Zirconium Oxide Molds for Molybdenum
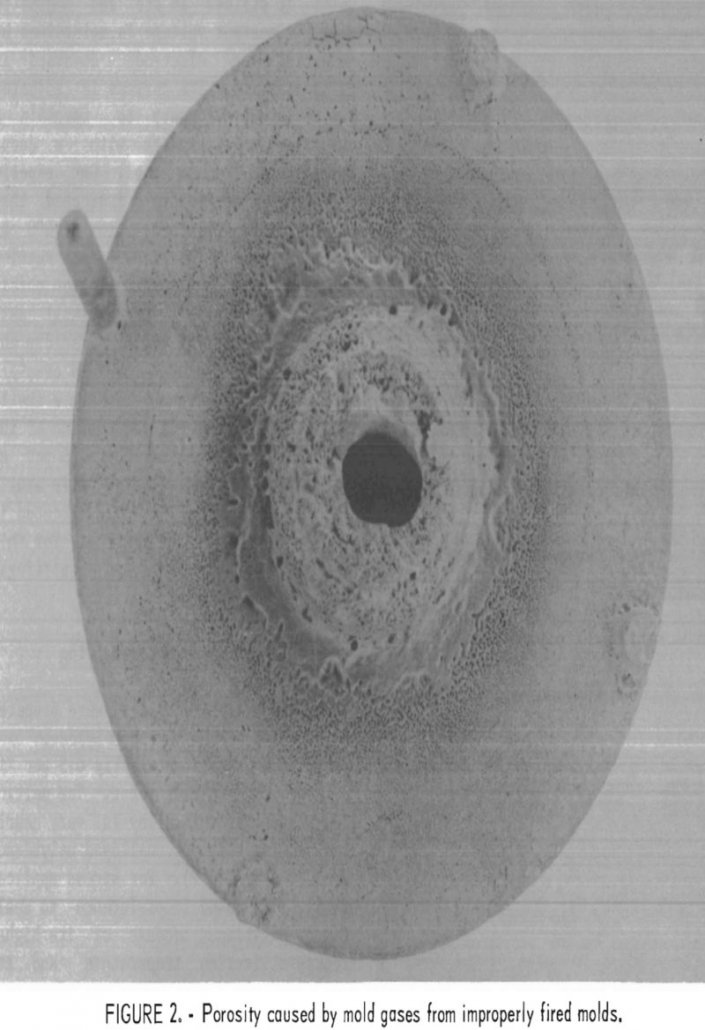
One of the goals is to minimize the requirements for critical and strategic mineral commodities through conservation and substitution. As a part of this effort, the Bureau conducted research to develop molybdenum as a potential substitute for alloys containing the critical and strategic metals nickel, chromium, or cobalt. As expressed in Iron Age, this Nation […]
Radial-Axial Loading Splitting Tool
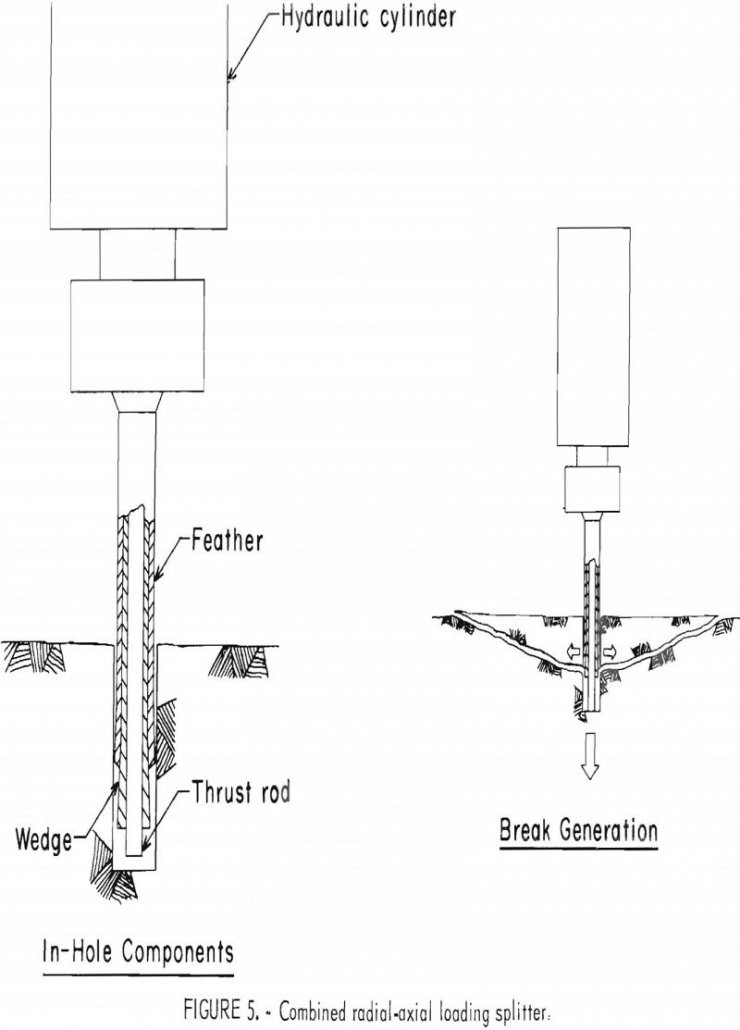
As a part of the Bureau of Mines research program to develop new mining methods for underground bedded deposits, a rock splitting tool capable of applying both radial and axial forces is being investigated as a primary excavation tool. From the long-known hammer-driven wedge and ice expansion methods of propagating existing cracks in rock, mechanical […]
How to Recover Chromium Nickel Cobalt Laterite
