Table of Contents
Gold Leaching done in round vats, constructed of wood, concrete, or iron and steel. If wood is used it is covered by a coating of paraffin paint, or by a mixture of asphaltum and coal-tar. Concrete and brick vats are not now advocated owing to their great cost and less convenient working, and wooden vats suffer more than iron and steel ones from exposure and from being alternately emptied and filled. Iron leaching vats are not usually coated inside, as little if any action goes on between the metal and cyanide solutions; occasionally, however, they are coated with tar inside. The steel vats at the at some plants are 40 feet in diameter and 7 feet deep inside. The sides are of ¼-inch steel plate, and the bottoms are 5/16 inch thick. The plates are rivetted together and strengthened by angle iron at the top and bottom of the vat.
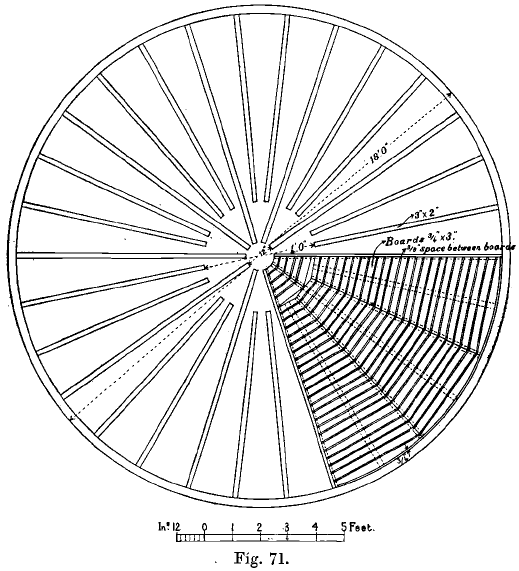
Wooden vats are made of staves, 4 to 6 inches wide and 3 inches or more thick, held together by round iron hoops, with bottom planks 3 inches thick, fitting into a slot in the staves. Sometimes in new mining districts square tanks are built, as being cheaper and more easily constructed, but they do not last long and are more difficult to keep tight.
The dimensions of vats vary with the work to be done. In calculating the capacity of a leaching vat, the volume of a ton of raw ore may be taken at from 22 to 28 cubic feet when dry, and from 20 to 26 cubic feet when wetted down. Tailings sometimes occupy 30 cubic feet per ton or even more. Among
very large vats may be mentioned those at the Simmer and Jack Works, in the Transvaal, which are 40 feet in diameter with 14-foot staves, holding 600 tons of ore each. If the material to be treated is such that percolation is difficult, the depth of the vat is kept small, and the diameter made as large as possible.
In the direct treatment of dry-crushed ores this is usually necessary, as they always contain some slimes. A depth of 2 or 3 feet of dry-crushed ore is usually as much as can be conveniently leached, and vacuum pumps are often added to expedite the work.
The vacuum may be obtained by a direct-acting pump, or by the use of a large boiler, in which a vacuum is created by a Westinghouse or other pump. This is, perhaps, the most advantageous course. As soon as the pressure in the boiler falls to about half an atmosphere, it is connected with the aperture of the vat below the filter-bed. The rate of leaching is often doubled by the diminution of the pressure, below the filter-bed, to half an atmosphere, and in some cases it is increased from ½ or 1 inch to 7 or 8 inches of liquid (in the leaching vat) per hour.
The false bottom is usually a wooden framework, constructed of boards pierced with numerous auger holes, or in larger vats of wooden slats crossing each other. The framework is covered by cotton twill, canvas, or cocoa-nut matting, which are not rapidly destroyed by the solution as they are in the chlorination process. Fig. 71 shows a filter bottom for wooden vats used in Colorado. It is from a working drawing kindly supplied by Mr. W. F. Tindall. Thick canvas duck, resting on matting, forms a trustworthy filter-cloth. The filter-cloth is protected by wooden slats which prevent it from being injured by workmen’s shovels in clearing out the charge.
An iron pipe communicates with the space below the false bottom, and conveys the liquid to the pumps or to the zinc boxes. The solution does not attack wood or iron; brass and bronzes are attacked and corroded rapidly.
