Table of Contents
- Forms used in Hoisting Calculations
- Calculations for Alternating-Current Hoist Motor
- Drum Calculations
- Maximum Rope Speed
- Time
- Inertia
- Friction of Hoist Parts
- Load Diagram
- Capacity of Hoist Motor
- Speed of Motor
- Input with Rheostatic Control
- Control of Hoist Motor
- Alternating-current Hoist Motor Calculations
- Calculations for a Direct-current Hoist Motor
- Voltage control with Flywheel
- Capacity of Alternating-current Induction Motor
- Capacity of Direct-current Generator
- Determining the No-load Losses
The rapid increase in reliability, the low cost of operation, the ready application of safety devices, and the growing availability of central-station power have made the question of installing a hoist of the electric type no longer debatable. Where adequate electric power is available, there are few cases where it would be advisable to install a steam or air hoist.
The type of electrical equipment depends largely on the nature of the power supply, its capacity, and the form of the power contract under which power is purchased. In a large majority of cases, the available electric power is alternating current, three phase, 60 cycles. There is, however, considerable 25-cycle power in use; and in a few instances constant voltage direct current is the only power available for a small or an occasional medium-size hoist.
Where a new hoist is to be installed, the designer of the mechanical parts can readily take care of the maximum stresses likely to be imposed by the motor. Where the hoist is already installed and operated by steam or air and it is desired to substitute an electric motor for the engine, a careful check should be made to determine the advisability of using the old mechanical parts. In most cases it is better to install a complete new hoist than to attempt to use old mechanical parts. A steam engine has a definite maximum torque, which the hoist has been designed to withstand, while a motor may be able to deliver momentary torques beyond the strength of the mechanical parts of the hoist.
The selection of the proper type of electrical equipment can only be made after complete information is obtained and certain calculations made to determine the capacities required. There are several methods used in making hoist calculations, but no matter what method is utilized a fair degree of familiarity with hoists and hoisting conditions is necessary before an intelligent analysis and proper selection can be made.
Forms used in Hoisting Calculations
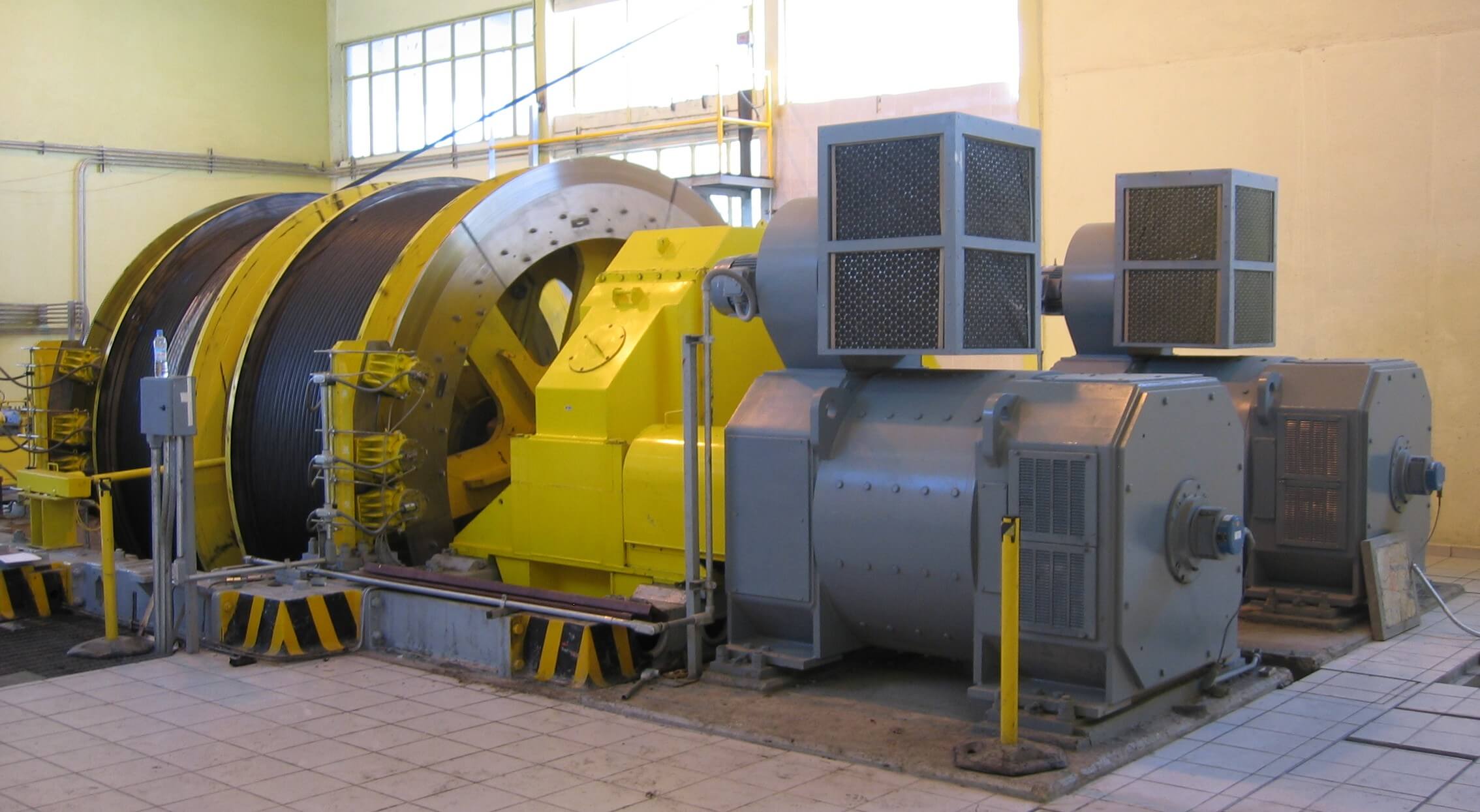
Some of the hoist calculation methods are long and complicated. Where such calculations are seldom made, it is better to use the longer methods; but where the calculations are made daily, short cuts can often be used to great advantage. Engineers associated with the writer, during the last few years, have felt that the various short-cut methods that had been worked up could be assembled in such a manner that any engineer working on hoisting problems could complete the necessary calculations in a short time and the results could be easily checked by another engineer. With this end in view, forms were evolved so that it was only necessary to fill in blank spaces to make a complete set of hoist calculations. These forms have been modified from time to time, in accordance with suggestions by various engineers. At the top of the form is place for the name of the customer, filing information, the date, and the characteristics of the power system. Under the heading General Data are the specifications or the information necessary before calculations can be made. This is followed by the various steps necessary to obtain the complete hoisting cycle, which require only calculations of a fairly simple character. As many of the conditions of operation cannot be approximated more closely than 3 to 5 per cent., all calculations can be made by using the slide rule.
