So, most of you who are attending today are affected in some way by regulations of consumer products or hazardous substances in consumer product manufacturing. Today we’ll be giving you two of the big regulations: RoHS and CPSIA. We’ll talk about how as a manufacturer or importer subject to regulation you can set up a testing plan to help mitigate the risk associated with regulation. And lastly we’ll cover use of XRF as a screening method, especially as part of a production testing plan. Also, I just want to mention that nothing in this webinar should be construed as any sort of legal advice. We’ll go over the regulatory landscape and talk about key elements of the testing program, but every manufacturer’s requirements are different, and we’re not making specific recommendations about any individual should have in their testing plan. So first I’ll turn things to Joe Langton from Intertek to tell us about his company.
We specialize in XRF and XRD testing equipment, primarily for in-situ analysis, meaning we provide instruments for where the testing is needed. The emphasis is on developing applications where you can bring the analyzer to the sample rather than have to bring the sample to the analyzer. Innov-X has been part of Olympus since 2010, we’re part of the analytical instrumentation group. Our headquarters is just outside of Boston, Massachusetts and we have over 10,000 XRF analyzers in the field for a whole range of applications, including especially for consumer products testing. And now Jiaxin will give us an update on the current state of RoHS and CPSIA.
So today we’ll focus on the two regulation updates. RoHS we talked and CPSIA. First, let’s take a look at RoHS. As we all know, ROSS – the restriction of hazardous substances in electronics was adopted in February 2003 by the EU and took effect on July 1st 2006. Both the original RoHS include the same 6 elements and compounds: lead, mercury, chromium, PBB and PBDE, the brominated flame retardant – restriction level is 1000 ppm. Cadmium has a much tighter level in 100 ppm. For RoHS the most noticeable change would be the two of the 11 categories: category 8 medical devices and category 9 monitoring and control equipment. These two categories have benefitted to some extent status but will be brought into scope 3 years after the date of entering the enforcement. Also pay attention to the category 11: this new category serves as catch-all. Because of this very broad categorization, one should refer back to the existing definition of electrical and electronic equipment and realize that everything not expressly exempted would be subject to RoHS under the provision of the [05:14] specific timeline for compliance, such as for category 8 medical devices and monitoring and control equipment. Members should ensure the compliance for that after July 2014. For category 9, they should be in compliance after July 2017. Products in category 11 have 8 years after entering into force to comply with RoHS which is 2019.
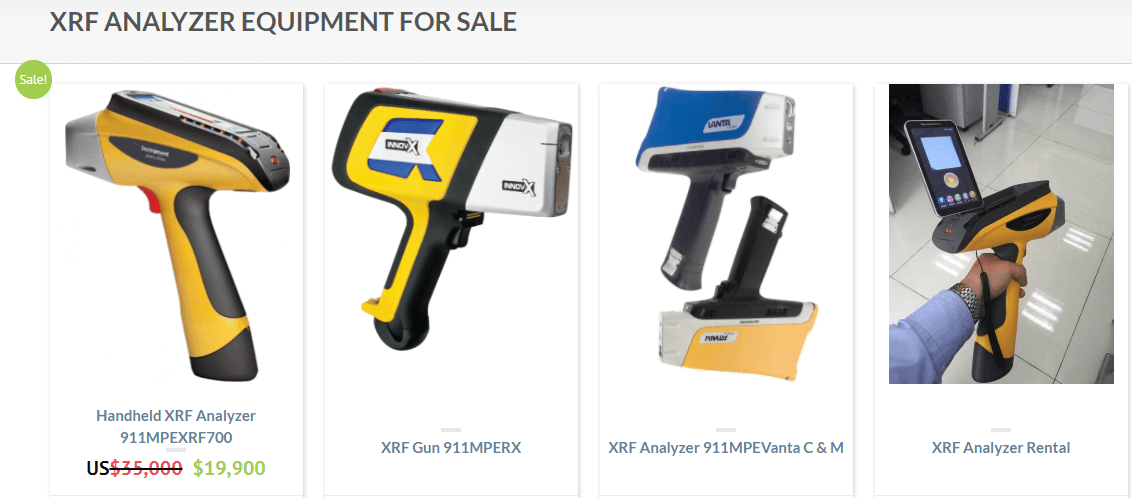
Next, let’s have a brief review on CPSIA. So, last year CPSC decided to drop the lead content limit to 100ppm in August. Since that, there were two more related final rules that have been approved. One is conditions and requirements for relying on component part testing group, and the other is testing and enabling pertaining to product certification rule. Within this rule, the third-party testing rule is the center of the discussion. The component the rule mentioned that responsible projects, issue with CPSC as part of the certification or GSS – General Conformity Certification based on the component report certifications. So the finished product should be certified partially or entirely based on the test reports for the individual component. For instance, if you manufacture children’s clothing with zippers and your zipper supplier has certified them for lead, you can use the report to support your certification on the finished product. But remember: when you apply this rule you should exercise your due care which means you receive with due and ensure the providence of the documentation. Also, you need to keep the records and make sure it is traceable. In addition, when there is a material change such as change in design, manufacturing process or suppliers you need to recertify the product.
