Table of Contents
Zinc Electrolysis was studied to help maintain an adequate domestic minerals base, the Bureau of Mines is investigating an aqueous chlorine-oxygen leaching procedure to produce ZnCl2 from sulfide concentrate and is also studying a fused-salt electrolytic technique to produce zinc metal from ZnCl2.
Several chlorine leach/electrolysis methods for treating zinc ores and concentrates have been reported. Swinburne obtained a patent in 1897 on a process for treating sulfides with chlorine, electrowinning metal from the fused chlorides, and recycling the chlorine. Ashcroft joined forces with Swinburne in 1898 and subsequently summed up 35 years of work in an extensive report. Ashcroft foresaw no problems in implementing chlorine smelting of zinc, but materials for cell construction and the quality of his ZnCl2 feed posed serious production problems. Concurrently, Threlfall conducted a study similar to Swinburne’s and Ashcroft’s work. He arrived at essentially the same conclusions and cell design as Swinburne and Ashcroft.
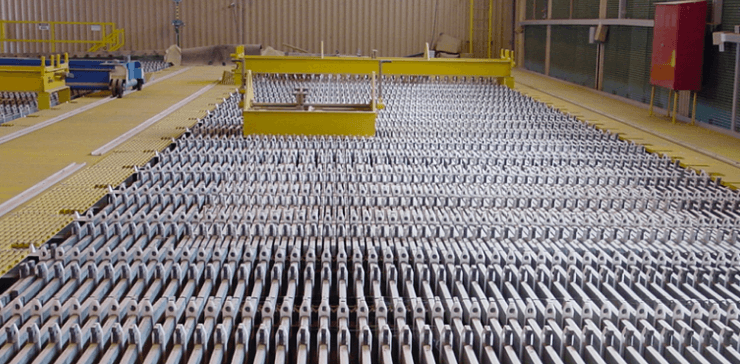
Zinc Chloride-Alkali Metal Chloride Electrolytes
Several others tried to scale up the process. Ralston, at some time between 1914 and 1921, successfully produced zinc by fused-salt electrolysis while working for the Hooker Electrochemical Co. of Niagara Falls, N.Y., but discontinued the project because the cell voltage was inordinately high, even with the closest possible electrode spacings. Malm conducted basic research on the process beginning about 1907, and designed a $2 million plant. His plans failed to materialize because of financial problems, but the idea was carried out by the Bunker Hill & Sullivan Mining Co. of Kellogg, Idaho. The plant was completed in 1914, but never operated because of technical difficulties.
More recently, laboratory-scale investigations have been conducted by Kammel, Fray, and the Bureau of Mines into the effect of bath composition on energy and current efficiency in electrowinning zinc by fused-salt electrolysis. These investigators showed that zinc could be electrowon at current efficiencies of over 90 pct and with energies comparable to those required by present industrial methods. However, a basic disagreement exists between the work of Fray and that of Kammel and the Bureau of Mines. Kammel and the Bureau of Mines found that the highest current efficiency and lowest energy requirement were obtained with the lowest concentrations of ZnCl2 that could be tolerated without freezing of the electrolyte; Fray found that the highest current efficiency and the lowest energy requirement were obtained at ZnCl2 concentrations between 39 and 56 mole-pct, with rapid deterioration in results at lower ZnCl2 concentrations. The high voltage and low current efficiency that Fray observed with ZnCl2 concentrations below 39 mole-pct may have been due to the formation of a frozen layer of electrolyte on the electrodes; this often occurs with electrolyte compositions near the freezing point.
The objective of the work reported herein was to relate the properties of various ZnCl2-alkali metal chloride electrolyte systems to the production of zinc metal. The studies include determinations of liquidus temperature, bath stability, cell voltage, and current efficiency with ZnCl2-NaCl-KCl, ZnCl2- NaCl-LiCl, and ZnCl2-KCl-LiCl electrolyte systems; sludge formation in the ZnCl2-NaCl-KCl, and ZnCl2-KCl-LiCl systems; and the use of large-scale, internally heated cells.
Procedure & Results
The broad scope of the investigation required the use of five different experimental groupings, each requiring different procedures and equipment.
