How to Separate Columbium, Tantalum, Titanium and Zirconium
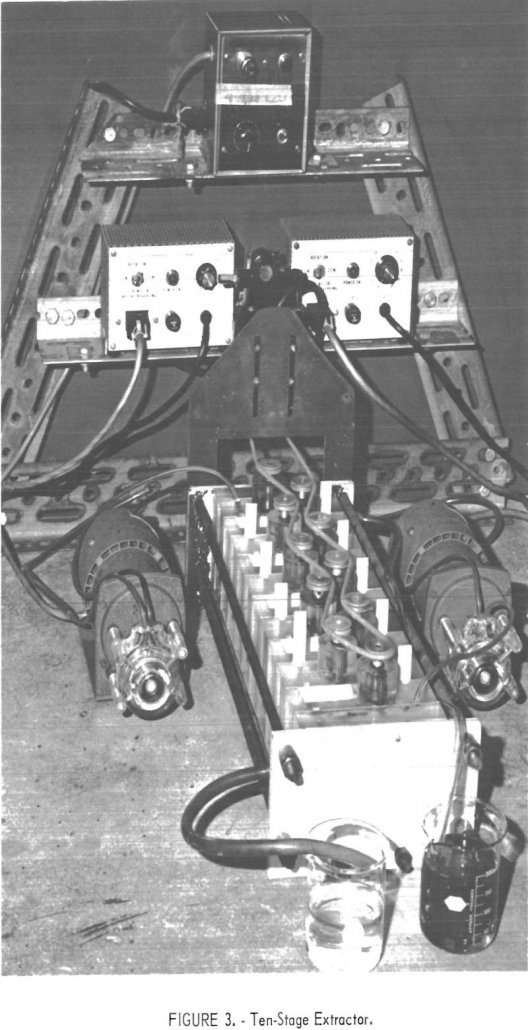
Waste products from the chlorination of rutile present a serious disposal problem because of the toxicity of some of the metallic ions when waste residues are dissolved in water and HCl gas is released into the atmosphere. Previous work showed that the water-soluble portion of the chlorination waste contained chloride and chloride-oxide complexes of Cb, […]
Mercury Detector
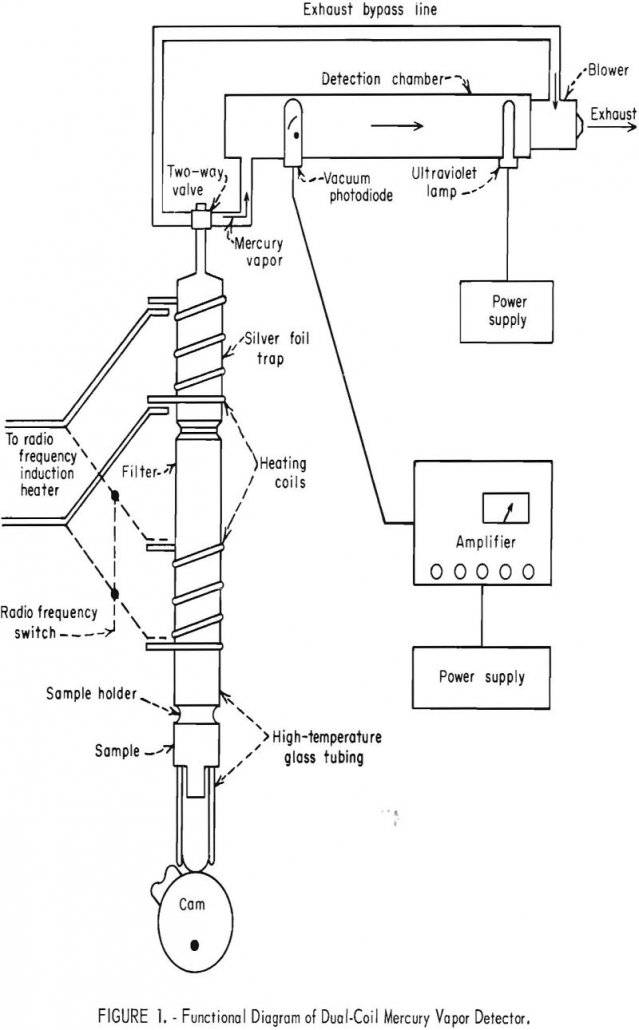
The Bureau of Mines recognized the need for a high-sensitivity mercury detector years ago and undertook the development of such an instrument at the Denver research facility. Although the detector has been used primarily in mining applications, the instrument could readily be adapted for use in pollution measurement. The amplifier circuit is designed for use […]
