ULTRAFINE GRINDING USING AN ATTRITION GRINDING MILL
In recent years the consumption of nonmetallic industrial minerals has increased substantially. Concurrent with this general increase is the rise in demand for finely divided mineral filler materials. Simply defined, “a filler is an inert material that is included in a composition for some useful purpose.” Fillers are used, for example, on compounding paints, plastics, linoleum, and rubber products. Size specifications for industrial mineral fillers vary greatly, depending primarily on the particular end purpose and, to a great extent, the physical properties of the mineral itself. Generally, some method of particle size reduction is employed in preparing the raw material for use as filler-grade product. Size reduction of industrial minerals usually is obtained by conventional crushing and grinding methods. However, specialized comminution techniques are required for some minerals such as mica that show a refractoriness toward conventional crushing and grinding procedures. During recent years the Bureau of Mines has been investigating an attrition method of grinding to produce ultrafine mineral particles. The Bureau-developed attrition-grinding process, which has been patented, comprises the intense agitation of a slurry composed of the material to be ground, a relatively fine granular grinding medium, and a suspending fluid. The process has been shown to be effective for the comminution of kaolin in the sub- sieve particle size range on a batch and continuous basis.”
This report presents the results of batch testing six minerals to investigate the effectiveness of the attrition-grinding process in producing fine-size mineral products. Using a statistically designed experimental program to make preliminary trials for establishing trends, the batch tests were made on mica, pyrophyllite, talc, marble, barite, and fluorite.
EQUIPMENT AND MATERIALS USED
Attrition Grinder
The batch grinding tests were made in the Bureau’s 10-inch-diameter attrition grinder, which is described in detail in an earlier report. The unit, as assembled for batch testing, is shown in figure 1. The grinder consists of a rotor and stator fabricated of carbon steel and assembled in a vertical, cylindrical container. Referring to figure 1, the cylindrical container or grinder proper (C) is rubber lined. In the grinder, the cagelike rotor (G), built with vertical bars, rotates inside the cagelike stator (H), which is also constructed with vertical bars. The rotor is turned by shaft (E) attached to a 5-horsepower motor (B). Connected to the motor drive shaft is an electric clutch (A) for the controlled application of torque when starting under load. In batch testing, the feed is placed in the grinder by removing the top cover (D). After grinding, the pulp, which consists of the

material to be ground, water, and sand, is discharged by washing it through the central opening (F) at the bottom of the container (C).
Samples Tested
The industrial minerals used in the investigation were obtained from industrial operations. The samples included two mica products and one each of pyrophyllite, talc, marble, barite, and fluorite. Each sample was screened to remove plus 35-mesh material. By using minus 35-mesh material for the grinding tests, recovery of the ground products from the sand grinding media was facilitated. For benefit of the reader, sizing analyses of the minus 35-mesh materials are given in the sections dealing with each of the individual minerals. All particle size determinations reported herein were made by screening and sedimentation methods. The sedimentation method was a modified application of an ASTM procedure. The procedure yielded particle size analyses in the micron range based on calculations made using equivalent spherical particle diameters. All particle size analyses below 44 microns (325-mesh) that are reported herein are given on the basis of an equivalent spherical diameter (esd).
Brief descriptions of each of the products tested, with their true and bulk densities, are given in table 1. The true densities, which were used for calculating charge volumes and sizing constants, were determined by an air pycnometer. All bulk densities were determined with a Scott Paint Volumeter that has a 1-cubic- inch receptacle and the deagglomerating screen in place.

