Vat leaching is carried out in vats ranging in capacity from 30 to 1200 tons. Sand for leaching is separated from slime in cones, V boxes, classifiers, and in collecting vats filled by distributors—the overflow in each case being slime or finer portion of the ore. As a rule, leaching is a simple process, involving a vat of well-mixed neutralized sand, ample contact with strong and weak cyanide solutions, water washes, aeration of the sand and solution, and rapid filling and discharging. It is a cheap and effective process for clean ores when fine grinding is not necessary for good extraction.
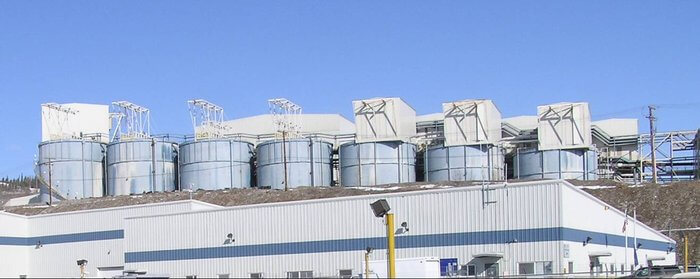
The importance of classification prior to leaching cannot be over-emphasised. Sands that are essentially free from colloidal material behave quite differently from the same type of sand with a small percentage of colloid. The two following examples from plant practice are illustrative.
The Golden Cycle mill at Colorado Springs, Colo., grinds roasted siliceous ore in rod mills through 20 mesh before sand-slime separation at about 200 mesh. Prior to the development of the Dorr bowl classifier at this plant, this separation was made in Dorr classifiers which produced a sand containing about 15 per cent minus 200 mesh, with an appreciable amount of contained colloid. The leaching rate in the same tanks varied from 0.7 to 1.4 in, per hr.
Following the adoption of the bowl classifiers, which produced practically colloid-free sand, the leaching rate increased to about 10 in. per hr., and leaching results were much more uniform. The table on the following page shows a typical screen analysis of the bowl-classifier sand when the overflow contained 2.6 per cent plus 200 mesh.
The Homestake Mining Company grind their ores in closed circuit with rod and ball mills through about 80 mesh and, following amalgamation, make a sand-slime separation at about 2 per cent plus 200 mesh. In their new plant, Dorr bowl classifiers make this separation prior to leaching and slime treatment. The Homestake ores contain an appreciable amount of pyrite which is gold bearing, and the bowl classifiers are adjusted to produce a maximum of minus 200-mesh granular material in the sands, including very fine pyrite, but to remove all colloidal material. Even with this unusually fine sand, excellent and uniform leaching results are obtained at rates up to 2½ in. per hr. in 11-ft.-depth tanks. Table 9 is a typical screen analysis of this sand.

Although it is finely ground in water, Homestake sand can be cyanided by gravity leaching to yield a high extraction of the gold. Sieve analyses and assays reveal that the finer the sand the higher the extraction. This varies from better than 90 per cent in the minus 200-mesh material to less than 50 per cent in the case of particles coarser than 50 mesh.
Leaching is done in two sand plants, one with 8 vats 44 ft. in diameter by 12 ft. deep, the other with 21 vats 44 ft. in diameter by 11 ft. deep. They are filled through Butters-Mein distributors. Lime is added to the pulp as it leaves the final set of classifying cones. The filter bottom consists of the usual wooden frame covered with coco matting and 10-oz. canvas duck.
Repeated aeration is essential to maintain enough oxygen in the solutions to effect extraction, according to A. J. Clark in E. and M.J., Oct. 12, 1931. This is done by introducing low-pressure air under the filter bottom of the leaching vat.
The leaching practice is designed to effect a progressive enrichment of the solution before precipitation, the effluent from the latter part of a treatment being strengthened but not precipitated before being returned to the top of another charge. Solution and zinc are conserved by this system. The total solution used amounts to only 0.8 ton per ton of sand. The water draining from the newly filled charge contains sulphates and thiosulphates. After the second aeration, when cyanide solution has been added to the top, these compounds appear in larger quantity. Later, they are followed by thiocyanates, which in turn are followed by the first traces of cyanides. Gold appears in the effluent soon after the first trace of cyanide is noted. Thiocyanates, the main source of cyanide loss, are stable compounds, but although they build up in solutions, they do not affect extraction.
Low alkalinity is favored, a pH of 9.6 to 10.2 giving the best extraction. A cyanide of 49 per cent NaCN equivalent is used. Strong solutions carry 0.095 per cent and the effluent 0.035 per cent NaCN. Cyanide consumption is ¼ lb. per ton treated.