In order to better illustrate the value of the method, examples are given showing the determination of the electrical equipment of an alternating- current hoist, a direct-current hoist with flywheel motor-generator set, and a direct-current hoist with a synchronous motor-generator set. The forms are so arranged that a single sheet 8½ by 11 in. is required for the complete calculations of an alternating-current hoist and but two sheets are required for either of the direct-current hoists. In the typical case selected, the hoist is of the vertical type using self-dumping cages.
The output of the hoist is figured at two values, the first being 2100 tons in 7 hr. and the second 3000 tons in 7 hr. These capacities are selected to show that for moderate rope speeds the alternating-current motor can be readily adapted directly to the hoist in case the power conditions are suitable. For high-speed hoisting and short cycles, the alternating-current motor applied directly to the hoist is not suitable, so a direct-current motor using the flywheel motor-generator set or synchronous motor-generator set should be selected. The daily output of a coal mine is generally estimated on the basis of getting this output in 7 hr., allowing 1 hr. for delays.
https://www.youtube.com/watch?v=l7-ju2b4h2U
Calculations for Alternating-Current Hoist Motor
Calculation sheet No. 1, Fig. 1, shows the complete calculations for hoisting 2100 tons in 7 hr. It is seldom that most of the information required under the heading General Data is obtained from the customer;
the first seven items are usually given and the engineer recommends or estimates the other eleven.
Drum Calculations
A plain cylindrical drum has been assumed for simplicity; the question of conical and cylindro-conical drums will not be considered in this paper. The method of figuring special-shape drums is practically the same as for cylindrical drums, but somewhat more complicated as it is necessary to take into account the varying radius of the ropes on the drums and the varying rates of acceleration and retardation. Conical or cylindro-conical drums, in general, cut down the peak load during acceleration and retardation, but in many cases they introduce undesirable elements. Often the inertia of the special drums is high, which in a way defeats the purpose for which the drum is designed. In many cases considerable power is required to carry the cage into the dumping position, while with the cylindrical drum the cage will drift into the dumping position without the use of power.
In general, the drums should be as small in diameter as good rope practice dictates, for the smaller the drum diameter the greater will be the speed, which will permit of a fairly high motor speed or a lower gear reduction. Wherever possible the drum size and motor speed should be so selected that single reduction gears can be used where gearing is necessary. It is considered good practice to use not less than a
1 1/8 in. rope on a 6-ft. diameter drum
1¼ in. rope on a 7-ft. diameter drum
1 3/8 in. on a rope 8-ft. diameter drum
1½ in- rope on a 9-ft. diameter drum
1 5/8 in. rope on a 10-ft. diameter drum
1¾ in. rope on a 12-ft. diameter drum
From the maximum capacity in 7 hr. the trips per hour can readily be determined. The time for caging varies from 4 to 10 sec., and should be kept as low as possible in order to cut down the rope speed and the capacity of the equipment. After the caging time has been selected, the running time can readily be determined.
Maximum Rope Speed
With a plain cylindrical drum, the maximum rope speed, in feet per second, is obtained by dividing the depths in feet, by the running time per trip in seconds, minus one-half of the sum of the accelerating and retarding time. After the rope speed is obtained the maximum drum speed and angular velocity can readily be determined. The inertia of the drum should be obtained from the hoist builder, when possible.
For estimating purposes, the inertia of a cylindrical drum with head sheaves and gears can be closely approximated by allowing 200 lb. per sq. ft. of drum surface and assuming the radius of gyration at 3 in. inside of the drum surface.
