In a recent discussion of Dr. Jeffries’ paper on tungsten, J. C. W. Humfrey, after taking exception to certain of the author’s ideas relative to the cohesion of A and C metal, expresses the opinion that future research is likely to develop a method of preparing tungsten possessing “mechanical properties in line with those of other metals.” The present paper by Dr. Jeffries begins with a determination of comparative properties of tungsten, copper, and iron, in which much dissimilarity is apparent, and ends with a coherent explanation as to why much of this dissimilarity is natural and inevitable, thereby supplying theoretical means for visualizing the changing properties of metals in general, once certain fundamental facts are known.
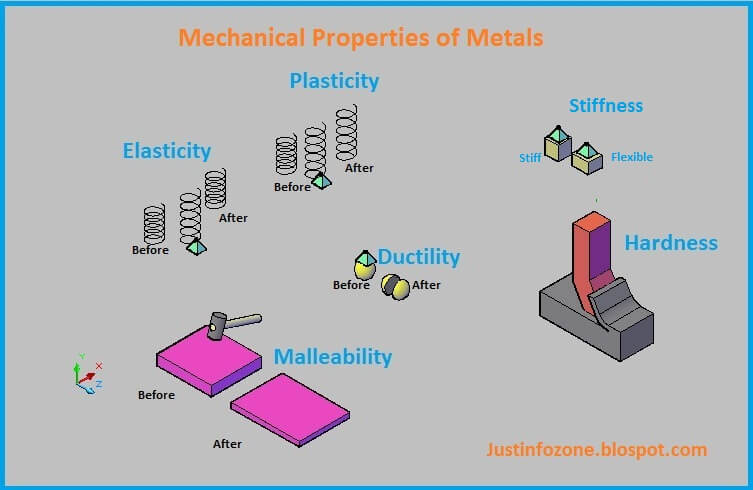
The author’s reasoning is primarily from the standpoint, of the amorphous theory and his principal achievement is the development of an idea of differential cohesion according to conditions of temperature, etc., between A and C metal (which was first plainly suggested by Rosenhain and Ewen, in their papers on Intercrystalline Cohesion of Metals) along with associated ideas, so as to give us a really useful working theory.
I have come rather reluctantly to believe in the amorphous theory, or some theory admitting a modification of the ordinary crystalline phase so as to permit differential properties within the conglomerate, mainly because in no other way does it seem possible to account for observed changes of properties with temperature, etc. The very best illustration of the competency of the amorphous theory in this respect is seen in this and other recent papers by the author. All fractures through normal or healthy metal that have been preceded by deformation are supposed, by Dr. Jeffries, to take place either through the amorphous phase or at certain boundaries between amorphous and crystalline material; his reference to fractures, both members of which are similar in appearance and do not reveal a preexisting coarse-grained structure because of a coating of amorphous metal, indicates his preference for the former interpretation.
It is difficult to imagine any structure made up of crystalline grains surrounded by a truly amorphous cementing material—that is, any structure in which there is an abrupt transition from a crystalline orientation of particles to a truly amorphous orientation—which will not show preponderating weakness at the junction between phases. On the other hand, it is easy to imagine a structure in which there is material between neighboring grains wholly belonging neither to one nor the other, but passing from one orientation through a more or less neutral position or subcrystalline condition to the other orientation, and such a structure might well reach its greatest strength in the boundary region.
Some detail of this sort appears to be necessary because the majority of Dr. Jeffries’ conclusions are based on a process of weighting averages from a specific assignment of properties to an amorphous component and a crystalline component. Ordinarily, allowance would need to be made for the cohesion or attraction between these phases, but on the above assumption of continuity this would not seem necessary, as every property would pass from one extreme to the other without discontinuity.
