How to Make Boron by Electrolysis
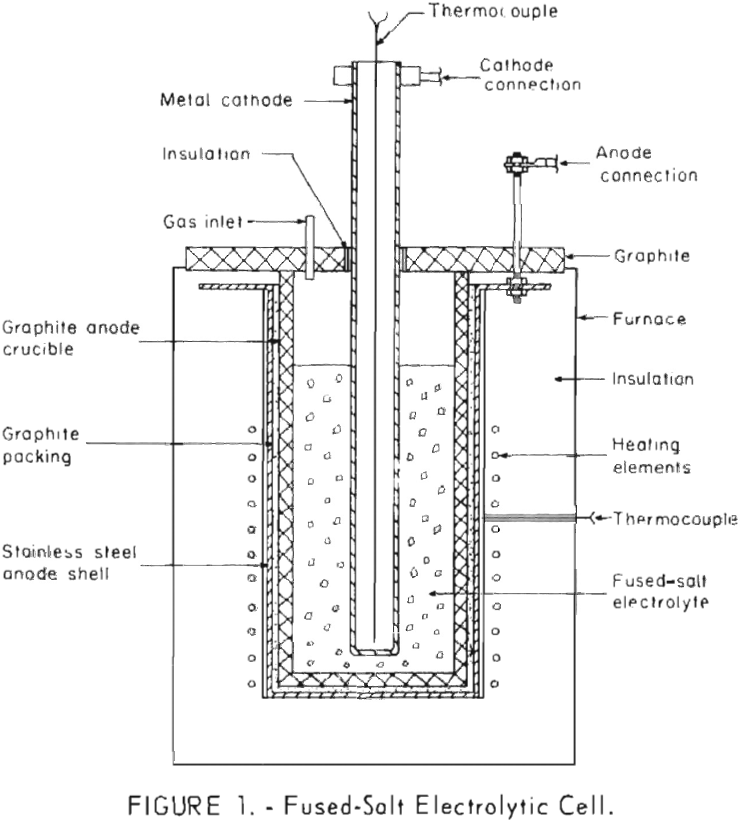
Because an economic method for preparing pure boron has not been developed, a program was started by the Bureau of Mines to evaluate existing techniques or to develop new methods for preparing the pure element. This report describes investigations directed toward the development of techniques for the preparation of pure boron by fused-salt electrolysis. Only […]
How to Determine Trace Impurities in Helium
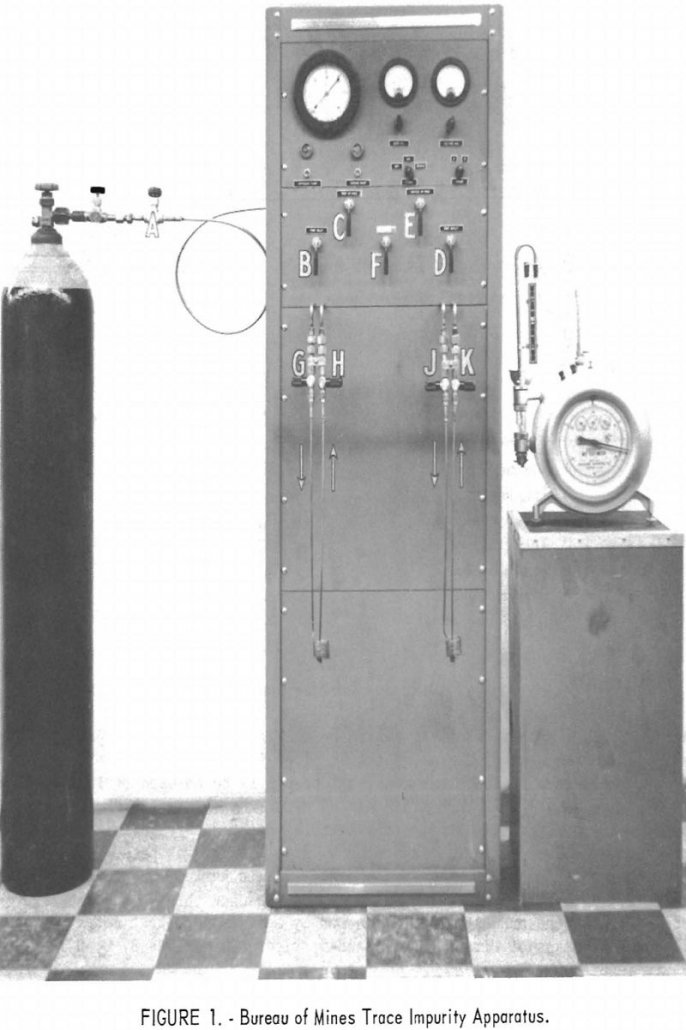
An apparatus for determining trace impurities in Grade-A helium by mass spectrometer methods was designed and built by the Federal Bureau of Mines. Grade-A is the designation for helium commercially produced by the