EXPERIMENTAL WORK
To investigate the extent of size reduction obtainable on the minerals studied, batch tests were made in the Bureau’s 10-inch-diameter attrition grinder using a statistically designed 4 by 4 Latin Square test program. The planning and analysis of the experiments were made using the procedure out-lined by the National Bureau of Standards to make preliminary tests for investigating the large effect of the variables studied. The tests were made to investigate the influence of (1) percent solids of the mineral-water feed pulp, (2) amount of sand grinding medium in the charge, and (3) size of the sand grinding medium used on particle size reduction, bulk density of the ground product, and electrical energy consumed during grinding. In designing the test program, it was assumed that there was no interaction between the three independent variables. Optimization of grinding conditions for the various minerals was not an objective of the investigation since a specific test campaign with additional tests would be required to obtain these data.
In the tests reported herein, Ottawa sand, which is essentially spherical in shape, was used as the grinding medium. Constants for the four levels of each variable investigated are given in table 2. Inasmuch as the test charges were based on a constant operating volume, the quantity of mineral and sand added varied for each of the samples tested because of the differences in the densities of the minerals. Depending on the total pulp density of the charge, the peripheral rotor speed ranged from 1,400 fpm in dilute pulps to about 1,350 fpm in the dense pulps. Unless otherwise indicated, the tests were made using a 30-minute grinding period with tetrasodium pyrophosphate added in the amount of 6 pounds per ton of mineral feed as the pulp dispersant. Gross energy consumed by the grinder motor was determined by a recording wattmeter and by periodic voltage and amperage readings taken during the tests. Owing to the small size of the grinder, the energy consumption data presented in the report are relative values obtained for the purpose of comparing results of tests made under different conditions.

Mica
Sample A
A sizing analysis of a representative sample of mica product A is given in table 3. The results of the 16 grinding tests made on this mica are given in table 4.
The data revealed that comminution of the mica through 325-mesh was appreciable, and with the exception of tests 11, 12, 14, 15, and 16, all of the ground slips contained more than 82 percent of minus 325-mesh particles. Particle size reduction of the mica at the 2-micron range also was appreciable. The coarsest product contained 10.3 percent of minus 2-micron particles; the finest product contained 48.3 percent of minus 2-micron mica. Mathematical analysis of the data demonstrated that best particle size reduction of the mica through 325-mesh would be approached when grinding sample A with sand in the minus 8- plus 10- or minus 10- plus 14-mesh particle size range at a sand-to-mica weight ratio of 2.5 or 3.0 to 1. Statistically, the greatest production of minus 325-mesh material would be obtained when the pulp density of the mica feed was maintained at 20 or 30 percent solids. Analysis of the data, based on the 2-micron content of the ground products, gave the same results regarding the size and quantity of sand used for grinding as those when considering only the cumulative minus 325-mesh size analysis. However, the analysis did indicate that pulp density of the mica feed had no influence on the production of minus 2-micron material.
Interpretation of the extrapolated values for the electrical energy consumed in grinding a ton of mica feed revealed that the most advantageous utilization of electrical energy was obtained when comminuting the mica at a feed pulp density of 50 percent solids while using either the minus 8- plus 10- or minus 10- plus 14-mesh sand.


