Table of Contents
The generally recognized fact that for economic reduction of any material, it is desirable to perform such reduction in steps or stages, removing that material which is sufficiently fine as soon as it is reduced and grinding it still finer in some device more adaptable to this finer reduction. It has been found that by so doing, the efficiency of the grinding machinery is increased, since material which is already finished and not removed interferes with the reduction of the coarser particles. This general principle is applied in the laboratory for the grinding of samples, where, after the material has been ground for a short time, it is screened for the purpose of removing the finished particles and the coarser material is then returned for further reduction.
Working Theory of the Hardinge Conical Ball Mill
Another application on a larger scale is the use of crushers or rolls in series with screens or trommels between them for removing finished or semi-finished material. It was with this idea in mind and with a realization that the machinery in use did not embody this working principle, that the Conical Mill was designed.
WORKING PRINCIPLE inside the Hardinge BALL MILL
In the Hardinge Mills, due to the action of the cones, the coarse material on entering the machine gravitates to the point of largest diameter. Here it comes in contact with, and is broken by, the largest balls moving at the highest velocity and falling from the greatest height. As the particles are broken, they automatically work their way forward, being subjected to a gradually diminishing breaking and crushing effect as they decrease in size. The particles undergoing reduction reach the required degree of fineness and arrive at the discharge end of the mill at the same time. Thus it is seen that this automatic classification, both of the material being reduced and of the grinding mediums, as well as their height of fall, proportions the energy expended or exerted in crushing to the work required to be performed. In this way, we obtain an ideal step or stage reduction in a single machine, which is conducive to a maximum crushing effect for a minimum expenditure of power.
This classification of the material undergoing reduction, as well as of the grinding bodies, is illustrated in Figure 1, in which it is seen that in the largest diameter of the mill, the incoming feed is acted upon by the largest balls with the greatest superincumbent weight, the greatest height of fall, and the greatest peripheral speed. The grinding bodies and the crushing forces exerted are gradually reduced, as well as the size of the material undergoing reduction, as the discharge end is reached.
Conical Type VS Compartment Type Ball Mills
The Hardinge Conical Mill—because of its conical shape—offsets one of the serious disadvantages found in the cylindrical, compartment type mill, i. e., unproportionate speeds for the different size balls.
The Hardinge Conical Ball Mill—because of its conical shape—offsets one of the serious disadvantages found in the cylindrical, compartment type mill, i. e., unproportionate speeds for the different size balls.
In the latter type mill, the smaller balls travel at the same rate of speed as the larger balls, the height of fall in the different compartments being equal.
This is entirely unnecessary and entails an excessive use of power, for the smaller balls, grinding finer particles, do not require as great a speed as the larger balls.

In the Conical Mill, the largest balls being kept at the greatest diameter in the cone by centrifugal force, have greater height of fall and greater peripheral speed than the smaller balls which are found at the smallest diameter in the mill. Fig. 2 shows the decreasing peripheral speeds as the diameter of the cone decreases, and shows the various size balls as they are found in the mill.
It is not claimed that the Conical Mill absolutely adjusts the energy expended in crushing to the work to be performed, since in order to make it absolutely efficient, the design of the mill would have to be adjusted to the material and particular conditions attendant upon its reduction. This, of course, would be economically impracticable. However, the Hardinge Mill more nearly approximates this desired result than does any other type of crushing or grinding machine.
The Hardinge Conical Mill can be used in various combinations for the grinding of limestone and clay mixtures, coal and cement clinker. As a mill for preliminary grinding, it is equipped with balls of various sizes selected from an assortment running from 5-in. to 2-in. balls. It will grind material of 3-inch and finer sizes, and reduce this to a size suitable for feeding to the finishing mills of the same type as the preliminary mills, except that they are equipped with smaller balls.