All chemicals used in the tests, except ZnCl2, were reagent grade. The ZnCl2 was technical grade, containing the impurities shown in table 1. All chemicals were dried by spreading in thin layers in trays exposed to circulating air at 150° C. This reduced the oxygen content of the ZnCl2 to 0.45 pct. Oxygen content differed little between air-dried and vacuum-dried ZnCl2, provided there was no visible moisture present prior to drying.
Liquidus Temperature Diagrams
A systematic evaluation was made of the fused-salt systems that appeared suitable for use as an electrolyte for zinc electrowinning. An evaluation of the binary ZnCl2-KCl, ZnCl2-NaCl, and ZnCl2-LiCl systems had been reported previously. In the present work, an evaluation was made of the ternary ZnCl2-NaCl-KCl, ZnCl2-NaCl-LiCl, and ZnCl2-KCl-LiCl systems, for which no information was available in the literature. Time did not allow for a rigorous determination of liquidus temperatures. Therefore, a simple visual procedure was devised. Dried salts were quickly weighed and mixed. One-hundred-gram charges were melted in 100-ml Pyrex glass beakers. A beam of light was directed through the fused-salt mixture as it was stirred slowly and cooled. The temperature at which the first crystals were detected then was recorded. Liquidus temperature versus electrolyte composition was plotted on rectangular coordinates for each isopleth investigated to obtain liquidus profiles; these were, in turn, transposed to triangular coordinates to obtain diagrams of liquidus temperature surface.
The accuracy of this procedure, shown in table 2, was checked by investigating the ZnCl2-KCl, ZnCl2-NaCl, ZnCl2-LiCl, NaCl-LiCl, KCl-LiCl, and KCl-NaCl binary systems and comparing the results with data presented by Janz, which include a compilation of the best binary liquidus temperature data available up to 1975. Averaging the discrepancies in eutectic-peritectic composition and temperature for the six systems investigated gave a composition difference of 2 mole-pct and a temperature difference of 17° C. This is in surprisingly close agreement, considering the experimental techniques employed, and was considered accurate enough for the use intended. Figures 1-3 are liquidus temperature-electrolyte composition diagrams of the ZnCl2-NaCl-KCl, ZnCl2-NaCl-LiCl, and ZnCl2-KCl-LiCl systems, respectively. The heavy lines are boundary curves between liquidus temperature surfaces. Arrows indicate the direction of decreasing temperature along the boundary curves.
The liquidus temperature is shown at all boundary curve junctions. In all three systems, the liquidus temperature generally decreases with increasing ZnCl2 concentration. The liquidus temperatures reach minima between 50 and 65-mole-pct ZnCl2 concentration, depending upon the system, then increase slightly with increasing ZnCl2 concentration.
Effect of Electrolyte Composition
Experiments to determine the effect of bath composition on current efficiency, cell voltage, and electrolyte stability were conducted in the apparatus shown in figure 4, which consisted of a 1,000-ml, tall form Pyrex glass beaker in a protective, 316 stainless steel container. In a typical test, 1,000 grams of dried salt was weighed quickly, mixed, and melted. When the temperature reached 450° C, 320 grams of Special High Grade (SHG) zinc metal was added to the molten electrolyte. After the zinc was molten, the electrode assembly was inserted into the cell. The assembly consisted of two 1½-inch-diameter coaxial graphite cylinders, Poco grade AXF-Ql, separated 1 inch by glass spacers. The cathode cylinder was 2 inches thick with the bottom immersed one-quarter inch into the molten zinc pool. Electrical contact with the cathode was established by a ¼-inch- diameter graphite rod. The tip of the rod was immersed in the molten zinc, and the body of the rod was shielded from the electrolyte by a Pyrex glass tube. Temperature was measured with a Chromel-Alumel thermocouple.
External heat was supplied by a pot furnace. A regulated, 25-amp power supply provided direct current for electrolysis. The electrolysis current was monitored with potentiometer connected to a 25-amp, 50-mv shunt. Electrolysis commenced as soon as the electrolyte constituents had melted.
