Solvent Extraction of Nickel and Zinc
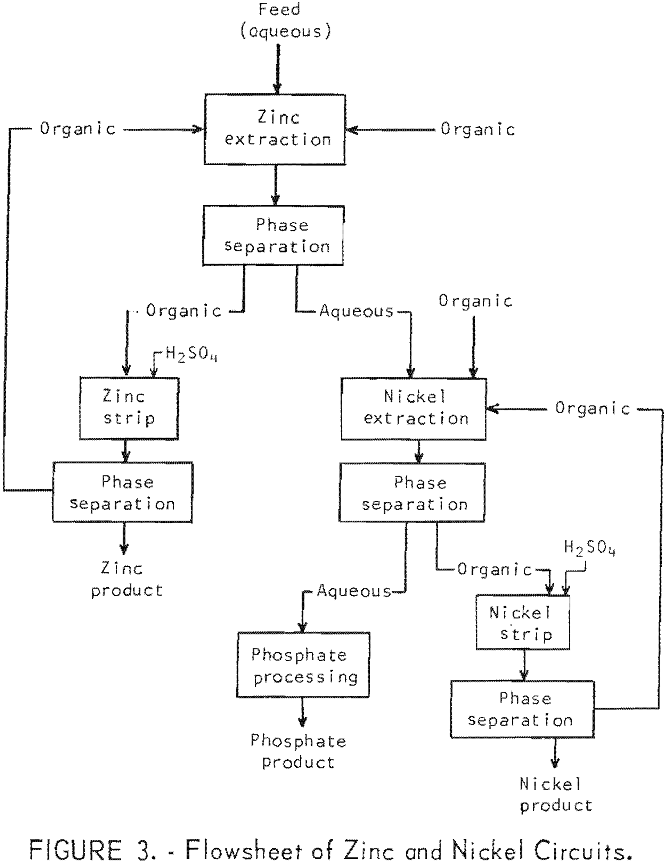
Solvent extraction of a waste solution from the phosphating of automobile bodies led to the following conclusions: Separate zinc, nickel, and phosphate products, essentially free of each others were produced. Zinc was 99 percent extracted by di-2-ethylhexyl phosphoric acid in kerosene, and nickel was 99 percent extracted by dinonyl naphthalene sulfonic acid in butyl ether. […]
Silver Chloride & Silver Bromide Thermodynamic
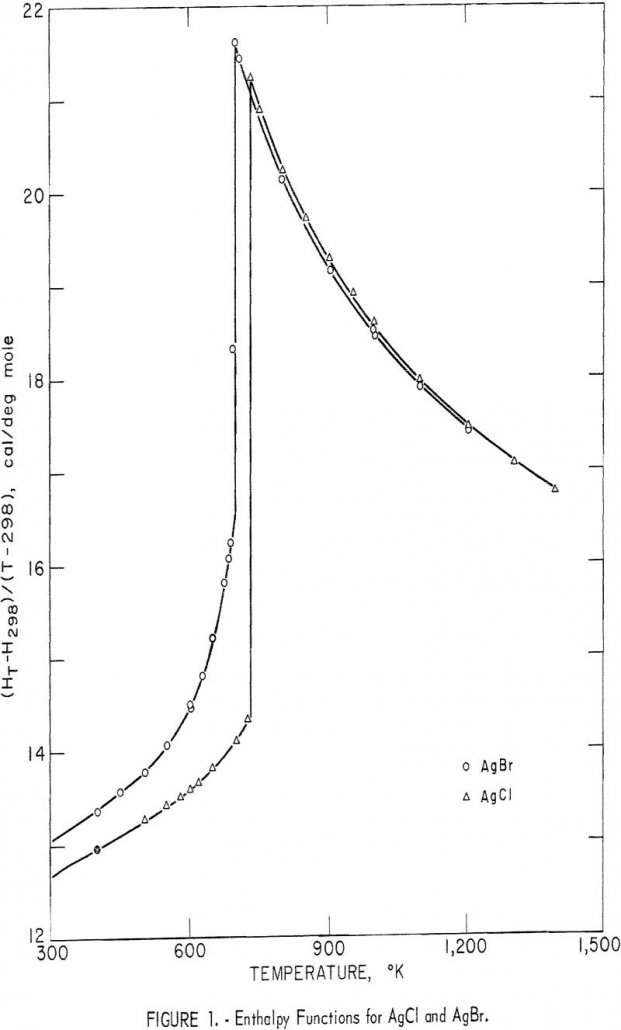
Adequate values for the standard heats and entropies of formation of silver chloride and silver bromide are available. However, thermodynamic calculations involving these substances have been hampered by the lack of accurate high-temperature enthalpy and entropy data. The enthalpy and heat capacity results reported in the literature are fragmentary and conflicting. As part of a […]