The bulk densities of the ground products ranged from 9.8 to 20.5 pounds per cubic foot and appeared to be a function of the particle size of the mica. Analysis of the test results indicated that lower bulk density products would be obtained when grinding at pulp densities ranging from 40 to 50 percent solids, at sand-to-mica weight ratios of 2.5 or 3.0 to 1, and using either of the two coarser sand fractions tested.
From a compilation of the analyses, it was construed that best particle size reduction with least energy consumption would be obtained when grinding mica sample A at a mica feed pulp density of 50 percent solids, with a sand- to-mica weight ratio of 3.0 to 1 and with minus 10- plus 14-mesh sand. Sizing analysis of a test made using these conditions, with the sizing analysis of the raw mica feed for comparative purposes, is graphically shown in figure 2.
The test results substantiated the mathematical interpretation of the data. The curves in figure 2 show that the feed, which contained 11.1 percent of minus 325-mesh material and essentially no minus 2-micron mica, was ground to a product containing essentially 100 percent minus 325-mesh mica and 52.3 percent of minus 2-micron particles. The electrical energy consumed by the
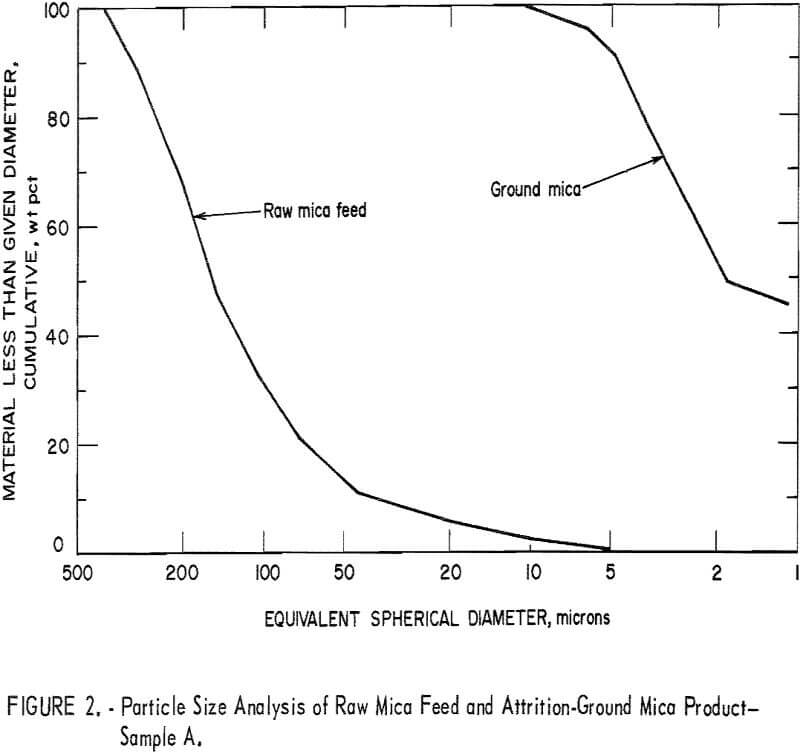
grinder motor was 304 kilowatt-hours per ton of dry raw feed. Based on the amount of new 2-micron mica produced, the electrical energy consumption was about 581 kilowatt-hours per ton. The bulk density of the ground product was 9.9 pounds per cubic foot.
Sample B
Given in table 5 are the results of a sizing analysis made of a sample of mica product B, a high-density mica. Recorded in table 6 are the test results made of this mica to establish the relationship .between the three variables tested and particle size reduction, bulk density, and the electrical energy consumed during grinding.
The data recorded in table 6 show that with the exception of tests 11, 12, 14, 15, and 16 all of the ground products contained more than 80 percent of minus 325-mesh mica. Comminution of the mica at the 2-micron particle size range also was appreciable. Analysis of the data revealed that, as when grinding mica sample A, best particle size reduction of mica sample B would be approached when grinding with sand in the minus 8- plus 10- and minus 10-plus 14-mesh particle size range at a sand-to-mica weight ratio of at least 2.5 to 1. Greatest production of minus 325-mesh material was again found to occur when the pulp density of the feed was maintained at 20 to 30 percent solids. Similar trends were observed when analyzing the data based on the amount of minus 2-micron material produced.
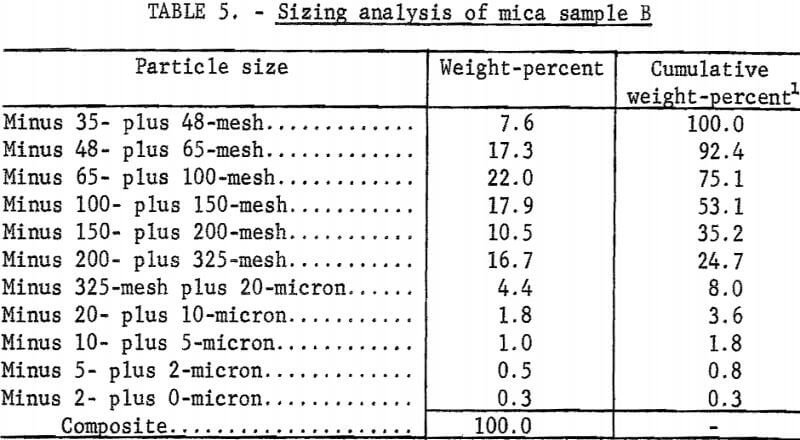