Effect Of Temperature, Deformation & Grain Size On Mechanical Properties of Metals
Dr. Jeffries’ cites cold coarse-grained zinc as a brittle metal that, at the fracture, shows grains reflecting light directionally owing to an absence of amorphous metal on the surface of fracture. Cold zinc is an admirable example ,of something that must be placed in a class intermediate between “easily deformable” and “brittle.” It can be worked cold, but with greater expenditure of energy than when heated and with greater likelihood of complicated fracture before the grain becomes materially refined. If all the elements of fracture through different crystals are brought into one plane they cannot be distinguished from one another either by direct observation with any variety of illumination or under any form of microscopic examination. Either the fractures are all through one set of cleavage planes or the directional irregularities of the surface are so minute that the reflection of light takes place as it would from an ideally plane surface. I am thus of the opinion that no conclusion can be drawn, as to the presence or absence of an amorphous film by simple examinatipn of fractured surfaces. Directional characteristics are revealed only after etching, straining to produce slip bands, or like methods. Even some forms of etching fail absolutely to develop the minute etching pits, which, collectively furnish the evidences of orientation but leave surfaces that appear smooth under the highest magnifications. It is quite easy to develop a coarse-grained structure in a piece of rather pure thin zinc sheet, originally of small equiaxed grain, by moderate local strain followed by annealing. If, after annealing, the piece is dipped momentarily in concentrated nitric acid, a surface effect similar to that obtainable by fine polishing is secured. It is inconceivable that any amorphous coating can remain on the surface as the dip can be repeated at will with the removal of any desired amount of metal from the surface and the effect remains the same.
It would appear that the tin fracture which Dr. Jeffries contrasts with the zinc fracture does not reveal the original coarse-grained structure because sufficient, deformation has taken place during the tensile test to produce small grain fragments and complicate the path of rupture. The outlines of the original grains may be visible on a polished and etched section near the break because the fragments from one grain, although differently oriented, conform somewhat to the original orientation within the grain. I believe, with Dr. Jeffries, that the fracture is through amorphous or subcrystalline material, but see no way of demonstrating this visually.
There is little satisfaction in the conventional idea that the early process of rectilinear slip carries with it a generation of amorphous material. When an annealed metal begins to accommodate itself to an applied stress, movements either of simple translation or of rotation into twinning position occur and can be observed up to a certain point, as is well known. A coarse-grained and etched piece of zinc strip, for example, when stressed on the microscope stage shows instantaneous eruptions across the surface of a grain. Bands of variable, but usually quite appreciable, width leap across or up through the grain and lie inclined to the original horizontal place of the grain. Unquestionably, a movement in accord with the general symmetrical relationships within the grain has occurred: probably a movement into twinning position. It seems to me that any unsymmetrical disturbance of the molecules must have been confined to the grain boundaries where several systems meet and conflict. Should there not be an increase in the amount of amorphous material at the boundaries with every movement of this sort?
The movements of simple translation are also instantaneous and give the impression that blocks of material have jumped from one position of equilibrium into another. I would also expect these movements to effect some sort of dislocation at the grain boundaries rather than along the places of slip. As the stress builds up, these movements within the grain may well be expected to lose their simple character; perhaps the thickened or strengthened boundaries resist load from within and cause a kind of crumpling effect, which brings about a slight change of orientation from block to block within the grain. This is the beginning of a true fragmentation, which increases with the degree of deformation, and ultimately, after very severe deformation, produces fragments that in the case of brass, must measure more than 1,000,000 to the square millimeter because the first visible recrystallized units are at least as small as this.
I cannot see where our ordinary micrographic observations conflict with the above views. The first, stages of fragmentation are not visible because the changes in orientation within a grain are slight and the appearance of etching pits will not suffice to bring about a distinction between fragments of nearly the same orientation. It is my experience that, after severe deformation, the etching pits are similar in neighboring grains; they are no longer true etching pits and give no idea of orientation, as individual units of definite orientation are too small for observation. The original grain boundaries may be even more prominent than before deformation because they are likely to etch selectively as the principal seat of the most electropositive (amorphous ?) material in the conglomerate.