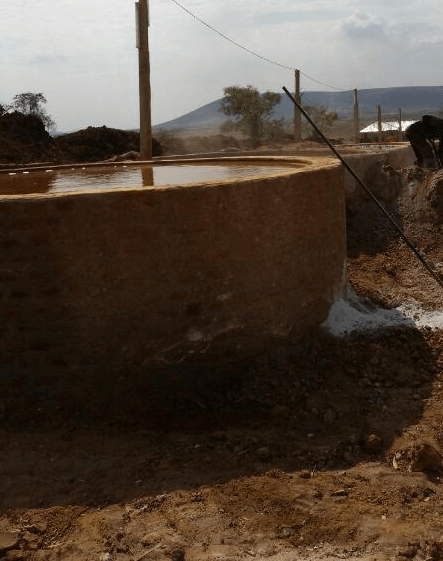
At the Golden Cycle, Dorr and Akins classifiers make a sand-slime separation as shown in Table 11.
The sands are conveyed to 10 leaching vats 50 feet by 15 ft. deep with a capacity of 1200 tons each. The initial leaching period is 48 hr. with solution containing 0.5 lb. cyanide per ton. This solution goes to the precipitation presses. Sand charges are drained and aerated at least four times for 8-hr. periods during the 6- to 8-clay treatment cycle. Barren- solution washes and a water wash follow. Two men using 2½-in. hose and water at 120-lb. pressure discharge the vats in 3½ hr.
While the trend on the Rand is toward all-slime plants, a considerable tonnage is still handled by leaching of the sand fraction of the ore.
Randfontein Estates Gold Mining Co. This mill, which is described in detail in Chap. XV, Sec. 3, mills 13,000 tons per day, of which 20 per cent is handled by sand leaching.
The sand from bowl classifiers at 51.8 per cent plus 100 mesh, 8.5 per cent minus 200 mesh, is pumped to Butters distributors serving thirteen 60-ft .-diameter by 12-ft.-deep sand-collecting tanks, which, in turn, discharge the collected sand to twenty-six 60-ft.-diameter by 10-ft.-deep leaching vats. Treatment cycle is 22 hr. collecting and transfer, 10 hr. leaching and washing, and 4 to 5 hr. emptying.
A charge of about 1000 tons of sand is leached with 250 tons of strong solution made up to 0.056 per cent KCN, followed by 750 tons of plant circulating solution and then 1000 tons of barren solution. Seventy-four per cent of the effluent at an average value of 1.5 dwt. per ton goes to precipitation. The balance is by-passed to plant circulating solution.
Cyanidation and concentration of gold and silver ores
Vat Leaching Copper Ore
Vat leaching is a simple and efficient mode of effecting adequate contact between the solute and aqueous solvent. It utilizes the countercurrent principle, with the ore to be leached remaining stationary, as differentiated from most counter-current methods, where all materials are moving. The ore, confined in a rectangular leaching vat is successively treated with an increasing concentration of leach solution, which may be added as a continuous flow or on a batch basis. Thus, maximum leaching strength first comes in contact with minimum metal concentration in the ore, and as its leaching potential diminishes, it comes in contact with increasing metal concentration in the ores. In the event of the leach solution entering the vat at the bottom and overflowing at the top, the system is known as upward percolation. It is more common if the flow of solution is continuous through a series of vats. If the solution enters either at the top or the bottom, but is withdrawn from the bottom, the system is known as downward percolation, which is the more common method if the batch method is used. A predetermined filling and soaking period, followed by a drain, complete a single cycle. This drained solution then advances to the next vat. and the process is repeated. Solutions arc referred to as first advance, second advance, etc., to designate the position in the complete leaching cycle. Dependent on the solubility of copper in the ore, a single charge of ore could be given any number of successive leaches with increasing concentrations of leach solution; if, for example, six cycles were necessary for optimum extraction, six charges of ore would be undergoing simultaneous leaching treatment.
It is also important to separate the occluded leach solution from the final leach residue (it may represent as much as 30% of the total copper dissolved). A countercurrent principle of washing is employed. This method, essentially the same as that described for counter-current leaching, may also be effected on either a continuous or batch basis. In either case, the residual gangue and its occluded solution are successively treated with wash solutions of decreasing copper concentration. The final step is effected with copper-free wash solution. The process consists, accordingly, of a series of dilutions, the effectiveness dependent on the degree of diffusion of the remaining occluded solution and incoming wash solution in each other.
Ores may be separated into sand and slime, and the sand leached by upward or downward as well as upward and downward percolation of cyanide solutions. Leaching practice has decreased in recent years with the development of closed-circuit grinding and now is seldom incorporated in new plants. Ores are known which need only to be crushed coarsely to ½ in., and the whole leached. Deposits of ore amenable to coarse crushing, however, are rare. The gold must be on cleavage planes or in the cavities left by previous natural leaching of the ore in place.