A little earlier I talked about the rakes of the thickener, these are long arms that extend off of the bottom of the DRIVE SHAFT. As the shaft turns the rakes will sweep the entire bed of the thickener thereby applied Torque. Each rake arm is higher at its far end than it is where it joins the drive shaft. This is designed this way to give the bed a slope towards the centre of the thickener. As the rakes are turned by the drive shaft they cause the concentrate that has settled onto the bottom of the thickener to be pulled into the discharge chamber at the centre of the thickener. This is called the CONE. It is from this cone that the thickener underflow is taken.
During normal operations of the circuit, the thickener may be pulled empty. That doesn’t mean that there isn’t any concentrate left in it. It means that the concentrate hasn’t settled enough to maintain the necessary underflow density required by the filters. When this happens the rest of the De-watering circuit will have to shut down. While the circuit is down there will still be feed coming into the thickener from flotation and the concentrate will still be settling. This means that the rakes will have to be kept turning to evenly distribute the concentrate over thickener bed. To give the circuit the longest possible down time, the drive shaft and rake arms may be lifted to make room for the mineral as it settles.
As the load in the thickener settles to the bed, the Torque on the rake arms will be climbing. Torque is nothing more than a rotary force being applied from the rake arms to the drive shaft. It is the degree of torque that indicates to the operator the load that is in the thickener and when the rake arms have to be lifted. Usually there is a point on the thickener torque indicator where the power to the rakes will be shut off if the torque should happen to become too great.
Whenever the rakes are shut down there is the danger of the rakes being buried in the concentrate as it settles. This very real danger makes the torque and the movement of the rake arms a must for constant supervision. If the rakes do shut themselves down and go unnoticed it could mean that the thickener will have to be drained onto the floor and the concentrate washed away from the rakes until they are free to turn again. This type of occurrence will be very expensive as the entire mill may have to be shut down while the thickener is washed out.
More about thickening ‘this old fashion way’.
This is also the danger that I mentioned earlier of using flocculants. If your thickener “begins to “slime”, (This is the term used to describe the thickener whose contents are not settling fast enough and whose interface is getting closer to the surface) You have three things that you can do about it. Restrict or stop the feed going into it, pull more material from the underflow, or add flocculent. If you add flocculent there is always the danger of adding too much at once. This can start a chain reaction. As the mineral at the surface begins to settle it pushes the material below it down. Sometimes that initial movement is all that is needed to restart the settling process. If this happens the load will settle quickly and all at once. If the operator isn’t on his toes he may end up burying the rakes. The load aided by the flocculent can settle unbelievably fast.
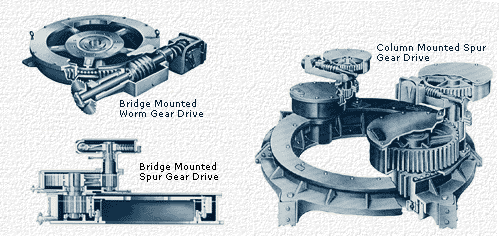
In a plant where sliming thickeners are a problem you may find a device to determine at what depth that the interface is at in the thickener. The best that I have seen is a long glass tube with both ends open. By pushing it into the thickener and then putting your thumb over the open end before you pull it out, you are able to obtain a sample. The glass of the tube allows you to visually measure the distance from the top of the water to where it and the slimes meet.
As to controlling the operation of a thickener the Torque and the density are your control indicators. As you are removing the concentrate from the thickener underflow you will be monitoring the density and the torque. To maintain the density of the underflow, you maintain the torque on the arms. What this means is the density must be controlled within operating guidelines. As the load on the thickener rake mechanism drops off the density will go down. To bring the density back to the operating range you lower the rakes. When the rakes are lowered as far as they will go, and the density has dropped below the operating range, the thickener will be considered empty.