As near as I can judge, these views differ from Dr. Jeffries’ ideas only in one essential respect: he believes that, during the deformation of annealed material below the equicohesive temperature, material within a given grain begins to be reinforced against further deformation by the development of amorphous metal along the slip-planes, immediately after the elastic limit has been exceeded; whereas I believe that the first reinforcement occurs at the grain boundaries and that no reinforcement begins within the grain until the grain itself is broken down into fragments of varying orientation. That this latter effect begins very soon is evident from the small amount of deformation necessary to bring about a visible refining of the grain on subsequent anneal or a visible coarsening if conditions are such as to induce selective growth; viz., the elastic limit cannot be raised greatly by such deformation as merely brings about movements of simple translation, and this form of deformation can hardly play any prominent part in reinforcing the grain-substance.
Dr. Jeffries states that the principal difference between annealed and hard-drawn metal (copper) is in the quantity and the arrangement of the amorphous phase. Regarding the amorphous phase as something more of a transitional product, a little more crystalline and a little less amorphous, this suits my own conception of the difference between worked and annealed metal. However, my idea of the arrangement of the amorphous or sub-crystalline phase in worked metal confers upon the latter characteristics that would cause it to resemble what might be called abnormally fine-grained annealed metal; that is, equiaxed metal free from any possible strain complication and finer grained than can be obtained in any ordinary way.
I call to mind in this connection Bennett’s observations that hard-drawn copper can be deposited on a rotating cathode and likewise annealed copper by proper variation of current density, temperature, and speed of rotation. The tensile strength varied between 30,000 to 68,000 lb. per sq. in.; and although no photomicrographs were included, corresponding variations in grain size were especially noted. Hardness, slight ductility, and very fine grain were associated with high tensile strength; softness, pronounced ductility, and coarser grain, with low tensile strength.
Dr. Jeffries, in his experiments with copper at a given temperature, obtains higher strength and lower ductility in worked samples as the degree of deformation increases; with annealed samples he obtains higher strength and higher ductility as the grain size decreases. This association of high ductility with small grain size as exemplified by the quoted statement. “The elongation of annealed copper at all temperatures was less, the larger the grain size,” gets me into difficulty. In these particular experiments, metal was actually annealed before test at only two temperatures, 750° and 450° C., yielding a quite coarse and a very fine structure, respectively. Other conclusions are based on predicted changes of grain size as a result of annealing during test. In the case of iron, a sample annealed at 800° C., showing a considerably coarser grain than one annealed at 750° C., gives the lower elongation at any temperature of test.
It cannot be argued that all simple metals or solid solutions, when tested below their equi-cohesive temperatures, will become more ductile as their grain size decreases, because examples of a contrary behavior are very well known. Thus, throughout, a normal annealing range of several hundred degrees ordinary cold-worked 70/30 brass increases quite as regularly in ductility as it does in grain size. Beyond a certain temperature (which varies with the composition of the metal, the amount of surface exposed, the period of annealing, and the annealing atmosphere) the ductility commences to decrease although the grain size continues to increase. I have always attributed this to general deterioration of the metal, although certain other factors, such as the relation between area of section and grain size, may be of importance.
If it is assumed that a metal remains normal in all respects during the annealing treatment and if the grain sizes in question are small enough to more or less nullify the adverse effect of directional properties (premature break at a given section because directionally weak grains preponderate in that region), should not a decrease in grain size bring about a decrease in elongation for substantially the same reasons that an increase in the degree of deformation does? And should not this be a general property of all metals treated equivalently and tested below their equi-cohesive temperatures, so as to produce the effect of increasing reinforcement of the structure with the stiffer amorphous, material as the grain size or number of inner surfaces increases? Bennett’s copper, and brass at large, fit this argument. Jeffries’ coarse-grained copper is not anomalous, for, to use his own phraseology, “its elongation at the lower temperatures is less than ordinary annealed copper, because it has comparatively few grains on a cross-section.” Doubtless orientation had something to do with the low elongation.
There are no lack of reasons why coarse-grained structures might be expected to show impaired ductility. Such structures are usually produced by annealing at temperatures that may be regarded as high for the metal in question. So much in the way of mechanical stability depends on the grain or fragment boundaries that any cause tending to alter their nature or continuity should have a profound effect on ductility. Annealing at high temperatures may bring minute quantities of dissolved or intermixed substances into reaction with the evolution of gas, which should collect in the weakened boundaries. A little hydrogen and a little cuprous oxide would produce this effect in copper. It may actually volatilize metal from the boundaries.
