparation for Thickener Start Up
The following items must be checked before the associated thickening equipment is started.
- The thickener should be running on recycle; ie. underflow pump and trash screen should be running. If they are not, refer to the introductory remarks at the beginning of this section.
- Ensure that all associated equipment is available to operate.
- Check that the Leach Circuit is available to start—up.
- Check the pregnant solution tank level to ensure there is sufficient room for thickener overflow. If the pregnant solution tank is full, the Merrill Crowe Circuit will have to be started prior to the thickener.
- Check that flocculant stock is adequate for a few hours of running time.
- Check shut-off valves in air lines to the sampler are open.
- Ensure that the shut-off valves in the flocculant lines are open.
- Notify the shift foreman that the thickener is ready to receive feed.
A high torque alarm signal must be investigated IMMEDIATELY. Failure to do so may cause severe and costly damage to the thickener rake mechanism and drive components causing a lengthy plant shut down.
Thickener StartUp Sequence and Procedure
- When cyclone overflow material starts to enter the thickener feed launder the flocculant metering pump should be started and the flow rate adjusted, with flowmeter, to the normal rate of 3 cubic meters per hour.
- The thickener should remain on recycle until the underflow density approaches the desired 60% solids. When the density set point is achieved, begin feed to the leach circuit. Monitor the underflow to ensure that the flocculant is not being overdosed, i.e. “jelly-like”.
- Open the shut-off valve in the barren solution line to the trash screen and manually adjust the flow rate to achieve 45% solids in the feed to leach.
- Turn the sampler timer on.
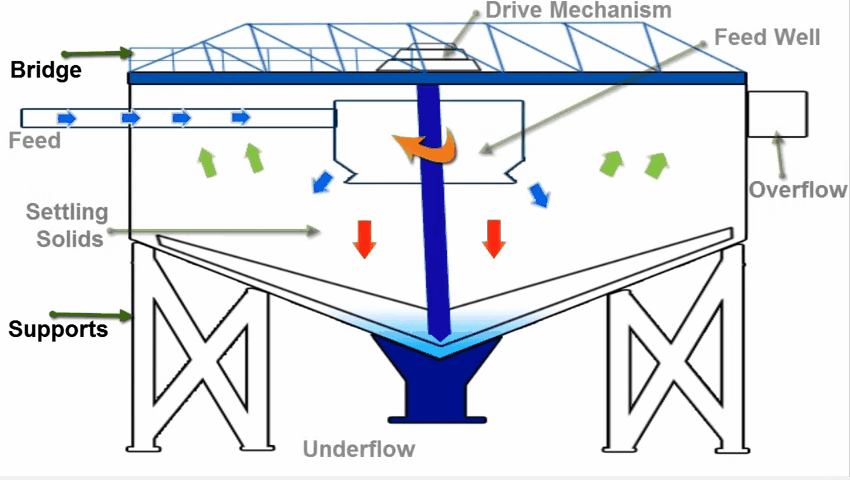
Thickener Normal Operation Procedure
After the thickener has been brought up to normal operating conditions, the operator must monitor the process variables and alarms. The operator is also required to sample and analyse process streams and read local indications.
Flocculant is added to the thickener feed pipe. The operator must adjust the addition rates to give optimum solid settling with minimum flocculant consumption. Flocculant must also be used to give a clear overflow from the thickener.
The thickener should be run to give 60% solids or as high an underflow density as can conventionally be achieved. The thickener underflow density recorder should be monitored frequently. If the thickener is operating smoothly, the recorder monitoring the underflow density should almost be a straight line. The underflow pump speed will automatically change to maintain the set underflow density.
Thickener Normal Shutdown Sequence and Procedure
- When the plant is shut down, the thickener underflow must be put on recycle; leave the underflow pump and trash screen operating.
- Put density controller on MANUAL, and adjust the output (pump speed) to 30% or to that level that will maintain the underflow at a constant pulp density.
- Discontinue flocculant addition to the thickener. Note that the flocculant low flow alarm will sound at the mill control panel.
- Close the barren solution shut-off valve at the trash screen.
- Shut off the sampler timer and close shut-off valve in air line to sampler.
Thickener Emergency Shutdown Procedure
In the event of an emergency, the equipment in the Thickening Circuit can be shut down with locally mounted STOP switches from the MCC located in the mill control room.
Unless absolutely necessary, the thickener rake drive must be left running.
Once the equipment is shut down, close all shut off valves in the reagent, air and solution lines.
https://www.911metallurgist.com/mill-feed-thickener
https://www.911metallurgist.com/how-cyanide-dissolves-gold-and-silver