Gold Alloy Melting and Casting
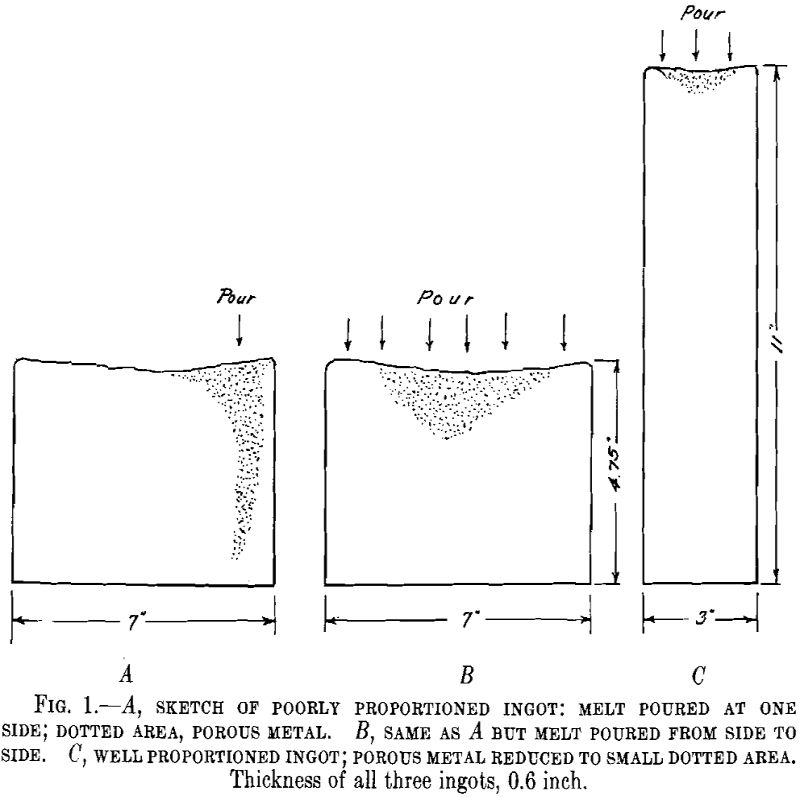
The problem of scrap is probably of greater importance in the production of gold, silver and other precious metal alloys than is the case for base metals and alloys. Remelting of gold and silver scrap in the shop is always a costly process because it involves losses by oxidation of the base metals in the […]
How to Operate a Blast Furnace
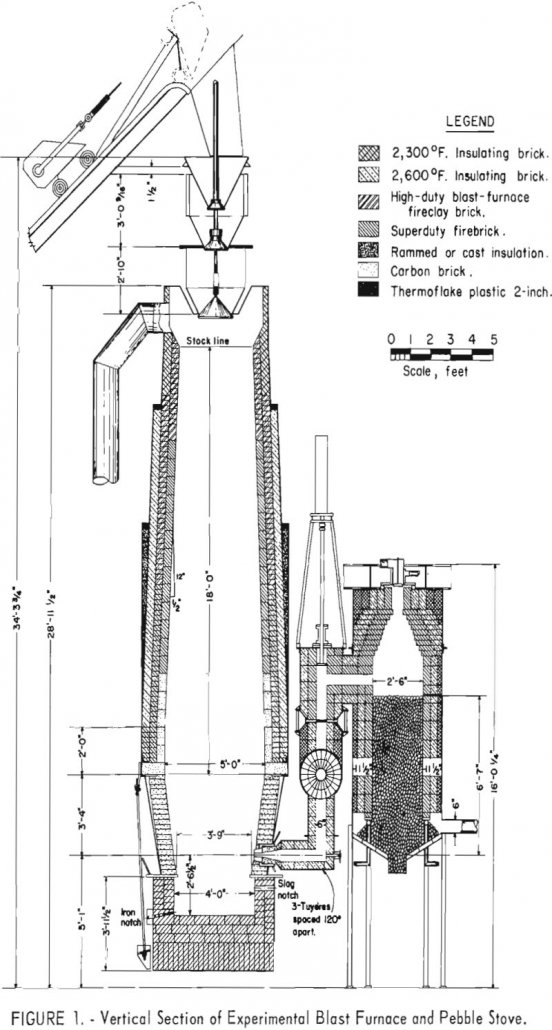
The experimental blast furnace has attracted increasing interest during the past decade as a practical means for investigating a broad range of blast-furnace smelting problems. Under experimental-furnace conditions, information can be obtained with less expenditure of time and raw materials