Some of the experimental data reported by D. K. Crampton, in a recent thesis, have a certain bearing on this question. In these experiments, test pieces cut from severely cold-worked 70/30 brass, 1/8 in. thick, were first annealed in duplicate sets at a given temperature. One set was then rolled to a very slight reduction, after which both were re-annealed at a temperature lower than before. Selective growth occurred in the first set and, as both had received identical heat treatment, certain conclusions as to the effect of temperature and grain size on the strength and ductility could be made.
In both sets, maximum ductility occurred after anneal at 750° C.; that is, the effect of temperature was in general, greater than the effect of grain size. Selective growth at 750° C. produced about the same grain size (6.38 gr. per sq. mm.) as normal growth at 825° (6.08 gr. per sq. mm.) but the elongation, in 2 in., of the material annealed at the lower temperature was 84 per cent, as against 77 per cent, in the material annealed at the higher temperature. As these test pieces were annealed in air, there has, of course, been a complication of volatilization and oxidation at the surface of the metal. The ordinary relationships between mechanical properties and annealing temperatures of copper, brass, and other metals are so important that any theoretical effort that may lead to a better understanding of them may be regarded as well spent.
Some two years ago, in conversation with Dr. Jeffries, I called attention to the dissimilarity between copper and brass, in that while the former showed about the same ductility over a wide annealing range, the latter continually increased in elongation over a similar range and I found him ready with an explanation based on the amorphous theory. Using the theory in its present development, a given property—say elongation—will vary more with the grain size at room temperature in the case of brass than in the case of copper because the former is further from its equicohesive temperature than the latter; viz., crystalline and amorphous copper are more nearly alike in cohesion than crystalline and amorphous brass. Furthermore, as Dr. Jeffries has observed in the results of Mathewson and Thalheimer, there may be little difference in the grain size of copper over the annealing range in question. This appears to be rather common in the annealing of copper, at any rate changes in grain size with the temperature in the medium range of annealing are not striking as in the case of brass; which, of course, aids us to understand the test results.
In the upper part of the annealing range, the ductilities of both brass and copper diminish. In the lowest part, the ductilities again diminish; here there is perhaps room for some conflict of opinion.
I shall be greatly interested to learn whether Dr. Jeffries can agree with me that the ductility decreases as we pass from annealed metal, the grain size of which is still coarse enough to permit direct observation, into the range of worked metal where the term “fragment” may replace the term “grain,” mainly because of the decreasing size of particles, possessing the normal attributes of a crystal, whether they be called grains or fragments, and each surrounded by amorphous or subcrystalline material which supplies the reinforcement. The action in this case is very similar to the action originally described, wherein part of the reinforcement is due to amorphous metal along true slip planes. In either case the reinforcement raises the load that is necessary to further stretch the metal, while with additional stretch the resistance increases owing to the formation of more amorphous material, until finally the amorphous metal gives way locally and follows the line of least resistance through the metal. My interpretation, however, indicates a clear relation between ductility and grain size; very fine grain has a shorter road to travel before rupture than moderately coarse grain.
I do not mean to argue that there are no characteristic differences between a very fine-grained annealed metal and a coarse-grained metal that, by cold working, has become resolved into fragments similar in size to the grains of the annealed metal. There is certainly some form of internal strain associated with the worked metal. The two structures must represent a different distribution and probably different quantities of amorphous material; also a different scheme of orientation of the component grains or fragments. It has been suggested that the original grain boundaries have received additional amorphous material by the action of slip in this vicinity. Doubtless they continue to receive additions during their change of shape as the bar lengthens and very likely the fragment boundaries subsequently formed contain quantities of amorphous material more or less in proportion to their age. The characteristic irregular lines that develop when severely worked metal is etched seem readily explainable in some such manner.
The elongated and thickened boundaries are strong in tension but weak under certain other forms of loading. Thus a hard-rolled brass strip mounted lengthwise in a vise and bent back and forth fails much sooner than when mounted crosswise and the fracture follows the boundaries.