For third-party testing, it’s only applied to the children’s products which are defined or intended primarily for children 12-years age or younger. It covers toys, children’s clothing and a few other product categories. So you may ask – who are responsible for the certification? So, only importers and domestic manufacturers are the two parties that are responsible for the GCS or CPSC. When you look at the chart you find that children’s products must undergo third-party testing while non-children’s products can be certified by a reasonable testing program. To ensure continuing product compliance, it is required that the children’s product be sent to the lab periodically. The minimum required to send interval will vary based on what the preorder position in place. If you have no other preorder testing in place, which means you are only controlling your business by sending the samples to the lab, the maximum testing interval is up to 1 year. It is two years if you have a production testing plan or reasonable testing plan in place. And a maximum of every 3 years if you have an in-house ISO accredited lab. Of course, a number of factors listed in the regulation will have impact on your final decision.
So, why do you need a reasonable testing program? A reasonable testing plan can be used to certify for non-children’s products under CPSIA can help assure compliance and demonstrate due diligence for RoHS and at the same time it helps you save costs for children’s product testing. The CPSC guidance documents are as we mentioned before the testing and enabling pertaining to production certification room management that you might send off fewer samples if you create finished product that are unit for composition and quality to provide a high degree of assurance of compliance to achieve that reasonable testing program could be one of your options. And again, you can send a sample to the lab with less frequency with a RTP program in place, which can save you both time and money, most importantly control the resources. Of course, the cost savings effect here is subjected to a list of factors under the rule.
Other than CPSIA and RoHS, reasonable testing plans can be applied to many more important regulations around the world, such as California Proposition 65, EU reach, etc.
So in the next section of the presentation we’re going to talk about the steps involved in putting together a reasonable testing program. Part of the step is we wanted to find the goals and the criteria and then outline the process steps. The overall goal of a reasonable testing program is to provide reasonable assurance that the product or the end-product or the material meets more applicable requirements. Not only existing safety and customer requirements, but also new requirements related to non-restrictive substance. And how can we implement XRF and utilize it as part of this program? We recommend that all elements of an overall compliance scheme should be part of an existing quality management system or an environmental management system. Your supplier management is the key step in any testing process. Part in component compliance is always the responsibility of your supplier, but you need to assess your supplier’s risk to determine what needs to be tested because of any gaps in supplier control.
The three main steps of a reasonable testing program is assessing requirements, verifying those requirements and then making your claims if your product is green or any type of eco labeling or marks that you require on your product. As far as assessing requirements, we want to make sure we assess not only customer requirements, but also regulations. Regulations specifically for restricted substances. It is key again to know your supplier’s process for assessing restricted substances as well. Once we get into the verification certification step, we want to know what material needs to be tested. If your supplier does not have a robust system or cannot produce compliant documentation, testing will be needed at your facility for either subcontract lab. We also want to make sure we want to choose the proper test methods and inspection techniques and everything needs to also be documented as far as procedures and processes. Once these steps are in place, we can then better make claims if a product is green or any environmental claims that the requirements have been designed to.
Additional elements under assessing requirements and verifying steps, we need to understand additional elements and criteria to develop the process steps required for a RTP. We need to supplement what is known about our components and material. Is there a risk that a restrictive substance is present? Can we test components further upstream in the supply chain to reduce the cost of the final product testing? And again, what is the frequency to mitigate as much risk as possible? We need to select the best techniques for testing, we recommend starting with XRF for screening because this may enable you to reduce most costs as far as lab testing at a final product stage. And again, always follow standards. There’s test methodologies that are available, they are published by the IC, or CPSIA, ASTM, whatever you requirements specify.
So again, to summarize the criteria for a testing program: again, we need to provide reasonable assurance that the product meets all requirements. We need to determine the type of testing that is needed, XRF screening is used to detect restrictive substances, lab testing is always used to confirm inconclusive based on our XRF screening. The final frequency depends on the material and product and always used methods and procedures that are industry standard. Additional requirements that you may apply to your product or material, product specifications. Always use product specs to determine what materials may contain a restrictive substance and compare these specifications to applicable safety rules, whether they’re CPSIA, RoHS or whatever other standards that may be applicable. We also want to assess market and customer drivers. Does a customer have a specific restricted substance list that he requires you to test or be compliant to, to define substances beyond CPSIA or the RoHS requirements?
Once the criteria and the requirements are defined and understood, process steps can be developed. On this slide, these are the steps we recommend. They may not be applicable to any situation, but we feel that these are the proper steps needed to put in a reasonable testing program. Identification of applicable requirements, again we spoke of market drivers, regulatory requirements and possible RSL if necessary. Always have procedures which we refer to as compliance assurance system or process within your own manufacturing facility as well as within your supply chain. Employee-vendor communication and training is always key as well, as well as supplier data collection. GAP assessment is always performed as part of our program within the supply chain as well as manufacturing facilities. Once these steps are implemented and we have a robust system, we can then be assured we’ve done the best due diligence to make our product claims.
Reasonable testing programs should always be part of what we call an overall Compliance Assurance System. The Compliance Assurance System is very similar to existing quality management systems or EMS’s that you may have in place in your organizations. We recommend that reasonable testing procedures should always be implemented into the product utilization process which is defined by the ISO standards. Moving on to specific types of tests that are required or are maybe part of your program is production testing, can be component testing, before final assembly, it may contain XRF for screening. When certification testing is needed, this requirement would fulfill any needs for the IC, CPSIA or GCS requirements as needed as well. Always make sure corrective action is available as well, in case they’re in a plant for containment and recourse analysis. And again, always document process steps.