Leaching Gold in Vat
The crushed ore is conveyed in cars pushed by hand, running on an overhead railway, and emptied into the vats by tipping. The supports of the railway must not touch the sides or any part of the vats or their supports, as the jarring caused by the running of the cars makes the ore settle down, and so renders the leaching more difficult and tedious.
The vats are filled to within a few inches of the top, and the charge is levelled by means of hoes. The amount of ore charged- in is such that, after the solutions have been applied, the surface of the charge may stand at about 12 inches below the rim. In levelling the ore, the labourer must not step into the vat or forcibly press down the ore, as irregular filtering is produced by this cause. The shrinkage of the charge on the addition of liquid is from 10 to 18 per cent. The ore should be charged-in as dry as possible, but a few per cent, of moisture makes very little difference to the subsequent leaching. As has already been mentioned, the vats are occasionally charged direct with the tailings from the stamp battery, the excess water and slimes being allowed to overflow.
Gold Lixiviation in Vat
The charge is now ready for lixiviation. If soluble salts are present in it, a preliminary washing with water is required, while, if decomposed pyrites are present, treatment with an alkaline solution is also necessary, for reasons to be explained when the chemistry of the process is considered. In each case, from 7 to 9 cubic feet of liquid per ton of ore are added from below, rising through the ore and overflowing at the top. The alkali used is either milk of lime or a solution of caustic soda. The former is preferred in South Africa, and latterly has often been charged into the stamp batteries with the ore, the amount being regulated by the requirements of the slimes settlement. After the caustic alkali (if it is used) has been allowed to remain in contact with the ore for a sufficient length of time, it is usually displaced by wash-water, which is added above, while the alkaline solution is allowed to run out at the bottom. A dilute solution of cyanide is then sometimes run in to displace the wash-water and prevent the “strong” solution from being unnecessarily diluted. The amount of weak solution thus used may be from 1 to 3 cubic feet per ton of ore. The strong solution is then added. The liquids are run on to the top of the charge through pipes of 2½ to 4 inches diameter, and are distributed by a large box with a perforated bottom, by which the force of the discharge is broken. The orifice below the filter-bed is closed before beginning to add the liquids, and not opened until the solution stands about 3 inches above the surface of the ore. The strong solution is often allowed to remain in contact with the ore for some hours before percolation is allowed to begin. Sometimes it is necessary to expedite the rate of percolation by means of vacuum pumps, sometimes the lower stop-cock is partly closed to prevent the solution from running through too rapidly. The time of treatment with strong solution is often about one or two days.
The strong solution is usually conveyed at once to the zinc boxes, but it was formerly preferred either to raise it and pass it through the charge again (circulation method), or to transfer it to a second or even a third charged vat before precipitating the gold. The advantage of these “ circulation ” and “ transference ” methods is that the solutions become much richer in gold than if they were only allowed to percolate through a single charge of ore, and consequently they give a cleaner deposit on the zinc with much less consumption of cyanide, the volume of solution passing through the precipitation boxes being less. At the Mercur Mine the circulation was formerly kept up for from 24 to 240 hours, according to the speed of leaching, the usual time being about sixty hours. At the Robinson Mine 20 tons of solution cover the ore in a 75-ton vat, and were continually pumped back into the same vat for thirty-six hours, and then passed to the zinc boxes.
When the strong solution has drained away, the weak solution is run on. The amount used is often three or four times as much as that of the strong solution, but was formerly less. The oxygenation of the charge, obtained by draining it dry after the completion of the treatment with strong solution, is often necessary to enable the residue of the gold to be dissolved by the weak solution. The weak solution is sometimes drained off, and sometimes displaced by water washes passed through as quickly as possible.
Cyanidation will always be indissolubly connected with the names of its discoverers, J. S. MacArthur and the Forrests. The solvent action of potassium cyanide on metallic gold and silver has long been known, but it was believed that the use of an electric current in conjunction was needed to quicken the action, which was otherwise too slow to be of any practical value. Until the surprising results of the MacArthur-Forrest process, as it was called for some years, were made public, metallurgists were all disposed to condemn the use of cyanide as a solvent for gold in ores as being chimerical, on account of the instability of potassium cyanide, combined with its high cost and poisonous character.
