Sample Size: Each container has a total capacity of 2.4 liters. To avoid spilling any sample, each container should be filled with a volume of 2.2 liters, or less. Therefore 12 containers with 2.2 liters will have a total volume of 26.40 liters (6.97 gallons, .9323 CF).
Table Rotation: The optimum table speed is between 12 and 20 RPM’s. By running the table at higher speeds, the sample tends to bounce off of the rotating containers, and lands outside of the sample collection containers. Optimal rotation is obtained by adjusting the variable speed table rotational control, from 20% to 100%.
Adjustable Feed Spout: The gap between the feed spout is adjustable from between 1/8″ to 2″ gap, between the hopper and the bottom of the feed spout. The gap should be set larger than the largest size particle being split. The adjustable feed spout may be used to shut off the flow of material, by placing in its lowest position, resting against the bottom of the feed tray. Material Feed Rate The vibrating feeder, with a 3″ wide by 16″ long mild steel pan has a maximum capacity of 2 tons per hour. At a feed rate of 50 pounds per hour, it will take 2 minutes to empty the hopper (based upon 100 lbs/CF material density).
Inspection: When the splitter is received, it should be inspected to be certain no damage has occurred to the unit in shipment. All items should be checked against the packing list to be certain that all components have been received. In the event any damage or shortage in shipment is found, a claim should be filed with the delivery carrier and a report should be submitted.
Operation: The rotary sample splitter is designed and manufactured to give accurate (+/- 1%) splits of representative samples, consisting of dry, flowable material. The largest particle size the splitter will adequately handle is 1/2”, so the particle range is 1/2” x 0. The solids are placed in the feed hopper. The table rotation is turned on, and the rotation speed is adjusted by sight, to where one thinks particles will not bounce around when hitting the container edge, with the default to slower than faster. The feeder is now turned on, and adjust the speed where the material is flowing into containers, again, with the default towards slower than faster. Once speeds are initially adjusted, make note of the setting for table rotation and feeder speed (0 to 10 on the dial). Do not change the speed during a sample run, run the sample through the machine at the set speed. The easiest method of roughly checking the accuracy of the splitter settings is to weigh each container full of split material. The containers should be numbered (markers work nicely) for identification. Empty each container and weigh the empty container. Sub- tract the weight of the container from the weight of the container and sample. The difference is the weight of the sample in the container. The 12 containers should not vary in weight more than + or– 1% of the total sample weight (sum of all 12 containers sample weight). If weight differs by more than 1%, adjust the speed of the feeder and or the feeder, and try again. (Usually slower speeds improve performance), and try again. Note that all splitter containers are not equal in weight, so each will have to be weighed to determine the weight of material in the container. Note that coarse material (1/4” to 1/2”), may cause a nugget effect, when combined with mostly 10 mesh material. By trial and error, a set of ideal speeds can be determined for many various types of material split, and if records are likewise maintained, they may be set each time the splitter is used to split similar materials.
Materials of construction: All structural parts are constructed of mild steel. The table is laminated wood with a Formica top. The sample containers are 304 SS and passivated. All mild steel parts are prepared and painted with one coat of enamel.
Lubrication: The worm gear should be inspected at 120 day intervals, by draining/siphoning a sample of oil from the case to determine that excessive gear wear is not occurring (evidenced by high concentration of metal shavings in the oil). At first site of contaminated oil, the oil should be drained and replaced immediately. Under normal circumstances, the gear oil should be replaced annually as a preventive maintenance procedure. For gear and worm gear lubricant, use petroleum based gear oil with EP additives. Bearings should be lubricated with a suitable high quality NLGI #1 or #2 multi-purpose grease.
Table Diameter: 24″
Hopper Size: 2.2 CF
Container Size: 2.4 Liter
Number of Stainless Steel Containers: 12
Voltage required 110 V/1 Ph/60 Hz or 220 V/1 Ph/50 Hz The sample splitter should be placed on a stable, flat surface. Appropriate electrical connections should be made. The stainless steel sample containers should be placed on the carousel table top in the manner indicated on the product literature, enclosed. The table rotation should be started by turning the variable speed control knob to about 35% and adjusting it to obtain 12 RPM’s. Next, the vibrating feeder should be started, and adjust the feeder to a very slow feed rate of approximately 50 to 100 lbs. per hour, (at 100% it feeds 2 TPH). Fill the feed hopper with 24 liters of material (Maximum) [approximately 100 pounds of sand sized quartz]. Allow the feed hopper to empty before stopping the feeder or table rotation. After the feed hopper is empty, stop the table rotation and remove the filled containers. Each container should now contain a representative sample of the material in the hopper.