Statistically, the most advantageous utilization of electrical energy was obtained when comminuting mica sample B at a feed pulp density of 50 percent solids and using either minus 8- plus 10-mesh or minus 10- plus 14-mesh sand.
Bulk densities of the ground products were unexpectedly low, ranging from 11.1 to 26.1 pounds per cubic foot. The data again indicated that low bulk densities appeared to be a function of the particle size of the ground products.
Analysis of the data revealed that best particle size reduction with least energy consumption would be obtained when comminuting mica sample B at a feed pulp density of 50 percent solids, a sand-to-mineral weight ratio of 3.0 to 1, and with minus 10- plus 14-mesh Ottawa sand. A graphical presentation of the size distribution of a sample of mica sample B, ground using these conditions, is shown in figure 3. For comparative purposes, the sizing analysis of the raw mica feed is also shown
The results of the test substantiated the mathematical interpretation of the data. Figure 3 shows that mica sample B, which contained only 8.0 percent of minus 325-mesh and 0.3 percent of minus 2-micron particles, was ground to a product containing 100 percent minus 325-mesh mica and 56.8 percent minus 2-micron material. During the test, the electrical energy consumed by the motor was 320 kilowatt-hours per ton of dry raw feed. On the basis of a ton of new minus 2-micron material produced, 565 kilowatt-hours was required. The bulk density of this ground product was 11.4 pounds per cubic foot.
Pyrophyllite
Recorded in table 7 is a sizing analysis of the pyrophyllite used in the investigation. The results of the programmed tests are given in table 8.



The data indicated that comminution of the pyrophyllite was rapid. In each of the 30-minute tests the feed, which contained 27.2 percent of minus 325-mesh material, was ground to a product containing 100 percent of minus 325-mesh particles. The data also show that with the exception of test 16, the ground products contained from 80.2 to 100 percent of minus 10-micron material. Comminution of the pyrophyllite at the 2-micron particle size range was appreciable. Statistically, it was found that best particle size reduction of the pyrophyllite sample would be approached when grinding the material at a sand-to-mineral weight ratio of 3.0 to 1, a pulp density of 40 percent solids, and using either minus 10- plus 14-mesh or minus 14- plus 28-mesh Ottawa sand as the grinding medium.
The data further indicated that least electrical energy consumption per ton of pyrophyllite would be obtained when grinding the sample at a pulp density of at least 40 percent solids and using either of the two coarser sizes of sand.
Bulk densities of the ground products were low, ranging from 10.3 to 14.6 pounds per cubic foot. Analysis of results indicated that products having low bulk densities would be obtained when grinding the pyrophyllite feed at a sand- to-mineral weight ratio of 3.0 to 1 using the coarser size sand fractions. Statistically, there was no significant difference in the bulk densities of the ground products when pulp density of the feed was varied.
The data also revealed that best particle size reduction of the pyrophyllite would be approached when grinding at a mineral feed pulp density of 40 percent solids using a sand-to-mineral weight ratio of 3.0 to 1 and with either minus 10- plus 14-mesh or minus 14- plus 28-mesh Ottawa sand as the grinding medium. Test 7, recorded in table 8, was made using the conditions outlined above with minus 10- plus 14-mesh sand. For comparative purposes, a test was made at 40 percent solids with a sand-to-mineral weight ratio of 3.0 to 1, using minus 14- plus 28-mesh sand as the grinding medium. The sizing results of this test and test 7 of table 8 are graphically shown in figure 4. The sizing analysis of the feed product is also shown.
Figure 4 shows that grinding with the minus 14- plus 28-mesh sand gave slightly more particle size reduction of the pyrophyllite than that obtained when grinding under the same conditions with minus 10- plus 14-mesh sand. Both tests, however, yielded the finest pyrophyllite products obtained in the test series. Grinding with the coarser sand yielded a product containing 61.1 percent of minus 2-micron particles, whereas grinding with minus 14- plus 28-mesh sand gave a pulp containing 64.3 percent of minus 2-micron pyrophyllite. The raw material contained only 1.6 percent of minus 2-micron particles. Bulk density of the ground material from both tests was 10.8 pounds per cubic foot. Electrical energy consumed when grinding with the minus 14- plus 28-mesh sand medium was somewhat higher than that obtained with minus 10- plus 14-mesh sand; 274 kilowatt-hours per ton of raw feed were consumed when grinding with the finer sand, whereas 260 kilowatt-hours were consumed when using the coarser material.
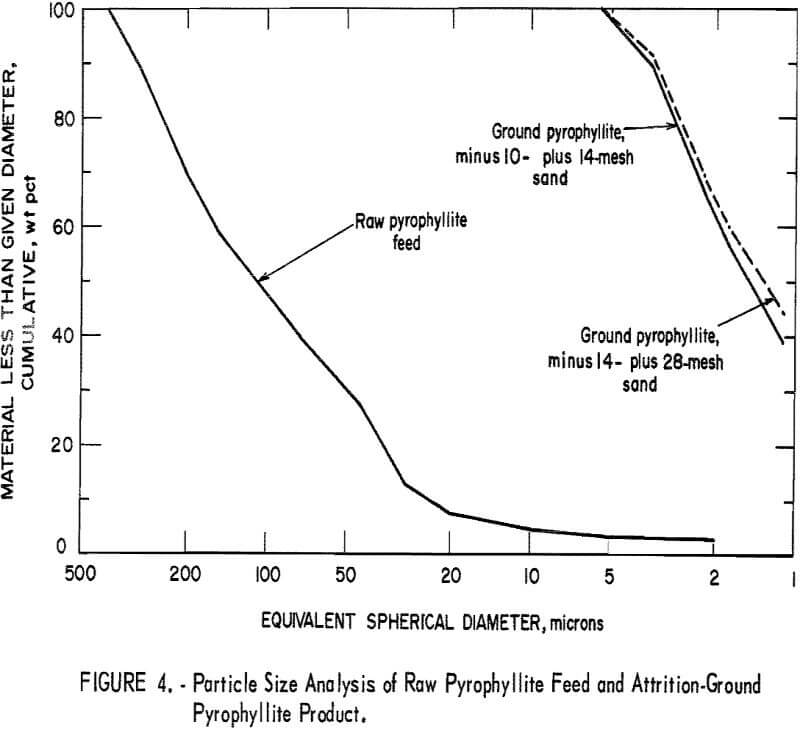
Talc
A sizing analysis of the sample of talc used in the investigation is given in table 9. Recorded in table 10 are the results of the 16 grinding tests made of this material.
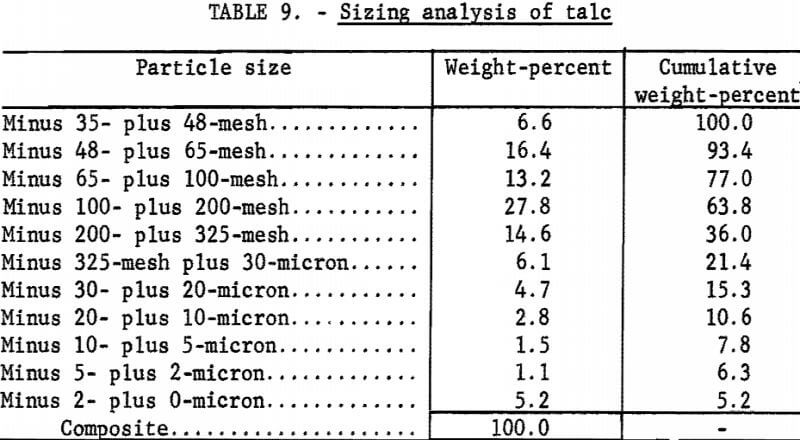