Bureau. Its nominal purity is 99.995 percent. The device, following a suggestion by Deaton, concentrates the impurities in the helium by freezing […]
How Impurities Affect Titanium Properties
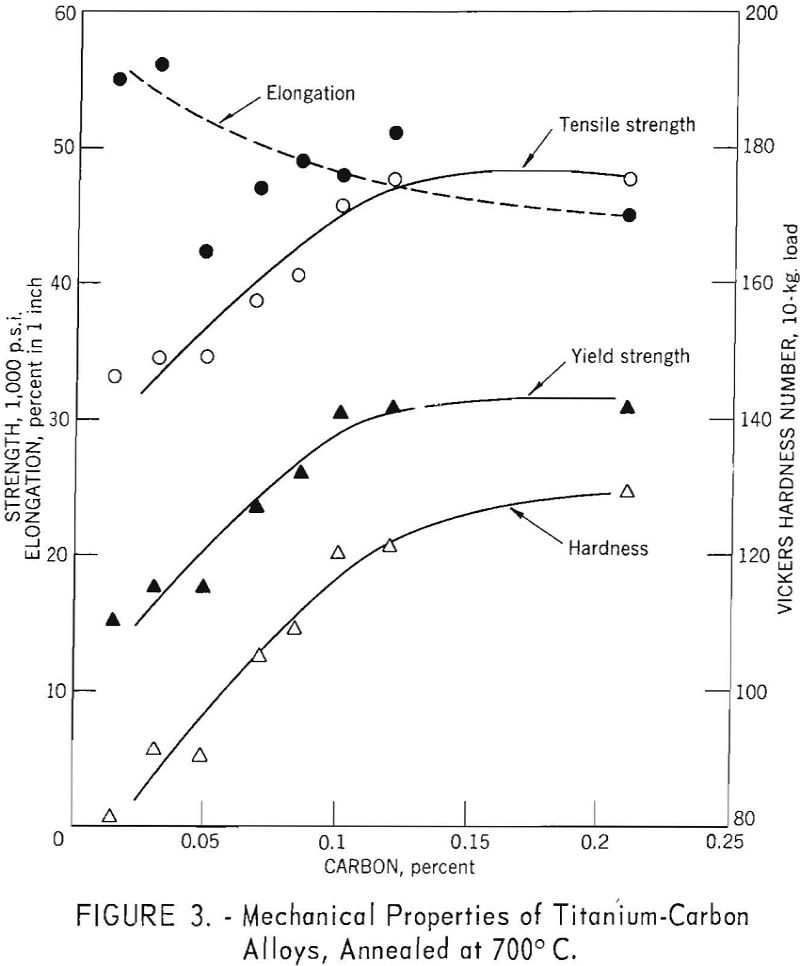
The purpose of this investigation was to determine the effects of the impurities, oxygen, nitrogen, carbon, and iron (in low percentages) on the mechanical properties of electrolytic titanium. The strength and hardness of binary Ti-O, Ti-N, and Ti-C alloys are linear functions of alloy content in the composition range investigated. Compared to oxygen and carbon, […]
How to Increase Tensile Strength Titanium
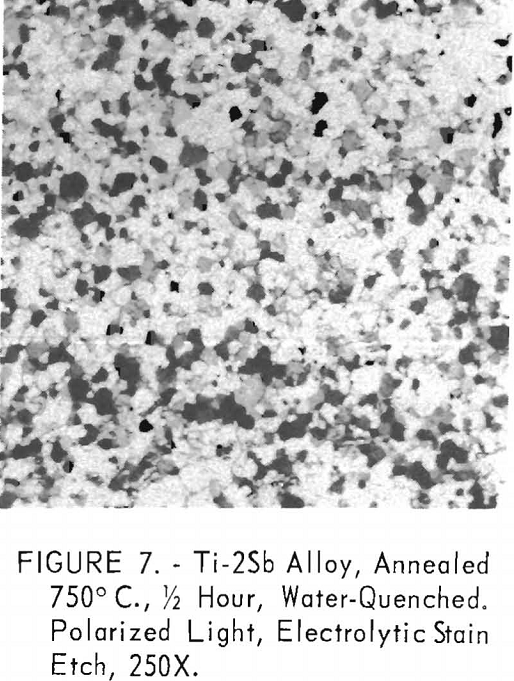
