Solving Flocculation Problems
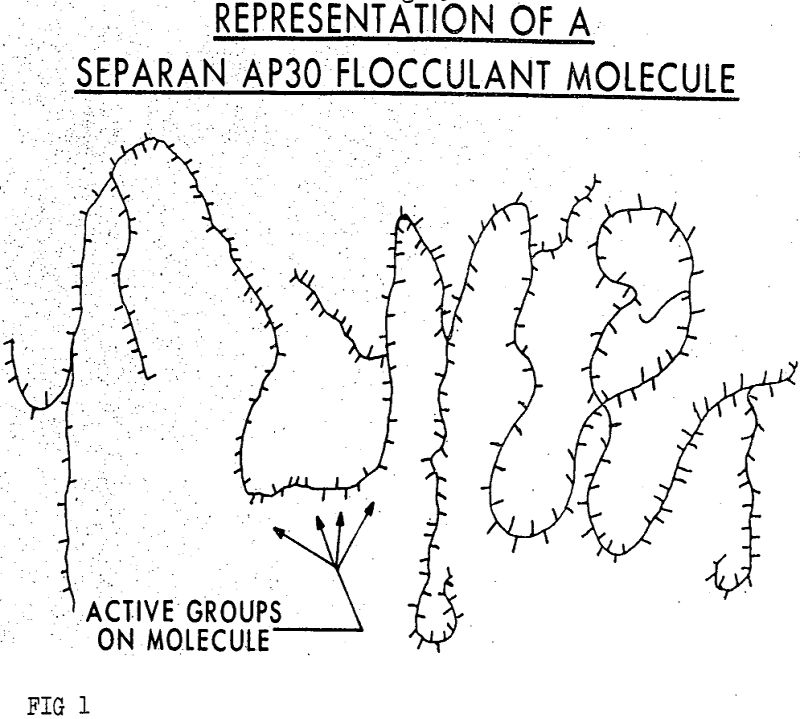
This is the case history of how two nearby plants in Southwest Virginia solved their water clarification problems. While the solutions should not be considered applicable industry-wide, the methods used in arriving at the answers deserve, consideration. As the plant tonnage increased, it became evident that the amount of coal fines produced in the mining […]
Effect of Pulp Depth and Pulp Density in Thickening
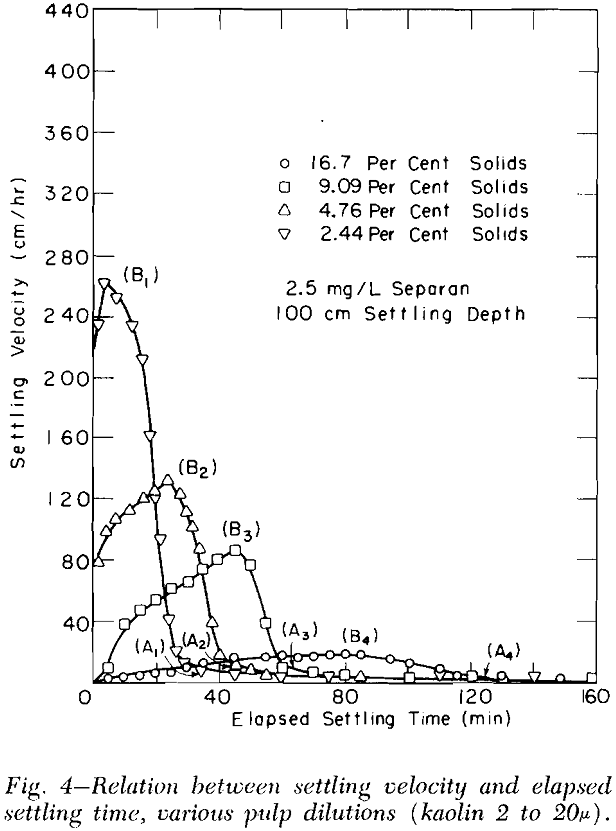
The two principal attributes of a thickener pulp are its settling rate and the ultimate pulp density of the thickened mud. Testing for evaluation of thickening attributes of a pulp has usually been done batch-wise by placing the pulp in a one-liter glass graduated cylinder and noting the position of the boundary between clear liquor […]
Solid Liquid Separation by Flocculation
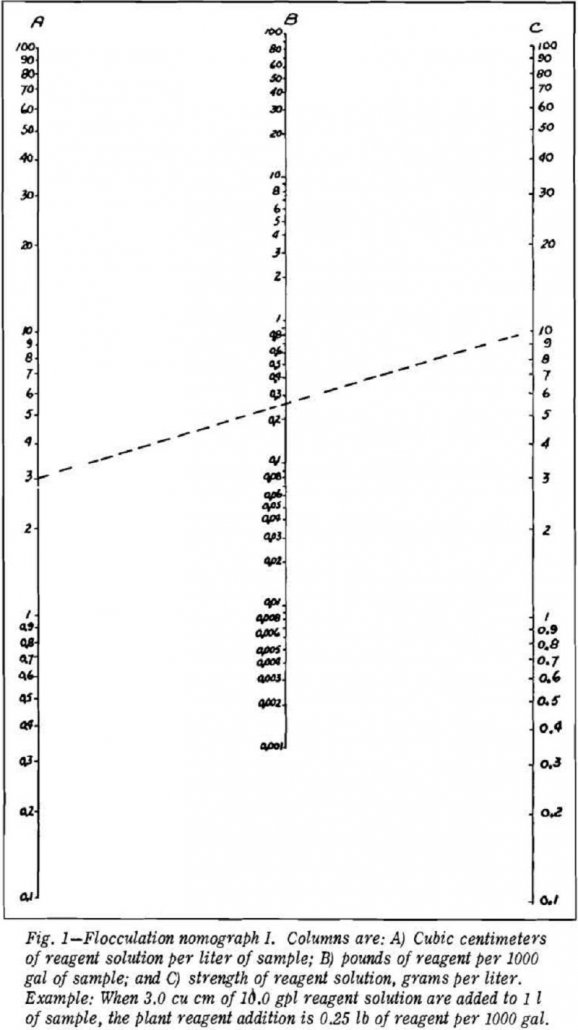