The selection of the accelerating and retarding time depends on the hoisting conditions; this time will vary from 4 to 8 sec. for fast coal hoists and 10 to 20 sec. for slopes and deep metal mines. These values should be made as small as is practical, for the smaller they are the lower will be the maximum rope speed. The retarding time is frequently made less than the accelerating time, as the friction of the hoist assists during retardation. On the forms, a space is left for a sketch showing the size and shape of the drums. This sketch is particularly necessary when a special shape of drum is used in order that the turns and varying radius at different parts of the cycle may be shown. The item, Total Revolutions per Trip, is used only for special-shape drums.
Time
The distance traveled by the cages or skips can be readily determined from the rope speed and time. The angular acceleration and retardation is obtained by dividing the angular velocity by the accelerating and retarding time.
Inertia
With high-speed hoisting, inertia plays a prominent part and in many cases the power required during acceleration and retardation is the dominant factor in determining the capacity of the electrical equipment. Under the heading Inertia, the inertia of the various parts is determined based on the drum radius. The moment of inertia is the weight multiplied by the radius of the gyration squared and divided by 32. Where the motor is geared, the moment of inertia of the armature must be multiplied by the square of the gear ratio to refer it to the drum radius. A motor is selected that will probably be of sufficient capacity so that the inertia of the rotor can be estimated. If the weight of the rotor is known, the inertia can be calculated by assuming the radius of gyration to be 75 to 80 per cent, of the radius of the rotor, depending on the details of the construction. In some cases, it is necessary to go back after the load cycle has been calculated and select another size of motor.
The load part of the inertia consists of the weight of the material to be hoisted, the weight of the cages, cars, and the rope on both drums. This total weight is suspended from the drum rim so that the radius of gyration is the same as the drum radius. The addition of the individual weights is shown on the left-hand margin of sheet No. 1. After the total inertia of all moving parts is obtained, the moment due to angular acceleration and retardation can be readily calculated by multiplying the total inertia by the angular acceleration and retardation.
Friction of Hoist Parts
The friction of the hoist parts, including windage and friction of the cages in the shaft, has been the subject of much controversy. This friction is sometimes assumed on the basis of a certain hoist efficiency of 80 to 85 per cent. This method may result in considerable error during the high-speed portion of the cycle, where the actual load on the hoist motor is very low and when the friction load is really at its maximum. A load cycle for a deep mine hoist may show that during the constant high-speed portion of the cycle, the load on a 2000-hp. motor may go as low as 100 hp. or less. With a 15 per cent, loss, the friction load would figure 15 hp., while the actual friction load would probably be over 200 hp. The friction of a hoist based on the pull produced at the drum rim is practically constant throughout the cycle, so that a method involving the equivalent pull at the drum rim would seem to be much more logical. It has been the practice of the Westinghouse engineers to assume that the total friction of a hoist is based on a rope pull of 7½ per cent, of the total suspended weight on the drums for single-reduction geared hoists, and 5 and 5½ per cent, for direct-connected hoists. This rope pull, when multiplied by the radius of the drum, will give the moment at the drum rim due to friction. This value is assumed to represent the friction throughout the entire cycle. The value for frictional resistance can, however, be varied to quite an extent either way without vitally affecting the capacity of the equipment.
Load Diagram
With the foregoing information, which has involved calculations of the simplest nature only, the load at various points in the hoisting cycle can be determined, as outlined under the heading Load Diagram. The load diagram is determined by calculating the torque, or moment, in foot-pounds at the drum rim at the start, at the end of accelerating period, at the beginning of the constant-speed period, at the end of the constant-speed period, at the beginning of the retardation period, and at the end of the retardation period. This involves six equations for the plain cylindrical drum. Special drums frequently require a larger number of equations, which of course can be readily taken care of in the hoist calculation form.
The total moment at any point of the cycle will consist of the moment due to the load to be hoisted plus the unbalanced cable. This is obtained by multiplying the weight of the load and unbalanced cable by the drum radius; to this is added the friction moment and the accelerating and retarding moment if the hoist is accelerating or slowing down. The retarding moment has, of course, a negative value. The total moment must be supplied by the hoist motor. The cages and empty cars balance each other and affect the load cycle only during acceleration and retardation. As the loaded cage ascends and the empty cage descends, the amount of unbalanced cable changes rapidly. At the end of the cycle, the suspended cable is on the empty side and its weight tends to balance the load. Where very deep mines are involved, the weight of the suspended cable will often more than balance the load, causing the power to become negative.
The angular velocity is the linear speed, in feet per second, at the radius of 1 ft. (0.3 m.). As the total moment is the equivalent rope pull at 1 ft. radius, the product of the two will give the rate of work, in foot-pounds per second. If this value is divided by 550, the result will be horsepower. It is, therefore, only necessary to multiply the total moment by the angular velocity and divide by 550 to obtain the horsepower values.
Having obtained the entire load cycles in six equations, the results can be plotted, as shown in Fig. 2. It will be readily noted that a considerable portion of the motor capacity is due to acceleration and retardation. This curve indicates clearly the desirability of keeping all moving weights down to as low a value as possible, consistent with strength, reliability, and good practice.
