In a recent reminiscence my friend Ben Stanley Revett has recorded how he bet “a bottle of bubbles” with that peripatetic philosopher Thomas F. Criley, the partner of Carrie Jane Everson in an oil process of concentration whereby the valuable sulphides were made to float above the worthless gangue in a pulp of crushed ore. Mr. Revett says that he bet his bubbles against Criley’s, but we suspect that in saying so he was interpreting the prior art in terms of latter-day metallurgy, for it is doubtful whether any of the persons concerned in that early experiment at Baker City, Oregon, had a clear understanding of the function of the bubbles in assisting the oil to give buoyancy to the sulphides. However, in staking his bubbles of carbon dioxide dissolved under pressure in the vintage of Champagne against the performance predicated by Criley. Mr. Revett must be credited with successful anticipation, for 27 years after the incident we know that the key to the flotation process is to be found not in the oil, the acid, or the apparatus, but in the bubbles.
The man who understands the physics of a soap bubble has mastered the chief mystery of flotation. The small boy, who, as pictured by Millais, watches the birth, ascent, and bursting of the iridescent sphere of his own making, is the type of our modern metallurgist who makes the multitudinous bubbles constituting a froth and then wonders to what laws of physics this filmy product owes its existence.
To put it briefly, the boy, having dissolved soap in water, holds a little of it in the bowl of his clay pipe while he blows through the stem. The soapy water forms a film that is distended by the boy’s warm breath into a lovely sphere, which is lighter than the surrounding air and therefore rises, while the sunshine undergoes refraction into the colors of the spectrum. When the boy blows through his pipe into pure water, he makes bubbles likewise, but they break instantly. It is the soap that lengthens their life. In the language of physics we say that high ‘surface tension’ causes the pure-water bubbles to burst immediately, while the addition of soap introduces a contaminant that lowers the tension so as to enable the bubbles to last longer.
The basic factor in the making of bubbles is surface tension. This is the force that causes the surface of a liquid to resist rapture. The particles at the surface have a greater coherence than the similar particles within the body of the liquid. In other words, each molecule within the interior of the liquid may be pictured as surrounded by molecules like itself in being attracted toward each other equally in all directions; while the molecules at the free surface of the liquid are attracted only by those internal to themselves, the result being to constrict the free surface to the least area. In consequence, the surface acts as if it were elastic. Hence the attachment of water to the sides of a tube and the drawing of that water upward—which is called ‘capillarity’ because it is most marked in a tube as small as capillus, a hair.
Numerous manifestations of surface tension on water could be cited. Fill a tumbler a little more than full and the water will have a convex surface, indicating that there is some force at work to prevent the water from spilling. Note the cohesion between two plates that have been wetted. Dip a camel’s-hair brush into water and the hairs cling together; immerse the wet brush in the water and the hairs separate. Watch the formation of a drop of water and note that it behaves as if enveloped by a stretched membrane. Water-spiders can be seen running over the surface of a pond in summer, as small boys run over a pond covered with ice in winter. The ice bends under their weight without breaking; so also the spider makes a visible dimple without wetting his feet. The surface is not ruptured.
The force of surface tension has been measured by ascertaining the weight that can be suspended from a film of water in air. It has been stated as 3¼ grains per inch or 81 dynes per centimetre. The most recent determination is that of Theodore W. Richards and Leslie B. Coombs, who found it to be 72.62 dynes per centimetre at 20°C. Many disturbing factors enter into the measurement of this force, so that divers figures, ranging from 70.6 to 81, have been announced at different times.
Surface tension differs as between various liquids and fluids in contact; for example, the tension separating mercury from water amounts to 418 dynes per centimetre, while that separating olive oil from air is only 36.9 dynes. A drop of pure water will spread over the surface of pure mercury as oil will spread over water. The surface tension of an oil-water surface is only 14, as compared with the 73 of an air-water surface at a temperature of 18°C. “While the film of oil on water may be only one molecule thick, or one twenty- five millionth of an inch, it will suffice to reduce the effective pull of the water surface from 73 to 43. This latter figure represents the effective surface tension of water modified by oil as used in flotation. It is the main factor in the formation and persistence of a bubble. Heat lowers the surface tension of water. Place powdered sulphur on the surface of the water on a horizontal plate of clean metal; apply heat locally; the sulphur is pulled away by the cold liquid as against the feebler tension of the warmer liquid.