In spite of the differences thus noted, I believe that the two structural types just mentioned are alike in the main essentials and that the great change in properties brought about by cold working is due chiefly to an extremely thoroughgoing mechanical refinement of grain. We have in Messrs. Bassett and Davis’ paper some very carefully prepared data on grain size versus hardness in cartridge brass, which may be used to illustrate this point. Their coarsest grains count about 8½ per sq. mm. and correspond to a Brinell hardness of about 41, while the finest grains that could be reported with any certainty counted about 2000 per sq. mm. and raised the hardness to about 75. Beyond this, the structure could not be resolved for counting but my own examination of similar material has convinced me that grains that could count more than 1,000,000 per sq. mm. can be distinguished and these have grown out of an irresolvable environment of still greater fineness corresponding to a hardness of approximately 170. The count stands in the relation of 1:235:120,000+ and the hardness values: 1:2—:4+. From these figures it would appear that Brinell hardness is related to grain size through some exponential law:
The value of this constant appears to be in the neighborhood of 30.
Dr. Jeffries gives in this paper a more detailed account of his investigations on deformation, the results of which were indicated in a general way in his recent article on the Metallography of Tungsten, and we are indebted to him for the discovery of some very interesting and curious facts. Most important is his confirmation of Beilby’s experience that decrease of temperature would cause increase of ductility in copper. The possibilities of obtaining commercially valuable variations in the mechanical properties of wrought materials by working them at different temperatures are quite fascinating. But the greatest value of the experimental material of the author lies in its bearing upon the theory of plastic deformation in metals, and the author’s thought and speculation along these lines is original and highly illuminating.
We are, it seems, being gradually forced, by the facts presented in these papers of Dr. Jeffries, to a more careful analysis of such phenomena as ductility, tensile strength, and brittleness in metals than has been given these simple appearing concepts in the past. It may well be found that such complex phenomena as the author describes will reduce to very simple terms when our analysis has finally been completed.
Ductility, as the author points out, must depend primarily on resistance to rupture. All metals could be deformed if stresses great enough to produce deformation were not sufficient in some cases to produce first rupture. The mechanism of deformation in metals is well known in its general features. It occurs by progressive slipping along definite planes within each grain or crystal caused by shearing stresses parallel to those planes. The shearing stress per unit area of such a plane at which slip just begins is an important physical constant of the metal, and depends probably only on the temperature and the orientation of the plane in question. After slip has occurred along any plane, the regular arrangement of several layers of atoms or molecules at this plane has been disturbed; these layers are amorphous. Further slipping along this plane will occur under the action of shearing stresses, which will overcome the resistance of viscous flow of the amorphous metal; this stress probably depends on the rate of deformation or flow as well as on the temperature. The yield point of an aggregate of grains is a most complex function of both of these two limiting stresses and of the statistical orientation of the possible slip planes with reference to the direction of the applied stress.
Although we can thus form a fairly definite picture of the mechanism of deformation, we know comparatively little about that of rupture. Where does it occur and how? Does its path lie within amorphous metal or within crystalline metal? Does it occur simultaneously, or is there an initial local failure which rapidly and progressively develops into a complete fracture?
The author’s results throw some light on the location of the path of rupture. The increase of ductility and tensile strength of copper at lower temperatures indicates that the breaking strength of the metal at the path of rupture increases with temperature decrease more, rapidly than the elastic limit of the crystalline metal in shear. It is not readily conceivable that the breaking strength of the crystalline metal would do this; one would rather expect a less rapid increase of breaking strength than of elastic limit. It must therefore be the amorphous metal of which the alteration in breaking strength is the determining factor.
This conclusion brings with it a rather curious corollary that although below the author’s equicohesive temperature the elastic limit in shear along any crystal slip plane is less than the apparent elastic limit of the amorphous metal, the breaking strength in shear or tension of the amorphous metal must be less than that along any crystal planes other than those at which slip can occur. At the latter planes the breaking strength of crystalline metal cannot be determined as slip occurs with generation of amorphous metal before rupture.