Specific types of testing that we use when we’re doing it are reasonable testing program, of course. We spoke of XRF screening. XRF is the best method for screening for RoHS heavy metals, whether it be for RoHS or CPSIA for lead, and also for the presence of bromides. But again, chemical testing must always be part of your program to verify any inconclusive as a result of your XRF screening. There are also small off the shelf methods that you can use for screening techniques for heavy metals, chromates, cadmium and lead. But again, chemical methods must also be used for quantifying any of the heavy metals when XRF results are inconclusive or there’s uncertainty in the reading using XRF. These test methods are always in a laboratory environment, are the best and have the lowest detection limits available.
Another additional test when testing for phthalate – phthalate are a requirement under CPSIA for children’s products. XRF cannot detect phthalates. Lab testing is the only method that’s available for detecting phthalates in your product. A real-life example that we use every day here within Intertek as part of our green leaf program and it is an example of a reasonable testing program is this very simple process, 3-step process where we review documentation from suppliers. We assess BOM’s, drawings, material decorations and test reports. If we identify any high-risk substances as part of this review, we then move that on to a testing phase. We always do a process audit. The process audit identifies gaps when substances are processed. XRF is always used to detect residual substances in material as well as contamination on the production floor. Third step is always lab testing to verify any inconclusive or detect any substances that XRF has limitations in detecting. And then once we complete the process, we can issue our certifications once we’re satisfied with the results. At this point I want to hand it off to Brendan where he’ll talk more about the XRF equipment and how it can be used within the testing program.
So, as we heard so far, the verification step in a reasonable testing program includes a few key elements such as auditing, certification testing and screening. Screening usually takes place in the form of production testing plan that’s deployed based on a manufacturer’s assessment of risk. When drawing up a production testing plan, a manufacturer or other responsible party can decide what samples can be tested, what kind of testing would be done, how frequently testing will be done and what would be done if a failing test is found. All of these are decided based on analysis of risk, so where are you most likely to catch failures and what is your greatest exposure to non-compliance? Among the testing methods that are available for production testing, XRF is the most powerful tool that’s likely to be used in-house. Most manufacturers don’t have an in-house wet chemical lab available for testing in most cases.
We talked a bit about XRF now. I think many of the attendees are familiar with XRF already, but for those who aren’t: what is XRF? XRF or X-ray fluorescence is a technique for measuring elements in a sample. The principle is that if you expose a sample to X-rays, the elements in the sample will send X-rays back at different energies. The X-rays that go into the sample come from an X-ray tube which you can sort of think of as a light bulb for X-rays. The X-rays that return have, from the different elements in the sample that go back to the analyzer, have different energies or wavelengths which you can think about as having different colors. It’s not exactly the same thing, but the analogy sort of holds. A detector in the analyzer collects all of these X-rays and software on the analyzer can translate that information into what elements are present, and how much of those elements are present.
The user sees a readout on the screen of the analyzer or on attached computer on what elements are present and the concentration readout might look something like this. So what this means is XRF is a pretty powerful and non-destructive technique to identify and measure the elements in almost any sample type. If we start with a periodic table of the elements like we have here, XRF can be used to measure any element that’s highlighted here with magnesium on up. This makes XRF useful in production testing where regulations like RoHS are directed towards restricted elements: lead, cadmium, mercury and other hazardous elements. XRF is well-suited to detecting those elements in a variety of materials.
So, let’s say you’re considering XRF screening as part of your testing program or you have an XRF analyzer already but you want to use it more effectively. There are a few things you want to keep in mind before you get started. First, you need to determine what you’re going to test. So to determine that you want to start with the items of biggest risk. Where is most XRF most likely to find non-compliant materials? You’ll want to look for materials that are likely to contain restricted elements, just to give a few examples: some brass alloys may have some grade specifications have percent levels of lead or lead can make it into alloys as an impurity in some of the raw materials. They might be an area you’ll focus more on. Solders are materials that historically have contained lead in different formulations. Plastics that have high recycled content, may have a greater likelihood of containing restricting elements than virgin plastics, depending on sourcing. I don’t mean to pick on any of these materials, the risks vary based on what kind of products you’re making. But these are just some of the examples of things you’d want to look for in deciding where to focus your efforts in production testing.
You’ll also need to determine screening levels. The XRF analyzer will give you a ppm or percent result for the elements that are present but you need to decide how that result will translate into a pass or fail decision for that part or material or component. There are standard methods available to help you with that as Joe mentioned: IEC 62321 is a pretty common one that gives some guidance on how to set up screening levels based on XRF results and here’s an example of one that’s specifically for testing of homogenous plastic materials under the RoHS regulations.
So, the IEC also recommends having a buffer zone around your screening levels and that’s known as the uncertainty budget. That’s what the IEC document calls it – the ‘uncertainty budget’. The uncertainty budget is the sum total of all of the limitations of your technique limits on sample preparation, limits based on what calibration you’re using. May include possible user error and if your results fall within that area of uncertainty you may need to do additional testing in order to ensure your product is compliant or be sure your product is not compliant. Notice also that bromine and chromium are treated differently in this testing scheme. Bromine and chromium, again this testing scheme is for RoHS specifically, those two elements are not restricted elements. They’re restricted in certain chemical form, so chromium is restricted as hexavalent chromium and bromine is restricted in certain flame retardants. XRF can tell you the total elemental content for these elements, but it can’t tell you what chemical form they’re in or what molecules they’re bound in. So you can use an XRF to see results for those elements to say that a sample passes if you have a very low result for those elements, but if you detect higher levels of those elements you may need to do some additional testing.
