Table of Contents
Recovery and dilution usually are interrelated; with some methods of stoping a high recovery involves contamination of the ore from the walls or capping, and often clean ore can be obtained only by leaving some ore in the mine.
In open-stope mines the greatest loss of ore is that tied up in pillars left for support of the back or hanging wall. The amount of ore thus left varies considerably with the strength of ore and wall rocks, thickness of the ore, its depth below surface, and the requirements for permanent support to prevent movement and subsidence of overlying strata and of the surface. Where eventual subsidence is permissible, much of the pillar ore often can be recovered on the retreat by robbing operations, the amount recoverable depending to a considerable extent on roof characteristics; sometimes almost complete extraction is possible. Where it is imperative to prevent surface subsidence and resultant damage to surface improvements or to prevent an influx of surface or underground water, 20 to 40 percent of the ore in the deposit may have to be left as pillars. Aside from ore left in pillars, high extraction is usually possible in open stopes, since the stope boundaries are exposed to view and all showings of ore can be attacked and mined.
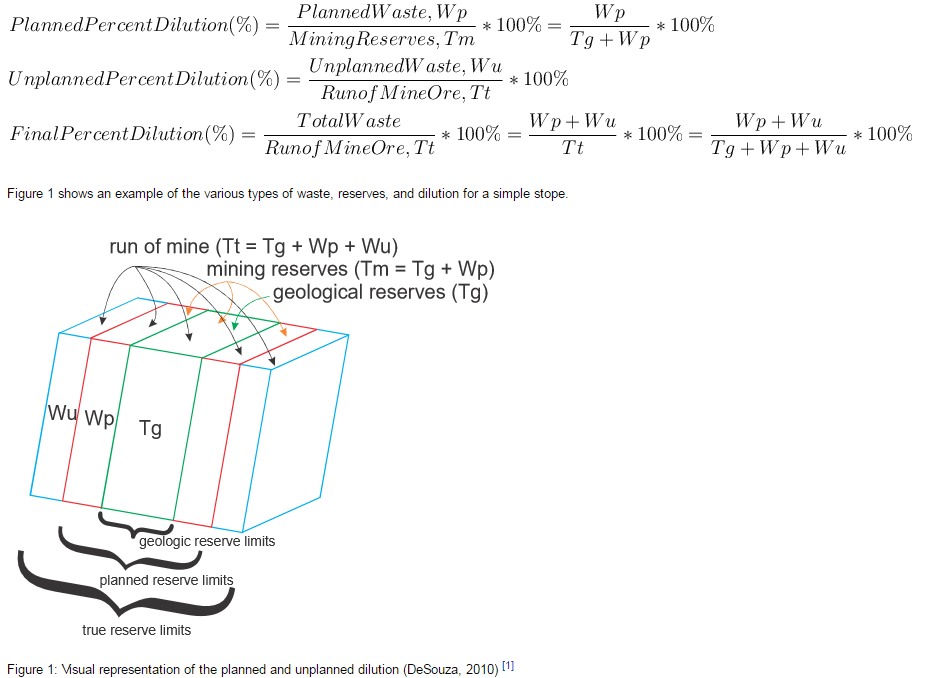
With shrinkage stoping, high extraction can be obtained if the lode is regular in strike, dip, and thickness and the walls are firm. If the lode is very irregular, there are numerous rolls in the footwall, or there are abrupt offsets due to strike or diagonal faults or if tongues of ore make off into the walls, considerable ore may be lost. Ore in the footwall in the form of bulges or branching tongues is likely to be overlooked because covered by broken ore; however, if the walls are exceptionally firm much of this often can be recovered during final drawing of the stope. When the stopes are silled above the level, that is, on drift pillars (called boxhole pillars in Canada), complete recovery of these pillars is frequently impossible. Likewise, some loss may be incurred in recovery of floor or crown pillars. Loss in pillars may run up to 10 or 15 percent of the total ore in the deposit. As in open stoping, pillars may also be left at various horizons in the stope for roof support, but the aim usually is to leave these in low-grade sections as much as possible.
Some dilution almost always occurs in shrinkage stoping, either because of overbreaking the walls of the vein during mining or later sloughing, especially during final drawing. Overbreaking is almost unavoidable when the vein is irregular in strike and dip and especially so if there are numerous small offsets.
From 85 to 95 percent of the ore usually can be recovered by shrinkage stoping with dilution of 5 or 10 to 25 percent, except where some other method would be better suited to the conditions. Sometimes dilution runs 30 percent or more, but in most such instances cut-and-fill or some other method probably should be employed.
The use of cut-and-fill stoping under conditions to which it is suited usually results in high recovery and little dilution, except in very heavy ground, as at the Morning mine, although some ore may be left in drift pillars where the stopes are silled above the level and in floor pillars. As previously stated, the fact that irregularities in the vein and tongues of ore can be mined and blind lodes prospected for in the walls, and, when found, mined as a tributary stope, makes a high recovery possible. Dilution is small, since the fill prevents sloughing of the walls, and any wall rock that comes in or horses of waste in the vein are left in the fill. Hand sorting is often employed to remove coarse gangue material with resultant raising of the grade of the ore trammed.