The test results revealed that the comminution of the talc through 325- mesh was essentially complete. With the exception of tests 1, 2, and 16, all of ground slips contained 90 percent or more of minus 10-micron material. Particle size reduction of the talc at the 2-micron range also was appreciable. The coarsest product contained 32.1 percent of minus 2-micron talc. Evaluation of the data demonstrated that best particle size reduction of the talc in the 2-micron range would be approached when grinding with minus 14- plus 28-mesh sand at a sand-to-talc weight ratio of 2.5 to 1. Statistically, greatest production of minus 2-micron talc would be obtained when the pulp density of the talc feed was maintained at 40 percent solids.
Most advantageous utilization of electrical energy per unit of feed was achieved when grinding at low sand-to-mineral weight ratios, using high-pulp- density feed pulps, and with the coarser sand size fractions. In most of the better tests recorded in table 10, the electrical energy consumed did not exceed 300 kilowatt-hours per ton of talc feed.
Bulk densities of the ground products were extremely low, ranging from 10.9 to 15.7 pounds per cubic foot. The data indicated that a low bulk density product would be obtained when grinding at a talc feed pulp density of 40 percent solids, with a 2.5 to 1 sand-to-mineral weight ratio, and using minus 14- plus 28-mesh Ottawa sand as the grinding medium.
In summary, analysis of the data revealed that best particle size reduction of the talc with least energy consumption would be approached when comminuting the material using a sand-to-mineral weight ratio of 2.5 to 1, a 50-percent-solids talc feed pulp and with sand in either the minus 10- plus 14-mesh or minus 14- plus 28-mesh particle size range. Test 8 (table 10) was made using the indicated conditions with minus 10- plus 14-mesh sand. For comparative purposes, a grinding test was made of the talc using the indicated conditions with minus 14- plus 28-mesh Ottawa sand. A graphical presentation of the sizing analysis of the ground product, in addition to the sizing analysis of test 8 in table 10 and the raw talc feed, is shown in figure 5.
As shown in figure 5, grinding with the finer sized sand gave a somewhat greater minus 2-micron content than that of grinding with the coarser sand; 63.3 percent as compared with 61.4 percent of minus 2-micron particles. However, overall particle size reduction was slightly greater when grinding with the coarser sand size. The minus 10- and minus 1.5-micron content of the ground products was greater when comminuting the talc with the minus 10- plus 14-mesh grinding medium than when grinding the feed with the minus 14- plus 28-mesh sand. The bulk density of both ground products was 11.2 pounds per cubic foot. Electrical energy consumed when grinding with the minus 10- plus 14-mesh sand medium was slightly lower than the energy required to grind the talc with the finer sized sand, 244 kilowatt-hours and 271 kilowatt-hours per ton of talc feed, respectively.