The first attempt at the direct extraction of gold by the use of cyanide was made in the United States in 1867 in a process dependent on the removal of gold and silver from their ores by the combined action of a “ current of electricity and of suitable solvents or chemicals,” such, for instance, as cyanide of potassium, the gold being simultaneously precipitated on copper plates by the electric current.
It was originally proposed to treat ores containing gold, silver, and copper by a solution containing 3% of potassium cyanide and 0.19% of ammonium carbonate. Copper was to be dissolved at the same time as the gold; if silver was present also, an addition of common salt was made. The inventor appears to have believed that, by using carbonate of ammonia, the necessity was obviated of employing an electric current, in conjunction with cyanide of potassium, in order to dissolve the gold. The precipitation of gold was effected by “a piece or plate of zinc.” The process was not tried on a large scale.
Later, a series of experiments on wet processes of treating gold ores was begun and it was entirely owing to their energy and skill that cyanide of potassium was successfully applied in practice to the treatment of gold ores. Their process consists essentially in attacking gold and silver ores by dilute solutions containing less than 1 per cent, of KCy, caustic soda or lime being added to ores rendered acid by the oxidation of pyrites, and then in precipitating the precious metals by zinc shavings. This process has now passed into use in all parts of the world. Its success is complete on many ores, and its extension has become very great, partly at the expense of the chlorination process, but mainly in treating the tailings of ores which have been crushed and amalgamated. These tailings were formerly run to waste. In a still larger number of cases, ores are treated by amalgamation and cyaniding which were formerly too poor to treat at a profit by any known process. The chief advantage of the cyanide process over the chlorination process is that roasting is not necessary, even if sulphides are present; this is a most important point in the treatment of low-grade ores, especially in places where fuel and labour are costly. Moreover, silver as well as gold is extracted by cyanide solutions. If tellurides are present, ordinary cyanide is inefficient, and the ores must either be roasted or treated with bromo-cyanogen. In the course of their investigation on wet methods, metallurgists became dissatisfied with chlorine as a solvent, owing to its energetic and preferential action on sulphides of base metals and other bodies, and its inapplicability to ores containing silver. They desired to find a solvent which would exercise a selective action in favour of the precious metals, instead of other substances. With this object in view, they experimented with a number of solvents (such as ferric bromide, ferric chloride), and finally decided that potassium cyanide possessed advantages over all other substances. They showed that it was essential to use very dilute solutions, which do not energetically attack pyrites and other base minerals, but readily dissolve gold and silver.
The process comprises four distinct operations:
- Preparation of the ore for treatment.
- Solution of the gold in potassium cyanide.
- Precipitation of the dissolved gold by means of zinc; and
- Conversion of the precipitated gold into bullion by fusion.
Preparing the Ore for Vat Cyanidation
The ore is crushed to a suitable degree of fineness, which depends partly on the condition of the gold and partly on the nature of the gangue. In the Transvaal, where tailings are treated, the ore is crushed in stamp batteries previous to amalgamation, the screens being usually about 20 or 25 mesh. Here, and in all similar cases, part of the ore is reduced to “slimes” or very finely-divided material which interferes with percolation. The tailings were formerly allowed to settle in pits or dams, when part of the slimes passed off suspended in the water. The sands, however, often contained too much slimes for efficient leaching, and the practice has been superseded generally. The tailings are now usually dewatered and partially classified in spitzkasten, and the overflow of slimes either allowed to accumulate in settling pits or else treated separately with cyanide. The material discharged from the bottom of the spitzkasten which still contains some slimes is sometimes passed into deep “ intermediate vats ” by means of Butters and Mein’s distributor, an automatic revolving apparatus working on the principle of the automatic garden sprinkler. Pipes of several different lengths conveying the pulp revolve round a central spindle, and spread the pulp evenly over the surface of the water with which the vat is filled. The sand settles to the bottom and accumulates there, while the slimes overflow at the top. Later, however, automatic distributors were discarded at several mines and hose-filling resorted to. This gives a more complete separation of sands and slimes, though automatic distribution might be made more satisfactory if the overflow were at the centre. When the accumulation of sand in the vat reaches nearly to the top, the water is drained off and the ore discharged by shovelling, or by means of machinery, such as the vat excavator, in which steel discs attached to revolving arms push the sand towards the centre of the vat. In either case the sand falls through an aperture in the bottom into ore-cars, or on to a travelling belt below. The sand is now in a suitable condition for leaching, containing only small quantities of slimes. Sometimes the pulp collected in this way is treated directly without removal. In other mills, where the method of “double treatment” of the tailings is employed, the first solution of cyanide is directly applied to these vats, and, after draining, the pulp, wetted with cyanide solution, is transferred to the second treatment vats. As already stated, the usual method is to remove the collected sands to the cyanide vats for treatment. The slimes overflowing from the intermediate vats are treated with the rest of the slimes.
