Electrically Leach Molybdenum by Oxidation
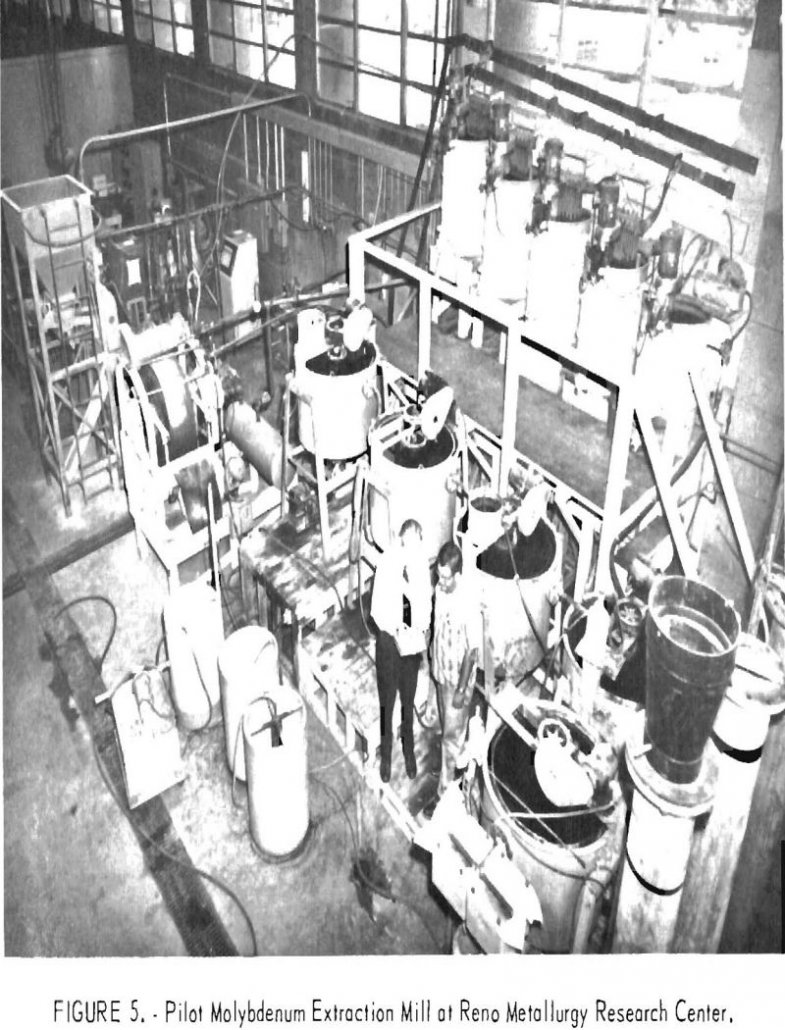
Classic flotation and roasting procedures for recovering molybdenum oxide from molybdenum source materials frequently result in low recovery of molybdenum. This is particularly true in molybdenum flotation from porphyry copper ores where difficulties can he encountered in refloating molybdenite which has been recycled to rougher and cleaner flotation sequences. Because copper-molybdenum separation may be less […]
Impact Crushing Size Distribution
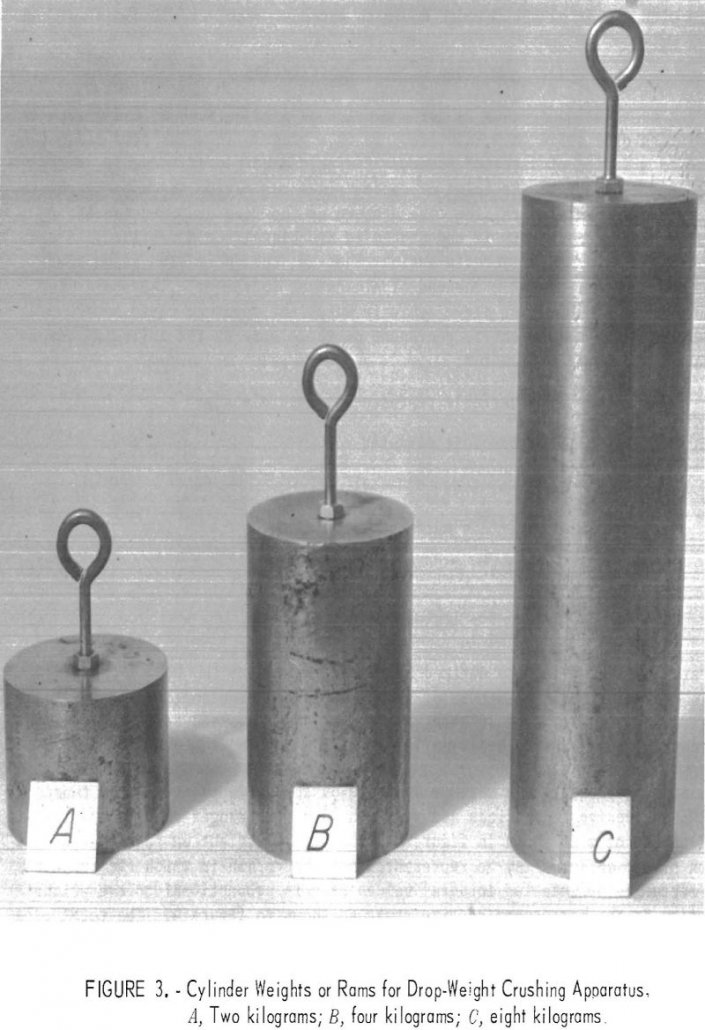
Although the comminution process has undergone much experimental study, there is not yet an adequate theoretical basis for predicting the mean size and size distribution of the product from a comminution machine. This lack is hardly surprising, since most of the considerable body of knowledge concerning the deformation of solids becomes inapplicable when the stresses […]