The Metallurgical Field has demonstrated the advantages to be obtained by quickly removing the finished material from the discharge end of the mill in order to increase the output. In accomplishing this, a certain amount of oversize material must be returned to the mill. Likewise in the Cement Industry, in two-stage grinding, it is desirable to utilize a separating screen in closed circuit with the preliminary mill. In addition to increasing the output, this permits definite control of the finished product, and as the separating screen will be ahead of the second stage, or finishing mill, it allows for close regulation of the entire operation and insures a uniform product of the desired fineness.
The Hardinge Mill is adapted to the complete finishing of limestone mixtures, coal and cement clinker, in one operation. To accomplish this with a good output, it is advisable to crush the feed to 3/4″, or preferably 1/2″ in size. This will allow the use of balls ranging from about 1 1/2″ in diameter to 3/4″, and will give a large output with extremely low use of power.
In one-stage grinding, in order to achieve the best results, it is recommended that a considerable oversize be run from the mill and the product be obtained through a separating screen, or air separator. See Figures 3, 4 and 5 for several different arrangements.
Materials a Conical Ball Mill can Grind
Some of the materials being successfully ground: |
Hardinge Mills in all parts |
|
Cement | Chrome Ores | Colors |
Limestone | Manganese Ores | Brass Ashes |
Limestone Mixtures | Molybdenum Ores | Sulphur |
Coal | Phosphate Rock | Slags |
Gold Ores | Feldspar | Mattes |
Silver Ores | Talc | Lead Skimmings |
Copper Ores | Silica | Zinc Skimmings |
Lead Ores | Fuller’s Earth | Aluminum Dross |
Zinc Ores | Glass | Copper Skimmings |
Tungsten Ores | Clay | Iron Borings |
Iron Ores | Graphite | Brass Turnings |
Graphite Ores | Chemicals | Steel Turnings |
How is the Hardinge Mills General Built
Hardinge Mills are built in several standard sizes (see Figures 6 and 7). A complete stock of linings and repair parts is carried at all times so that deliveries can be promptly made. For dry grinding, the Conical Mill, 6-ft. in diameter and over, is made of a plate steel shell, with cast steel trunnions. Trunnions are machined on the inside faces of their joints together with the plates before being riveted to the cones, insuring a perfect fit and producing a cylindrical truss of great strength. All rivet holes are drilled in trunnion castings, countersunk and rivets flattened on the inside of the mill, making a smooth surface for the lining.
When completely assembled and riveted, the drum is swung in a lathe, centered, the trunnions turned and polished, and the supports for the gear machined. This method of construction and the care exercised in the plate work assure a true
alignment of trunnions and gears, as well as a machine which is perfectly balanced, with the consequent advantages of smooth, even-running and minimum power consumption. All seams and joints in the shell are thoroughly caulked and tested before shipment. Gears are ample in size and are made of steel, with cut or cast teeth, as desired.
Mills furnished for wet grinding may be supplied with cast iron trunnions, cones, gears and gear rings. The absence of heat in mills used on this class of work permits the use of less expensive material.
The feeder supplied for coarse, dry feed is of the plunger type, which is positive in action. Where the feed is 1J/2 inches or smaller, it is practical to use a screw feeder with cast steel or cast iron flights.
For wet grinding, the feeder is simple and takes no extra machinery for its operation. A patent reversible scoop feeder or a conical feeder may be used. Under certain conditions, a combination scoop and conical feeder may be used to advantage.