and, therefore, at lower cost than comparable information could be obtained under industrial operating conditions. […]
Smelting Taconite in Blast Furnace
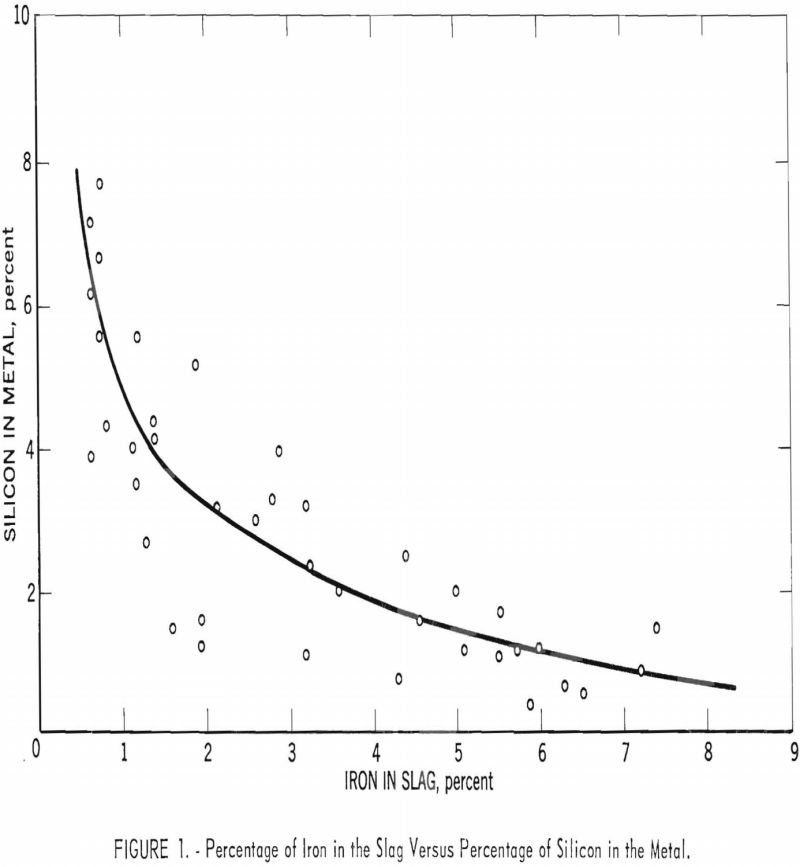
Crude Minnesota taconite was charged in the Bureau of Mines experimental blast furnace so that smelting characteristics of such highly siliceous raw materials could be studied and smelting costs compared with those of a standard Mesabi ore. The Bureau recognized that the highly siliceous nature of the crude ore and its relatively low metallic content […]
Casting Titanium Zirconium and Hafnium
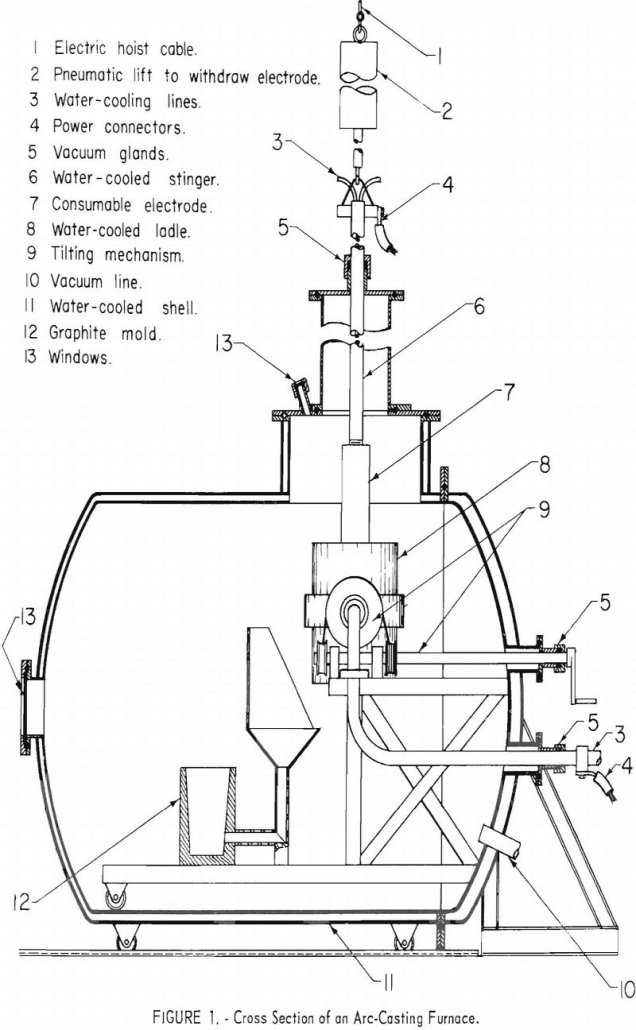