Extraction Process Sm2O3 Samarium Leaching
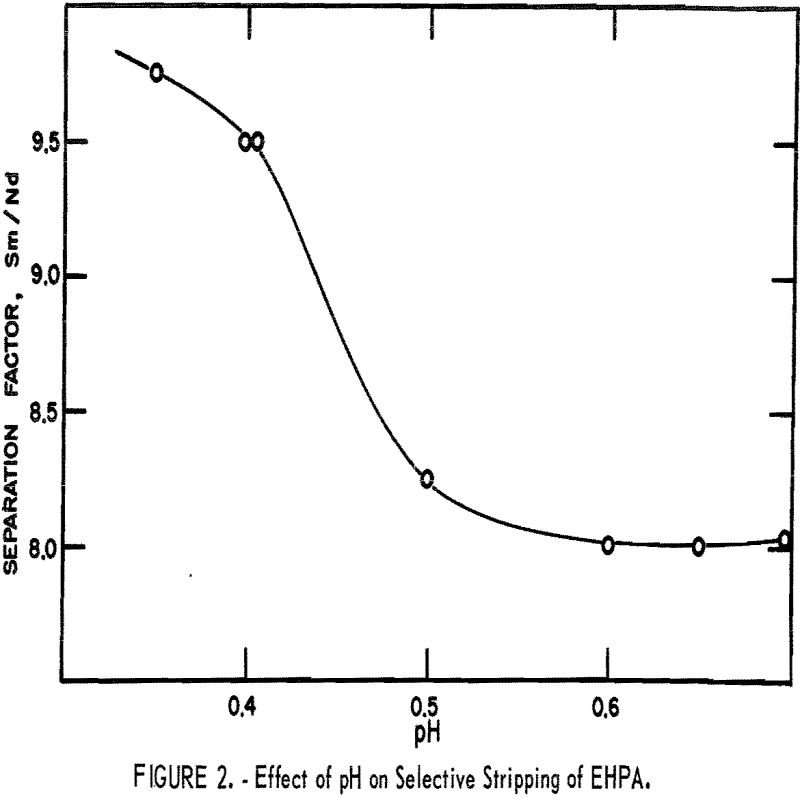
The growth in demand for certain lanthanides has resulted in the development of industrial processes for their separation and purification from source materials. These operations have resulted in the availability of substantial quantities of a byproduct mixture of rare-earth elements that contain mostly samarium and neodymium, and lesser amounts of praseodymium, cerium, and lanthanum. Potential […]
Electrowinning of Titanium
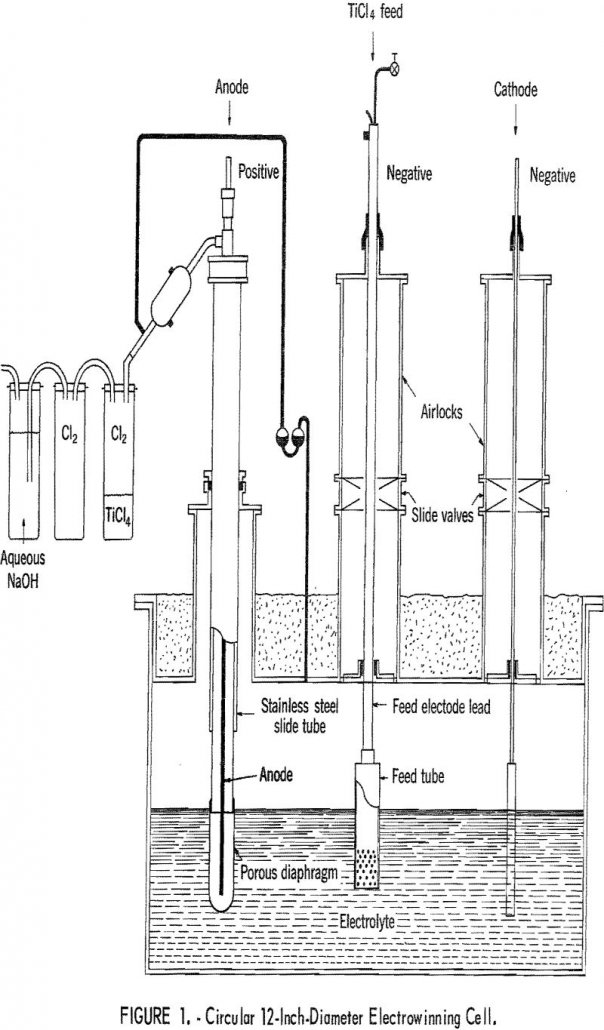
Composite diaphragms were constructed and used for the electrowinning of Ti from TiCl4 to eliminate some of the problems associated with diaphragm failure. High-purity titanium (Ti) was previously electrowon from titanium tetrachloride (TiCl4) fed into a molten electrolyte (520° C) composed of lithium chloride, potassium chloride, and titanium dichloride (LiCl-KCl-TiCl2). Two papers describing the work […]