This elastic force at the surface of a liquid tends to draw it into the most compact form. That is why a drop assumes the form of a sphere, in which shape it presents the smallest surface in relation to its volume. Surface tension is a contractile force. This is shown in a simple way by blowing a soap bubble on the large end of a pipe and then holding the other end of the pipe to a candle, when the air escaping from the shrinking bag of the bubble extinguishes the flame, as in Fig. 1. When water is spilled on a stove, it assumes a globular form and dances on the hot iron until it flashes into steam. When water is sprinkled on a dusty floor, the dust forms a layer upon the drop of water, which draws itself together into rolling spherules.
The smallest drops are the most nearly round; in the larger ones the weight causes a flattening, because gravity overcomes the elasticity of the surface film. That is shown even more clearly in the case of drops of mercury, and by the beads of gold on an assayer’s cupel.
This contractile force at the surface, whereby a portion of liquid gathers itself together into spherical form, explains why the pure- water bubble bursts so readily. The high tension shatters it. It does not burst explosively, by expansion of the gas within the envelope, but by lateral displacement of the substance of the elastic film. It collapses because the surface tension draws it together. To prevent such immediate collapse it is necessary to lessen the tension, that is, diminish the contractile force in the elastic membrane constituting the film of the bubble. This can be done by introducing an impurity or contaminant, which lowers the surface tension, that is, diminishes the contractibility of the bubble-film. Water has the highest surface tension of any common liquid except mercury, so that the addition of another liquid usually lowers its surface tension.
Oil in emulsion and organic substances in solution can be used for this purpose. Soap will have the same effect, and that is why a soap bubble lasts longer than a pure-water bubble, the film of the former consisting of water having some soap in solution. When water has been modified by such a contaminant, the components of the film can so dispose themselves that the superficial forces will be the same everywhere, that is, tend to remain in equilibrium, including the force of gravity, which otherwise would pull the film apart.
When two bubbles come in contact they tend to coalesce because the two of them have an aggregate area greater than that required to include the same amount of air within a single bubble. In pure water the bubbles coalesce with a violence that is mutually destructive. Even when a survivor is left, the violence of coalescence of such bubbles in a pulp unhorses any mineral particles that may be riding the bubbles. When, however, the water is modified by oil, the contractile force of surface tension is diminished, the bubbles are less fragile, and they survive long enough to perform their metallurgical duty of buoying the metallic particles to the surface of the liquid pulp. In practice the ‘modification’ of the water is effected by emulsification or minute subdivision (as in a mayonnaise) of an insoluble oil, such as cotton-seed and oleic; or it may be done by means of a soluble oil or derivative, such as cresol and amyl acetate.
The presence of a contaminant in water may also affect its viscosity or internal friction, whereby it offers resistance to a change of shape. This strengthens the film of a bubble generated in such water. Moreover, it has been asserted that a concentration of the contaminant occurs in the surface of a liquid, causing the viscosity to be highly magnified as compared with the body of the liquid. It is also known that the films made of any definite liquid are of the same strength, irrespective of their thinness; so that the attenuation of the skin of a bubble does not decrease its strength. This again follows from one of the most remarkable properties of a bubble: the ability, within small limits, of adjusting its tension to the load. Briefly, the tension at the surface of a contaminated liquid is able to adjust itself within fairly wide limits. Thus a film of such a liquid can remain in equilibrium when a film of pure liquid would have to break.