The work covered in this report is a continuation of an earlier feasibility study by the Federal Bureau of Mines and points out improvements in the skull-melting method for casting reactive metals such as titanium, zirconium, and hafnium. Machined graphite molds with laminated sections can be reused many times. Large tube sections can be produced […]
Smelting Unfired Iron Ore Pellets
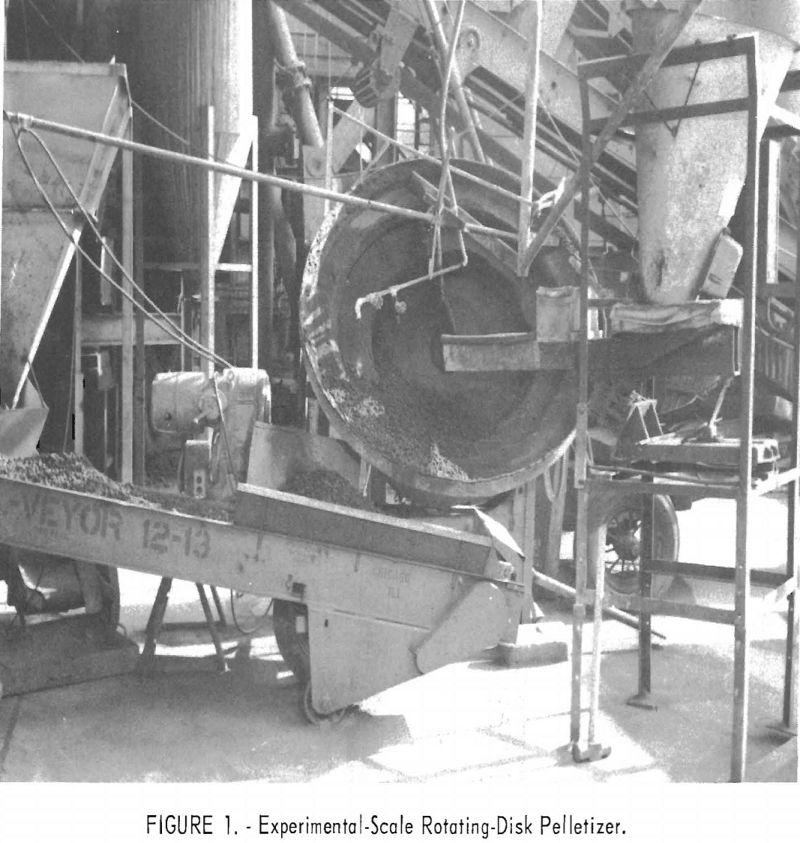
Fines and concentrates must be consolidated or agglomerated into larger masses before they can be smelted in a commercial blast furnace. Such agglomeration is usually done by sintering, pelletizing, nodulizing, or briquetting. Sintering has been the more common practice, but with the advent of taconite concentrates pelletizing is increasing in importance. Pellets in the blast […]
How to Convert Nickel Oxide to Nickel Metal