Antimony up to 10 percent increases the strength of titanium by solid-solution hardening. The general relationship of hardness, strength, and elongation in these alloys is similar to that found in several grades of high-purity and commercial titanium. Tensile strength (annealed condition) appeared to be a linear function of Vickers hardness regardless of composition. For equivalent […]
Electrorefining Beryllium
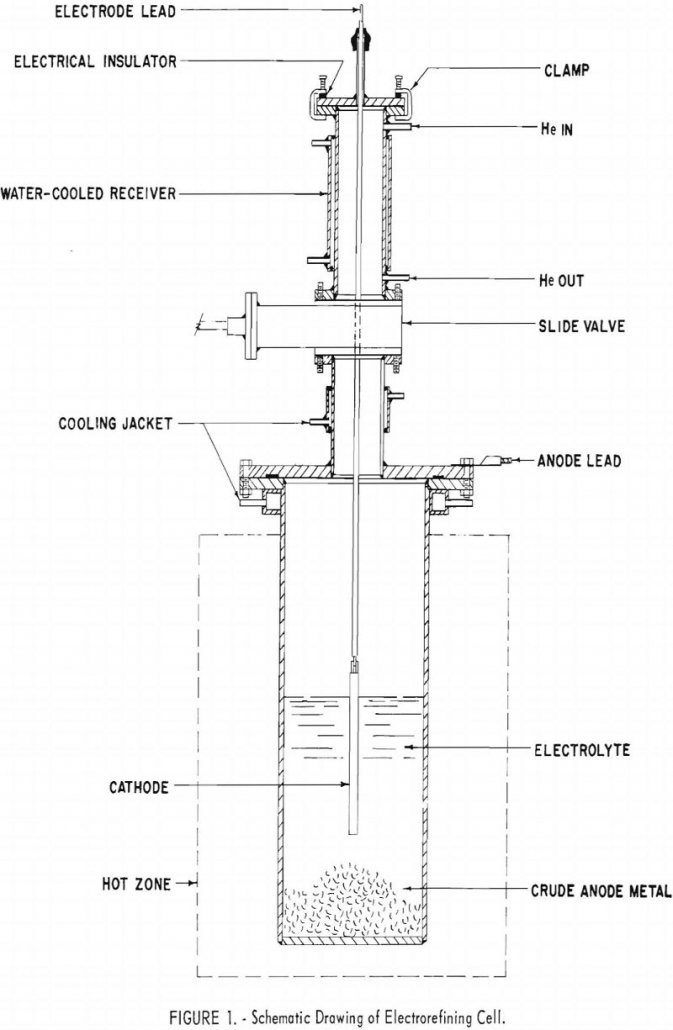
Results of the preliminary tests have demonstrated the possibility of electrorefining beryllium in KCl-LiCl-BeCl2 baths. Qualitative spectrograph analyses of the starting material and the products indicate the following estimated percentages of reduction of metallic impurities: Magnesium was reduced by at least 50 percent. Iron, copper, silicon, and manganese were reduced by at least a slight […]