When is use of a flocculant justified in terms of overall process economy? when it results in process improvement, such as producing a clear liquor for electrolysis, precipitation, ion exchange, or solvent extraction; when it results in satisfying requirements of pollution abatement ordinances; when it results In increased recovery of values that would otherwise be […]
Thickener Design Underflow Pump Arrangement and Automatic Controls
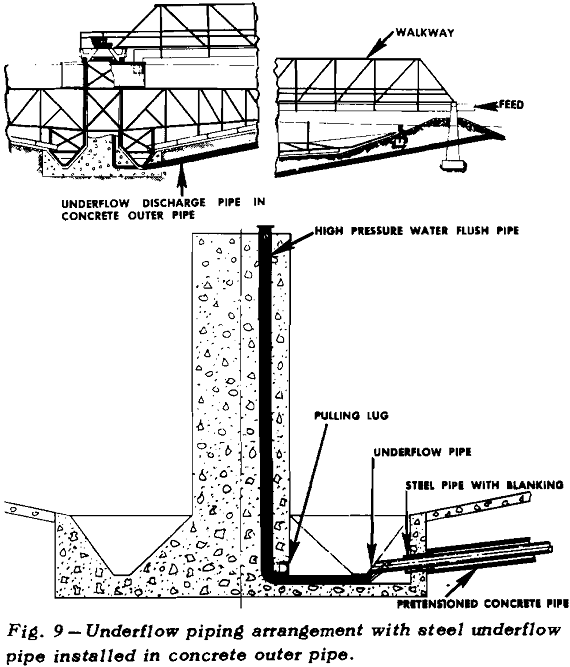
A number of unique thickener mechanism designs with the operating results achieved in various installations are discussed. These unusual designs include new types of raking arms, lifting devices, and feed-wells employed to obtain higher underflow densities and minimum operator control or improved overflow clarity. Thickening The conventional raking arms consist of a relatively simple truss […]
Double Stage Filtration Circuit & Wash Thickener
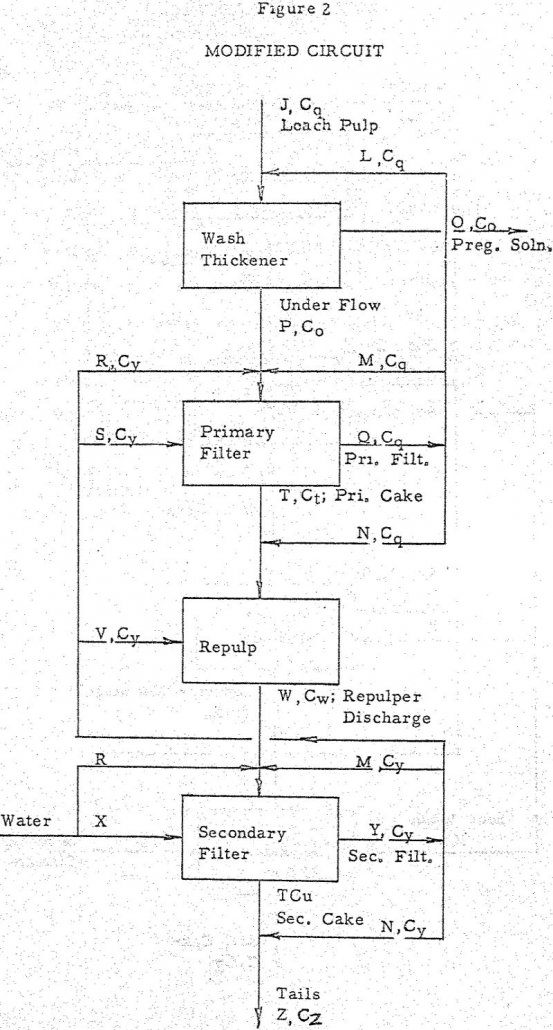
The operation of a series wash thickener-two stage filtration circuit determines the soluble loss in many hydrometallurgical operations. A study of this circuit yielded expressions which permit calculation of soluble loss for almost any condition of operation. The soluble loss over a range of the circuit variables is presented to illustrate and evaluate circuit performance. […]