In his book T. J. Hoover states how the presence of a mere trace of saponine will kill the froth in the flotation cell. He does not explain why. It happens that saponine, which can be dissolved out of horse- chestnuts, is an aid to the blowing of big bubbles. But they are weak and tender. Why? Because saponine increases the tension. When a saponine bubble is brought into contact with a soap bubble, the former contracts and blows air into the soap bubble. Rayleigh proved that the tension of the soap-film is only two-thirds of that blown from a saponine solution of equal strength. One part of saponine in 100,000 parts of water will suffice to make a liberal froth. But the bubbles are flimsy. They are so fragile as to render them of no use as carriers of mineral. Hence they spoil the normal working of a flotation-cell, in which it is necessary to employ a contaminant that lowers the surface tension so as to yield bubbles that are both persistent and sufficiently robust to buoy mineral particles.
In approaching the rationale of the process under discussion it may now be assumed that we are dealing with a pulp consisting of ore and water, modified by oil, the ore having been crushed sufficiently to separate the metallic sulphides from the associated gangue in a pulp consisting of minute particles of each. In ordinal water-concentration the lower specific gravity of the gangue permits the mill-man to wash it away from the heavier metallic sulphides, but in the flotation process this action is reversed, the metallic particles being lifted above, and away from, the gangue particles. Apparently, it is a metallurgic anomaly.
To this crushed ore we have added oil. The oil serves as a contaminant that lowers the surface tension; also it augments the viscosity of the liquid. These two effects unite in facilitating the formation of strong and persistent bubbles. The necessary air is introduced by agitation or by direct injection. Sea-weed contaminates sea-water and makes foam in the breakers, as oil makes froth in fresh water that is agitated.
Air has a marked adhesiveness for metallic surfaces: this attachment is supposed to be enhanced by the presence of oil or grease on the metallic surface. In other words, the metallic surface, such as that of a sulphide mineral, when in the presence of both oil and water, will exhibit a preference for the oil. Hence the sulphide is not wetted.
This characteristic is less marked on the part of the heavy silicates, such as rhodonite or garnet, and still less evident in the case of the lighter silicious minerals, such as quartz and orthoclase. The addition of acid lessens the oil attachment to the gangne particles without decreasing the selectiveness of the oil and the air for the sulphide particles. Thus we can understand why the bubbles attach themselves to the metallic particles and buoy them to the top, while ignoring the gangue particles, which sink to the bottom of the vessel in which the pulp is undergoing stirring or agitation. This preference of air for metals and metallic surfaces must be emphasized. It is the decisive factor in the process of flotation. Most minerals when pulverized, and then sprinkled on water, will float, particularly if they are in flakes or plates, as gold often is and as minerals with a highly developed cleavage usually are. Such flotation is due to air, which forms a discontinuous film under the mineral particles. Mickle proved this by taking a magnetic mineral, like pyrrhotite, and pulling it out of the water by a magnet, when it could be seen that the water was dragged up with the mineral. These minerals float for the same reason as an ungreased needle will float, namely, the resistance to rupture of the surface of the water and the aid of the air attached. It used to be supposed that the needle must be greased in order that it may float. That idea, like the general exaggeration of oil as a factor in flotation, has been disproved by experiment.
If, to water in which mineral dust is floating, an addition of alcohol or caustic soda be made, or even the vapor of alcohol be allowed to play on the surface of the water, the mineral particles will sink. The contamination of the water has decreased its surface tension.
The bubbles collect the metallic particles, that is agreed; but whether the selection is dependent upon the previous oiling is a disputed point. Apparently the adhesiveness of air for metallic surfaces is greater than that of oil, and it would appear probable that in the flotation process the first phenomenon suffices without the aid of the second. It used to be an accepted canon of flotation that the oil coated the metallic particles, which therefore were not ‘wetted’ and did not sink, while the gangue particles were not oiled and therefore were wetted, especially in acidulated water, so that they sank. Testimony has been given by a keen observer that “the distribution of the oil in the concentrate and the gangue is entirely fortuitous.” It is even asserted now that instead of the oil residing with the metallic particles exclusively, and leaving the gangue untouched, it is distributed throughout the mixture. When the larger proportions of oil were employed, it is likely that such promiscuous oiling of all the particles of the pulp did take place, but now that the quantity has been reduced to a proportion so small that the presence of oil on the concentrate is not discernible by the senses, we may assume a preference for the metallic particles in accordance with laboratory observation. This appears to be confirmed by experiments showing that in the case of specific minerals, such as chalcocite, it is necessary to oil the mineral in order to lift it by an air bubble.