Marble
A sizing analysis of the marble used in the investigation is given in table 11. The results of the 30-minute grinding tests made on this sample are given in table 12.


The data show that regardless of the conditions of trial, each of the ground products contained more than 93 percent of minus 325-mesh material. The feed product contained only 19.4 percent minus 325-mesh marble. Comminution of the marble at the 2-micron particle size range was also appreciable. Statistical analysis of the data, based on the production of minus 2-micron material, demonstrated that best particle size reduction of the marble would be approached when grinding the feed material with minus 14- plus 28- or minus 28- plus 35-mesh sand media, and at a sand-to-marble weight ratio of 3.0 to 1. Best production of the minus 2-micron was predicted to occur when the pulp density of the marble feed was maintained at 50 percent solids.
The most advantageous utilization of electrical energy was obtained when grinding the marble at a 50-percent-solids feed pulp, with the coarser sand sizes and the lowest sand-to-mineral weight ratio.
The bulk densities of the ground products ranged from 21.8 to 28.4 pounds per cubic foot. The data indicated that low bulk density products would be obtained when grinding a marble feed pulp containing 40 to 50 percent solids at a sand-to-mineral weight ratio of 3.0 to 1 and with either minus 14- plus 28- or minus 28- plus 35-mesh sand.
From a compilation of the data, it was determined that best particle size reduction of the marble with least electrical energy consumption would be obtained when attritioning the marble at a feed pulp density of 50 percent solids, a sand-to-marble weight ratio of 3.0 to 1, and with either minus 14- plus 28- or minus 28- plus 35-mesh sand. A graphical presentation of the size distribution of two marble samples ground using these conditions is shown in figure 6. For comparison, the sizing analysis of the raw marble feed is also shown.
Figure 6 shows that grinding the marble with minus 28- plus 35-mesh gave slightly more particle size reduction than that obtained when grinding under the same conditions with minus 14- plus 28-mesh sand. Grinding with the coarser sand yielded a product containing 91.6 percent of minus 2-micron particles, whereas grinding with minus 28- plus 35-mesh sand yielded a pulp containing 95.2 percent of minus 2-micron marble. The raw material contained virtually no minus 2-micron particles. Bulk density of the material ground with the finer sand fraction was 20.6 pounds per cubic foot, whereas the bulk density of the material after being ground with the coarser sand fraction was 21.1 pounds per cubic foot. Electrical energy consumption per ton of marble feed was slightly higher when grinding with the minus 28- plus 35-mesh than when attritioning the marble with minus 14- plus 28-mesh sand-339 kilowatt- hours compared with 322 kilowatt-hours.

Barite
Results of a sizing analysis made of the barite tested are given in table 13. Data from 30-minute grinding tests of the barite are given in table 14.