It was very important to start electrolysis as soon as possible because air and moisture quickly reacted with the electrolyte when no current was being passed. The chlorine that evolved at the anode during electrolysis provided some protection against air and moisture and probably reduced the amount of sludge formed in the electrolyte by rechlorinating some of the ZnO to ZnCl2. The current was regulated at 10 amp, and the electrolyte temperature was regulated at 500° C; selection of these conditions was based on previous work. After the passage of 20 amp-hr of current, electrolysis was terminated, and the electrodes and thermocouple were removed from the electrolyte. The electrolyte was allowed to freeze in the cell; reaction with moisture was minimized by storing the cell in a drying oven at 150° C. The frozen electrolyte and metal were broken out of the beaker and separated. Any adhering electrolyte was leached from the metal, and the metal was dried and weighed. Electrolyte composition was determined by X-ray fluorescence for zinc and potassium and by atomic absorption for Zn, K, Na, and Li.
The results of experiments conducted to determine the effect of electrolyte composition on current efficiency, voltage, and electrolyte stability are summarized in figures 5-10. Those electrolyte concentrations that showed crystallization at the operating temperature are indicated by diagonal lines. Electrolyte concentrations that have a high enough vapor pressure to cause visible fuming are indicated by dots. The white area between these two extremes represents the preferred composition range for each electrolyte system. Earlier work had shown that 500° C was a near optimum temperature for electrolysis.
Figure 5 is a plot of current efficiency versus electrolyte composition for the ZnCl2-NaCl-KCl system. The current efficiency exceeds 95 pct for all electrolyte compositions that are amenable to electrolysis. As the ZnCl2 concentration is increased, the current efficiency decreases.
Figure 6 is a plot of voltage versus electrolyte composition for the ZnCl2-NaCl-KCl system. Isovoltage lines form a series of elipses, with the lowest voltages centered on the 50-mole-pct ZnCl2 isopleth. The voltage in the optimum composition region increases roughly in proportion to the KCl content.
Figure 7 is a plot of current efficiency versus electrolyte composition for the ZnCl2-NaCl-LiCl system. The current efficiency exceeds 95 pct in only the small region that approximates the electrolyte composition 2NaCl-ZnCl2, then rapidly decreases as both the ZnCl2 and LiCl concentrations are increased. Current efficiency is low and vapor pressure is high for all electrolyte compositions containing less than 5 mole-pct NaCl.
Figure 8 is a plot of voltage versus electrolyte composition for the ZnCl2-NaCl-LiCl system. The voltage is lowest at high concentrations of LiCl and low concentrations of ZnCl2, then increases nearly linearly as both the ZnCl2 and NaCl concentrations are increased.
Figure 9 is a plot of current efficiency versus electrolyte composition for the ZnCl2-KCl-LiCl system. Current efficiency exceeds 95 pct over most of the operating region and decreases rapidly with increasing ZnCl2 and LiCl concentrations in the region where fuming was observed.
Figure 10 is a plot of voltage versus electrolyte composition for the ZnCl2-KCl-LiCl system. The ZnCl2 concentration has very little effect on voltage in the optimum composition region. The voltage varies approximately linearly with the concentrations of KCI and LiCl – highest when KCI predominates and lowest when LiCl predominates.
The electrolyte composed of 38 mole-pct ZnCl2, 31 mole-pct NaCl, and 31 mole-pct KCl appears to be the best for electrowinning zinc metal in a cell from which air and moisure are not completely excluded. The cell voltage is 17 pct lower than for the 2KCl·ZnCl2 system with no detectable increase in vapor pressure or moisture pickup. The ZnCl2 concentration can be reduced by as much as 7 mole-pct with no decrease in current efficiency, no more than 0.1 volt increase in cell voltage, and no change in the physical state of the electrolyte.
The ZnCl2-NaCl-LiCl system is not suitable as an electrolyte for any cell in which moisture is not completely excluded. This system is prone to excessive fuming and moisture pickup. The utility of the ZnCl2-KCl-LiCl system is also questionable; except for high KCl concentrations, the stability for a given ZnCl2 concentration is no greater than that for the ZnCl2-NaCl-LiCl system. However, if some of the detrimental effects of electrolyte instability could be overcome, this system might be preferred. The composition region of maximum current efficiency and minimum voltage is twice as large as that for the ZnCl2-NaCl-KCl system.