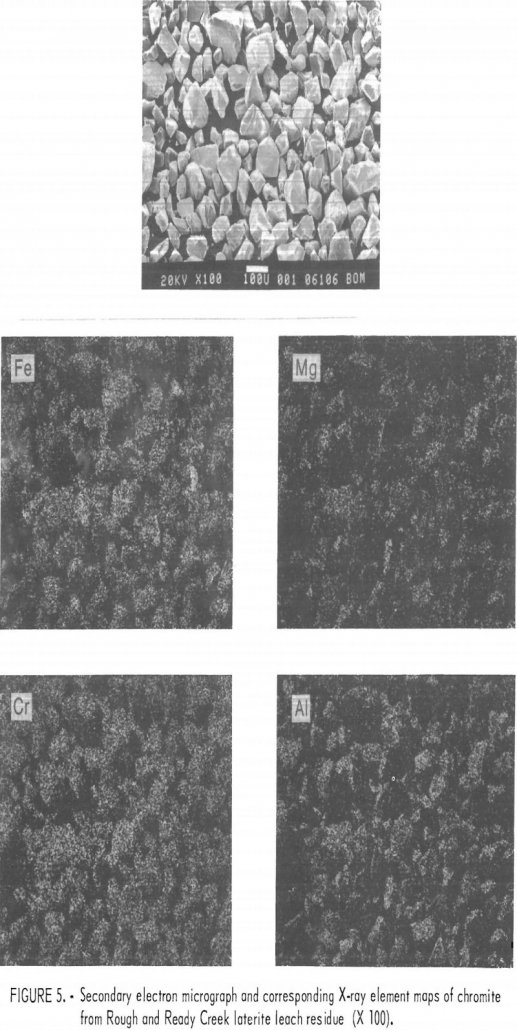
Chromium is essential to modern industry, and there are few acceptable substitutes for most of its metallurgical and chemical applications. In 1979 the United States consumed 610,000 tons of chromium, of which about 10 pct was supplied from secondary sources from within the country; the remainder was imported. Annual consumption is projected to grow to […]
Gas Fired Iron Ore Pelletizing Kiln
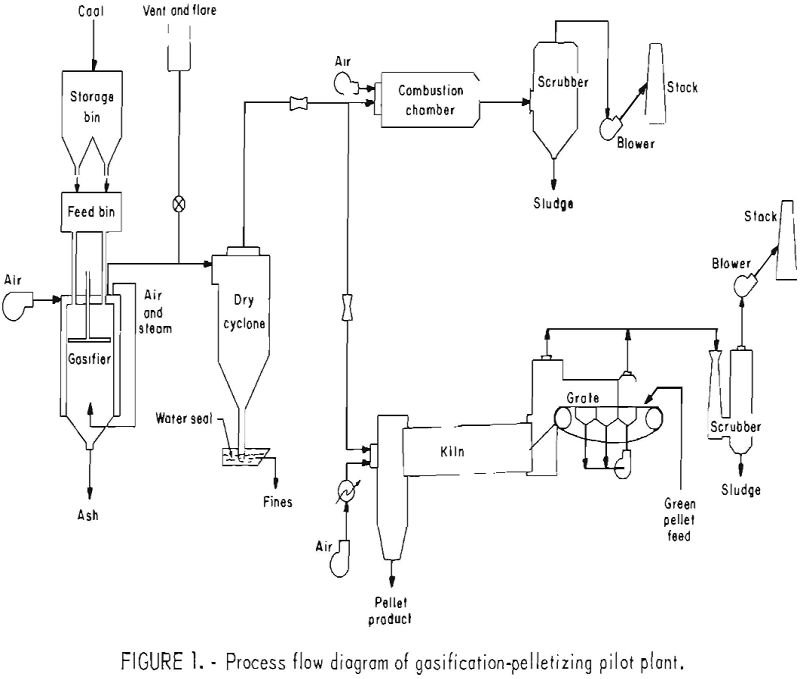
The iron oxide pelletizing industry is very energy intensive and relies heavily on natural gas to fire pellet-indurating furnaces. Approximately 75 million long tons of iron oxide pellets are produced in the United States each year, requiring a fuel input of about 55 billion ft³ of natural gas. During the past several years the industry […]
How to Recover Barite from Waste Pond Materials
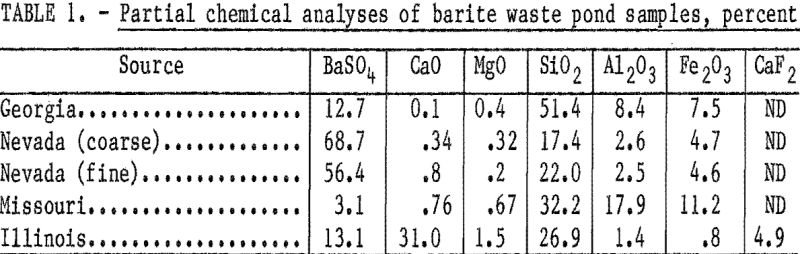