Sample Size Sample Size Each container has a total capacity of 2.4 liters. To avoid spilling any sample, each container should be filled with a volume of 2.2 liters, or less. Therefore 12 containers with 2.2 liters will have a total volume of 26.40 liters (6.97 gallons, .9323 CF).
Table Rotation The optimum table speed is between 12 and 20 RPM’s. By running the table at higher speeds, the sample tends to bounce off of the rotating containers, and lands outside of the sample collection containers. Optimal rotation is obtained by adjusting the variable speed table rotational control, from 20% to 100%.
Adjustable Feed Spout The gap between the feed spout is adjustable from between 1/8″ to 2″ gap, between the hopper and the bottom of the feed spout. The gap should be set larger than the largest size particle being split. The adjustable feed spout may be used to shut off the flow of material, by placing in its lowest position, resting against the bottom of the feed tray.
Material Feed Rate The vibrating feeder, with a 3″ wide by 16″ long mild steel pan has a maximum capacity of 2 tons per hour. At a feed rate of 50 pounds per hour, it will take 2 minutes to empty the hopper (based upon 100 lbs/CF material density).
Inspection When the splitter is received, it should be inspected to be certain no damage has occurred to the unit in shipment. All items should be checked against the packing list to be certain that all components have been received. In the event any damage or shortage in shipment is found, a claim should be filed with the delivery carrier and a report should be submitted to Sepor, Inc.
Operation The rotary sample splitter is designed and manufactured to give accurate (+/- 1%) splits of representative samples, consisting of dry, flowable material. The largest particle size the splitter will adequately handle is ½”, so the particle range is ½” x 0.
The solids are placed in the feed hopper. The table rotation is turned on, and the rotation speed is adjusted by sight, to where one thinks particles will not bounce around when hitting the container edge, with the default to slower than faster.
The feeder is now turned on, and adjust the speed where the material is flowing into containers, again, with the default towards slower than faster.
Once speeds are initially adjusted, make note of the setting for table rotation and feeder speed (0 to 10 on the dial). Do not change the speed during a sample run, run the sample through the machine at the set speed.
The easiest method of roughly checking the accuracy of the splitter settings is to weigh each container full of split material. The containers should be numbered (markers work nicely) for identification. Empty each container and weigh the empty container. Subtract the weight of the container from the weight of the container and sample. The difference is the weight of the sample in the container. The 12 containers should not vary in weight more than + or- 1% of the total sample weight (sum of all 12 containers sample weight).
If weight differs by more than 1%, adjust the speed of the feeder and or the feeder, and try again. (Usually slower speeds improve performance), and try again. Note that all splitter containers are not equal in weight, so each will have to be weighed to determine the weight of material in the container.
Note that coarse material (¼” to ½”), may cause a nugget effect, when combined with mostly – 10 mesh material.
By trial and error, a set of ideal speeds can be determined for many various types of material split, and if records are likewise maintained, they may be set each time the splitter is used to split similar materials.
Materials of construction All structural parts are constructed of mild steel. The table is laminated wood with a Formica top. The sample containers are 304 SS and passivated. All mild steel parts are prepared and painted with one coat of enamel.
Lubrication The worm gear should be inspected at 120 day intervals, by draining/siphoning a sample of oil from the case to determine that excessive gear wear is not occurring (evidenced by high concentration of metal shavings in the oil). At first site of contaminated oil, the oil should be drained and replaced immediately. Under normal circumstances, the gear oil should be replaced annually as a preventive maintenance procedure.
For gear and worm gear lubricant, use petroleum based gear oil with EP additives. Bearings should be lubricated with a suitable high quality NLGI #1 or #2 multi purpose grease.