Recover Metals from Electroplating Wastes
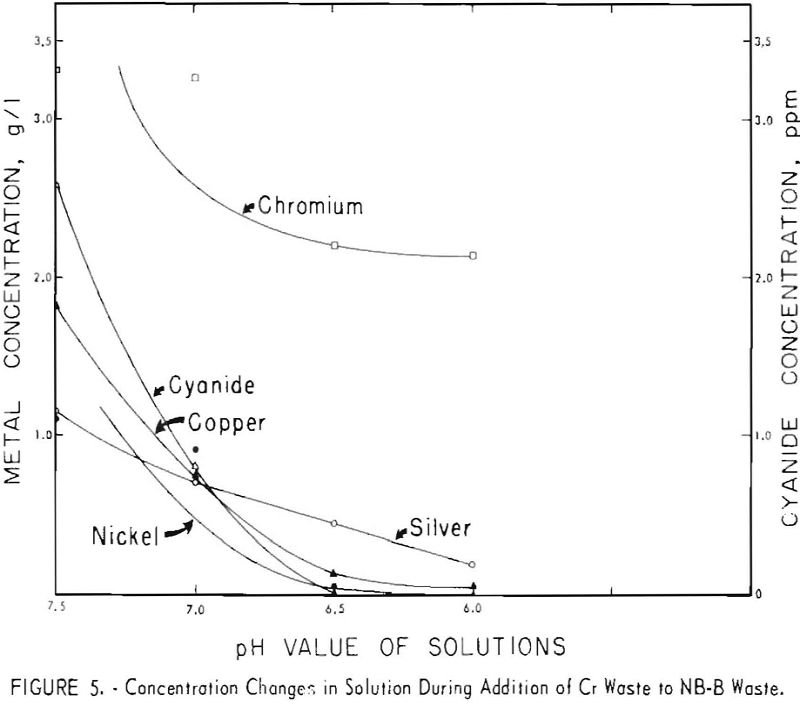
The waste-plus-waste treatment method can be successfully used on a variety of acid and alkaline electroplating wastes. The method is economically attractive because of the low cost of the waste-plus-waste addition step: No additional reagents are necessary, and the metal values are concentrated. In the five waste-plus-waste combinations investigated, combination of the two wastes caused […]
Convert Hydrous Calcium Sulfate to Hydrogen Sulfide
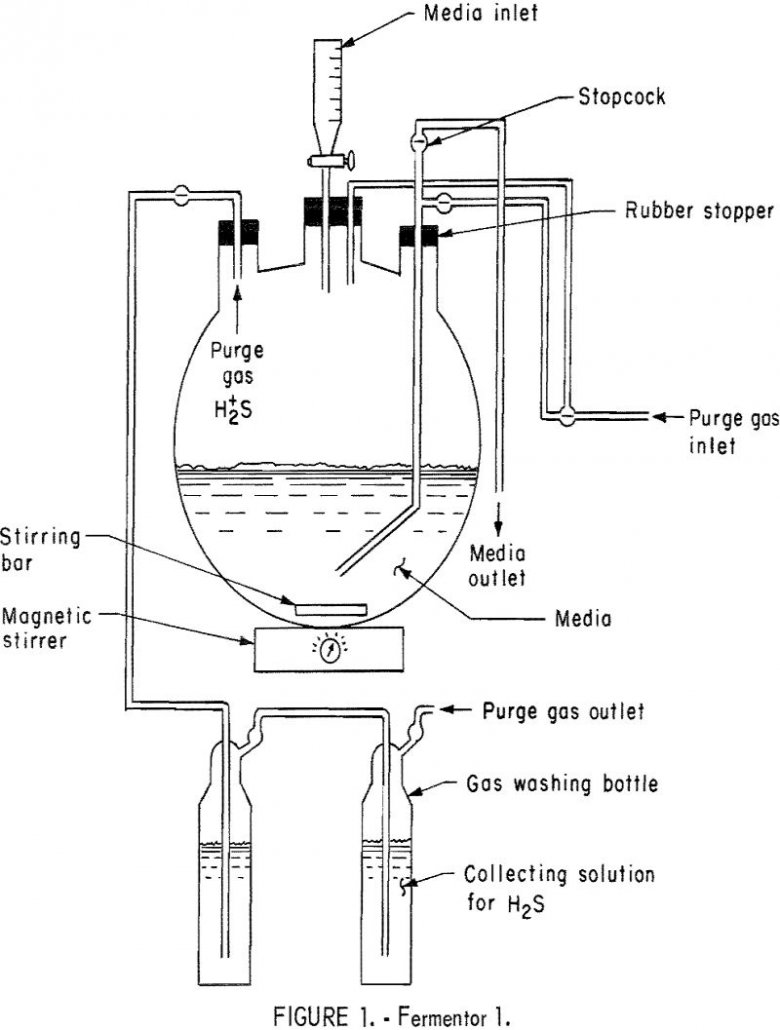
During the period 1960-65 sulfur consumption in the United States rose 40 percent to 7.96 million long tons. Since 1963, while demand has exceeded production, withdrawals from producer stocks have met the deficit. An assured steady supply of sulfur is essential for the national interest. Its applications are so diverse that the quantity used is […]