When using the, at present, minimum quantity of oil—say, one- third of a pound per ton of ore—it would appear that the oil forms a coating of microscopic thinness upon the metallic particles. The minimum thickness is the thickness of a molecule.
Metallic surfaces have a selective adhesion for air and for oil, as we have seen. Therefore the molecular forces of the oil and of the metallic surface may be supposed to unite in attracting the bubbles. What the nature of those forces may be is yet a matter of conjecture, although the idea that they are electro-static is suggested by the fact, among others, that the metallic sulphides most amenable to flotation are good conductors of electricity.
The foregoing statement of physical principles applies more particularly to the frothing method. The history of the ‘prior art,’ as it is called in patent litigation, shows that the first stage of the flotation process as now in vogue was performed by the use of a large proportion of thick oil. This is typified by the bulk-oil method of the Elmore brothers. It depends upon the lower specific gravity of oil as compared with water, so that when mixed in a pulp of crushed ore the oil rises to the top, dragging the metallic sulphides with it. This also was explained formerly as due mainly to the selective adhesiveness of oil for metallic surfaces, which prevents them from being wetted, while the lack of a similar affinity on the part of the gangue particles enables them to be so wetted as to cause them to sink to the bottom. All of this is measurably true, but the underlying fact seems to be that an excess of viscous oil causes the oiled particles to adhere or stick together so that they are rafted to the top. It is probable that when thus collected in groups they are more readily floated on account of their ability to hold more oil, as compared with individual particles, because the oil fills the spaces between the members of a group.
The lighter oils have a specific gravity ranging from 0.8 to 0.95, as compared with the 1.0 of water, so that the margin for flotation is small. For instance, in the case of a mixture of an oil having a specific gravity of 0.9 and of zine-blende, having a specific gravity of 4, it is necessary to use 6.7 parts by weight of oil to one part by weight of blende in order that the mixture may have a specific gravity equal to that of water. Thus an ore containing 20% blende, or 400 lb. per ton, would require the use of over 2680 lb. of oil in order to float all the blende in the ore.
In true bulk-oil flotation, which, as a matter of fact, was rarely performed, the phenomenon of surface tension does not play a prominent part. It is mainly a question of raising a mineral heavier than water by aid of a liquid lighter than, and not soluble in, water. The emulsification of the oil was carefully avoided by Elmore. In the later phases of flotation, in which the proportion of oil becomes steadily less, it is aimed to emulsify the oil and air. The oil produces a ‘micro-emulsion of air,’ as Leverrier expressed it. Thus the air is thoroughly distributed in the pulp and the oil is brought into intimate mixture with the water, which is thereby modified and prepared for the making of persistent bubbles.
The Processes
The application of the various physical principles outlined in the foregoing paragraphs has taken diverse forms, as expressed in scores of inventions, only a few of which have been developed into workable processes. The phenomenon of surface tension is used directly in the so-called skin-flotation methods of Hezekiah Bradford, Arthur P. S. Macquisten, and Henry E. ‘Wood. In the first of these, invented in 1886, the pulp flows down an inclined plane onto the quiet surface of water in a vessel, so that the sulphide particles float forward under the impetus of their descent while the gangue particles sink. See Fig. 2. The explanation is that sulphides, by exposure to the atmosphere, attach films of air to themselves, so that they are not wetted and move over the so-called water-skin, while the gangue, which has remained wet throughout the operation, sinks through the surface to the bottom of the vessel.