A major goal of the Bureau of Mines is resource conservation, which includes (1) maximizing mineral recovery from domestic resources and (2) recovering mineral values currently lost in scrap and waste materials. To help meet this goal, the Bureau of Mines has been investigating the recovery of various potentially valuable minerals from mineral- processing wastes. […]
Aluminum Extraction by HCl and Fluoride Leaching
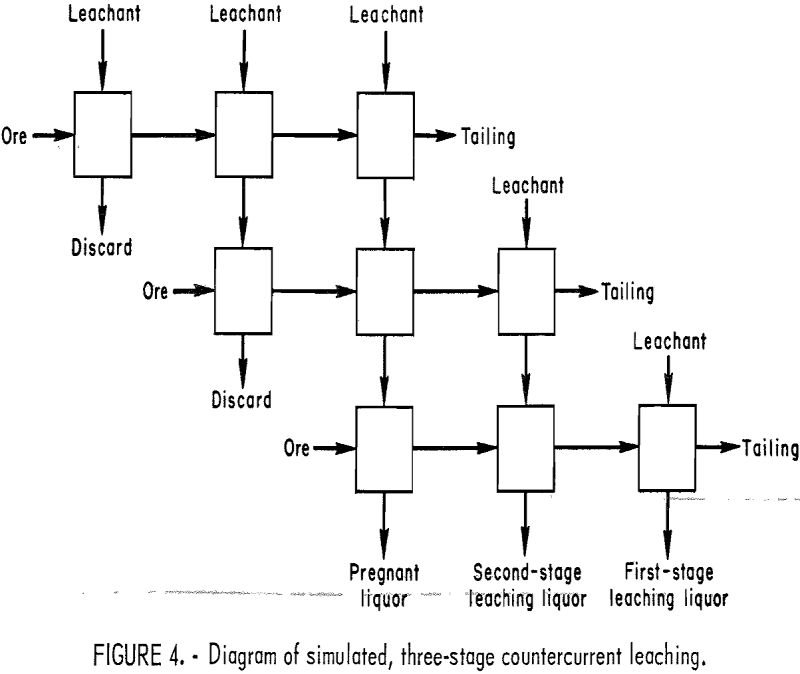
The United States depends on imports of bauxite and alumina for most of its aluminum requirements. To reduce this dependence, the Bureau of Mines conceived a raw materials-process technologies matrix as a means of systematically investigating the technology options available for processing domestic aluminum resources. In 1973, a research program was initiated based on this […]
Chemically Bonded Refractories