How to Measure Surface Tension of Molten Metals
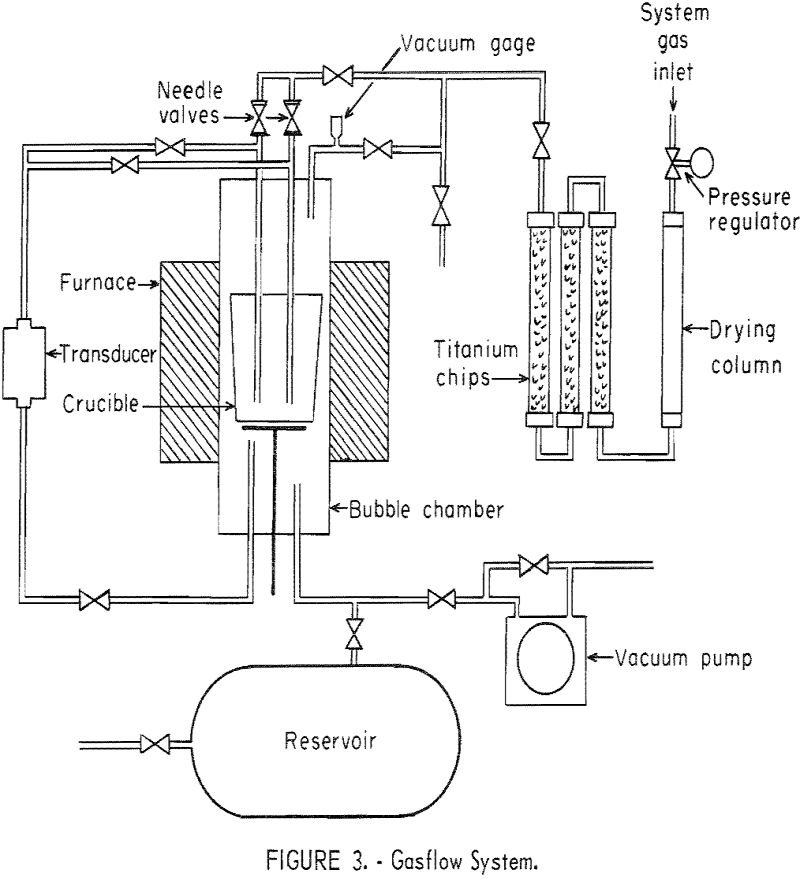
We been performing research on soft soldering with the objective of improving the strength of solder joints at elevated temperatures and pressures. Surface or interfacial phenomena and the factors affecting these phenomena are of major importance in soldering and brazing. A knowledge of the surface tension of the molten materials involved, such as the filler […]
Chalcocite Oxidation Roasting
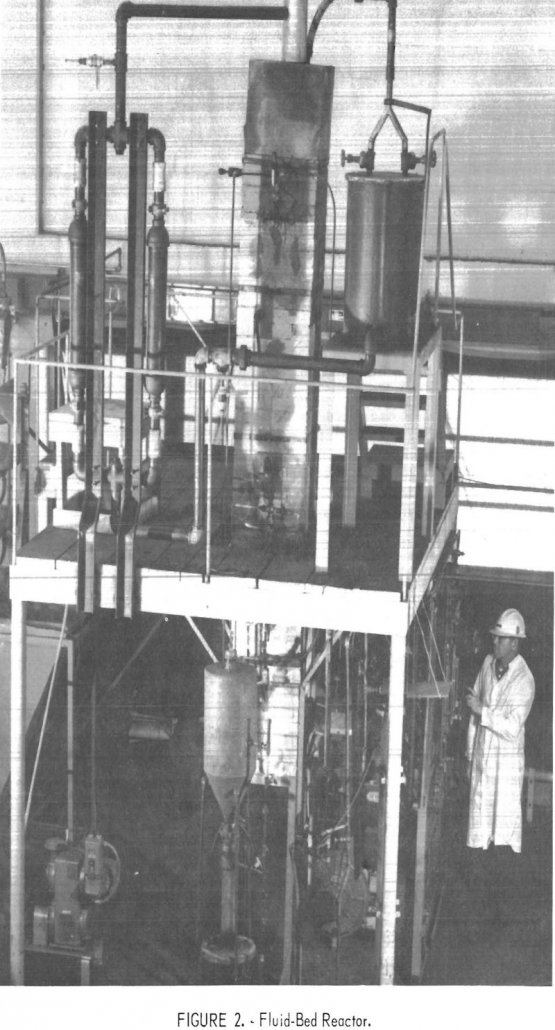
The Bureau of Mines Twin Cities Metallurgy Research Center is engaged in a study to uncover a cleaner, more direct pyrometallurgical process for winning copper from sulfides. The .initial target is low-sulfur concentrates containing primarily chalcocite (Cu2S). Development work, still in progress, points to a new and, perhaps, improved smelting procedure in which the following […]