Macquisten applied the same idea in a tube cast with a helical groove and revolved at a moderate speed. In 1906 this method was adopted in the Adelaide mill, at Golconda, Nevada. The ore contained 2.2% copper as chalcopyrite, with pyrrhotite and pyrite, as well as some blende and galena. The gangne was quartzose, containing spinel and garnet. The tubes were of cast-iron, 6 ft. long, 1 ft. inside diameter, and each weighed 450 lb. See Fig. 3.
Externally these tubes were cast with two tires, which rested upon supporting rollers. The discharge-end was entirely open. The feed-end was closed except for a hole in the centre large enough to admit the pipe through which the pulp entered. Internally the tube was cast with a helical groove of ¾-inch pitch, which was changed subsequently to 1½-inch pitch. The discharge-end was connected with a separating- box, the joint between this and the tube being water-tight, while the tube was free to revolve. At the side of the separating-box, directly opposite the discharge from the tube, an opening or lip was cut for the overflow of the surface layer of water, carrying the floating mineral. This opening regulated the depth of water in the tube. The bottom of the opening was three inches above the inside bottom of the tube, so that there was three inches of water in the tube; the feed and the discharge were so regulated that the water passing over the lip was about 1/32 inch deep. The tube was rotated at 30 r.p.m. in a direction corresponding with the helix of the interior. As Mr. Ingalls said: “The pulp is thus screwed through the tube and in its advance is repeatedly given an opportunity to slide upon the surface of the water, where it may be retained by surface tension.” The ore was crushed to pass 30 mesh. The capacity of each tube was 5 tons per 24 hours, and 25 tubes were in use. A concentration of 11:1 was effected on a 2.2% copper ore, the tailing assaying 0.2%; but this refers only to the deslimed ore, that is 70% of the supply, so that the actual extraction was only 63%. The inability to treat slime is a notable defect of this ingenious method of flotation.
Wood’s method is equally interesting. The ore is crushed dry to 30 or 40 mesh and is then fed in a thin stream from a vibrating plate onto the surface of water in a tank to the surface of which a forward movement is given by small jets, also of water. By a combination of the capillary attraction and the pressure of a constant feed, the sulphides are caused to move forward as a definite elastic film on top of the water. This film of mineral passes over an endless canvas belt, which emerges from the tank at a particular angle, varied according to the kind of mineral to be saved. The belt with its film of sulphides passes over three rollers so that its motion is reversed when it strikes the water-level of a second tank, where it releases its valuable burden. Very little gangue in suspension comes over, as the water drains back into the main tank. Any submerged particles that have been accidentally wetted or are so heavy that they have penetrated the surface-film, pass to standard concentration-tables, on which they are separated by gravity in the ordinary way. In the ease of molybdenite and graphite, the film concentrate is still further cleaned by being passed over a nearly vertical screen. Gangue in suspension passes through, while the flat crystals of the valuable minerals slide over the screen, which largely dewaters them. The flotation concentrate is collected and dried as usual. See Fig. 4.
Mr. “Wood is using his own process to commercial advantage in the treatment of molybdenite ore, at Denver. The Macquisten tube is still in use at Mullan, Idaho; but the Bradford patent is only of academic interest. These methods have been confused with the more recent flotation processes: they ought to be differentiated. I suggest therefore that they be classed under ‘film-suspension,’ for it may be taken that in every case the sulphides are carried with air over the tensional film on the surface of the water.
Incidentally, it may be well to point out that although it is convenient to speak of the ‘water-skin’ and of ‘skin-flotation, ’ the use of either ‘skin’ or ‘film’ is inaccurate. A skin is a thing of definite thickness, which therefore can be ‘peeled’ off, like the epidermis, for example. The phenomenon of surface tension involves nothing of the kind. It refers to a condition of molecular forces at the surface of a liquid, the effect of which can be only one molecule thick. Thus, ‘water-skin’ and ‘skin-flotation’ stand for water-surface and surface- suspension.