Capacity of Hoist Motor
The capacity of an electric motor depends on the temperature to which the various parts rise above the surrounding atmosphere. The temperature rise depends on the motor losses, most of which are dissipated as heat. If these losses were proportional to the load upon the motor, it would be a simple matter to determine the average load and select a motor of the same capacity. In the foregoing case, the average load, upon the motor is 450 hp. The losses, however, vary closely as the square of the load, so that to obtain a rating that will give an equivalent heating, it is necessary to determine the rating by taking into account the losses. The prevalent method for obtaining this equivalent rating is to calculate the root mean square rating, as shown under the heading Capacity of Hoist Motor. Each part of the cycle is taken separately and the equivalent heating calculated by adding the squares of the two horsepower values, dividing the sum by 2, and multiplying the result by the time. Where there is a fairly large difference between the horsepower values in one part of the cycle, a more accurate result is obtained by adding to the sum of the squares the product of the two values and dividing the result by 3 before multiplying by the time. This is considered later in determining the capacity of the synchronous motor, which is part of a motor-generator set.
The final value obtained is 610 hp., showing that a 600-hp. motor is required and also indicating that the average value in this case must be increased by 33 1/3 per cent, to obtain the correct value. The capacity obtained is based on reversing the motor to obtain retardation. If mechanical brakes are used, the last part of the calculation will be left out and the capacity required will be 579 hp. instead of 610. The same motor would be recommended, however.
There has been considerable argument regarding time used in a calculation for capacity. A fairly high-speed motor will dissipate heat at full speed much more rapidly than when standing idle. For this reason, the time will have a different real value at different parts of the cycle. Some engineers take the full time at full speed, a certain percentage of the accelerating and retarding time, and a smaller percentage of the rest period. The writer has adopted the scheme of using the full time during actual operation, one-third of the time during the rest period for geared motors, and one-half of the rest period for large direct-connected motors. The difference between the ability to dissipate heat at full speed and at a standstill is greater for a high-speed motor than for a low-speed. When forced ventilation is used on the hoist motor, full time can be used during the entire cycle.
From the heating standpoint, a 600-hp. motor will have ample capacity. The motor must, however, be checked for maximum load. Most induction motors are designed to have a pull-out torque of twice the full-load torque. In this case, if the motor has a pull-out torque of 2, the power required during the accelerating period will be very close to the pull-out torque of the motor, so that there will be no margin for a drop in line voltage, which is apt to occur even on the best-regulated power lines. As the pull-out torque of an induction motor varies directly as the square of the impressed voltage, a small drop in line voltage will cause a much larger reduction in the pull-out torque of the motor. It is recommended that the pull-out of an induction motor be selected at a value 25 to 30 per cent, greater than the maximum value on the load cycle to take care of a possible drop of at least 10 per cent, in line voltage. In the present case, this condition will be met by providing a motor with a pull-out torque of 2.5.
Speed of Motor
The speed of the motor depends on several factors. A high-speed motor will be cheaper and have a better performance, with regard to efficiency and power factor, than a low-speed motor. The high-speed motor, on the other hand, requires a high gear ratio and the equivalent inertia at the drum rim is very high. The low-speed motor is larger and more costly and has a poorer performance than the high-speed, the inertia will be greater than the higher speed motor, but in most cases the lower gear ratio will more than make up for this difference. In general, a motor speed should be selected that will permit of single reduction gears. Herringbone gears can be obtained with ratios as high as 15 to 1. The final speed of the motor is generally a compromise to obtain the best all around conditions and will be influenced, to some extent, by the available speed of motors as developed by the various manufacturers. In general, motors up to 200 hp. will range from ten to fourteen poles; from 200 to 600 hp., fourteen to sixteen poles; and from 600 hp. up, sixteen to twenty poles.
Input with Rheostatic Control
From the hoisting cycle, the kilowatt-hours per ton and the overall efficiency of the hoist can be estimated, as shown under the heading Input with Rheostatic Control. The output of the hoist motor, in horsepower-seconds, is calculated from each part of the cycle and an average efficiency of the hoist motor is assumed at 88 per cent. The total input, in horsepower-seconds, can be readily converted into kilowatt- hours from which the value 1.275 kw.-hr. per ton is obtained.
The shaft horsepower-seconds for the actual work done in hoisting the coal is obtained by mutiplying the load hoisted by the distance and dividing by 550. This value divided by the input to the alternating- current hoist motor will give the overall efficiency of the cycle, which in the present case is 29.5 per cent. If mechanical brakes are used, which do not require power from the line, the overall efficiency will be 35.5 per cent. Where considerable power is required during the retardation portion of the cycle, it is not possible to use mechanical brakes unless they are of a design that can readily take care of the amount of power involved. In many cases it is necessary to plug the motor to obtain the proper rate of retardation. This is necessary where the mechanical brakes do not have sufficient capacity to absorb the power required during the braking period.
The complete load cycle is plotted in Fig. 2, which also shows the rope speed, kilowatt-hours per ton, and other information in regard to the hoist. A glance at the load cycle will show why the efficiency is low. The shaded part of the accelerating portion of the cycle indicates the power loss in the rheostat; this loss is unavoidable when rheostatic control is used. If electric braking is used, the entire area of the quadrilateral representing the retardation period will be lost in the rheostat. The use of conical or cylindro-conical drums will, in some cases, reduce the capacity of the motor required, and also reduce the rheostatic losses by reducing the load during the accelerating and retarding periods.