Use Recycled Waste Glass as Flux for Clay Firing
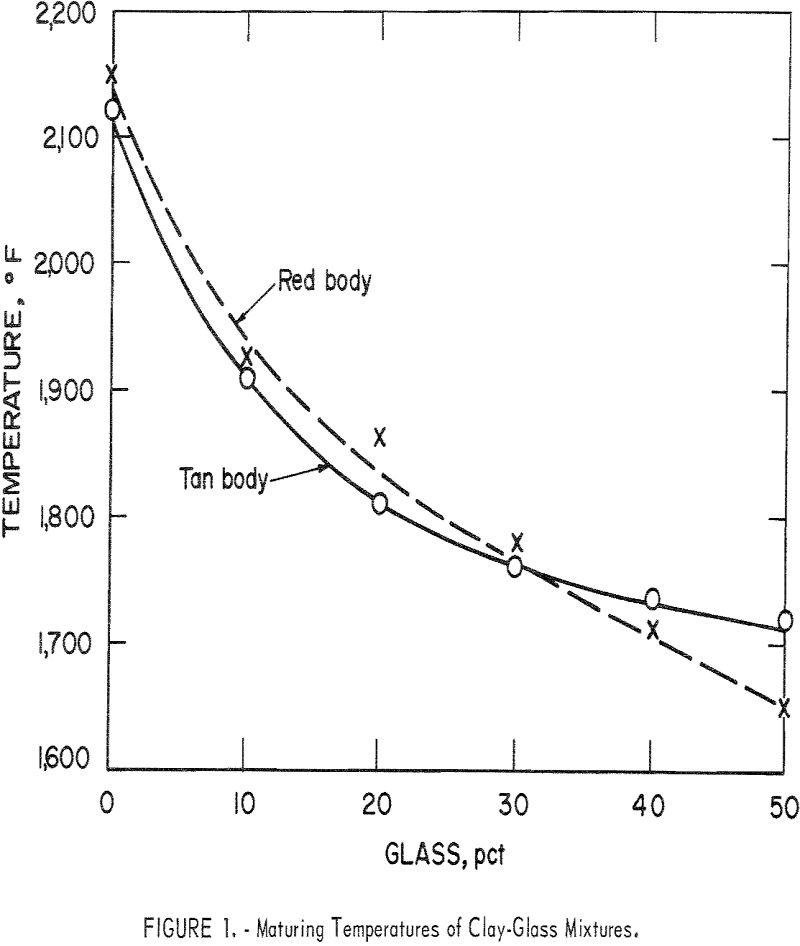
The Bureau of Mines Tuscaloosa Metallurgy Research Laboratory is conducting waste utilization research concerned with the development of building products from metal-free inorganic materials separated from municipal incinerator residues in the Bureau’s continuous residue-processing plant at the Edmonston Laboratory of the College Park Metallurgy Research Center. This is the third in a series of publications […]
How to Remove Bismuth from Lead
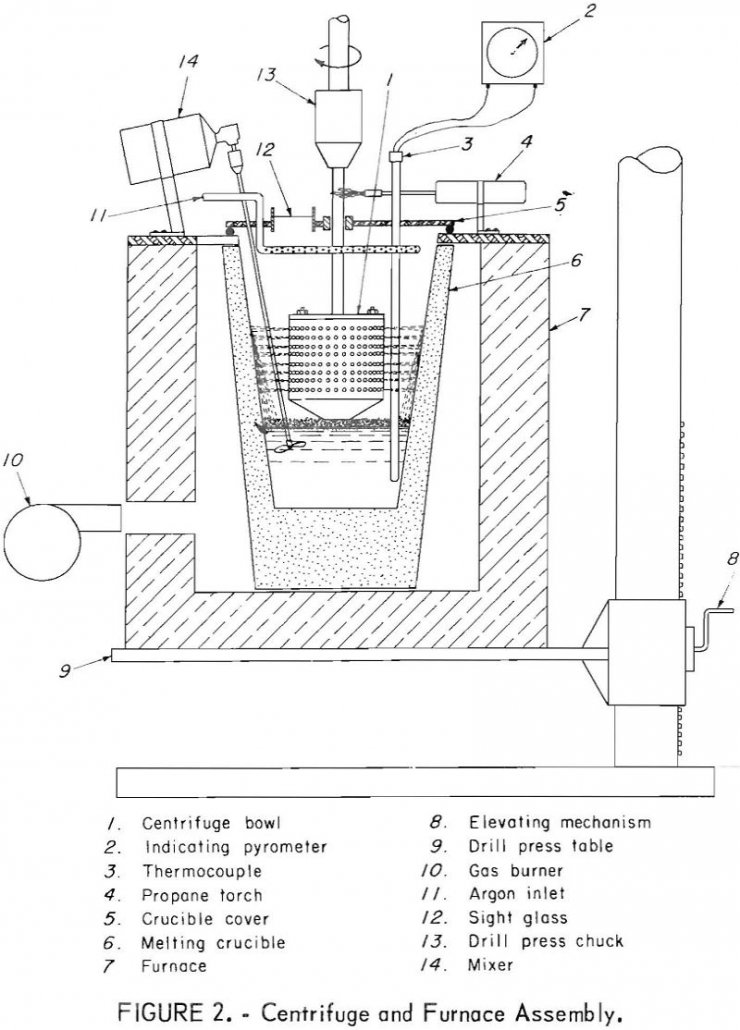
The Betts electrolytic process was for many years the only method available for debismuthizing lead Kroll suggested the use of calcium to form a high-melting-point Ca-Bi intermetallic compound that could be separated from molten lead. This process, however, was not used industrially. About a decade later, Betterton developed a commercially feasible process using a combination […]