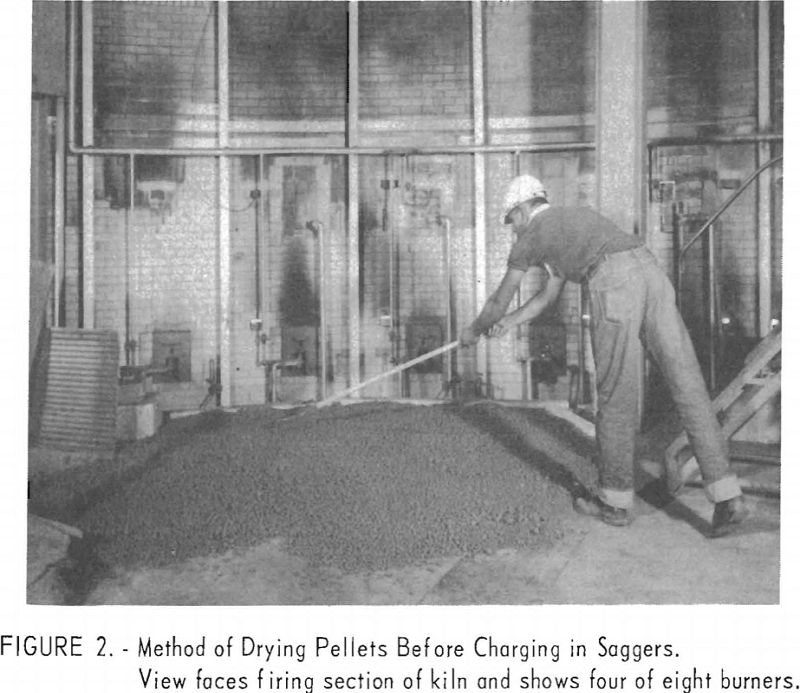
Sponge nickel can be produced by gaseous or solid-fuel reduction or a combination of both. Although pelletized nickel oxide was reduced in a laboratory rotary furnace, about 40 percent of the pellets abraded; magnetic separation was required to remove the fine sponge nickel from the charred coal and dolomite; hence, rotary-kiln operations were not considered […]
Refine Zinc from Iron Impurity
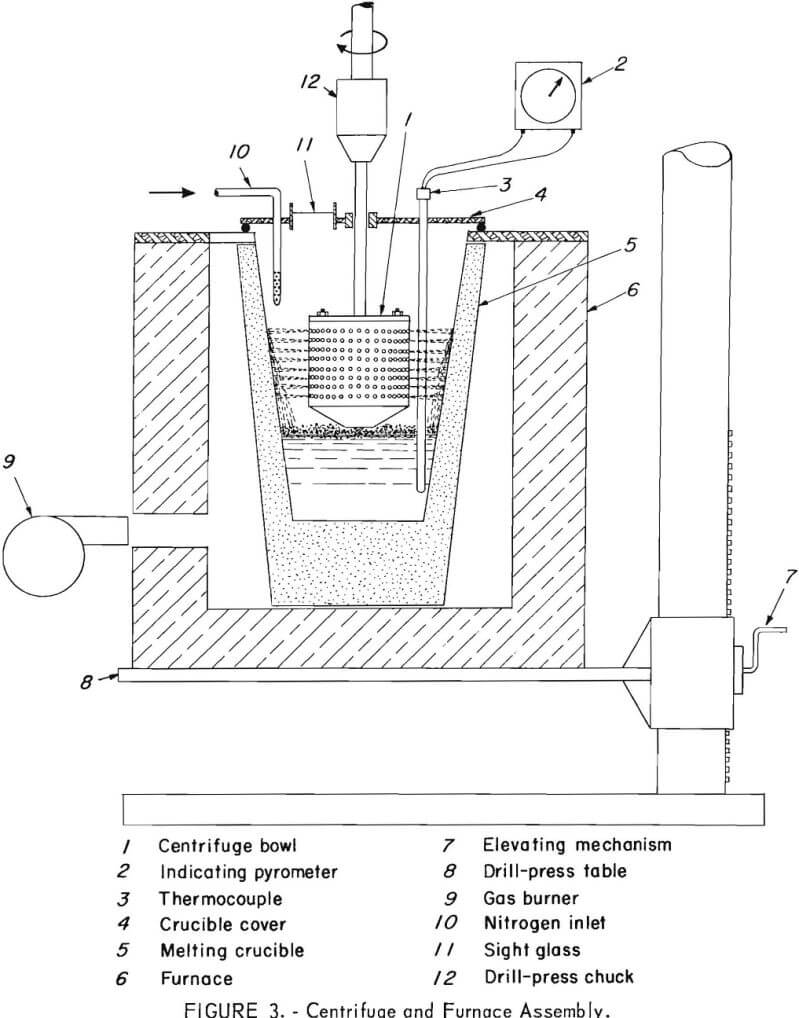
A process was developed in which iron-contaminated zinc was refined to readily acceptable purity. Aluminum added to the molten impure metal reacted with the iron, forming a solid intermetallic compound, Fe2Al5, which floated to the surface of the melt. Small amounts of residual aluminum were eliminated from the product easily by fluxing with zinc chloride. […]