The results of the 30-minute grinding tests revealed that regardless of the conditions of trial, the barite in each test was ground to pass 20 microns. Analysis of the data indicated that a statistical difference in test conditions regarding the particle size reduction of the barite could not be established until the 1-micron content of the ground products were compared. The mathematical analysis demonstrated that best particle size reduction of the barite at the 1-micron particle size range would be approached when attritioning the product with minus 14- plus 28-mesh sand at a sand-to-barite weight ratio of 3.0 to 1. Greatest production of minus 1-micron barite was shown to occur when the pulp density was maintained at 40 and 50 percent solids.
The most advantageous utilization of electrical energy was found to occur when comminuting the barite at a feed pulp density of 50 percent solids and using.sand in the minus 10- plus 14-mesh particle size range.
The bulk densities of the ground products were relatively low, ranging from 26.6 to 30.6 pounds per cubic foot, as compared with the feed product, which had a bulk density of 125.6 pounds per cubic foot. Analysis indicated that the low bulk density products would be obtained when grinding the barite at a pulp density of 40 to 50 percent solids, with a sand-to-mineral weight ratio of at least 2.5 to 1, and using minus 14- plus 28-mesh sand as the grinding medium.
To establish more reliable data regarding the grinding conditions most suitable for optimum particle size reduction of the barite, tests of a 15-minute duration were made. Results of the statistically designed experiment are given in table 15. The grade of the finished product in weight-percent is given on the basis of the 1- and 10-micron content to compare the results of the 15-minute tests with those of the 30-minute tests given in table 14.

The results of each of the 15-minute grinding tests demonstrated that the barite was ground to pass 325 mesh regardless of the conditions of trial. Analysis of the data revealed that greatest particle size reduction of the barite at the 10-micron particle size range was approached when grinding a barite feed pulp to 40 percent solids at a sand-to-mineral weight ratio of 3.0 to 1 with minus 14- plus 28-mesh Ottawa sand. A similar trend was observed when analyzing the sizing data at the 1-micron particle size range. In general, the trends established regarding particle size reduction in the 15-minute tests agreed favorably with those observed in the 30-minute grinding tests.
Electrical energy consumption in the 15-minute tests, based on a ton of feed, was lowest when grinding at a feed pulp density of 50 percent solids and at a sand-to-mineral weight ratio of 1.5 to 1. Statistically, minus 10- plus 14-mesh sand gave most efficient utilization of electrical energy. These findings agreed with the observations made in the 30-minute grinding tests.
The bulk densities of the products obtained in the 15-minute tests were, as expected, somewhat higher than those obtained in the 30-minute tests. The products ranged from a low of 28.8 to a high of 34.3 pounds per cubic foot. The analysis of the data agreed with the analysis made of the 30-minute tests in that low bulk density products would be obtained when grinding the barite at a pulp density of 40 to 50 percent solids, with a sand-to-mineral weight ratio of at least 2.5 to 1, and using minus 14- plus 28-mesh sand as the grinding medium.
Statistical analysis indicated that best particle size reduction of the barite with most efficient utilization of electrical energy should occur when grinding the material using minus 14- plus 28-mesh Ottawa sand as the grinding medium, a sand-to-mineral weight ratio of 3.0 to 1, and with either a 40- or 50-percent-solids barite feed pulp. Using the indicated conditions, two tests were made of the barite, the first at a 40-percent-solids barite feed pulp and the second at a 50-percent-solids barite feed pulp. Sizing analysis of the ground products from the tests in addition to the sizing analysis of the raw barite feed are graphically shown in figure 7.