Chemical Aspects of Thickening and Clarification

Chemistry plays a more important role in milling operations than is generally recognized, particularly in fluid-solid separation processes. Chemical aspects are also very important insofar as plant water quality is concerned, and in the manner in which this water quality effects plant design and operation. One aspect of the use of mining chemicals which has […]
Thickener Design and Theory Problems
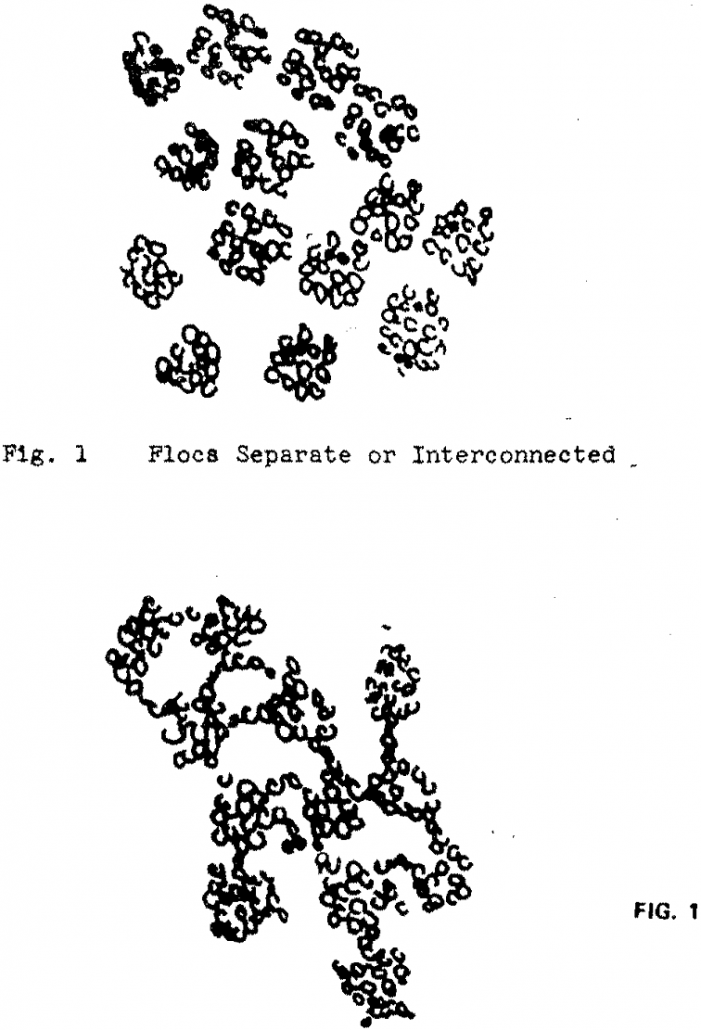
This paper will review thickening theory, from the study but of the practicing engineer, with particular emphasis on areas of uncertainty or disagreement. It will attempt to outline broadly what we know and what we don’t know. This should serve two purposes. First, it will warn the process engineer where he might get into trouble. […]
Lamella Thickeners
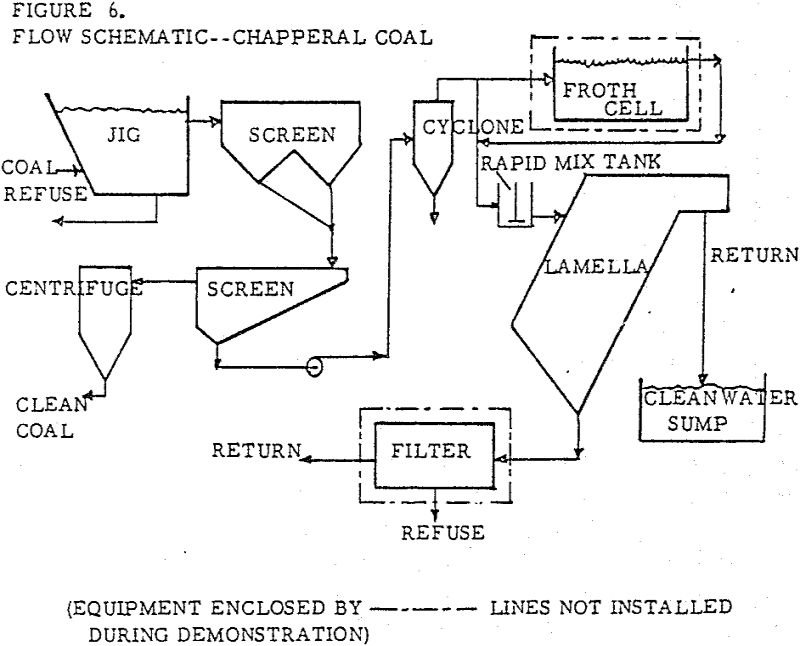