In places where the separate treatment of slimes is not desirable, either from their small quantity or from other reasons, the slimes and sands are thoroughly mixed before and at the time of charging them into the leaching vat, but the results are seldom quite satisfactory. In India, the siliceous slimes are dried in the sun and then treated in the ordinary way by leaching. In the direct treatment of ores by cyanide without preliminary amalgamation, it has been usual to resort to dry crushing.
Reprecipitation of Gold & Silver in the Leaching Vats
If the solution is acid there is said to be some danger of a precipitation of gold previously dissolved, insoluble aurous cyanide being thrown down, according to the equation:
KAuCy2 + HCl = KCl + HCy + AuCy
This, however, need not be feared as long as there is an excess of KCy, which must all be destroyed by the acid before the aurous cyanide can be precipitated. Moreover, aurocyanhydric acid, HAuCy2, is formed and remains in solution, AuCy being precipitated only as the HCy leaves the solution by evaporation. There is danger in transferring a solution containing gold to a vat containing pyritic material. If the latter should contain any soluble salts of the heavy metals, insoluble salts are thrown down, e.g.:
2KAgCy2 + ZnSO4 = K2SO4 + ZnAg2Cy4
The salt ZnAg2Cy4 is probably a true double salt, but the opinion has been expressed that it is merely a mixture of simple cyanides.
A. N. Mackey attributes re-precipitation of gold to the action of free alkali on fine sulphides, by which soluble sulphides are produced. In one case in which the protective alkali amounted to 0.04 per cent, and the cyanide to 0.02 per cent., complete re-precipitation of dissolved gold took place in 18 hours. The slimes in contact with the solution contained 0.5 per cent, of FeS2. By reducing the alkalinity to 0.01 per cent., the reprecipitation was prevented from occurring.
Vat Sumps
The solutions, after passing the zinc boxes, are stored in sumps, which are now usually large steel tanks. These may be placed either at a lower or a higher level than the leaching vats. The former is the more convenient plan. A single storage tank to hold enough solution for one day’s work is then placed above the leaching tanks, and is filled by pumping from the sumps once a day. In the alternative, a single sump of moderate size receives the liquid from the boxes, and as soon as it is nearly full its contents must be pumped to the large vat above the leaching tubs.
Vat Tailings Disposal
These are sometimes sluiced out of the tanks by water under pressure. The sluice gates may be of about 1 or 2 square feet in area, and are placed so that their lower edges are level with the surface of the filter. The gates are furnished with a rubber ring to be pressed tightly against a flange by a screw. Where the supply of water is not large, or the fall of the ground is insufficient for sluicing out the tailings, they are removed by shovelling out. If the vats are deep they are furnished with doors in the bottom, which are usually circular. They are often fitted with removable cylinders, 3 or 4 feet long, inside the vats, through which the upper part of the charge is shovelled. Bottom discharge doors are usually about 9 to 12 inches in diameter. A truck below receives the residues.
Samples of the residues are taken from the charge in the vat or from the ore-trucks, usually by means of a long iron semicircular probe, shaped like a cheese-taster, which is thrust to the bottom of the vat, then revolved by means of the handle, and withdrawn with the tailings adhering to it. If the results are high, samples from various parts of the vat should be assayed separately, so as to find out if the percolation is uneven.
At some plants, the five large 450-ton vats, whose upper edges are level with the surface of the ground, are discharged by a steam crane by which truck loads of tailings are elevated and placed on a tram line. The trucks are lowered into the vats and loaded up, and the total cost of discharge is said to be 2d. per ton, including maintenance. The vats and sumps are excavated in the solid ground, the walls being built of brick and lined with cement.