A high recovery with little dilution usually can be obtained with square-set stoping. This method finds its best application for mining in heavy ground where the ore is high-grade and any loss or dilution is to be avoided, regardless of cost. By square-set stoping and close filling, high-grade sections of an ore body below or adjacent to lower-grade ore often can be mined without disturbing the lower-grade sections, which changes in economic conditions or improved technology later may make it possible to mine profitably.
Recovery in block caving varies with conditions and is influenced by the amount of dilution the ore can stand, since high recovery usually involves high dilution also, and the amount of dilution permissible depends on metal prices. Thus, if the minimum grade of ore that it is profitable to handle is 1 percent copper, drawing should stop when, owing to dilution, the grade falls below this figure, regardless of whether or not all the ore has been recovered. Some dilution always results from “piping” of broken capping through the broken ore and from the margins, and the tonnage drawn from a block of ore usually is greater than the estimated tonnage in the block, whereas the average grade of ore usually is less than that estimated. If the margins of the deposit are very irregular in outline, either the extraction or the grade of ore recovered will suffer, as it is impossible to make the cave follow an irregular boundary closely. At Ray, Ariz., the dilution in drawing 40,000,000 tons of ore was estimated as 10 percent. At Inspiration, 110 percent of the estimated tonnage and more than 85 percent of the metallic contents are recovered. At Miami, operations in 13 completed stopes or blocks resulted in the recovery of 2.4 percent more copper than had been estimated previously, but 15.15 percent more tonnage was drawn, the average grade being 88.93 percent of the calculated grade. Careful regulation of drawing is essential to obtain minimum dilution and maximum recovery.
With sublevel caving the line of break may be controlled more closely around the boundaries than with block caving, as the ore is partly excavated by slicing, which can be confined strictly to the ore, and the blocks caved are relatively small both in vertical height and in horizontal area. However, as the backs are caved under a gob consisting of a mixture of broken capping, slice timbers, and flooring, which cannot always be prevented from breaking through and cutting off undrawn ore, some ore is bound to be lost; recovery usually is not as complete as with top slicing. Under the conditions on the Gogebic iron range, Michigan, where much of the capping carries 40 percent or more iron, a small amount of dilution does not seriously affect the grade of ore mined and the dilution from this source may offset tonnage of ore lost; the net result is therefore likely to be approximately 100 percent tonnage recovery, with a slight lowering of the total contained iron below that of the ore body proper.
Top slicing permits high recovery of ore with little dilution (provided a suitable mat is maintained) under conditions where any method of mining from the bottom upward would be difficult, hazardous, and costly. Small stubs of ore between the ends of slices or between the end of a slice and the cave are sometimes lost, and 2 or 3 feet of ore may have to be left around the margins of a deposit where a flat footwall comes up to the overlying mat.
Accurate figures on recovery and dilution are difficult to obtain unless waste and ore faces are measured and sampled after each round and the waste sorted out in the stopes is measured accurately. The finding during stoping of additional ore in the form of bulges in the lode or offshoots therefrom, inclusions of waste within the ore body, the sorting of waste from the broken ore, and the admixture with the ore, from sloughing, of waste and of capping or walls containing some ore minerals may combine to obscure the true situation with regard to recovery and dilution. Sometimes low-grade ore not included in the original estimates is found in mining under conditions such that it is profitable to extract it, and, on the other hand, low metal prices may necessitate leaving considerable ore that would be mined under higher prices.
It thus appears that “dilution” and “recovery” as applied to stoping results are not specific or rigid terms, and the data on recovery and dilution in table 37 should be interpreted with this in mind. In circulars dealing with cut-and-fill and square-set stoping, the authors have usually stated or implied that complete recovery is obtained and no figures are given; this accounts for the small amount of data on these methods of stoping in the table.
Rate of Extraction
Some stoping methods are inherently slow, whereas others permit rapid extraction of ore from the stope and, as previously stated, permit flexibility in rate of output. Thus, in cut-and-fill stoping the production rate cannot be forced very much as ore-breaking must be stopped in sections being filled, although production from an entire stope may be constant by breaking on one side of the ore pass while filling on the other side. In square-set stoping production, rate is slow (1) because the ore is broken in small blocks that usually can be drilled off in a short time, whereas timbering and filling consume a large part of the working shift and (2) because production cannot be forced in heavy ground without inviting danger of collapsing the stope. In open stopes where there are large areas of stope faces, production often can be forced by simply putting more machines to work. In sublevel stoping production can be speeded by simultaneous operations on all the sublevels and often by increasing the number of machines on each bench.
Forced caving, as employed at Alaska-Juneau, Beatson, and Climax, and block caving—all nonselective methods—permit a high production rate once ore production begins, although considerable time is consumed in preparatory work, especially for block caving. Best results are obtained with block caving if the ore is drawn at a uniform rate; therefore, any forcing of this rate is likely to cause the piping through of waste and incomplete breaking up of the ore.
The rate of output possible with any stoping method depends to a large extent upon the size of the ore body, especially the width, and the width of the stopes; a high rate of output is impossible in narrow stopes.
Effect on Recovery in Ore-Dressing Plant
The stoping method may affect the percentage of ore minerals recovered in the ore-dressing plant, especially where certain sulfide ores are concentrated by flotation. Thus, a stoping method that permits immediate removal of the ore after it is broken so as to preclude its partial oxidation before it goes to the mill may be desirable or necessary. Under these conditions, shrinkage stoping and block caving, in which large masses of broken ore are necessarily left in the mine for a considerable length of time, may be unsuitable.