Table of Contents
The Jig, placed between the ball mill and classifier, is one of the most valuable and affordable improvements in cyanidation in recent years and was developed by the metallurgical engineering and Mining Equipment Companies.
This Mineral Jig has the marked advantage of removing a large portion of the metallic values without excessive dilution, and water or solution is added to the discharge of the jig.
This jig handles the grinding mill discharge before it enters the classifier for final separation of the coarse material to be reground and the fine material for subsequent treatment by cyanidation. No elevators or pumps are needed in this jig circuit.
The hutch product secured from the Mineral Jig can be treated in a Amalgamator, or by other similar practical means.
Another important unit in these modern flowsheets is the Unit Flash Flotation Cell. This removes the cyanicides and other coarse floatable mineral and is an efficient unit in the grinding circuit due to the use of rubber wearing parts and the distinct gravity flow principle of the Unit Cell.
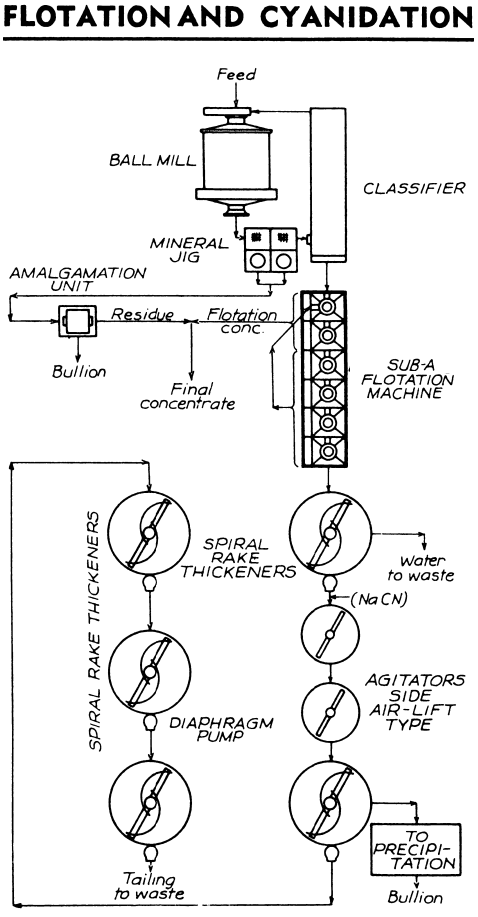
The discharge from the Unit Cell is higher than the feed inlet, thus making it possible to place the Unit Cell in the ball mill-classifier circuit without an elevator or pump.
Still another important unit in these cyanide circuits is the “Spiral Rake” Thickener with the beam type, lowhead superstructure. With this type of thickener one requires only a minimum building height because a very small distance above the beam superstructure Js necessary for its operation. This lower head room permits a more economical building and less fuel is required for heating the mill.
The “Spiral Rake,” which moves the settled material from the bottom of the thickener to the center, in one revolution, is an important improvement avoiding overload conditions and also giving greater capacity in the thickener with a clearer overflow product, due to less disturbance. The use of steel gears and ball bearings on the thickener mechanism also tends to lower the operating and maintenance expense.
Flotation and Cyanidation VS Whole Ore Cyanidation Leach
A thorough study of this subject is contained in an interesting article by J. P. Dick entitled “Mining and Metallurgy at Moneta Porcupine” in the March 1941 issue of the Canadian Mining and Metallurgical Bulletin. The following comparison is given:
Increase in cost of crushing and grinding is due to finer ball mill feed and regrinding flotation concentrate before cyaniding to 64%—10 microns.
To supplement these figures it should be considered that where metallurgically possible, lower cost per ton will be produced from a combination circuit. However this should not be accepted blindly, as the author believes that below 100 tons a day straight cyanide circuit will be cheaper to operate.
A further point to consider is that frequently the ore at the surface of a property is comparatively easy to treat, and a straight cyanide circuit is naturally installed, usually with a mineral jig in the grinding circuit to remove and recover free gold. As further development is done in depth the character of the ore frequently changes to include primary gold-bearing sulfides. Sufficient tonnage has also been blocked out to warrant mill expansion. Then the logical action is to install flotation cells to remove the sulfides, which are reground and cyanided in the original cyanide mill. Only a new grinding circuit, in addition to the flotation machine, is needed to increase the mill capacity. The ultimate increase will depend on the ratio of concentration obtainable by flotation with a flotation tailing that can be economically discarded. This ratio and consequent increase may range from 2:1 up to 35:1.
Even if the flotation tailing cannot be economically discarded, as such, these are certain additional considerations. For example: one concentrator with a very low record of cost feeds the flotation tailing to a hydroclassifier. The slime overflow is discarded. The sand fraction is given an agitation of about four hours, resulting in small agitators, and on account of the fast settling characteristics of the sand, thickeners with a capacity of about 0.3 sq. ft. per ton are successfully operated. Accordingly a very small, compact, cyanide mill was installed.
Batch Cyanidation
The batch process of cyanidation is usually applied in two different types of mills:
- Where the amount of material to be treated is quite small.
At some properties the type of material being handled is quite erratic and so to obtain the maximum extraction the batch method is used. The material is agitated, with perhaps several solution changes, until final assay of residue is satisfactory. Then the material is discharged from the tanks.
A super agitators with float decantation devices and bottom discharges are ideal for this type of work. - Where the material to be treated is quite erratic in nature.
Cyanidation—Sand Leaching
In practice, efficient classification is absolutely essential for the successful operation of a leaching plant. Even a small percentage of slimes will seriously reduce or even destroy the porosity of the sand bed. Size of particle in the feed is of little concern as long as granular.
Accordingly the discharge from the grinding circuit is classified, the overflow being either treated separately in a slime circuit or discarded, according to its value. The sand is pumped to one of a series of large diameter shallow tanks with porous false bottoms. The sand is evenly distributed in the tank by means of a mechanical distributor. Cyanide solutions may be introduced from the bottom and allowed to percolate upwards, or fed from the top and allowed to seep downwards. Usually the strongest cyanide solution, with the required dissolved lime, is added first, followed by weaker solutions and then one or more water washes. Between each percolation the sands should be allowed to drain so that air will reach the gold particles being dissolved.
After the percolation has been completed, the sand is usually discharged through doors in the bottom of the tank onto a conveyor belt that removes it to the tailing pile. Some operators prefer final washing in a series of washing classifiers after cyanidation in the tanks has been completed.
The number of percolation tanks required depends on the tonnage capacity of each tank, the daily tonnage, and the total time required for a cycle of operations. Leaching and washing may require from two to ten days depending on the ore.