So there are a few merits to using XRF as well as some cautions that we’ll go over. First of all, XRF testing is quick: your testing times are on the order of seconds to minutes and you test for multiple elements simultaneously. This allows you to have higher sample throughput. You can test more samples by XRF than you could by most other methods, and faster testing means you get faster turnaround of results and you can make decisions faster based on those results. XRF is non-destructive, so you can preserve a sample for further testing either to send to a lab, or if it’s a case of high value manufacture, you can still sell the product after XRF testing.
XRF allows you to test in-situ which means that you can take your XRF equipment unto a production floor in a warehouse. You can test fixed equipment and if you have multiple manufacturing locations you can move the analyzer around. XRF can be used by non-technical users. The day-to-day operation doesn’t need to be done by someone who has a technical background. We do recommend that any end-user who purchase an XRF analyzer have a standard operating procedure in place for using the analyzer to make sure that it’s being used correctly and that the results are being interpreted correctly. But the day-to-day operation doesn’t need to be done by someone with a technical background. Results from XRF testing can form the basis of compliance documentation where third-party testing is not explicitly mandated so this doesn’t apply to children’s products under CPSIA. But it does apply to non-children’s products where you can produce a general certificate on conformity based on a reasonable testing plan where XRF is a part of that testing plan.
So, there are a few challenges, cautions and caveats to using XRF as a screening technique. XRF is a surface technique: it’s measuring the surface layer of your material. The penetration varies based on what kind of material you’re looking at, but if you have a restricted element that’s buried deeper in your sample, you may not detect by XRF or you may detect it at lower amounts. XRF is an elemental testing technique, so it’s great for testing lead, cadmium and other restricted elements, but as Joe mentioned, it’s not compatible with testing phthalates in materials or finding out what kind of flame retardant you have in your material. You need to use other testing methods to get that information.
You want to be familiar with what detection limit you are going to be seeing for your sample type and make sure that your screening level is realistic based on that detection limit. So as your organization is part of your production testing plan, you’ll decide on what screening levels you want to go with but you want to make sure you can reach those with the kind of XRF equipment that you have and the kind of samples that you’re testing. Detection limits do vary based on what kind of sample you’re testing.
You also want to make sure you understand the material that you’re testing and the regulations that apply. You want to know what your action levels are and what the exemptions are if there are any. There’s another example: RoHS has some exemptions for certain materials, for example steels have a higher lead exemption limit than the standard 1000 ppm. And so you want to make sure that you’re applying the correct action level to the material that you’re testing. You want to know the capability and limitations of the particular equipment that you have. There are a couple of specs of XRF equipment that I’ll go over briefly.
The X-ray tube in the analyzer that produces the X-rays operates at a given voltage, and the common ones that you’ll see are 40-45 or 50 kilovolts. This mainly has an impact on some heavier elements, specifically cadmium and antimony and a few other elements, but cadmium and antimony are the two big ones that are of concern in consumer product testing and your tube voltage, maximum tube voltage will have an impact. For other elements including bromine, mercury, lead and a few others, tube voltage doesn’t have as much of an impact on detection limits you can reach.
The detector and the analyzer, there are a few different kinds that are common, probably two of the most common that you’ll see are the silicon drift detector (SDD) or the PiN diode. The SDD is a bit newer technology, it has better sensitivity, higher performance, it can reach the lower detection limits that the PiN diode can. This is especially of help if you’re doing testing of a lot of metals. Usually detection limits for different elements are higher in metals than they are in lighter materials like plastic and so the SDD will help you a bit more. The PiN diode still works for a lot of applications but you want to make sure that the performance level that you can reach is going to match what your screening requirements are. Also, you want to make sure that you’re operating the analyzer safely. It is an instrument that’s based on using X-rays and the instruments can be used safely, they’re used safely every day. But you want to make sure that proper procedures are being followed so that users aren’t exposing themselves or others to X-rays.
Probably the biggest challenge in interpreting XRF results is looking at inhomogeneous samples. So, the analyzer’s calibration normally assumes that the material being tested is uniform and the elements detected are distributed homogenously. When testing a material made up of multiple different materials, the XRF result may not represent any one material tested, so in order to deal with that you want to test at the homogenous level as much as possible, as high up in the production stream as you can. For inhomogeneous samples your results are usually qualitative. You can see what elements are present and you can judge how much relative to other sample, similar sample types. But the ppm result that you see on the screen may not apply to any one material in that sample. Sample thickness can have some effect on your measurement, mainly by raising detection limits when samples are very thin. The IEC document that I’ve mentioned earlier has some recommendation for minimum sample thickness when testing by XRF for plastic materials, it gives a recommendation of 5 millimeters minimum thickness so you don’t want to go any thinner than that. If you do, be aware that your detection limits will be maybe higher.