The author’s discussion of the mechanism of rupture is interesting and he points out the significance of the probable fact that rupture does not occur simultaneously. He concludes, however, that, the area or intricacy of the path of rupture affects the measured breaking strength of an aggregate of grains of metal. This does not seem consistent with the first, conclusion, for the breaking strength is the maximum stress that a material will bear before fracture. If fracture during the ordinary tensile test is progressive, the first local failure within the mass causes a reduction of the test load and the maximum tensile stress has been measured before rupture has fairly begun. The path of the ensuing rupture can hardly have determined the maximum stress as so measured.
The rather curious conclusion is reached that the ultimate breaking strength, at least in tension, shear, or torsion, depends on the strength of the weakest part of the metal or on the value of the highest local internal stress or on both. It may therefore be related principally to: (1) the degree of uniformity of breaking strength of individual component elements of a mass of metal, or (2) the uniformity of the local internal stresses produced by the application of an external load. In this sense it would be chiefly a statistical characteristic of the particular mass of metal in question; i.e., of the orientation of its grains, etc.
This raises a question which has been in my mind for some time. In view of the quite obvious complexity of our supposed simple mechanical concepts and characteristics of metals, why should we not revert for our fundamental investigations of deformation to the methods of Osmond and others, and use for this purpose individual crystals or grains? I believe that our progress in the interpretation of mechanical phenomena in metals will be slow until this simplification is introduced, at least until certain fundamental facts are established.
It is difficult to find an explanation of the fact that although the tensile strength of both copper and iron increases as the temperature decreases from 300° C., the ductility of copper increases but the ductility of iron decreases. The author attributes this decrease of ductility of iron to the fact that internal stresses set up between the amorphous and the crystalline metal weaken the metal along the path of rupture. Yet the tensile strength does actually increase very rapidly and shows no indication of this weakening effect.
The author’s suggestion as to the cause of brittleness in tungsten at low temperatures as being due to internal stresses set up between the amorphous intercrystalline metal and the crystalline grains is interesting. If the rate of contraction on cooling of the amorphous metal is less than that of the crystalline metal below the equicohesive temperature, as the author believes, the system of stresses set up in a structure consisting of continuous thin walls of amorphous metal inclosing grains of crystalline metal on cooling would consist of a negative hydrostatic pressure within the grains, and within the amorphous envelopes tensional stresses normal to the envelopes and compression in all directions in their plane. Secondary stresses somewhat similar to shearing stresses would be produced at the boundary of envelopes and grains tending to strip envelope from grain, and thus to produce a weakening of the whole structure.
At present, there seem to be two schools in metallography, one which has adopted the amorphous-phase theory for the explanation of the effect of cold work, mechanical deformation, etc., and one which is not ready, at present to adopt this theory. It seems to me that this theory can at least be used as a convenient means of explaining various facts that are demonstrable in the laboratory but the presence of this amorphous material, through our lack of experimental means, we are unable to prove. That we have failed in this direction should not necessarily hinder us from using a theory that is as workable as this.
I understand Dr. Jeffries to say that fracture occurs between, the crystals at room temperature. According to the amorphous-phase theory, as originally expounded by Dr. Rosenhain, if I remember correctly, fracture occurs across the crystal. Now, is it true, assuming that we have amorphous material, that fracture always occurs in the amorphous material, whether that amorphous material is between the grains or in the grains along the slip planes? We have heard a very great deal lately about allotropy in iron, although those discussions had to do with the beta and gamma phases rather than the possible presence of low-temperature allotropy. So far as my interpretation of the curves given by Dr. Jeffries, showing the variation of tensile strength, elongation, and reduction at variable temperature, enables me to predict, the tensile- strength curve shows that the change takes place, speaking in degrees centigrade absolute, from 300° to 500°, the curve for elongation shows the change to take place from 300° to 400°; and the curve reduction of area shows that it takes place from 300° to 600°. In other words, there seems to be a lack of agreement as to the temperature range over which this allotropic transformation has taken place, depending on whether the determination is that of tensile strength, reduction of area, or elongation.