How to Evaluate Face Respirator Fit

For the past few years there has been increasing interest among respirator users in determining quantitatively the degree of protection afforded by protective respiratory devices. Overall protection depends on both the efficiency of filters and/or sorbents used and the tightness of seal around the edges of the facepiece. The Bureau of Mines first introduced quantitative […]
Recover Mercury by Electrolytic Oxidation
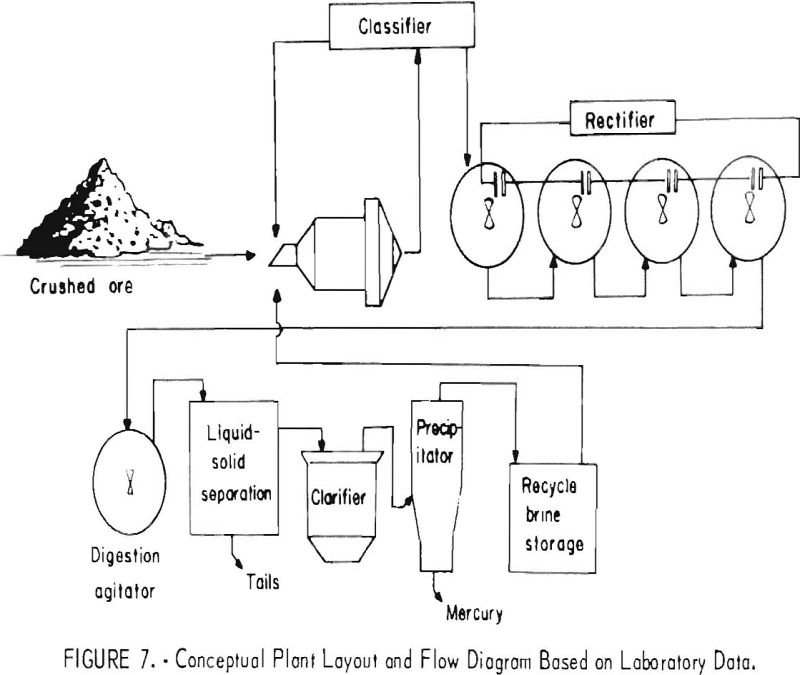
An aqueous oxidation treatment process developed by the Bureau of Mines has been shown to be effective for treating carbonaccous gold ores to improve gold recovery. Ozone, chlorine, sodium hypochlorite (NaOCl), and calcium hypochlorite [Ca(OCl)2] were all shown to be effective reagents for oxidizing the carbonaceous material in the ore. However, generation of oxidizing conditions […]