It’s also very helpful to understand how your instrument is calibrated. XRF instruments usually come with several factory installed calibrations for different material types, so you may need to validate that calibration on your own sample types. Now, you can do this with reference materials, certified reference materials – CRMs – for your sample type, but there are a limited number of CRM suitable for XRF compared to the total volume of different sample types that people want to test with XRF. And this is one place where lab testing can be of big help in complimenting XRF. Most XRF analyzers will allow the user to adjust the calibration based on their own real-world samples and so if you have an independent test result from a lab for your own sample you can adjust the calibration to make sure that the XRF response matches whatever your independent test says.
In XRF we’re usually looking out for what are called matrix effects. These are the effects that most of the elements that are in your sample are having on the few elements that you’re actually looking for. Sometimes elements can interfere with each other, can raise detection limits or cause deviation in results. The software normally takes care of all of these, the calculation software that comes with the analyzer, but there’s some cases where you may want to be aware of what’s going on. Just as an example, if you’re testing for lead in brass alloys, some grades of brass alloys contain high bismuth content – because of some line overlaps, an alloy with high bismuth content will have a higher lead detection limit than an alloy with no bismuth content. And so if you see detection limits changing like that, that’s one thing to look for. Matrix effects, what kind of interferences are present.
So, XRF screening complements lab testing in a lot of ways. XRF allows for testing a much greater volume of samples than you could test by a lab, cast your net wider, look wider for non-compliant products. But at the same time, lab testing allows users to validate their XRF testing approach and make sure that procedures are being followed and that the correct decision, pass or fail is being made based on your XRF results. Also XRF results can become part of documentation. Most instruments will allow you to print a test report based on the results you got, and if your instrument is equipped with a camera, it can save a picture of the sample as well so you can see what you tested and for a larger item, precisely what location you tested on the sample. This can become part of your product documentation and can be useful down the road to demonstrate due diligence in testing if you should ever need to do that.
So, here are a few examples where XRF might fit into a reasonable testing program. With incoming part QC you specify ordering compliant parts from your vendors, but for new suppliers or for parts that contain materials that have historically been more likely to contain restricted elements, you may want to scrutinize those more closely. XRF is useful for inventory control if you’re ordering parts, similar parts that are both compliant and non-compliant, you can make sure that they’ve been sorted appropriately. This is mainly of concern if you’re a manufacturer who’s operating compliant and non-compliant manufacturing streams. This is less common than it was a few years ago just because of the prevalence of environmental consumer product regulation in the last few years, but if you do have multiple manufacturing streams you can make sure the parts are being sorted appropriately.
XRF is useful in process control. For example, if you check your raw materials and they are free of restricted elements but somehow restricted elements are being added to your product somewhere along the production stream, XRF is useful for pinpointing those sources. Checking heavy machinery, checking chemicals and solvents, trying to find out – I’ve seen cases where the raw materials don’t contain any restricted elements, but somehow they’re introduced along the way because of some procedure that’s being carried out. XRF can be used as a final QC check, test products before shipping. If you’re manufacturing low volume production, then you may be able to test every product you send out the door by XRF. With higher volume, you may do a more random sampling and for a larger item, larger component with XRF you can test multiple locations, multiple materials.
And so, we’re commonly asked what kind of detection limits can XRF reach down to compared to what the regulations are. So this is jus a very broad overview of what a typical XRF analyzer can reach, and this is based on a few of our products at Innov-X. And so you can see what roughly detection limits an analyzer can reach down to in different materials. You can see that for metals the detection limits are higher than they are for plastics. And also I mentioned earlier about the X-ray tube voltage that you’re using. 40 kilovolts versus 50 kilovolts – it’s mainly helpful for certain heavy elements that have what we call a higher energy emission line, and so the tube voltage will mainly have an impact on that. It won’t – 40kV vs 50kV won’t have as much of an impact on the other elements. Again, these are typical LODs based on ideal homogenous samples. They do vary based on application, so this is just to give you a broad overview of what sort of performance XRF can reach to.
And with that, I thank you all for attending. I hope you enjoy our talk about testing programs, regulation and XRF. And we’re happy to take any question you might have. I actually see quite a few have come in already. Ok, so I see one question here on can we provide any information about sampling plan for testing? I assume this is part of a reasonable testing program. Should that only include testing high-risk parts or medium-risk parts from high-risk suppliers and certain number or lot numbers from certain suppliers?
I guess it’s very difficult to kind of paint a broad brush over sampling plans, but typically what we like to do – in my case, if it’s any risk, I don’t like to use medium risk myself. If there’s a chance of risk then I test the product or test the component. I don’t tend to classify them into three classes: high, medium and low. There’s risk or there’s no risk. And typically, we like to use sampling plans that will enable us to sample at least one product in the batch. We like to use if anyone remember old AQL – melt standard AQLs, we would use a normal AQL at around 10 to make sure we test at least one product out of a batch. And when we get into higher batches again, we’ll test a few more samples. But again, we want to make sure we have enough data, collect enough data and statistics to then claim that the product is compliant and I can take it off that high risk list. So, again if any more information is needed on that question, you can always email me or anyone in the panel here, we can get some more information for you as far as specifics.