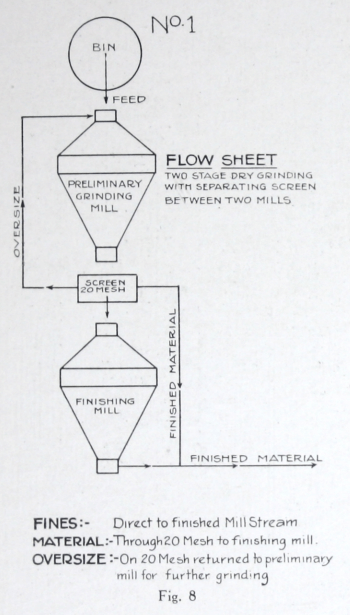
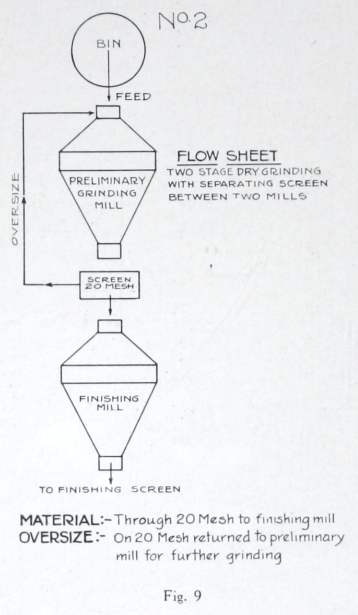
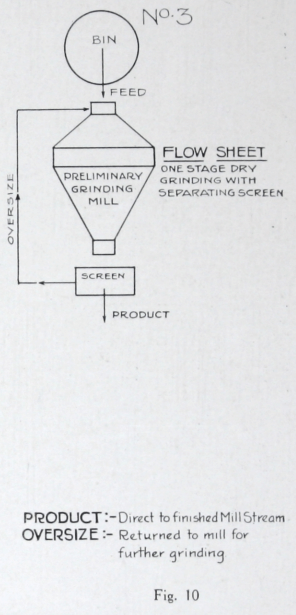
The Conical Ball Mill is lined with “Titanite” metal plates which are held in place by heavy chrome steel bars and heavy taper head bolts. The design of the bars and bolts allows for considerable wear on the bars without affecting the bolts. The construction of the lining, as indicated by the illustration, prevents the slipping of balls, thereby increasing the efficiency of the mill and reducing the wear on both lining and balls.
The charge for balls furnished with the mill varies with the size of feed and product desired. The larger sized balls are made of forged steel. For sizes of 2 in. and smaller, cast iron balls of a special mixture are recommended, as they are more uniform in size and material and less subject to fracture.
How a Conical Ball Mill Operates & what is its working principle
Hardinge Mills may be used for grinding limestone or raw material mixtures used in the manufacture of Portland Cement, cement clinker and coal, either as preliminary or finishing machines, or as units to complete the grinding in one operation. The size of the plant determines in a large measure the best way to utilize the machine. In a large plant, it is recommended that the mills be installed in two stages with a screen between the two sets of mills to insure a uniform product for the finishing mills. Used in this way, as indicated on the diagram or flow sheet, one mill or battery of mills would perform the heavy grinding, say, from feed which would pass through a 1.5″ ring, delivering the product to a separating screen. From this separating screen, the finished material would pass immediately to conveyor lines running to cement storage; the material which has passed through the 20-mesh screen, would go to one or more finishing mills for final grinding; and the oversize or rejected material would be returned to the preliminary mill for further grinding as indicated on the flow sheet. This insures the greatest possible production and the lowest cost of operation.
For grinding in one-stage operation, it is advisable to reduce the feed by rolls or crushers so that it will pass a %-in. ring. This permits the use of much smaller balls. In order to get the greatest possible production from a Conical Mill in a one-stage operation, it is recommended that a separating screen be used in closed circuit with the mill. (Air separators may be used instead of screen if desirable.) From this screen, the finished material will pass directly to the cement storage, and the oversize will be returned to the feed end of the mill for further grinding.
The results from one-stage grinding do not show quite the same efficiency as from two-stage operation, but it is often desirable, particularly in small plants, to complete the grinding in one or two mills in order to take advantage of the greater efficiency which is obtainable by the use of larger units.
The results obtained in exhaustive tests made within the past two years in grinding an unusually hard clinker, taken with the extensive experience of the Hardinge Company in the grinding of many kinds of ores and industrial material, permit a close approximation of results that may be expected in the grinding of cement clinker.