Control of Hoist Motor
The control for a hoist motor is particularly important, since with improper control the success of the entire installation is jeopardized. For small low-voltage hoists, a drum controller can be recommended in most cases for either alternating or direct current. For the medium and larger sizes of a.c. hoists, 2200-volt motors are becoming standard and the most satisfactory control is the magnetic type with air-brake switches in both primary and secondary circuits. The high-voltage air-brake magnetic contactor is to be recommended for the primary, especially where frequent operations are necessary. The magnetic type of control readily lends itself to the application of safety devices, such as automatic acceleration, overload trip, low-voltage trip, brake magnets, interlocking reverse switches, geared and hatchway limit switches, etc.
Slope hoists should be equipped with at least one more accelerating point than vertical hoists of the same capacity, with a lower torque provided on the first notch to permit of slow starts, which is particularly necessary where slack cable exists.
The liquid rheostat is used to some extent in connection with a.c. hoists. This is a simple piece of apparatus and will give satisfactory service where a supply of good cooling water is available. This type of rheostat makes the best showing with the larger a.c. hoists and where, the cycle is not too rapid. For most installations, however, the magnetic type of controller is to be preferred.
Where the maximum rope speed exceeds 1800 ft. per min. (329 m.) and the cycles approach 3 per min., the application of an a.c. motor to a hoist becomes questionable. For such high rope speeds and rapid cycles, the inertia effect of the a.c. motor is great, the power loss during acceleration and retardation, high, the peak loads upon the power system in some cases prohibitive, and the braking system questionable. Under such conditions the best solution seems to be the application of a d.c. hoist motor receiving power from either a flywheel or synchronous motor-generator set. The inertia of a d.c. motor is, in most cases, much lower than an a.c. motor; and the control, where field control is utilized, is vastly superior, as rapid changes can be made in operating conditions and electric braking can be safely and economically obtained entirely independent of the power supply.
Alternating-current Hoist Motor Calculations
for an Output of 3000 Tons
Let us assume the same set of specifications, except that the output per day is 3000 tons. The calculations for an a.c. motor are given in hoist calculation sheet No. 2, Fig. 3, which shows that the cycle must be made in 21 sec. instead of 30 sec. The maximum rope speed has been increased from 1500 ft. per min. (457 m.) to 2730 ft. per min. (832 m.) and the drum speed to 108.5 r.p.m.
An a.c. motor is selected that has a 40° rating of 1500 hp. or a 50° rating of 1875 hp. wound for 2200 volts, three phase, 60 cycles, twenty pole. The WR² of the rotor of this motor is over five times that of the 600-hp. motor. The gear ratio, however, is only 3.22 to 1, so that the inertia at the drum rim; in pounds-feet squared, is really less than for the 600-hp. motor. In going through the complete set of calculations it is found that the capacity of the motor figures out 1870 hp. and the pull out required will have to be at least 2, based on the 50° rating.
It is possible that the margin in rating is not sufficient if a large amount of rock is to be handled. The next size of motor is selected having a capacity of 2000 hp. at 40° rise. The inertia of the rotor of this motor, as shown in hoist calculation sheet No. 3, Fig. 4, is nearly two times that of the 1500-hp. motor. The load diagram shows a large increase in the power required during acceleration and retardation. This increase is very apparent in figuring out the capacity of the motor, which proves to be 2340 hp. A 2000-hp., 40° motor will probably have a 50° rating of about 2350 hp., so that no advantage is obtained by adopting the larger motor. Applying a large motor on a high-speed cycle produces a pyramiding effect, for the added capacity is absorbed by the increased power required by the added inertia of the rotor.
The load cycles for both alternating-current motors are plotted in Fig. 5, which graphically shows the comparison. The efficiency is particularly low, especially with a larger motor, being 14.5 per cent, for the 1500-hp. and 11.8 per cent, for the 2000-hp. motor. In either case the power required during the retardation period is too great to absorb by mechanical brakes.
If the hoisting conditions do not permit the installation of any but an a.c. motor, it is sometimes possible to meet such a high-speed cycle b applying two motors instead of one. By using the same speed or possible a somewhat higher speed motor, the total inertia may be considerable
less by the use of two motors. This depends somewhat on the motors that have been developed and built. It would, of course, be possible to develop a special motor having very much less inertia than either of the motors shown in Figs. 3 and 4. The development of this motor, however, would probably cost several thousands of dollars, which would make it non-competitive. The control of two motors will be a little more com-
plicated than the control for one, but the cost of the entire installation may not be any greater than when using one large motor of a capacity greater than the combined capacity of two motors.
The theoretical power required to drive the hoist is represented, in Figs. 2 and 5, by the heavy diagonal lines starting at zero. The actual power taken by the hoist motor when an alternating-current motor is used is represented by the light line starting at a high value. In other words, practically all of the high peak load at the moment of starting is absorbed in the rheostat. The same applies to the retardation portion of the cycle, except that when electric braking is used with an a.c. motor all of the power represented by the quadrilateral is drawn from the line and wasted in the rheostat.