Electrorefining Chromium
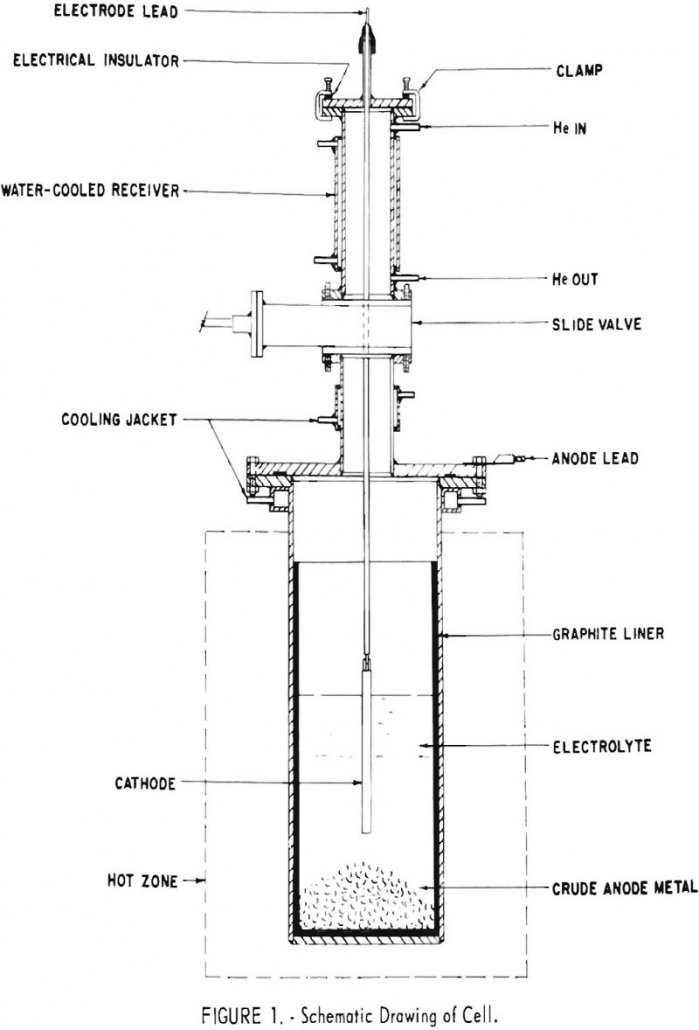
The Federal Bureau of Mines refined chromium from an aqueous electrolytic process in molten sodium chloride-chromium chloride electrolytes. Oxygen and nitrogen contents were reduced by a factor of 10 to 40, but most other impurities were little changed. The product usually contained a little more iron than the feed. Since iron was entering the bath […]
Electrowinning of Ceric Oxide and Cerous Fluoride
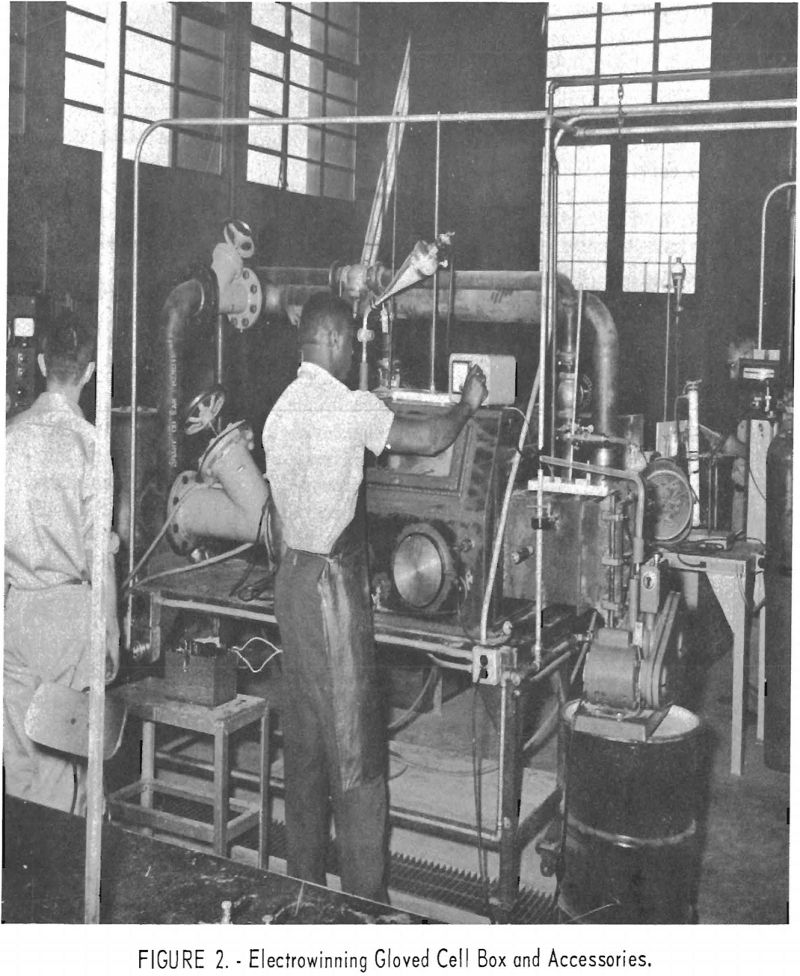
The metallurgical laboratory data developed in this study indicate an improved electrowinning process for producing higher purity cerium ingot. Equipment under development included the