These capacities are furnished as a guide for the selection of sizes of mills that will meet the desired requirements, and are not to be considered as absolutely correct on account of the various degrees of hardness of cement clinker. It may, however, be expected that Hardinge Mills will grind approximately the amount of material indicated, and in many cases the capacities will greatly exceed these figures.
Hardinge Grinding Cement Clinker Approximate Capacity
The cost of grinding with Hardinge Mills is remarkably low. It has been found, by comparing the operation of Conical Mills with cylindrical tube mills in the grinding of ore and limestone, that with the same ball load in both types of mills, the cylindrical mill will consume about 60 per cent, more power for the same work as will the Conical Mill. Likewise, in comparison with a cylindrical tube mill, taking approximately the same power for operation, the Conical Mill will have a capacity greatly in excess of the tube mill, with a consequent lower cost of operation. It has been definitely determined that the wear on the lining plates and balls per ton of material ground, is much less in the Conical than in the cylindrical ball and tube mills.
When used in grinding clinker, it is estimated that the lining of the mills will last three or four years and the wear on the balls will not exceed one-tenth pound per barrel of clinker ground.
Hardinge Mills require a minimum amount of attention in operation and maintenance, and, due to the low consumption of power per barrel of clinker, the cost of grinding is remarkably low. Clinker ground in Hardinge Mills with a maintenance cost at present prices should not exceed one-half cent per barrel, and on a conservative estimate, the complete cost of grinding on a five-year basis, during which time the first cost of equipment may be entirely absorbed, should favor the Hardinge Mill by at least 50 per cent, over any other machine or combination of machines presently used in the cement industry.
What Information is Required to size a Ball Mill
The Engineering Staff of the Company has had extensive and varied experience in the grinding of materials used in the manufacture of Portland Cement and various other industrial products, as well as the reduction of practically all types of ore. Their knowledge of the many problems incident to this work is at the disposal of those desiring information regarding the application of the Hardinge Mills to their individual requirements.
In order that we may make an intelligent recommendation of the size and type of Conical Mill most adaptable, it is necessary that we have the following information:
- Capacity of Hardinge Mill in tons per hour.
- Character of material, with special reference to hardness and toughness. If possible, send a few ounces by mail, crushed to the size at which it will be fed into the Hardinge Mill.
- Size to be fed to the Hardinge Mill, with approximate screen analysis, if possible. We will be pleased to furnish screen test sheets on request.
- To what mesh or size is the material to be ground, with approximate screen analysis, if possible?
- Will the grinding be done wet or dry, and approximate percentage of moisture contained when fed to the Hardinge Mill?
- What grinding machines, if any, are now in use, and what results are at present being obtained with them, including screen analysis of feed and product, capacity per hour, and power required to operate?
- What effect has the material on the wearing parts of the machines now in use, especially if there is any chemical action?
- State whether power available is from a line shaft or whether alternate or direct current is used and what size motors are available, with their speeds.
- If possible, send a sketch showing the space available for the mill, indicating the space at disposal for a pulley—if the power is to be taken from a line shaft.
- We would appreciate such information as will be of assistance to us in making our recommendations.
It is very important that the information outlined be as full and explicit as possible, especially with regard to the fineness of the product desired. If, for example, 90 per cent, of the material through a certain mesh screen is satisfactory, it is advisable to state this fact, since a smaller mill would be more practical to give this discharge than to put all the material through the same screen. The reason for this is that it is much more difficult to reduce the last 8% or 10% to a certain fineness than it is to reduce the greater part of the previous reduction.
Recommendations as to the capacity of Hardinge Conical Mills are based upon results of machines already in operation under conditions similar to those specified, with due allowance for the difference in character of the material under consideration. It is the policy of this Company not to recommend the use of a Hardinge Conical Mill unless our Engineering Department is convinced of its adaptability to the requirements and that it will do the work specified to the entire satisfaction of all concerned.
Source https://archive.org/details/TheHardingeConicalMillSectionVii