Electric Smelting Lead Zinc
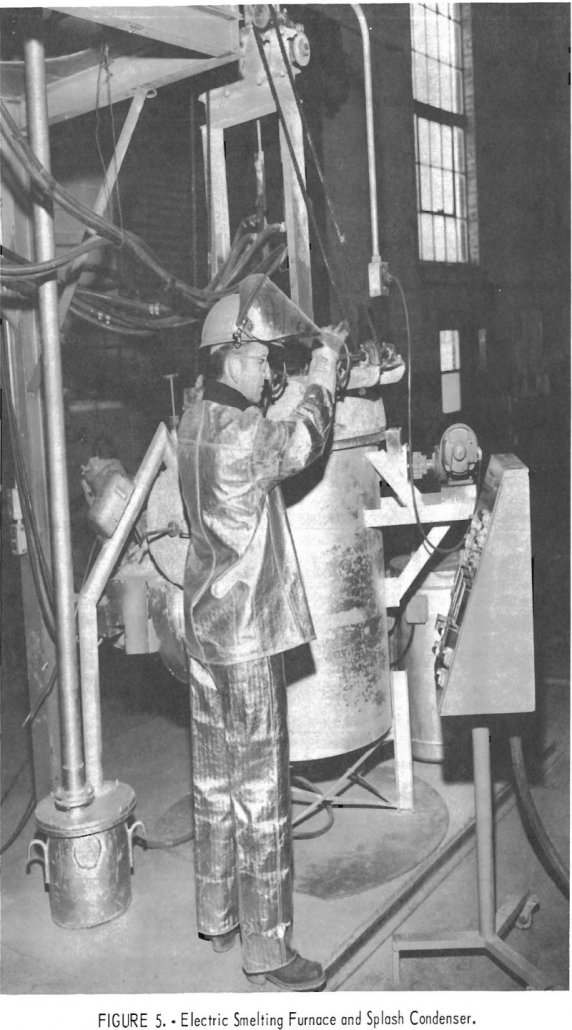
Based on the results obtained during this investigation, slag-resistance, open-bath electric smelting of complex lead-zinc sinter is not considered feasible. Inherent characteristics of electric smelting promote and permit excessive transfer of iron, lead, and volatile slag constituents to the condenser when smelting normal lead-zinc sinter. Reaction of these constituents with zinc causes its degradation. Consequently, […]
Smelting low Pyrite Copper Concentrate
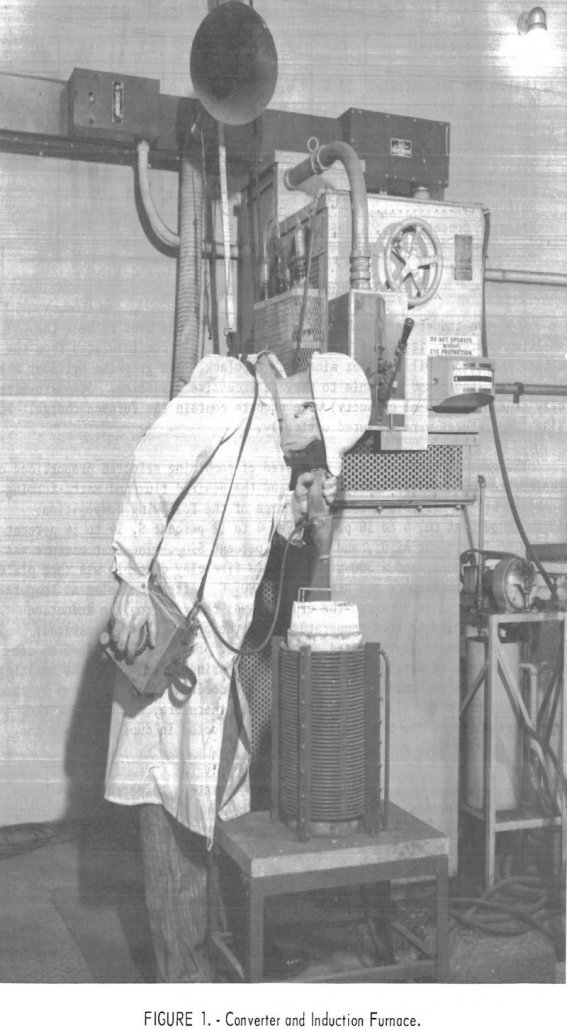