On page 83, the first sentence in the first paragraph reads: “The rate of transformation from one allotrope to another should depend on the cohesion of the metal at the temperature at which the change should take place.” This brings up the question of the rate of change of one allotropic modification into another allotropic modification, and the variation of that rate of change with temperature; and Dr. Jeffries brings up the question as to whether that change or rate of change depends on cohesion of the material. If it does—as we accept, of course, that as the temperature lowers the cohesion increases—we must assume a similar and corresponding increase in the rate of transformation of the one allotrope into the other allotrope. Prof. Tammann and collaborators have determined experimentally the rate of crystallization of various materials from their liquids; if we accept this work, we will see that the rate of generation of crystals of the new substance, as well as the linear velocity of crystallization or deposition about these crystal centers, is a function that varies in quite an irregular manner with the temperature. At least the variation in this function in temperature is quite different from the variation in cohesion. Prof. Tammann has shown that, at the equilibrium temperature, that is the temperature at which the two allotropes could coexist in stable equilibrium, the rate of formation of crystal centers of the new substance is practically zero. As the temperature drops to below the equilibrium temperature, there is a slow and then a very rapid increase in the rate of formation of the crystal nuclei; but very soon a maximum is reached, below which temperature the rate of formation of crystal nuclei takes an equally sudden drop. In other words, the rate of variation of the formation of crystal nuclei is entirely different with dropping temperature from that of the cohesion. If we are to consider the rate of transformation of the allotrope into another, we must take into consideration the work that Prof. Tammann has done.
One or two other points occur to me in this connection. If the rate of transformation varies directly with the rate of increase in cohesion, we would expect that at a very low temperature we would get a marked increase in the velocity of transformation. Accepting the view advanced by Prof Tammann, it would seem that, if temperature has such an effect and if we get a transformation at low temperatures that we do not get at the higher temperatures, we must look to some other cause as the explanation of it. It is true there is a transformation from austenite, that is, the high-temperature modification of steel into martensite at a temperature slightly above that of liquid air, and that point has been advanced by Dr. Hanemann, as a confirmation of the view Dr. Jeffries advances here; that is that the further we get from the true equilibrium temperature the greater will be the tendency to change. Dr. Guertler, in discussing this theory, pointed out that it was not at all necessary, in fact it was quite contrary to the generally accepted belief, for the rate of transformation to increase with temperature. I believe that these points have an important bearing on the effect of deformation of iron in particular because, as Dr. Jeffries says, there is a possibility of there being a low-temperature allotrope.
I should also like to ask Dr. Jeffries if he performed his experiments on both rising and dropping temperature. When we investigate allotropic transformations, we usually investigate them in both directions; the transformation should take place in one direction on heating and in a reverse direction on cooling. If there is a true allotropic transformation, it is quite necessary that there be hysteresis; if these transformations take place in the reverse direction on cooling from that in which they occur on heating, but the temperature at the beginning of the transformation is lower on cooling than on heating, there will be a strong foundation for the assumption of allotropy. But if the tensile strength, reduction of area, etc. of iron, at some certain temperature, for example 200° C., are the same whether approached from below or above that temperature, we will have a temperature effect as distinguished from an allotropic effect and the change in properties that takes place over this range cannot be considered as due to allotropy or due to a phasial transformation. I assume that Dr. Jeffries is considering here a definite physical transformation, when he speaks of the variation in properties between 0° and 200° to 300°.
The discussions by Mathewson, Merica, and Hoyt reflect the same general view as that obtaining at present on evolution, namely, every one now believes in the general theory but there is much speculation regarding the precise steps leading up to the development of the higher forms of animal life. So too, the amorphous metal hypothesis of Beilby, Bengough, and Rosenhain and Ewen is now very generally accepted as the best working theory but there is and will continue to be much speculation as to the nature of contact between amorphous and crystalline metal, the thickness of the amorphous films and their exact distribution, especially in cold-worked metals.
For several years I have had the opinion that the amorphous films between equiaxed grains were thicker in fine-grained than in coarse¬grained samples and that the minimum thickness must be greater than 100 atoms. There are several reasons for the above beliefs and I hope to have some experimental evidence soon. An amorphous film one atom thick (as would be expected if surface tension forces alone predominated) is entirely inadequate to account for certain properties.