Leach Gold by Sodium Hypochlorite / Chlorine

The extraction of gold from ores that contain carbon and organic compounds has presented a problem to the cyanide mill operator ever since the widespread adoption of this classical dissolution technique in the late 1800’s. The problem was studied in 1924 by Leaver and Woolf. More recently, Hedley and Tabachnick indicated that a general solution […]
Classification Solid and Liquid Oxidizers
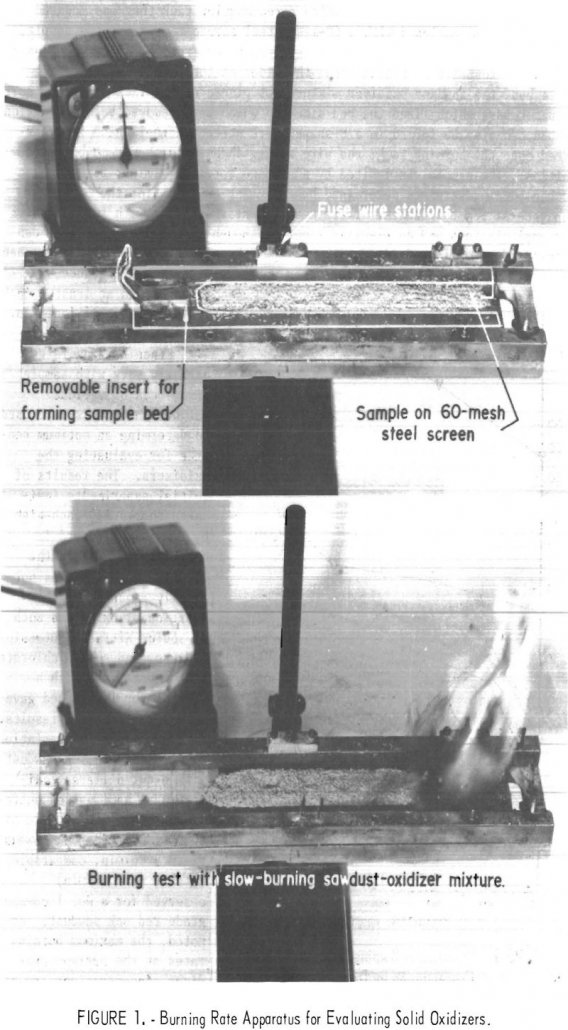
We recently prepared recommendations on methods of evaluating and classifying flammable liquids and solids for use in government transportation regulations. This report is the third in this series and describes the classification of oxidizing materials which are defined in the transportation regulations as substances that can yield oxygen readily to stimulate the combustion of organic […]