molten-bath container or electrolytic cell, electrodes, and related items, as well as an enclosure or cell box resembling that of a vacuum furnace. The cell box is designed to allow molten […]
Rare-Earth Elements Electronegativity
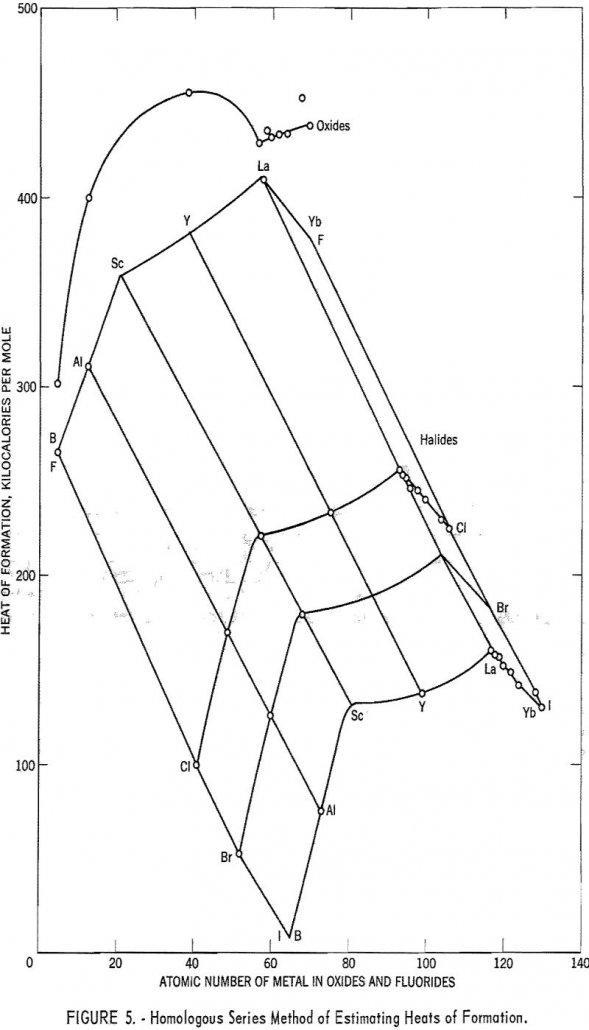
The rare-earth metals can be fitted into Pauling’s electronegativity scale if it is modified to take highly ionic bonds into account. Good agreement between theory and experiment is obtained only for metals of groups Ia, Ila, and IIIa of the periodic table, but here it is good enough to permit estimation of unknown heats of […]
Electrowinning Molybdenum & Tungsten
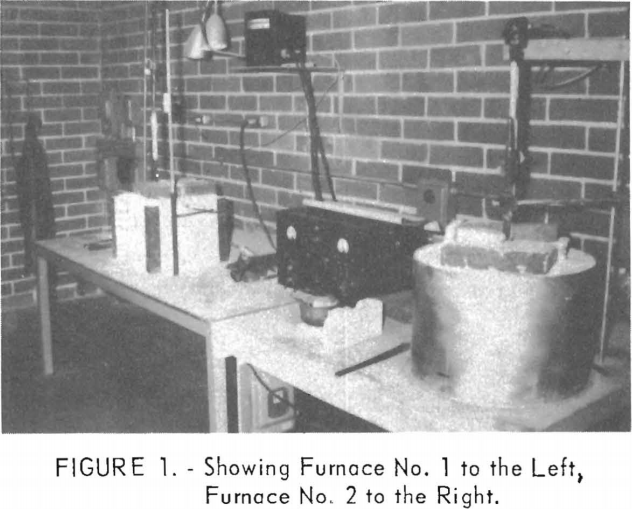