Hydrochloric Acid Leaching Trisodium Phosphate, Zinc
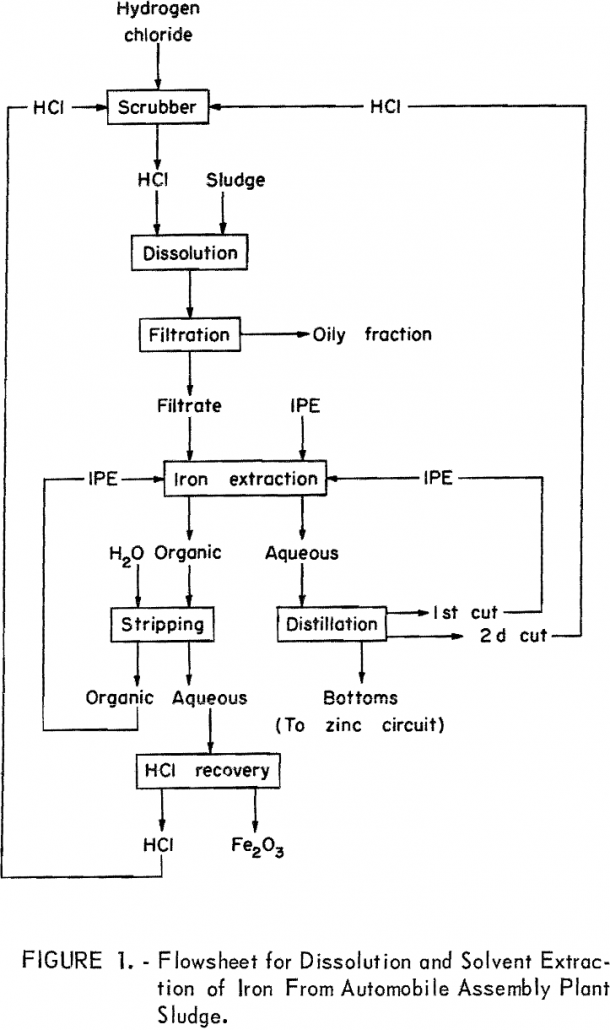
As part of its solid-waste research, the Bureau of Mines is engaged in a broad program to develop low-cost processes for recovering and recycling metals and minerals from a variety of industrial wastes. One benefit is the alleviation of pollution associated with many of these wastes. The phosphate coating of metals is widely used in […]
How to Reduce Surface Hot Shortness of Copper Bearing Steels
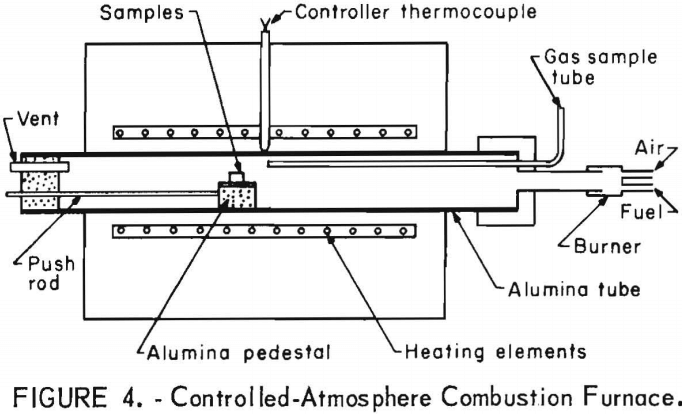
The use of controlled steel silicon content or the application of borax coatings showed promise in preventing molten copper from forming on the surface of steels containing up to 1 pct Cu when these steels were heated to 2,370° F (1,300° C) , a common temperature for rolling. By preventing copper formation during heating, surface […]