Sludge Formation in Electrolytes
The effect of electrolyte composition and prolonged operation on sludge formation in the molten electrolytes was investigated in 4-liter Pyrex glass beakers, each containing the electrode assembly shown in figure 11. Each beaker was protected by a 3/16-inch-thick stainless steel container and was heated by an electrical resistance pot furnace. The molten zinc metal served as the cathode; electrical contact was provided by a 5/8-inch, Pyrex-glass- shielded, molybdenum rod. The anode was a 2-inch graphite rod. Power was provided by a 1,000-amp, 20-volt rectifier. Electrolyte temperature was regulated by a controller operating through a Pyrex glass-shielded Chromel-Alumel thermocouple. By removing metal at 1-hour intervals with a Pyrex glass dipper, the cells could be operated with an approximate electrode spacing of 1 inch
and a total metal pool depth of 1 inch. One hundred grams of ZnCl2 was added every 30 min to the electrolyte to replace that consumed.
Operating data and experimental results are presented in table 3. The experiments were run with ZnCl2-KCl, ZnCl2-NaCl-KCl, and ZnCl2-KCl-LiCl baths for periods of 44 to 120 hours, using the compositions found best in previous work. The ZnCl2-KCl and ZnCl2-NaCl-KCl systems proved to be the most satisfactory with current efficiencies over 95 pct, no fuming, only slight surface frothing, good metal coalescence, no noticeable attack on cell components, and only a minor sludge buildup. The only significant difference between the two systems was the lower cell voltage with the ZnCl2-NaCl-KCl system. The difference was very close to that which would be predicted from figure 6.
The ZnCl2-KCl-LiCl system gave very poor results even though the bath composition of 15 mole-pct ZnCl2, 50 mole-pct KCl, and 35 mole-pct LiCl was selected for bath stability. After only 2 days of continuous operation, a thick layer of ZnO sludge had built up on the surface of the metal; metal coalescence was poor, current efficiency had dropped to 93 pct, the bath foamed badly (with periods of fuming during feed additions), and the beaker containing the electrolyte was badly etched.
Continuous Operation With a 360-Amp
Internally Heated Electrolytic Cell
The amenability of the fused-salt electrolysis of ZnCl2 to scaleup was investigated in a 360-amp, internally heated cell (figs. 12-13). This was about the smallest size that could be used with internal heating. The electrolysis chamber was 12 inches long by 9 inches wide by 15 inches high and was lined with fused-alumina brick (Monofrax), cemented with acid-proof mortar (3531 Carborundum). The fused-alumina brick was insulated by an inner layer
of castable refractory (Babcock & Wilcox Kaocrete) on the sides and insulating brick on the bottom (Babcock & Wilcox K-1620) and an outer layer of insulating board (Babcock & Wilcox Kaowool). The top of the cell was insulated with foamed glass (Corning Foamglas). The insulation was encased in a 3/16-inch- thick mild steel shell, 27 inches long by 24 inches wide by 26 inches high. The anode consisted of a 3-inch-diameter, AGSR-grade graphite rod, extending to within 3 inches of the cathode surface. The anode was protected from air oxidation by a mullite sleeve. Molten zinc metal in the bottom of the cell served as the cathode, and electrical contact was maintained by a water-cooled zinc rod extending through the bottom of the cell. Ports were provided in the lid for chlorine exhaust, a thermocouple well, immersion heaters, and a siphon to control the zinc metal level.
In starting up the cell, 33.8 pounds of ZnCl2, 33.7 pounds of KCl, and 7.5 pounds of NaCl were added and melted with quartz-shielded immersion heaters. Zinc metal for the cathode was introduced after the electrolyte was molten; electrolysis was begun as soon as the zinc was molten. After electrolysis started, the immersion heaters were removed. A slight negative pressure was maintained in the cell to draw chlorine liberated at the anode through a scrubbing tower containing caustic solution. Direct current for electrolysis was furnished by a 1,000-amp, 20-volt silicon-diode rectifier. Temperature of the bath was determined with a shielded Chromel-Alumel thermocouple. Cell voltage was monitored with a voltmeter connected directly across the electrodes. Energy consumed in electrolysis was measured with an integrating ampere-hour meter. Solid ZnCl2 was added to the cell at 30-min intervals to maintain an electrolyte depth of about 10 inches.