Tungsten Metal & Tungsten Carbide Electrolysis
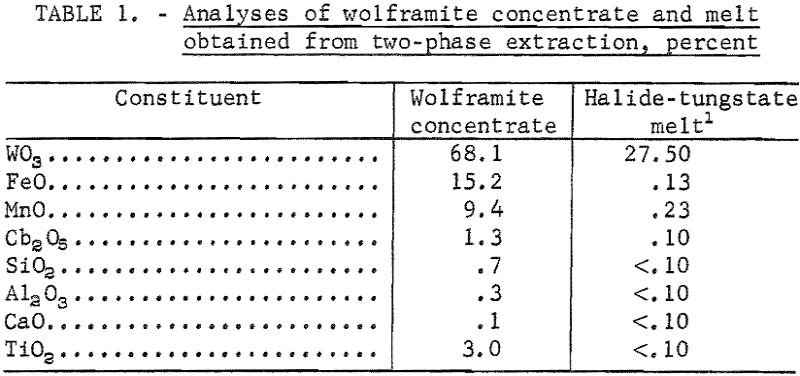
A high-temperature, two-phase extraction technique has been developed for the recovery of tungstic oxide (WO3) from tungsten-bearing minerals. The technique consists of dissolving scheelite (CaWO4) or wolframite in a system of two immiscible liquids-sodium chloride and sodium silicate-at 1,080° C. Tungstic oxide is converted to sodium tungstate (Na2WO4 ) and is transferred to the upper […]
Ion Exchange Resin to Recover Gold from Acid Solution
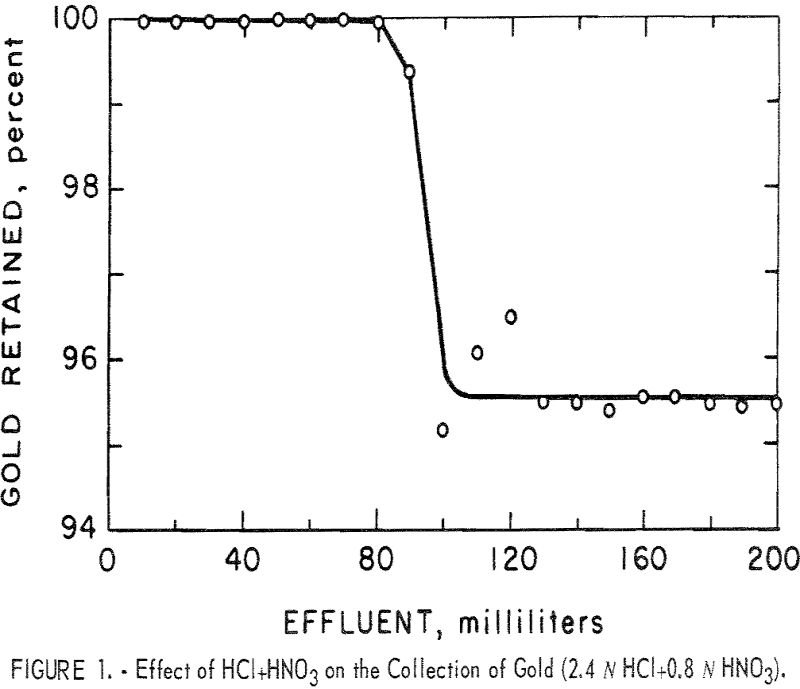
An ion exchange resin was found to quantitatively and selectively collect gold from acid solutions over a wide range of acid concentrations. Common metals at high concentration are not collected by the resin and they do not seriously interfere with the collection of gold. Alkaline cyanide solutions gradually destroy the capability of the resin to […]