How to Recover Aluminum & Precious Metals from Electronic Scrap
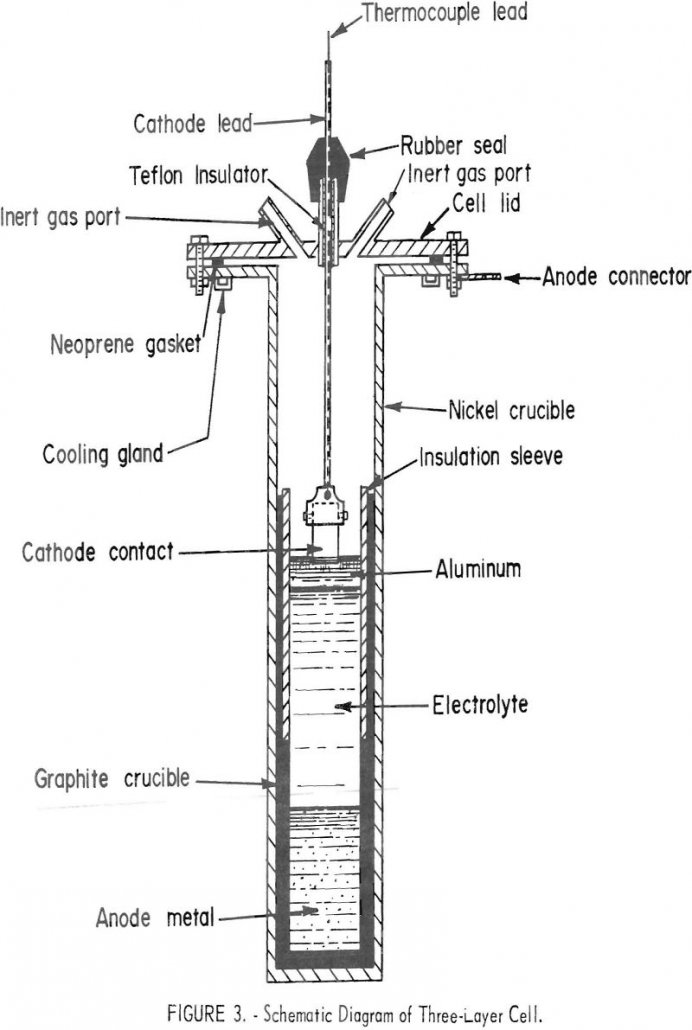
Our Solid Waste Program is directed toward three main areas of research: (1) Extraction of mineral, metal, and energy values from urban refuse; (2) recovery of mineral and metal values from wastes generated in the industrial utilization of raw materials and mineral-base products; and (3) upgrading and utilization of automotive scrap. The objective of this […]
Extraction of Manganese by Leaching
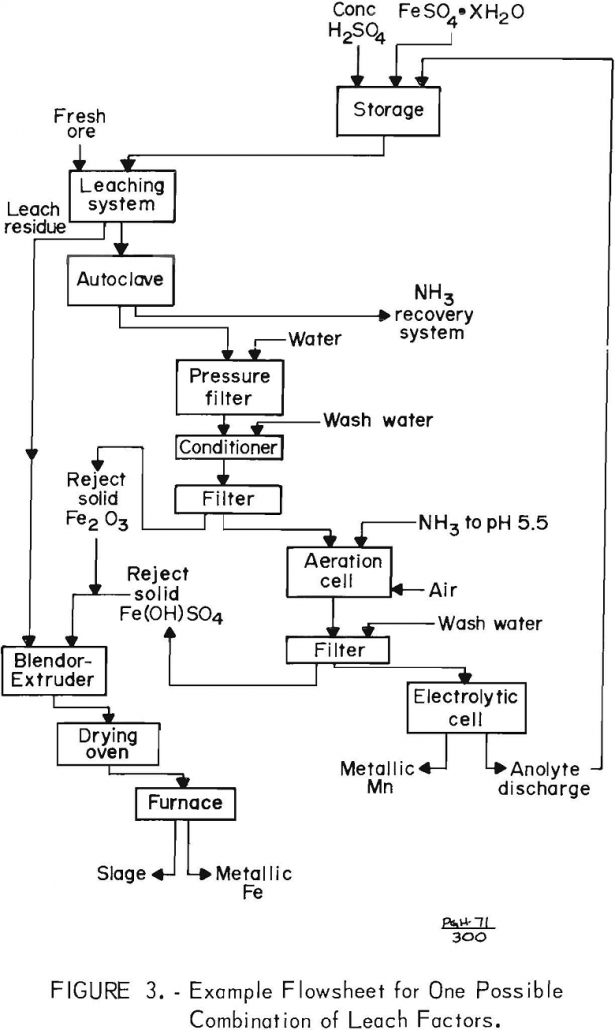
Demand for manganese continues to grow, but essentially all manganese used in the United States is imported. Although large deposits of low-grade manganese minerals are located in this country, domestic manganese producers have been unable to compete with the foreign ore except when subsidized by the Government. Desiring a degree of independence, both Government and […]