Calculations for a Direct-current Hoist Motor
Hoist calculation sheet No. 4 shows the same problem except that a direct-connected hoist motor is used instead of a geared alternating-current hoist motor. The weight and inertia of the d.c. armature is of course much greater than any of the rotors of the a.c. motors mentioned, but being direct connected the equivalent inertia at the drum is much less. There being no gears, the inertia of the drums and sheaves is considerably less. The friction is also somewhat less, being figured at 5½ per cent, instead of 7½ per cent, of the total suspended weight.
The hoisting cycle shows much smaller accelerating and retarding values and the capacity of the motor is but 1485 hp. The load cycle is plotted as a heavy dotted line in Fig. 5. With field control, there are no rheostatic losses in the main armature circuits, so that the power follows the diagonal line from the origin instead of the vertical line, as in the case of the a.c. motor. The light dotted line starting at 2500 hp. indicates the torque that must be delivered by the hoist motor. In other words, the hoist motor delivers a high torque at the start with a low expenditure of power, for there are no rheostatic losses. As the current in the hoist motor is proportional to the torque, this fine also represents the current from which the heating can be calculated. The power represented in the upper triangle during the accelerating period is only apparent and not real when using a field control system. The power represented in the upper triangle of the retarding part of the cycle is returned to the system instead of being drawn from the line, as with the a.c. motor.
All power taken from the power system, when using a flywheel motor-generator set, passes through the induction motor and since the flywheel cannot change its speed quickly, the load on the induction motor cannot change quickly. As the load comes on the hoist motor, it is transferred through the generator to the induction motor. As soon as the load on the induction motor reaches a predetermined value, a torque motor on the slip regulator causes a resistance to be inserted in the secondary of the induction motor. This causes the speed to drop and the flywheel to give up energy. By this means the maximum load on the induction motor is fixed at a predetermined value. At any time during the cycle that the load on the hoist motor is above this value, the flywheel will supply the surplus, while if the load is below this value, the flywheel will store up energy keeping practically a constant load on the induction motor.
Voltage control with Flywheel
When making calculations for direct-current field-control system, it is not necessary to fill in the spaces at the bottom of the calculation sheet under the heading Input with Rheostatic Control. With the d.c. field-control system, the d.c. hoist motor receives its power from a d.c. generator, which in turn is driven by an a.c. wound-rotor induction motor of a synchronous motor. The flywheel type of motor-generator set will be taken up first. Calculation sheet No. 5, Fig. 7, shows how the capacity of the generator, the weight of the flywheel, the capacity of the induction motor, and the overall efficiency are obtained.
At the top of the sheet are four columns, the items in the first, which is headed Hoist-motor Output, are obtained from the load cycle on calculation sheet No. 4, Fig. 6.
The second column gives the input to the hoist motor at the various points in the cycle. These values are obtained by adding the variable losses of the hoist motor to the output values in the first column. These losses consist of the copper, iron, friction, and windage. The excitation is considered a fixed loss to be taken care of later. The best way to obtain the variable losses is to plot a loss curve for the particular motor, as shown in Fig. 8. By means of this curve, the losses at each point in the cycle can be readily determined. During the retarding portion of the cycle, the hoist motor is acting as a generator to return power to the flywheel; consequently the losses must be subtracted instead of added.
The third and fourth columns are headed Generator Input, the third being the apparent input and the fourth the real. The third column is obtained by adding the variable losses of the generator to the values in the second column; that is, the copper and iron losses. The excitation, friction, and energy are fixed losses to be taken care of later. The generator variable loss curve is also plotted in Fig. 8.
The fourth column is the same as the third column, except, for the first and last values, which represent torque and not real horsepower in the third column. The real values are substituted in the fourth column and consist of the copper losses of the hoist motor and generator. The iron loss, friction, and energy of the hoist motor and the iron loss of the generator are practically zero at the moment of starting and stopping.
The fifth column, Horsepower-seconds Input, is used to obtain the average power input to the generator required during the entire cycle. The horsepower-seconds during each portion of the cycle is readily obtained by taking the average value and multiplying by the time. The power during retardation is subtracted, for it represents returned power. The total net value of 9137.5 hp.-sec. is divided by the total time of the cycle or 21 sec. The result is 435 hp. for the average power delivered to the generator.
The values in the fourth column are plotted in Fig. 9 and a horizontal line drawn at 435 hp. represents the average input. This curve shows that for complete equalization the power in the shaded portion above the
435-hp. line must be supplied by the flywheel. The value of this power, in horsepower-seconds, is readily computed, as shown on calculation sheet No. 5, Fig. 7, which indicates that the total power to be absorbed is 7071 hp.-sec.
The capacity of the generator will be close to 1000 kw.; an economic speed for this capacity is 720 r.p.m. synchronous when driven by a 60-cycle motor. The automatic slip regulator in the secondary of the induction motor has a normal slip of about 3 per cent, and the motor windings and leads about 2 per cent., making a total of 5 per cent. At full load, the speed of the motor-generator set with regulator plates closed will be about 685 r.p.m. Calculaton sheet No. 5 contains blanks for normal speed of set, diameter of flywheel, etc. Flywheels for such service in America almost exclusively consist of steel plates riveted together making
a solid disk. Such a flywheel can be safely operated at 20,000 to 24,000 ft. per min. (6096 to 7312 m.) rim speed. The wheel selected will have a diameter of 10 ft. (3 m.) and a peripheral speed of 21,600 ft. per min. The radius of gyration of such a wheel is 0.707 times the radius to the rim, so that is a simple matter to determine the speed, in feet per second, at the radius of gyration. The amount of speed reduction for flywheels in service of this kind varies from 10 to 20 per cent. The present problem will be worked out upon the basis of complete equalization with a slip, of 10 per cent. In many cases complete equalization is not necessary and considerable saving in flywheel weight and losses can be obtained: by using partial equalization. Partial equalization removes the heavy peaks from the power system, but does not give a constant load upon the alternating-current motor.