Laboratory results of fused salt-bath electrolysis indicate that recovery of crystalline tungsten metal from scheelite may be commercially feasible; that purity of the product, although not extremely high, can be controlled to a considerable degree in accordance with varying requirements of cost, product specifications, and purity of raw materials. The selective deposition of molybdenum and […]
Cathodic Protection
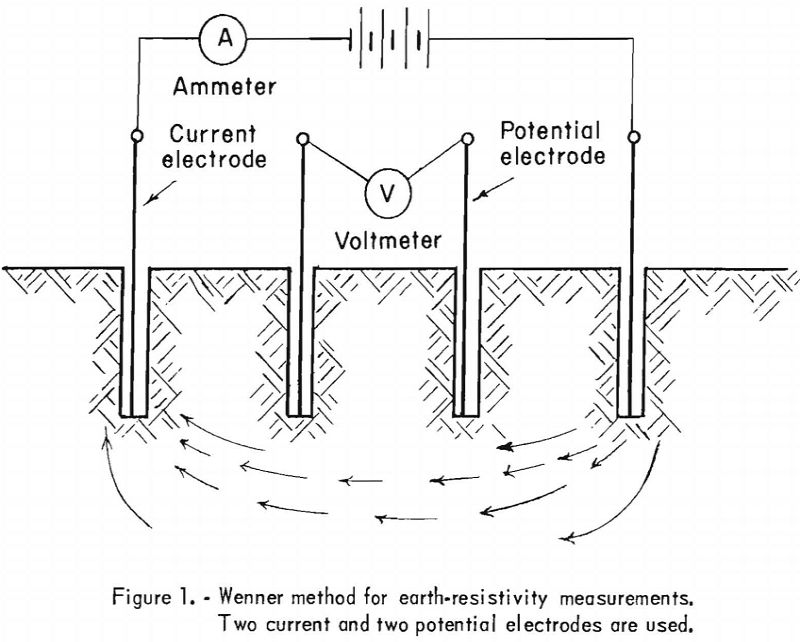
Loss of metal and damage to buried metal structures because of corrosive action is, to a large extent, determined by the soil resistivity in the immediate vicinity of the structure. The intensity of corrosive action is inversely proportional to the soil resistivity; that is, corrosive action will increase as the soil resistivity is lowered. Moisture […]