Stringent environmental regulations, which have limited the use of sludge ponds, coupled with the economic incentive to clean more coal or to add fine coal cleaning additions to existing preparation plants have increased the use of static thickeners in preparation plants. The Lamella Gravity Settler, sometimes designated Lamella Thickener, is a shallow depth sedimentation device […]
High Capacity Thickener
Conventional practice is to add flocculant as a dilute solution to the feed slurry in a launder or feed pipe, possibly using staged addition so as to improve the floc growth. Mixing in launders is not necessarily optimum, and with deep launder pulp depths lower layers of slurry do not readily rise to the surface […]
Earth Bottom Thickener Design & Construction
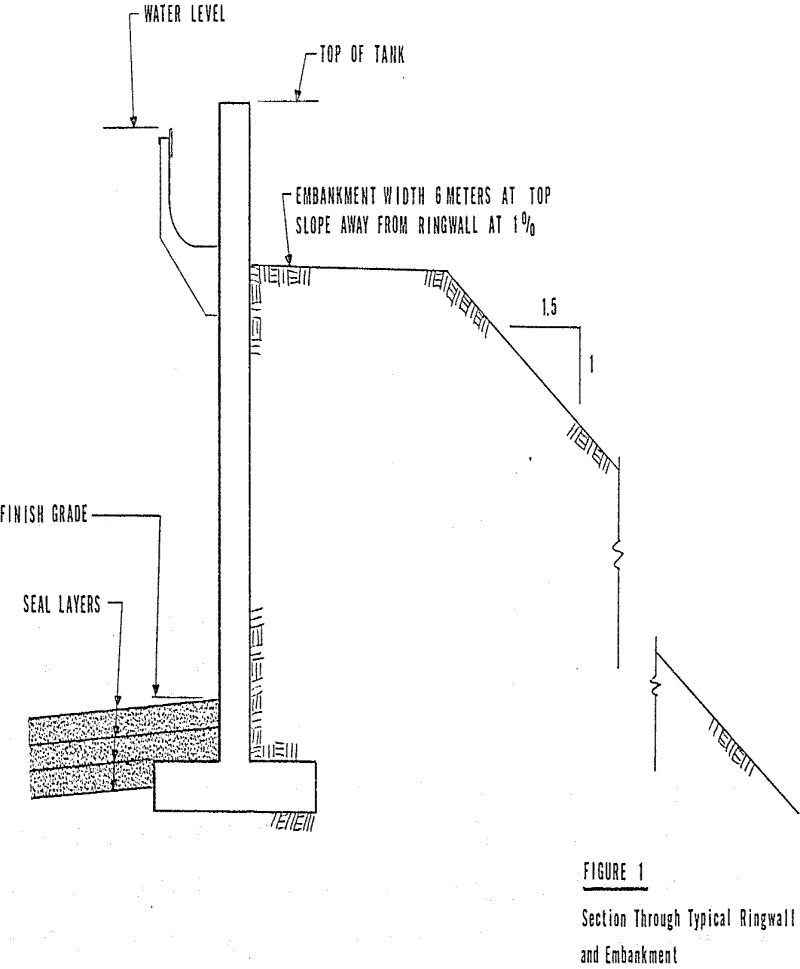
The essential elements of thickener basin construction consist of: Laboratory testing and selection of soil materials for thickener bottom and determination of required thickness of treated blanket. Rough grading of site to bottom slopes of thickener basin. If imported soil materials are to be used, establish rough grade at bottom slopes minus 150 to 450 […]