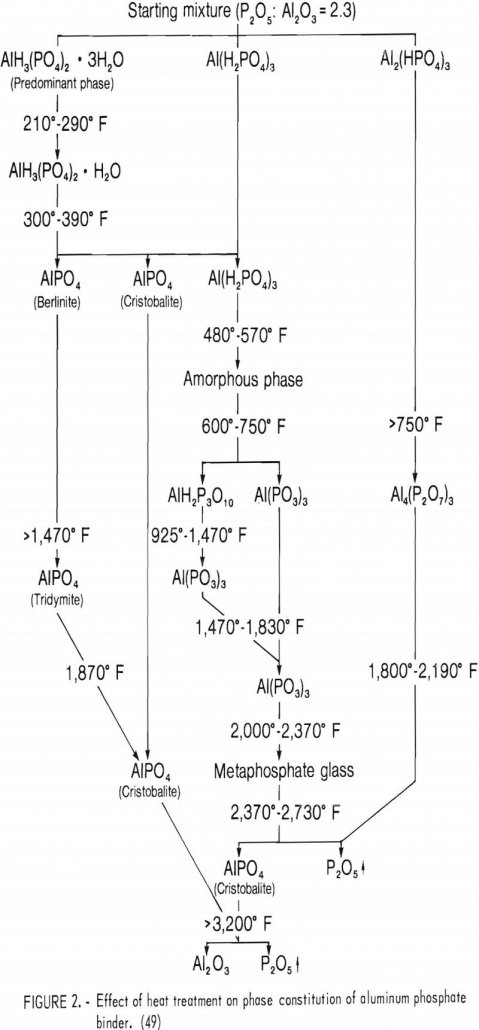
Improved ceramic materials are in constant demand for processes involving severe chemical, corrosive, and thermal environments, especially at high pressures. During the past decade, demand for higher quality ceramic materials has significantly increased. This is true, for example, in the steel industry where oxygen steelmaking has increased production rates and operating temperatures, thereby compounding the […]
Effect of Sodium Chloride Leach on Copper Chalcopyrite
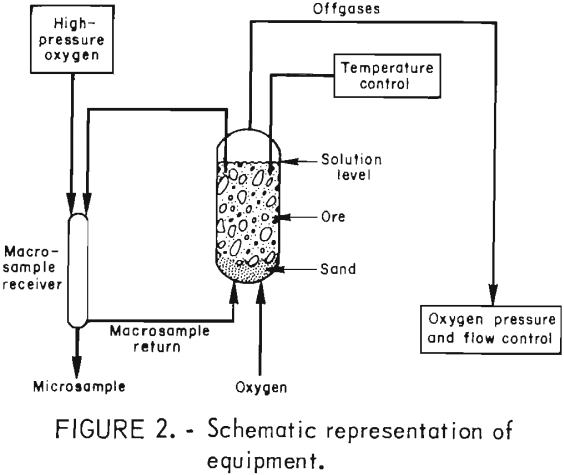
As part of the mission of the U.S. Department of the Interior’s Bureau of Mines to help insure the continued viability of the domestic minerals and materials economy, and to help maintain an adequate minerals base, research was conducted to investigate in situ leach techniques for extraction of copper from a chalcopyrite ore. Successful application […]