Ok, so we have another question on what types of product characteristics cause inconclusive results with XRF screening? There are a couple of different cases where you can get an inconclusive reading that might require additional follow-up testing, and also just to stress the inconclusive band needs to be decided by the manufacturer or whoever is setting up the production testing plan. It may be different for different manufacturers based on different kinds of samples that they’re testing. But a couple of examples of an inconclusive result are a result that’s very close to your legal action level, so the screening guideline that I showed earlier has a recommended broad uncertainty belt of about +/- 30% around your action level, so if you’re testing a sample for lead, and you see the action level is 1000 ppm, if XRF gives a result of 900ppm, that’s close enough to the action level that you’d want to do some kind of confirmatory testing to see if the product is compliant or not compliant. Also, if you’re testing for bromine and you test very high levels of bromine in your sample by XRF, that’s going to be determined as inconclusive because the XRF sees the bromine present, but it can’t tell you what chemical form the bromine’s in, and so it can’t tell you if that product contains the particular flame retardant that’s restricted by RoHS.
As far as the element, if you’re testing an element that’s very close to the action level, just on a practical level if a sample actually has 900ppm of lead in it when your legal action level is 1000, and that particular homogenous material has 900ppm, yes it’s compliant but you also need to ask do you really want to be accepting parts from that supplier that are so close to the legal action level? Does the supplier know how the lead is getting into that material and is there any way they can mitigate that? So yes, it’s true that that’s an inconclusive XRF result but you also sometimes need to take a step back and ask do you really even need to be in that situation to begin with?
Question about the surface effects of materials that are on the surface affecting XRF results. If the results on a metal can be affected by residual oil on the surface. This comes up a lot with any sort of surface coating. It really depends on what the surface coating is and what elements you’re looking for. With residual oil on the surface it’s usually not going to be a problem for most of the heavier elements that you’re testing for but if the oil contains wear metal content from some other source, that can interfere with the results. It’s usually best to clean your sample surface before testing but there are a lot of cases where you can test through a very thin surface layer. So the short answer is better to have a clean sample to be safer, but you may find there are cases where you don’t have to clean the sample based on your own testing.
Question about error measurement from the XRF analyzer. So the analyzer, when you’re testing by XRF the analyzer provides a measurement and an error. The error is the uncertainty on the measurement, and you get an uncertainty – you seen an uncertainty reading on any kind of analytical measurement you ever take. Any kind of analytical instrument will have some sort of uncertainty associated with it. And that’s the repeatability of the measurement based on the – based on statistical analysis if you’re familiar with the concept of Sigma. That’s one 1 sigma uncertainty. So it gives you some idea of if you run multiple tests on a sample, how much will the next result vary? You’ll get one test that’s 500 ppm, the next test probably won’t be 500 ppm exactly but it may vary. It will vary based on what the uncertainty is on that reading.
Another question on what would the process look like to screen an average laptop time number of samples, etc.
So we worked on similar situations and it really depends on what you’re looking for. Again, when you’re screening a laptop or a circuit board that’s already soldered and complete it’s going to be very difficult to get down to the level of components once they’re soldered. The small spot sizes, 3 millimeters on the end of X device… and you’re not going to be able to test down to that level. So you’re going to be able to screen for the certain substances whether it’s lead or cadmium, but you may get some inconclusive based on materials such as ceramics which do contain lead which have exemptions under RoHS directive. But we can screen a laptop, we can screen a computer or print circuit board. A typical laptop may take, depending on what we’re looking for, how many shots and how granular you want to get, anywhere from an hour to two hours and to do the analysis on what we found it actually takes a little bit longer than that to prepare a report and do the analysis. But again, it’s going to be a combination – I would suggest using a combination of XRF material datasheets that you have in your suppliers and as well lab testing. That’s going to be part of a reasonable testing program where you use all three methods.
For testing of stainless nickel and duplex alloy steels with high levels of chromium, what tube voltage is going to be preferred or better for that kind of testing? Of the options that I mentioned, 40-45 or 50, that’s the maximum spec for the tube voltage. It’s not going to matter much for chromium analysis. The voltage spec is just the maximum on the tube and the tube can always be run at lower voltages. This is something the user usually doesn’t have control over that setup within the analyzer software. But as far as the maximum tube voltage spec between the ones that I mentioned for chromium testing it’s not going to make much of a difference. We have a question about how long are we required to keep records?
Under the RoHS directive we are required to keep those for 10 years. I believe the CPSIA is just as long. We recommend that once you ship the product in the field that you keep those records on file somewhere for at least the life of the product if you can in the field, but the requirements under the RoHS directive is 10 years under the new RECAST.
For CPSIA I believe is 5 years right now, so you don’t need to translate everything in English but you have like 48 hours by request. So basically, you need to keep all the records for 5 years.
We have one question about XRF. Does the temperature of the sample affect results? Generally, no. XRF – the instrument will have some temperature range you can use it within, but the actual temperature of the sample doesn’t affect it. There are a lot of different applications for XRF, we’re been focusing on consumer products testing, but it is possible to test alloys in service, pipes for example, oil refineries that are hundreds of degrees Fahrenheit. You have to run very quick tests and you have to take some appropriate precautions to insulate the analyzer but it is possible to test those and that’s to make sure that the correct alloy or pipe is being used. It’s a completely separate application, but the short answer is no, there’s no effect of sample temperature on results.