Neither Bradford nor Wood uses oil or acid, but in the later applications of the Macquisten tube both have been introduced. As the ore contains carbonates that would react with the sulphuric acid so as to liberate carbon-dioxide gas, it is obvious that another factor is introduced, namely, the bubble idea, which has proved so potent in the more recent phase of flotation. The further addition of oil marks a distinct departure from the first idea of the inventor, causing the process to resemble those of Potter, Delprat, and De Bavay.
The methods of these three Australians were alike designed to treat Broken Hill tailings, containing zinc-lead sulphides in a gangue composed partly of carbonates, notably calcite, siderite, and rhodochrosite. Charles V. Potter used water containing from 1 to 10% sulphuric acid, which was added to crushed ore placed in a vessel (see Fig. 5) provided with stirrers (B’ the shaft and B the arms.) Heat was then applied by gas (3) ; whereupon the metallic particles rose to the surface of the liquid. It has been said that “it is clear that he (Potter) had in view a surface tension process.” if this is meant as a reference to the surface-suspension method, say, of Bradford, it is incorrect. Surely Potter used bubble-levitation as his principal effect. The gas generated by the action of the acidulated water on the carbonates joined with the air entrained by the ore is furnishing gas for making bubbles, this result being assisted further by the stirring of the pulp and the heating of it. See also Fig. 10.
G. D. Delprat had an apparatus suggesting the employment of surface suspension, but he also used chemicals to induce flotation. See Fig. 6. By the addition (through the pipe 5) of a hot solution of acid salt-cake to the crushed ore as it was fed (from the chute 1) upon a pan having a sloping bottom (4) heated by a Bunsen burner (14), the sulphides were made to rise to the surface of the vessel (at 3, passing forward along 13), while the gangue collected in a sump (10). In this case also the flotation was the result of forming bubbles of carbon-dioxide gas and of air by chemical action and heat.
Auguste J. F. de Bavay described a process in which a thin stream of freely flowing pulp was delivered upon the surface of a vessel of water, after the style of Bradford. The description of the method as used subsequently on the North Broken Hill mine does not correspond with this, for in that plant the mill-tailing, relieved of slime, is said to have been fed into a vessel provided with a mixing device, run at a high speed, so as to agitate the acidulated pulp. The sulphides rose to the surface, much in the same way as in the preceding methods of Potter and Delprat. That of Potter was used, in a modified form, at the Block 14 mine at Broken Hill in 1905 and 1906, while the Delprat process has been in use for several years successfully at the Broken Hill Proprietary mine. It is proper to add, however, that all of these acid-flotation methods are now only of academic interest. In the chief application of these processes it has not been customary to use oil, but as the material treated came from old dumps of tailing it may be assumed that there was some substance present capable of modifying the water sufficiently.
The first application of any of the oil-flotation processes on a working scale in a mill was that made at the Glasdir mine, near Dolgelly, in Wales, by Francis E. Elmore in 1899. The mixture of crushed ore and water was fed at the upper end of a slowly revolving drum, provided with annular helical ribs and transverse blades, so as to effect the mixing of the pulp and the oil without producing emulsification. See Fig. 7. The oil was introduced through a separate pipe. The mixture was discharged into a V-shaped vessel, where the water and sand subsided while the oil buoyed the sulphides to the top. An oil-residuum having a specific gravity of 0.89 was used in equal parts by weight with the ore, ton for ton. The oil was so viscous as to require the aid of small rotary pumps to propel it forward. The temperature of the oil and water was kept between 54° and 57°F. The loss of oil was 2 gallons per ton of ore. A concentration of 14:1 was achieved with a recovery (in the concentrate) of 69% of the gold, 65% of the silver, and 70% of the copper from a pyritic and chalcopyritic ore assaying 1.12% copper, 0.049 oz. gold, and 0.8 oz. silver per long ton. The process was described as “a somewhat dirty and nasty process.” It did not work on oxidized or earthy ores, nor upon tarnished sulphides.