Recover PGM by Matte Smelting and Leaching
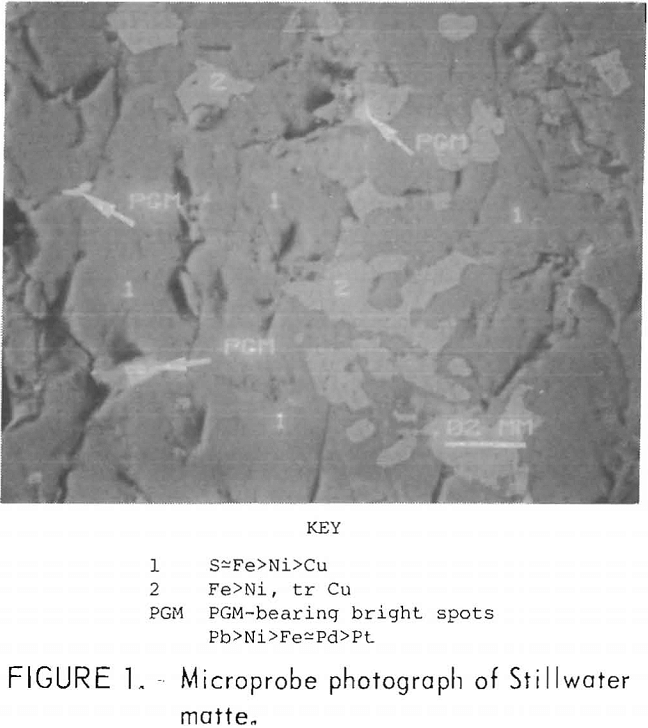
An important objective of Bureau of Mines research efforts is to investigate alternative technologies that may be applicable to domestic mineral resources. In addition, the Bureau seeks to avoid some of the difficulties or problem areas associated with conventional processing methods. In this regard, the Bureau has studied flotation concentration and extraction of platinum-group metals […]
How to Remove Molybdenum Process Plant Water
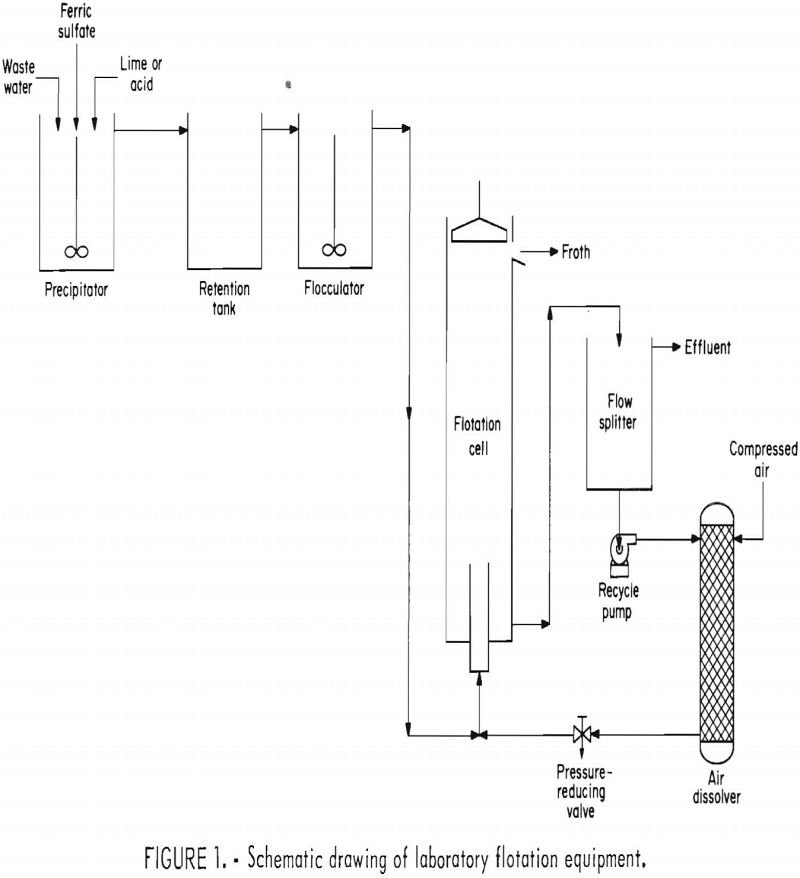
The minerals industry uses large volumes of water in many of its operations. Because of the rapidly decreasing availability of water in many areas and the need to control pollution, efficient and economical processes for purifying mineral waste waters are urgently needed. As part of a continuing program to devise technology for abating pollution caused […]