There’s a question regarding if a product has a layer of oil that contains a heavy metal contaminate, should that be shipped to the customer that way? Should the sample be cleaned before testing? Typically this would be considered two homogenous substances: the oil and the alloy. And both should be tested separately if possible. XRF can be used to screen the entire product to determine if there’s a substance there. Again, if the heavy metal is detected, we would not know where that was coming from unless the oil is separated. So it’s possible if both homogenous substances can be separated before screening them, that would give you better, conclusive results. Question as far as handheld XRFs in warehouses receiving products from overseas such as China perform scans, this is one excellent application for XRF because it is portable. You can screen products before they’re shipped. It may save you some cost if there are any infringements or substances detected. And I know this is one of the major applications that’s being used for right now.
I see a good question on what’s the main difference in operation between an isotope scanner, XRF equipment with Cobalt 57 source versus an X-ray tube? I only talked about X-ray tube XRF in this talk. It is also possible instead of using an X-ray tube to use an isotope source to produce your X-rays. There are a few drawbacks to using an isotope source. You actually have a radioactive material in your analyzer which means there’s a different set, in most states and most countries it’s a different set of regulatory requirements that you have. There are in some cases greater restrictions on travel with the analyzer and there are some disposal concerns with using an isotope source. We don’t see isotope sources being used as much for consumer products applications. A lot of that has to do with the regulatory requirements where manufacturing is going on in so many different countries and in a lot of places the requirements are more stringent. As far as performance difference between those, an isotope source is always running at one particular energy and an X-ray tube has a maximum energy but it’s adjustable over a whole range so that generally gives you, in most application can give you better sensitivity over a whole range of elements.
The question about packaging material – how do you test packaging material for scanning? This is another restricted substance regulation that we didn’t talk about – there are packaging directives in Europe where the sum of elements, chromium, mercury, lead and cadmium have to be less than 100 ppm. One of the most difficult things with packaging materials is that your samples are really thin. So I mentioned earlier that there’s a recommendation for plastics, samples should be at least 5 millimeters thick and in a lot of cases you want to go even thicker than that if you can. So the first thing I would say with testing packaging materials is if your sample is very thin, you’re testing cardboard or plastic, plastic wrapping, try to make a thicker sample as much as possible and you can do that just by stacking multiple layers and wrapping it around a bunch of times. That you may see a great improvement on the results that you’re seeing.
Ok, I see one question that came in early on is there any danger to operators using XRF? Is there any need for certificates for using handheld XRF? And I addressed that a bit in my talk, but because XRF is a technique that relies on using X-rays you need to make sure that you’re using it safely. But it can be used safely, whichever vendor you purchase from will give you some sort of information about safe operating procedures. Usually don’t want to have anyone else within 1-2 meters around you, certainly don’t point it off in the air. You don’t point it at other people and you don’t want to have your hand near the analysis window. But as long as proper procedures are in place, you can use it safely and with proper use, the risk of exposure is no greater than any number of other things you do during the day. As far as the need for any certification for using handheld XRF it varies by state and also by country. Your local vendor can give you more information about specifically what’s required. Some places are more arduous than others.
I also see another question on can we use XRF for analysis of a ceramic? And I see another one on can we use XRF to test liquids? There are a number of sample types you can use XRF for. I focused on plastics and metals here. But there’s not really limitation on what kind of sample you can test basically. As long as you can put it in front of the analyzer, you can test it. The limitation is what you’re testing for so it needs to be an application to test for elements, and they need to be higher than the minimum detection level for the analyzer.
I see one question in lithium testing in aluminum alloys. And the short answer is no, you can’t test for aluminum. With handheld XRF the lightest element that you’ll see, that you can test for is magnesium. And so anything lighter than that wouldn’t be possible. And I see another question on using XRF as a surface technique, what’s the depth of measurement? It’s going to vary based on what kind of sample you’re testing. For light materials, like plastics, your penetration depth for the X-rays will be millimeters, up to centimeters so you can be rather deep in the sample. But it depends on what elements are present in that plastic. If it’s a heavier plastic with maybe a few percent of zinc as an additive or titanium or certainly bromine as part of flame retardant, that penetration depth is a lot smaller. For aluminum, a lighter metal like aluminum the penetration depth is on the order of millimeters. For most other heavier metals, from titanium on up your penetration depth is on the order of microns. Only tens of microns for the densest metals and maybe hundreds of microns for some of the lighter metals.
I see a question about portable XRF used for geology applications. We’re only covering consumer products here but there’s a whole range of applications you can use XRF for and mining, prospective, geochemical exploration is a pretty common application that XRF is used for. Any element, mining of any particular element, there are plenty of them. One question came up on halogen free applications. Can XRF be used for halogen-free applications? I didn’t talk about that too much today. Halogen free if you’re not familiar is a voluntary standard that some manufacturers have signed on to limit the amount of chlorine and bromine that are going into plastics. XRF can be used to detect those two elements, and so the short answer is yes, you can use XRF for halogen-free applications. Chlorine’s a lot more difficult to test for than bromine. Bromine you can get a detection limit of a few ppm within a few seconds. For chlorine, you tend to need to run longer tests.