Zinc metal was electrowon continuously for 10 days to determine what problems would develop during prolonged operation. Operating data are presented in table 4, and the purity of the electrowon zinc is presented in table 5. Two hundred and thirty-six pounds of zinc metal was produced from 500 pounds of dried ZnCl2 at a current efficiency of nearly 100 pct, a current density of 3.2 amp/in² and a mean energy requirement of 4.0 kwhr/lb of zinc. No fuming was observed except for brief periods following ZnCl2 additions. The electrolyte was agitated by the mixing action of chlorine evolved from the anode. The only serious operating difficulty was the slow formation of a ½-inch- thick layer of sludge on the cathode during the course of the experiment. This sludge layer was composed largely of ZnO and some uncoalesced zinc metal droplets. During the 10-day run, the sludge did not affect cell operation or any of the operating parameters; however, if sludge formation had been allowed to progress, it is likely that it would have resulted in a reduction in current efficiency-partly because its formation represents consumption of zinc metal by the reaction, Zn + H2O → ZnO + H2, and partly because it prevents free access of zinc ions to the cathode. Water-free cell feed and a tighter cell should reduce the problem.
The only serious wear or corrosion of cell components observed was a 1/8-inch surface erosion from the fused-alumina brick in the area in contact with the zinc metal. Zinc metal attacks most types of refractories. Later work has shown that this problem can be eliminated by the use of a silicon oxynitride lining (Sioxyn).
The electrode spacing purposely was kept large to allow sufficient space for zinc metal to accumulate without shorting the electrodes, and this contributed to the high voltage. Although averaging 10.6, the voltage increased to 11.7 immediately after siphoning, when the metal level was lowest. The electrolyte was also made rich in KCl to obtain maximum electrolyte stability; this also served to increase the voltage. These factors contributed to a high cell voltage, which in turn resulted in high energy consumption.
Metal purity appeared to stabilize at a level of 99.99 pct after 6 days of operation. However, the iron concentration stabilized at 56 ppm, which is about double the concentration specified by the ASTM for SHG zinc metal. Higher impurity levels, especially of iron, in the first 6 days of operation probably resulted from attack on cell components.
Operation of a 1,500-Amp Cell
The effects of increased electrode area and decreased electrode spacing on cell operation were investigated in a 1,500-amp cell. The general design was the same as that of the 360-amp cell; however, major revisions were made in materials of construction and electrode design (fig. 14). The electrolyte chamber was enlarged to 20-½ inches long by 10-½ inches wide by 15 inches deep and was lined with a ¾-inch veneer of Sioxyn. This was backed by a 2-½-inch thickness of acid-proof brick (Harbison-Walker Durobrick) and insulated with a 4-inch thickness of foamed glass (Pennwalt Pennguard) on the sides, a 3-inch thickness of foamed glass on top, and a 5-inch thickness of
insulating brick (Babcock & Wilcox K-1620) on the bottom. The cell was encased in a 3/16-inch-thick, mild steel shell, 36 inches long by 26 inches wide by 27 inches high.
The electrodes consisted of two horizontal AGSR-grade graphite plates separated by one-half-inch silicon oxynitride spacers. Anode dimensions were 10 inches by 16 inches by 2 inches with 3/8-inch-wide grooves in the lower surface to facilitate escape of chlorine. Five parallel grooves were cut in the long axis of the anode and slanted from a 1/8-inch depth on one end to a 1-inch depth on the other end to direct the flow of chlorine. The cathode had the same dimensions as the anode but contained no grooves. Two-inch-high legs were attached to each corner of the cathode to maintain electrical contact with the molten zinc pool and provide a greater reservoir of zinc. The electrode gap was maintained at a fixed distance by using a graphite electrode as the cathode in this case instead of the molten zinc pool. Electrical contact for the anode was a 6-inch, graphite rod threaded and sealed with keypaste into the anode plate. The graphite rod was protected from oxidation by a ceramic sleeve. Cathode electrical contact was provided by a water-cooled, graphite-encased, zinc rod extending through the cell bottom and contacting the molten zinc pool.