Classification Flammable Solids
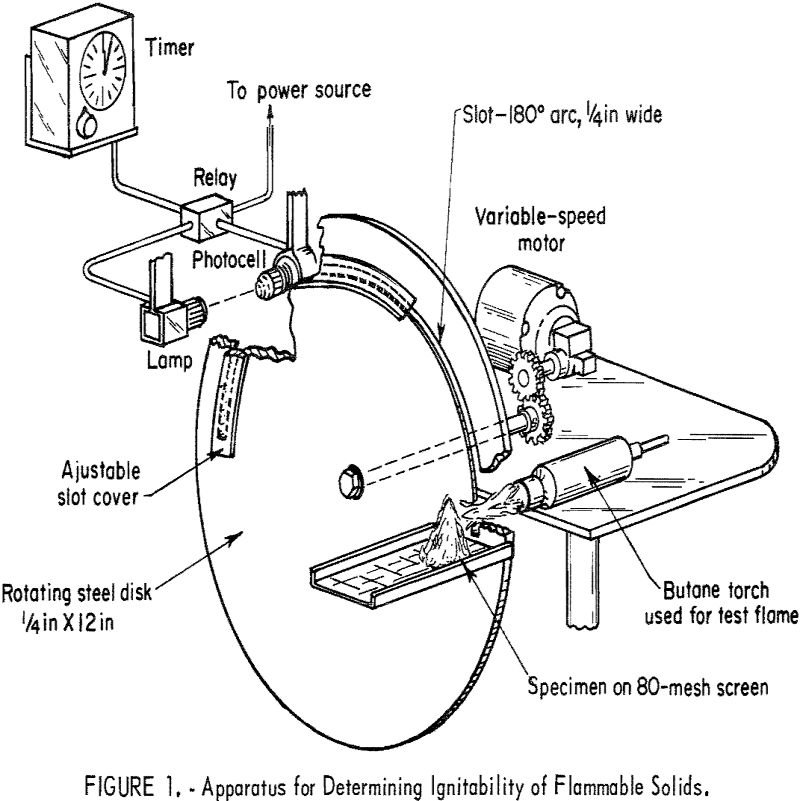
The Bureau of Mines research programs are partly directed to developing safety guidelines for the reduction of fires and explosions in industries that produce, transport, or utilize mineral fuels and their products. As a result of a request by the Department of Transportation, the Bureau is evaluating test methods for classifying hazardous materials and developing […]
Bin Hopper Flow Design & Engineering
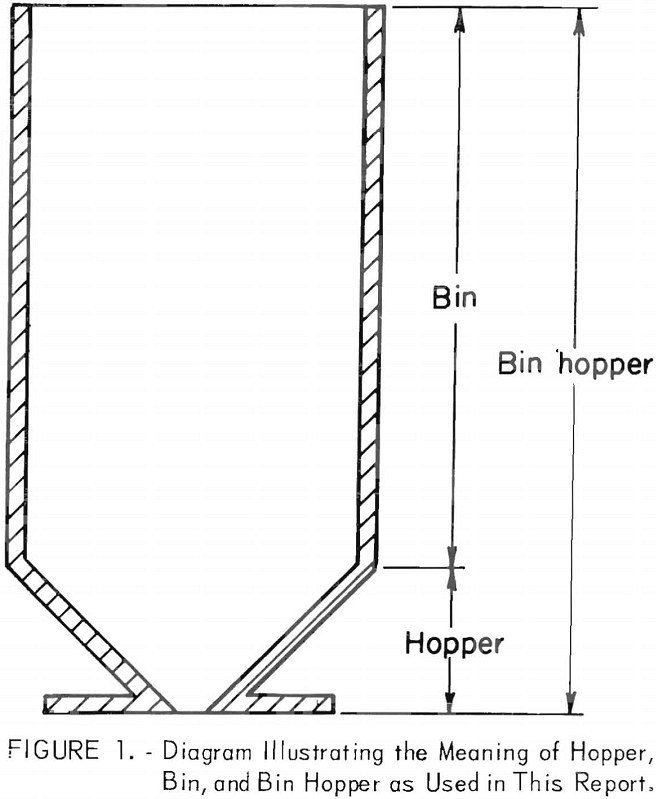
A detailed Bin Hopper Flow Design & Engineering Study: The mining industry in the United States alone produces nearly 4 billion tons of new bulk materials annually that has a mine-mouth value in excess of 20 billion dollars. The potential for realizing substantial savings in mining and processing costs through improved materials handling systems design […]