Recovery of Silver and Mercury by Electrolytic Oxidation
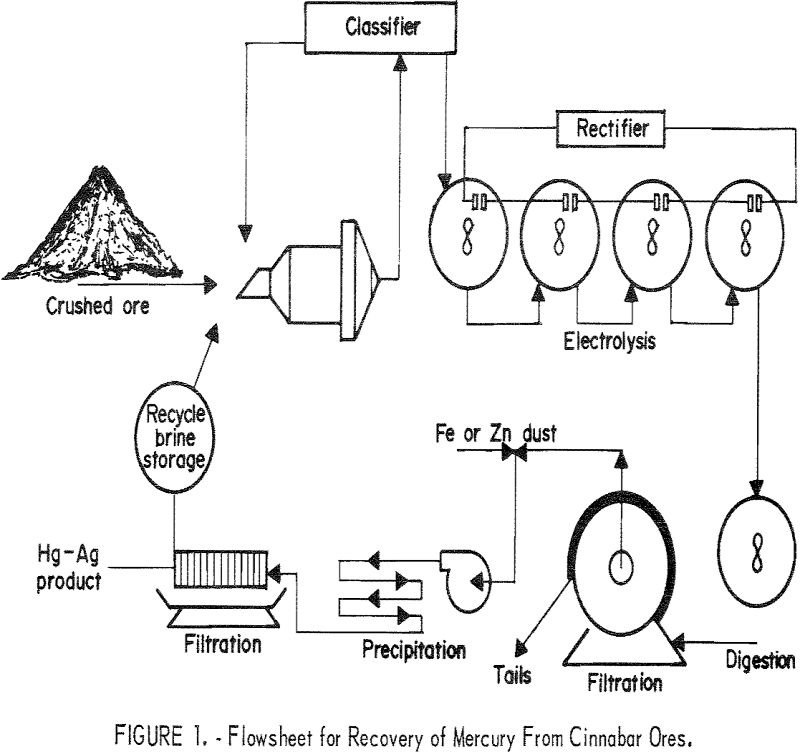
Silver was one of the first metals known to man, and metallurgical processes for the recovery of silver from ores date back into antiquity. Mercury amalgamation and retorting to recover metallic silver from slags, mine tailings, and scrap were in common use by the end of the 15th century. In 1557, the Patio process was […]
Drop Weight Impact Tester
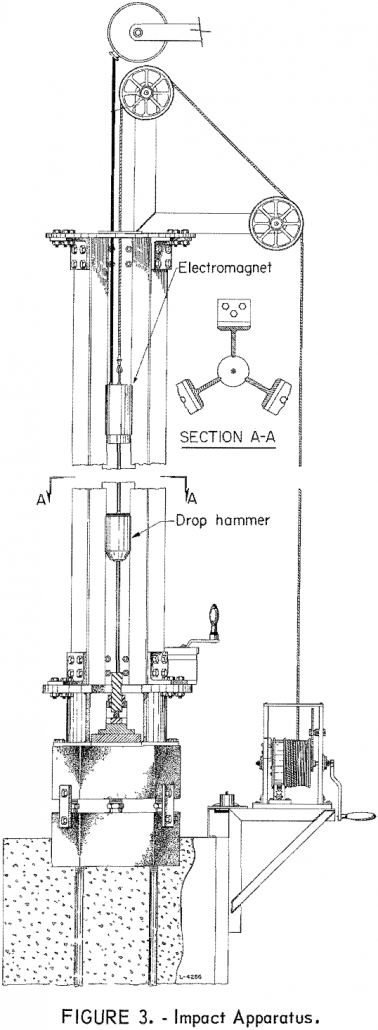
For many years, the impact test has been one of several techniques used to determine explosive sensitivity. This test has provided a useful index having practical value; however, it provides only an ordering of the sensitivities of a series of materials and, because of a lack of standardization in apparatus design and test conditions, comparison […]