Direct current was supplied by a 3,000-amp, 9.0-volt rectifier. Alternating current for initial bath meltdown and standby heating was delivered by a pair of 2-inch-diameter graphite rods extending through opposite sides of the cell. The initial electrolyte charge consisted of 60 pounds of ZnCl2, 20 pounds of NaCl, and 20 pounds of KCl, representing an electrolyte composition of 41.9 mole-pct ZnCl2, 32.6 mole-pct NaCl, and 25.5 mole-pct KCl. At 500° C, the molten electrolyte had a density of 1.9 g/cm³ and filled the cell to a depth of 10 inches. The temperature was maintained at 500° C during electrolysis by the direct current alone, using a current density of 12 amp/in².
The 1,500-amp cell was operated intermittently for a period of 6 weeks at an average current efficiency of 95 pct. The use of a silicon oxynitride brick lining appeared to eliminate any attack by the bath or the metal. The energy requirement was reduced to 2.5 kwhr/lb Zn by reducing the voltage about 40 pct compared with the 360-amp cell. This was achieved by tripling the anode area, increasing the cathode area about 50 pct, reducing the electrode gap to one-half inch, and increasing the NaCl content of the electrolyte. Only a slight buildup of sludge was observed during the 6-week period of operation.
Conclusions
The electrolysis of ZnCl2, dissolved in one or more fused alkali metal chlorides, is a promising method for the production of zinc metal. Of several electrolyte systems investigated, best results were obtained with a bath composed of 38 mole-pct ZnCl2, 31 mole-pct NaCl, and 31 mole-pct KCl. This electrolyte can be operated successfully in an internally heated cell to produce zinc at current efficiencies of over 95 pct. A silicon oxynitride cell lining was found to adequately resist the corrosive action of the metal, electrolyte, and chlorine.
Fused-salt electrolysis offers potential advantages over the present aqueous electrolysis process because much higher current densities can be employed to increase the production rate and considerably less manpower is required because stripping of cathode metal is no longer necessary. However, the problem of sludge formation must be overcome before the fused-salt electrolysis of zinc can be considered practical. ZnCl2 is very hygroscopic and absorbed water is extremely difficult to remove completely. Moisture reacts with the bath constituents and molten zinc metal to produce a ZnO sludge that slowly builds up on the cathode surface. Research is presently in progress to find methods to minimize sludge formation and to remove sludge once it is formed.
As part of its goal to help maintain an adequate supply of minerals to meet national economic and strategic needs, the Bureau of Mines,U.S. Department of the Interior, is investigating a fused-salt electrolytic procedure for producing zinc metal. A previous report described preliminary, small-scale work on the fused-salt electrolysis of ZnCl2. The present report covers a more detailed investigation of the properties of ZnCl2-alkali metal chloride electrolyte systems in relation to the production of zinc metal and also discusses electrolysis in large scale, internally heated cells.
The effect of composition on bath stability, current efficiency, cell voltage, and liquidus temperature was determined for the ZnCl2-NaCl-KCl, ZnCl2-NaCl-LiCl, and ZnCl2-KCl-LiCl electrolyte systems. An electrolyte composed of 38 mole-pct ZnCl2, 31 mole-pct NaCl, and 31 mole-pct KCl gave the best overall results.
Sludge (ZnO) formation in the ZnCl2-NaCl-KCl, ZnCl2-KCl-LiCl, and ZnCl2-KCl systems was investigated during prolonged electrolysis. The ZnCl2-KCl-NaCl electrolyte showed the least sludge formation. A 1,500-amp cell was operated using the ZnCl2-NaCl-KCl electrolyte at 500° C. Zinc metal was produced at the rate of 4.0 lb/hr with a current efficiency of 95 pct.