A laboratory smelting study was conducted on a copper ore containing chalcocite and native copper to test the technical feasibility of non-pyritic smelting (low pyrite). The results of this investigation led to the following conclusions, based on sulfur and copper recoveries and matte compositions: The concentrate can be effectively smelted when pyrite is replaced by […]
Induction Melting of Titanium
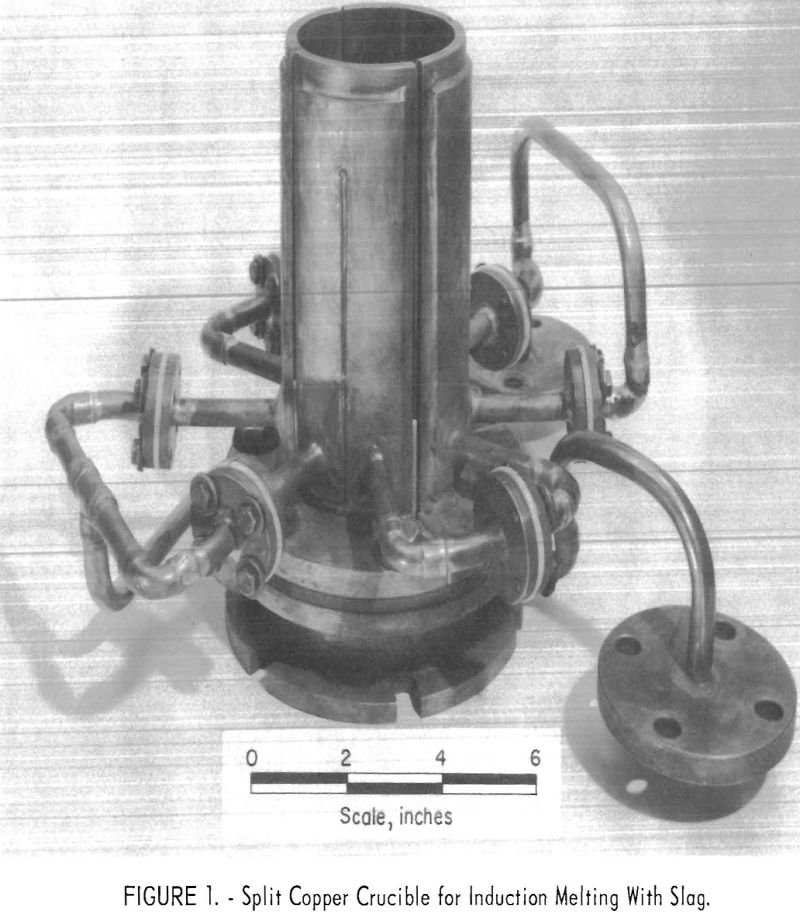
The primary purpose of the research covered by this report was the development of a method for induction melting titanium in a water-cooled copper crucible. The results reported represent findings obtained during the melting of a minimum number of ingots; therefore, only tentative conclusions can be drawn regarding the effects on metal quality of many […]