Spare Parts for 040J-001
Catalog Number
|
Description |
QTY Needed
|
040J-T001 |
24″ Rotary Splitter Frame |
1 |
040J-T002 |
Spindle 24″ Rotary Splitter |
1 |
020A-001-318S |
Feeder 3×18 T42112-001 • 115/60 |
1 |
GR-F71350B5J |
Gearbox F713-50-B5J • 50:1 |
1 |
MO-098002 |
¼hp 90V 1750RPM 56C |
1 |
040J-C009 |
2.4L SS Container Complete |
12 |
CNT-7200-006-A |
Feeder Controller |
1 |
CNT-174307.00 |
DC Table Controller |
1 |
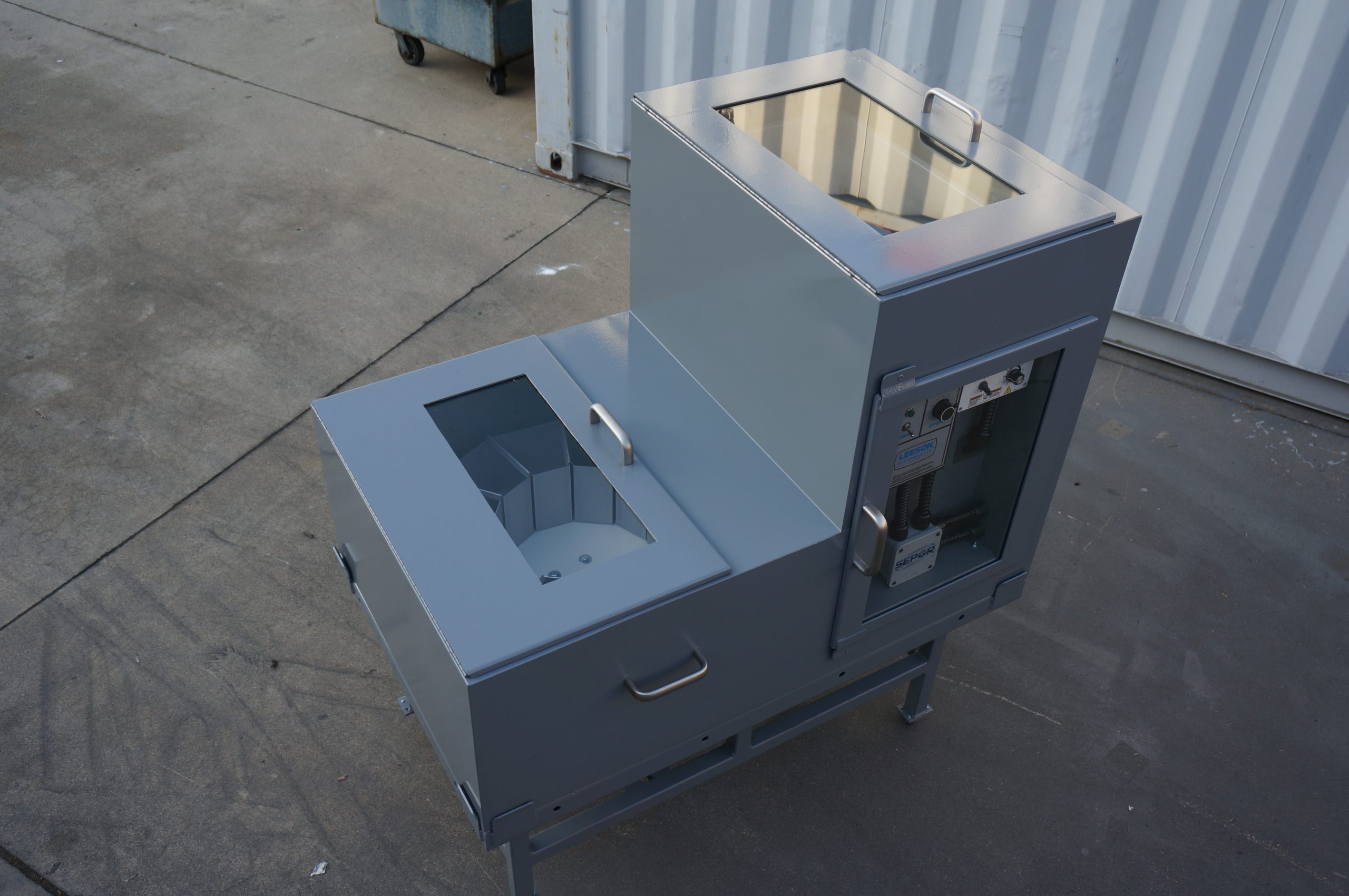