The formula to obtain flywheel weights is derived from the simple laws of mechanics in which the energy contained in a moving mass is one-half MV². The difference between the energy contained in the wheel at full speed and reduced speed divided by 550 will represent the horsepower-seconds given up by the wheel when the speed is reduced. The theoretical weight is estimated at 20,400 lb. (9253 kg.) and to use a margin of safety a 22,000-lb. (9979 kg.) wheel is recommended. This wheel will have a thickness of 7 in. (11.8 cm.) and will be surrounded by a sheet metal case to cut down the windage and prevent accidental contact by persons in the vicinity.
Capacity of Alternating-current Induction Motor
The average input to the generator was determined to be 435 hp. The various fixed losses not allowed for are listed under the heading Size of Driving Motor on calculation sheet No. 5. The excitation of the hoist motor and generator, although not constant throughout the cycle, is assumed at an average value of 25 hp. The latest type of field control is quite a modification over the original Ward-Leonard system of control, in that the hoist-motor field is not kept at a fixed value but is overexcited during acceleration and retardation, operated at its normal value during constant speed, and underexcited during the rest period. By overexciting during acceleration and retardation, the armature current is kept at a lower value, which reduces the heating effect in the main circuit. This is of considerable importance in cycles where most of the heating occurs during the accelerating and retarding period. The exciting current is reduced during the rest period to cut down the field heating and incidentally to save a small amount of power; this reduction is generally about 30 per cent., which reduces the heating 50 per cent. Further reduction is liable to slow up operations, due to the time element of the hoist-motor field. In addition, higher speeds are sometimes obtained by several notches of field weakening of the hoist-motor fields. This scheme is, however, more prevalent in reversing rolling-mill practice than in hoisting.
The generator field varies with the speed and, by means of a comparatively new type of relay, the acceleration and retardation is entirely automatic, during which time the main armature current is held at a predetermined fixed value. The relays are so sensitive that the usual variations in current due to notching are entirely absent. The absence of variation in current during acceleration and retardation should be of considerable benefit in keeping down rope wear. By means of geared limit switches, the retardation can be made entirely automatic and independent of anything the operator may do.
The next fixed loss is that of the exciter itself, which is estimated at 2 hp. The windage and friction of the generator are fixed, values, estimated at 15 hp. The flywheel loss is rather difficult to estimate and test results on existing wheels are rather erratic; the value of 20 hp. should be close to the actual power loss. The loss in the slip regulator varies throughout the cycle, the average is estimated to be approximately 7 per cent., or about 35 hp.
The total output of the a.c. motor will be 532 hp. A conservative value of 92 per cent, is selected for the efficiency so that the input from the power line will be 578 hp. This value is readily converted into horsepower-seconds and kilowatt-hours, resulting in a value of 2.52 kw.-hr. per cycle; this is equivalent to 1 kw.-hr. per ton of coal hoisted.
The overall efficiency is readily calculated by dividing the actual work done, in horsepower-seconds, by the input to the a.c. motor. The actual work done is designated as shaft horsepower-seconds and is the product of the weight of the coal by the depth divided by 550; the efficiency, as shown, is 37.5 per cent. Compared with the value obtained for the corresponding a.c. motor, there is not only a large difference in actual efficiency but also with the a.c. motor the momentary peak on the line is from 3400 to 4000 hp., depending on which a.c. motor is used, while the peak on the d.c. system is but 578 hp or a difference of 2800 to 3800 hp. Where power is charged for on a basis of momentary peaks, the penalty caused by the use of an a.c. motor is excessive.
Capacity of Direct-current Generator
The capacity of the d.c. generator is obtained, in a manner similar to that used to determine the capacity of the hoist motor, by using the values in the second column at the top of calculation sheet No. 5. The entire time is used in the denominator, for the generator operates at practically full speed during the entire cycle. The result gives a capacity slightly smaller than the hoist motor, because the time is taken at a different value. The capacity of the generator should be 1100 kw.
Determining the No-load Losses
It is frequently desirable to know the no-load loss of the motor-generator set or the power required to drive the set during the rest period. If the rest period is of short duration, the motor fields are kept excited; if the period is of longer duration, the motor fields are frequently opened which cuts down the no-load losses about 10 hp. The total no-load losses with motor fields excited are shown under the heading No-load Losses in calculation sheet No. 5. This value is 68 hp. with motor fields excited and about 58 hp. if the motor fields are open.
At the bottom of calculation sheet No. 5, recommendations for the capacity of the hoist motor, generator, a.c. motor, and weight of flywheel are made. These recommendations are often influenced by the available machines that have been built and may be the cause of a variation in the capacities recommended by different manufacturers.