Photoelectric Charging & Electrostatic Separation
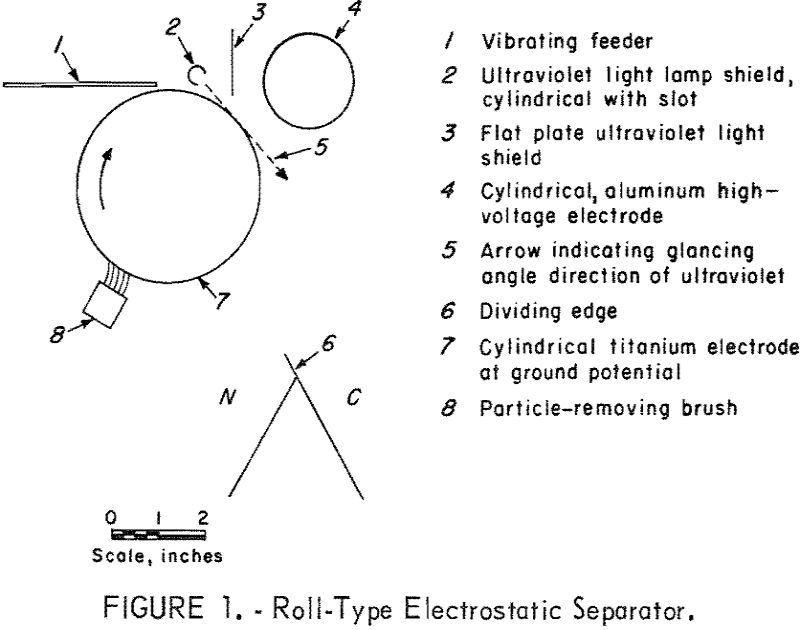
Electrostatic separation is used when froth flotation fails, such as with oxidized ores, or where there are similarities in response with magnetic and gravitational methods, or when the use of water is to be avoided. Theoretically, for fine-size particles the electric field has an advantage over the magnetic field in that the viscosity-limited particle velocity […]
Effect of Preheating Iron Ore Pellets
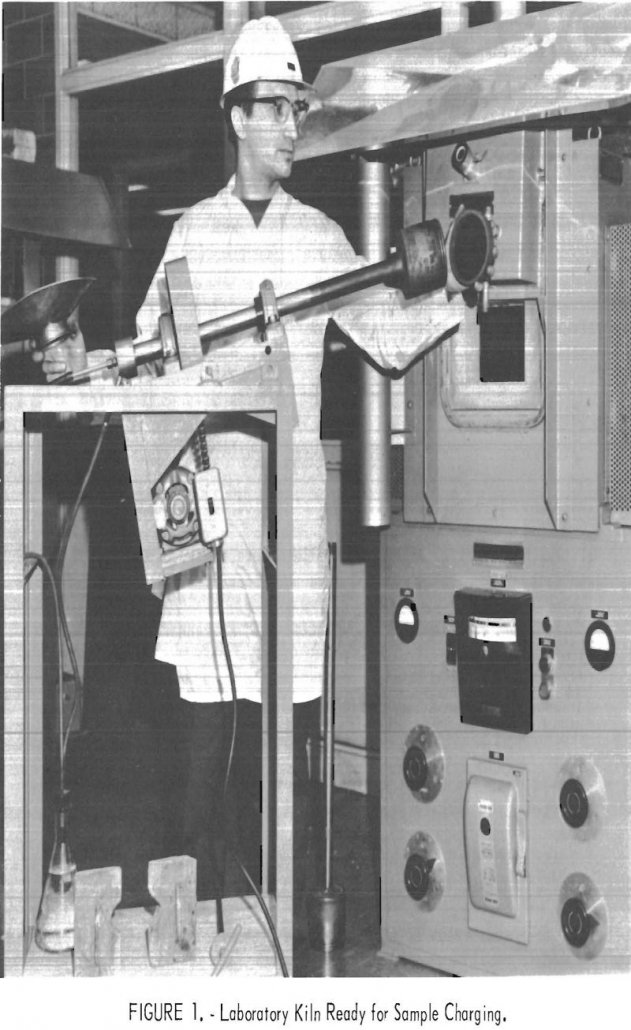
The production of pre-reduced iron ore pellets involves the expenditure of considerable capital and energy. Both prereduced and oxide pellets can be produced in similar equipment by using reducing and oxidizing processes, respectively. However, the throughput for a 5-m-ID by 50-m-long kiln with a preheating grate is 425,000 metric tons per year of ore, according […]