With reference to Dr. Mathewson’s discussion on the relation between grain size and elongation, I might refer to the statement near the top of page 72, “It would not be surprising if all metals at any given temperature would have maximum elongation and reduction of area with a certain small grain size, and either smaller or larger grains might produce less elongation or less reduction of area.” I had in mind here that the limiting condition with decrease in grain size would theoretically be reached only when the whole mass was amorphous. Certainly at low temperatures elongation would begin decreasing long before the metal reached this condition. I agree with Dr. Mathewson, in the main, on the relations between cold-worked metals and change of grain size in annealed metals. It is obvious that the shapes of grain fragments produced by deformation will be different from the shapes of grains in annealed metals and the shapes determine the position of the A metal, and the size and shape of grain or fragment determines the quantity of A metal. Several observations lead me to believe that the thickness of the A metal films at slip planes in deformed metal is greater than the thickness of the films between grains of annealed metal. If this is true the reinforcement would be greater in the former case.
The idea has been expressed, in a number of places recently, that cold-worked metals regain ductility on heating before recrystallization. The writer has never believed this and it is interesting to note that Dr. Mathewson does not. It may be true, however, that ductility is regained before visible recrystallization. It is highly probable that recrystallization has taken place whether or not evidence can be seen under the microscope and that restored ductility is a result of recrystallization. Dr. Mathewson’s formula relating Brinell hardness to grain size is extremely interesting. It would be as interesting to compare the relations between the tensile properties, and grain size.
With reference to Dr. Merica’s discussion, the writer mentioned in paragraph 7, of the Summary, that the maximum breaking load would be a balance between the two tendencies: rupture by degrees, which tends to lessen the maximum strength, and the increased path of rupture caused by deformation in ductile metals, which tends to increase it.
The matter of per cent, elongation in iron in liquid air is very perplexing. One annealed sample was stretched at room temperature 10 per cent, and then cooled to liquid air and it stretched 6 per cent, more before breaking. It should have elongated about 25 per cent, at room temperature and about 11 per cent, in liquid air if it had not, been elongated any at room temperature. This and other tests indicate that cold-worked iron has a tendency to be brittle in liquid air. We are not sure that iron at room temperature is completely in one allotropic condition. More experimental work is urgently needed to throw further light on this subject. Dr. Merica’s suggestion that more experimental work be done on single crystals is most timely.
Prof. Hoyt’s ideas on allotropic transformation do not differ markedly from mine. It is probable that the force tending to produce the allotropic change is zero at temperatures higher than that at which it is perfectly stable on heating, and that the force-tending to produce the change on cooling increases with decrease in temperature. There will be a temperature not far below that at which the change should take place on cooling, which will produce the maximum velocity of transformation. That this is true is shown by many experiments on steel, water, silver, and silica. Water and silver may be undercooled (silver as much as 70° and water 17° C.) before the change from the liquid to the solid state begins, if the materials in the liquid states are maintained in a very quiet state; then solidification takes place more rapidly than if undercooling had not taken place. The most rapid transformation in carbon steels occurs at a temperature about 100° lower than that at which it would occur on slow cooling.
Austenitic manganese steel will apparently remain in that condition at room temperature indefinitely. At (375° C., however, the change from austenite to martensite occurs after a few hours and if the austenite is deformed at 400° C. the transformation proceeds far enough in a few minutes to make the steel magnetic. This shows that mechanical disturbance of the atoms by deformation favors this transformation.
Silica and glass at room temperature will remain in the amorphous state indefinitely; but when heated to high temperatures for prolonged periods they crystallize. It therefore seems that the mechanical cohesion resists allotropic transformation. The change from austenite to martensite in high-carbon steels, brought about by cooling in liquid air, does not fit in with the above ideas but it is true that we know less about this change than the others cited above.
So far as I know, no work has been done on the relative positions of the maxima and minima points of the tensile properties of iron on both rising and falling temperatures. This line of investigation should prove interesting.