Where the power system is large and where momentary peak loads are not penalized, a synchronous motor can be used on the motor-generator set. The calculations necessary for such a system are shown on calculation sheet No. 6, Fig. 10. Calculation sheet No. 4 is used to determine the load cycle and capacity of the hoist motor.
The first four columns at the top of calculation sheet No. 6 are the same as on calculation sheet No. 5. The next two columns give the generator constant losses, including exciter losses, which must be supplied by the synchronous motor. All loads on the generator are directly transmitted and must be supplied by the synchronous motor, while with the flywheel this was not directly the case, since the flywheel takes care of all peak loads and sudden fluctuations. The load on the synchronous motor follows the load on the hoist motor with the exception that all losses in the system are added to the load of the synchronous motor.
The first column in the second row gives the output of the synchronous motor at each point of the cycle; the next three columns give the internal losses of the synchronous motor, and these losses added to the output column give the values in the fifth column, which is the total input to the synchronous motor at each point in the cycle. The total horsepower-seconds input is readily calculated as shown in the last column. Most of the retardation part of the cycle is negative while a part of it is positive; the net value, however, is readily computed.
From the total horsepower-seconds, the input is found to be 2.31 kw.-hr. and 0.925 kw.-hr. per ton. The overall efficiency is found to be 40.8 per cent, or a little over 3 per cent, better than when using the fly-wheel set; the difference is largely due to the flywheel and slip regulator loss.
The no-load loss of the set is 74 hp., or somewhat larger than with the flywheel set; as the synchronous motor is much larger than the induction motor, its losses, including excitation, more than make up for the flywheel loss with the induction motor set.
The capacity of the generator is calculated the same as on calculation sheet No. 5.
The capacity of the synchronous motor is calculated as shown. As there is so much difference in the values during the accelerating and retarding portion of the cycle, the method used is the square of the first value plus the square of the second plus the product of the two and the total divided by 3. The small values at the end of the retarding period and during the rest period are neglected, as their effect on the heating is negligible. The capacity obtained is 970 hp. A 1000-hp. motor would have sufficient capacity as far as heating is concerned, but would probably not have a sufficiently high pull out. A 1200-hp. motor with a pull out of 3 or a 1500-hp. with a pull out of 2.4, would be recommended. The additional capacity over that required can in many cases be used for power-factor correction. Where power-factor correction is not desired, a simple relay could be installed; this would reduce the excitation during light load periods and increase it during heavy loads, thus tending to produce a more nearly constant power factor and saving some power.
Fig. 11 shows graphically the input to the hoist from the power system with the three types of hoists just described. The heavy solid line shows the input when using the larger of the a.c. hoist motors. The maximum momentary peak at the start is 4100 hp. and the peak during retardation is a little over 2100 hp.; the kilowatt-hours per ton is 3.19.
The input when using the flywheel system is shown by the dot-and-dash line and is practically constant at a value of 578 hp.; the kilowatt-hours per ton is 1.
The dotted line shows the input to the line when using the synchronous motor-generator set. The maximum peak load during acceleration is 3050 hp., but this peak is not imposed upon the system suddenly. The load starts at less than 500 hp. and does not reach the maximum peak for 5 sec.; this permits the regulating devices on the power system to operate and produce good regulaton. All power below the line, when using the synchronous motor-generator set, is returned to the power system. The kilowatt-hours per ton using the synchronous motor-generator set is 0.945, or less than one-third of that required when using the larger of the two a.c. motors.
As before stated, a fair knowledge of hoist and hoisting conditions is necessary to use these forms intelligently, as well as a knowledge of the various pieces of electrical apparatus necessary to make up a complete hoisting equipment. It is necessary in many cases to make compromises and many additional short-cut methods can be evolved by one having to make such calculations daily.
After the machines are determined the details of the control must be settled; this in many cases means conferences with the hoist builders to determine the details so that the electrical equipment will coordinate with the mechanical equipment supplied by the hoist builder.
The control should be so arranged that any wrong or hasty movement of the control levers by the operator will not endanger any part of the hoist. With an a.c. hoist, this is accomplished by automatic acceleration and the well-known safety devices supplied by the various hoist builders. These devices open the power circuit and apply the brakes if the speed is above a predetermined value at any point in the cycle. They also take care of overwind in either direction. With the d.c. field-control system, the speed of the hoist follows the control lever irrespective of the load and drifting cannot occur; this makes it possible to apply safety devices that would not be effective with an a.c. hoist, also to apply automatic control, which can be made to function without the use of an operator.
With the field-control system the writer prefers to have no switch or circuit breaker in the main armature circuit between the hoist armature and the generator armature, but to obtain overload protection by opening the fields of the hoist motor and generator. A circuit breaker in the main circuit is large and cumbersome and the delay in reclosing it may cause serious trouble, as it is important for the operator to regain electric control of the hoist as soon as possible after the breaker has opened. A circuit breaker located in the field circuit can be more readily handled than one in the main circuit. With the new control system, it is almost impossible to have the circuit breaker opened unless there is some real defect, such as a short circuit in the main generator or hoist motor. This means that the operator has electric control of the hoist at all times, which is much safer than to depend on mechanical brakes in cases of emergency.