The sizing analyses show that comminution of the barite feed was considerable, and differences in the results of the two grinding tests was almost negligible. In the test where the barite feed pulp was maintained at 40 per-cent solids, a product containing 85.0 percent of minus 10-micron barite and 64.6 percent of minus 1-micron barite was obtained. The test in which the barite feed pulp was maintained at 50 percent solids yielded a product containing 84.6 and 64.2 percent of minus 10- and 1-micron particles, respectively. The bulk densities of the two ground samples were the same, 28.7 pounds per cubic foot. Based on electrical energy consumption, the test made at 50 percent solids yielded the best results. In this test 169 kilowatt-hours of energy were required per ton of feed, compared with 190 kilowatt-hours per ton of barite when grinding a barite feed pulp containing 40 percent solids.
Fluorite
A sizing analysis of the fluorite flotation concentrate used as the feed to the attrition grinder is given in table 16 and the results of the grinding tests are given in table 17.
The results of the tests revealed that comminution of the fluorite at the 5-micron particle size range was appreciable; all of the ground products contained more than 85 percent of minus 5-micron particles. Particle size reduction of the fluorite at the 2-micron range also was appreciable. The coarsest product contained 59 percent of minus 2-micron material. Statistical analysis of the data demonstrated that the greatest particle size reduction of the fluorite in the 2-micron range would be approached when grinding the material with sand in the minus 14- plus 28-mesh or minus 28- plus 35-mesh particle size range, at a sand-to-fluorite weight ratio of 3.0 to 1. Greatest production of minus 2-micron material was shown to occur when the pulp density of the fluorite feed was maintained at 50 percent solids.
The mathematical evaluation indicated that the most advantageous utilization of electrical energy would be obtained when attritioning the fluorite at a feed pulp density of 50 percent solids with minus 10- plus 14-mesh sand.


The bulk densities of the ground products, ranged from 18.1 to 21.4 pounds per cubic foot. The mathematical interpretation of the data indicated that low bulk density products would be obtained when attritioning a fluorite feed pulp containing 50 percent solids, with a sand-to-mineral weight ratio of 3.0 to 1, and using either minus 14-plus 28-mesh or minus 28- plus 35-mesh Ottawa sand as the grinding medium.
Based on the statistical analysis, two additional tests were made of the fluorite product. One test was made using a sand-to-fluorite weight ratio of 3.0 to 1, a fluorite feed pulp containing 50 percent solids, and minus 10-plus 14-mesh Ottawa sand as the grinding medium. The other test was made using the same conditions but with minus 14- plus 28-mesh Ottawa sand as the grinding medium. Sizing analyses of the two tests with the sizing analysis of the raw fluorite feed product are shown graphically in figure 8.
Figure 8 shows that grinding with minus 14- plus 28-mesh sand gave slightly more particle size reduction of the fluorite at the 2-micron size range than that obtained when grinding under the same conditions with minus 10- Plus 14-mesh sand. Grinding with the coarse sand yielded a product containing 92.0 percent of minus 2-micron particles, whereas grinding with minus 14- plus 28-mesh sand yielded a pulp containing 93.8 percent of minus 2-micron fluorite. The raw material contained only 10.5 percent of minus 2-micron

particles. Bulk density of the material ground with the finer sand fraction was 18.0 pounds per cubic foot; bulk density of the fluorite ground with the coarse sand fraction was 18.1 pounds per cubic foot. Electrical energy consumed when grinding with the minus 14- plus 28-mesh sand medium was somewhat higher than the energy required to grind with the minus 10- plus 14-mesh sand 306 kilowatt-hours per ton of fluorite treated as compared with 293 kilowatt-hours per ton of feed.
Conclusions
Batch laboratory scale tests showed that the Bureau-developed and patented attrition-grinding process was successfully used for ultrafine grinding of the industrial minerals mica, pyrophyllite, talc, marble, barite, and fluorite. Statistically designed test programs made for investigating large effects of the variables studied indicated that the materials could readily be comminuted with relatively low electrical energy requirements to very fine subsieve size products that have low bulk densities.
Interpretation of data from the tests indicated that generally the best conditions for particle size reduction and lowering of bulk density for each material with the least amount of electrical energy consumption was obtained when grinding with higher feed pulp densities, with a greater amount of sand grinding media in the charge, and with coarser sizes of sand grinding media.
Because of the different physical characteristics of the minerals, some minor exceptions to the generalized results were observed when evaluating certain specific grinding responses such as particle size reduction. For example, particle size reduction obtained when grinding marble and barite was greater when intermediate to finer size grinding media were used. Also, results from both mica samples showed that particle size reduction was greater at lower feed pulp densities. Despite these deviations, the generalized results held true because of the broad evaluation made on all results of the grinding.
To optimize the grinding conditions for each material, a more comprehensive test program designed to incorporate additional tests with those already completed would be required.