Someone’s asking about specific X-ray tube type in an analyzer. I only talked about tube voltage, but also the X-ray tube that’s in the analyzer has what’s called an anode material that will be some element. Common ones are gold anode, rhodium anode or silver anode. And someone’s asking which anode is best for consumer products testing? In our experience, of the ones that are out there, generally gold anode works very well because there’s very little interference from those elements on any of the elements that you’re testing as part of consumer products regulations. Silver anode you do have a little bit of overlap with some cadmium lines and if you do a direct comparison you may find that the gold anode will do a little better than silver anode. You may find the same for rhodium anode, gold anode would do a little bit better. But it depends on a lot of features, not just the anode type. So I see one question about XRF testing in the automotive industry. Any regulations for covering restrictive elements in automotive applications and cars basically, XRF can be used for. There is the set of ELV – end of life vehicle regulations in the EU that are very similar to RoHS and yes, XRF can be used for those applications.
see there’s an earlier question regarding looking for training and inspections in China. Intertek does that. I recorded the gentleman who asked that question, I will contact you with some information regarding what we can do to help you with factory inspections and our KPs as far as Asia or anywhere in the world. So that’s something Intertek can help you with.
Someone else is asking about surface effects. If you have your testing and aluminum alloy and you have an anodized layer, do you need to remove that? Do you need to remove an anodized layer or if you paint layer on top? It really depends on what you’re testing for. If it’s a very thin layer then you’ll be able – most likely the X-rays will penetrate through it because an anodized layer is usually very thin, only a few microns or less. Usually less and so X-rays can penetrate though that. But at that point you’re testing an inhomogeneous sample, so there is going to be some shielding of the substrate and so it may cause some deviation of your results. It’s always better to remove a surface coating, but you may find that in some cases you’re able to do your analysis without removing the surface coating. The general answer is yes, you should remove surface coatings but in some cases you don’t have to.
Can XRF be used for SVHC testing? Substances very high concern for reach? Typically, no, we depend on lab testing for SVHCs. Typically cause they are not the elements or compounds that are strictly in SVHC so it’s very difficult to check for the SVHC using XRF. There’s also a question regarding the correlation between XRF results and what chemistry – typically depending on the element and the actual product and material, we can see some correlation. But again, we want to reiterate that it’s a screening technique. It’s not for quantitative lab results, so if you need quantitative lab results we recommend always going for the wet chemistry testing.
You can use XRF to test for aluminum and silicon. The lightest element that you generally will see, able to test for by handheld XRF is magnesium. But magnesium, aluminum, silicon and anything heavier than that in metals or sample types you can use XRF to measure.
Can use XRF for industrial applications such as bearings if you’re looking for certain heavy metals and on the sample line, the question regarding electronic equipment – does it need to be homogenous. The answer is yes, we can screen electronics for substances but then we would much rather see the substance or the element in its homogenous state to get a true reading. Reason being there are a lot of exemptions on the electronics such as lead in ceramics, still that we do pick up lead if it’s not in homogenous state. So the best way for screening is homogenous; that’s not to say you can’t screen a printed circuit board for lead. We do do that but we make sure we understand what we’re looking at as far as the materials are made of and each component on the board.
We have one question again on the safety of handheld analyzers, if they’ve been tested by a third party. I know at Innov-X we test all of our handheld models tested by an independent agency for radiation profile to see what sort of radiation is coming out in which locations. Safety depends on what the regulations are for the place that you’re in. So, the independent third party can only tell you what your radiation levels are at different locations and you have to apply those to the local regulations on radiation safety. But generally you’ll see that as long as the instrument is being used properly that you’re not putting your hands too close to the sample analysis area that the level of X-rays you’re exposed to is no higher than background levels.
Do you need to use it through a computer program, or can we use it hooked up to a laptop? The units are actually portable but they can also be used within a test stand in a lab environment and you can see the results printed out on the software that’s provided on the computer screen and print a report out from the computer. It’s a very nice feature Innov-X has built into their system. There’s a question regarding some library materials based on European standards. I’m not familiar with that standard, Brendan if you can take a look at that one, if not we can get back to you on that standard.
All RoHS and Foreman is done by the individual member states. So the EU produces the directives, but it’s up to the member states to put them into law and then enforce them. I’m not sure if that’s from a particular country of if it’s a general EU document.
Good question on surface area that you’re testing with an XRF analyzer. I can tell you for Innov-X handheld instruments the standard beam spot is a circle about 10 millimeters in diameter, but we have small spot collimation available so you can confine the beam to a smaller beam spot of 3 millimeters diameter. You do have to be careful when you’re doing that. If you’re testing a circuit board, for example. Because it could be that you use your analyzer to focus down to a or to collimate I should say down to a smaller spot size so you can just test one component and maybe not the solder join that’s next to it. But the component that you’re focusing on is still not a homogenous material – it may be a resistor an IC chip that has a couple of layers inside. So you want to be aware that you don’t want to be lulled into some false sense of security that now I’m testing a homogenous material when in fact you’re not.
Can XRF determine if a proper solder, leaded solder was used in a portable water piping system? This, yes, it can be used in that application. Just realize that if you’re using any type of brass fittings, the gun may not be able to detect the lead and the brass and the lead and the solder. So that’s one of the limitations there when you’re using this for plumbing applications. I think there’s on I saw earlier with the minimum spot size for the detector. I believe 3 millimeters, correct me if I’m wrong on that.
The smallest Innov-X offers is 3 millimeters. Our standard spot size is 10 millimeters. And be aware that your detection limits are going to vary based on your spot size, so if you go down to a smaller spot size your detection limits get higher because you’re getting less information about your sample.
https://www.olympus-ims.com/en/webinars/xrf-for-regulaton/