In the course of the discussion following the reading of the paper by Mr. Rolker from which these facts are gleaned, it was acknowledged that the process developed by Mr. Elmore was based on previous experimental work done, at the same mine, by George Robson, who used petroleum in even larger proportion, as much—I have been informed—as three tons of oil to one of ore. But the most interesting fact elicited by the discussion was the statement made by Mr. Elmore, and confirmed by the superintendent of the mill, John Bevan, that the actual load of mineral carried by the oil was 25%, as against the theoretical load of 10% inferred by Mr. Rolker. In short, the oil did 150% more than anybody could explain. The ‘prior art’ was in the dark, but the posthumous art of today can make a confident guess.
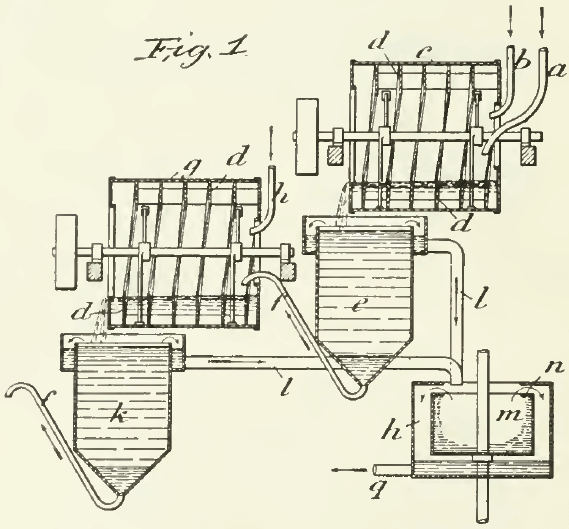
Of course, the larger part of the levitation was done by air, entangled previously in the ore particles and entrained subsequently during the mixing of the pulp with the oil in the drum. Later investigators can testify how difficult it is to prevent the indrawing of air under such circumstances. Therefore even in this beginning of flotation as a practical process the agency of air was utilized, although unwittingly. Four years later “Walter McDermott, who has been a consistent supporter of the Elmore brothers in their flotation business, acknowledged that “the agitation with the pulp results in the oil taking up a very appreciable quantity of air.”
This fact was not recognized at first, but in 1904, six years after the first bulk-oil patent of 1898, Francis E. Elmore took out his patent for vacuum-oil flotation. See Fig. 8. In this he subjected the oiled and acidulated pulp to a vacuum, thereby releasing the air dissolved in the water. The air thus held in solution amounts to 2.2% by volume, at sea-level and 60°F. By lowering the pressure and raising the temperature this air is released, thereupon attaching itself, in the form of bubbles, to the oiled sulphide particles, which rise to the surface. For example, the air in a pulp of 1 ton of ore to 6 of water suffices to lift 360 lb. of zinc-lead sulphides in a Broken Hill ore. In actual practice, however, the weight of sulphides floated is considerably greater than the theoretical capacity, as based on the efficacy of the air released from solution in the water. Part of the work is done by the gaseous carbon dioxide liberated by the reaction between the acid and the carbonates, such as calcite, either in the gangue or added in the form of limestone. Part of it is entangled in the ore particles and part of it is entrained into the pulp during mixing. In this process the quantity of oil added to the pulp was reduced to 10 lb. per ton and finally, in some cases, to as little as 3 lb. per ton of ore. The machine devised by Elmore was remarkably ingenious and to it the success of the process was largely due. It was applied at many mines, notably the Sulitelma copper mine, in Norway.
The Potter-Delprat and the Elmore vacuum processes are clearly based on the activity of bubbles of carbon dioxide or air, or both. Next, mention must be made of Alcide Froment, who, although he was not the inventor of a working process, introduced the idea of violent agitation for the purpose of producing bubbles of gas rapidly from a pulp containing both calcite and acid. While he looked to carbon dioxide as the gas from which to make his bubbles, he did undoubtedly entrain lots of air and obtained the use of it in generating the bubbles that attached themselves to the oiled particles. He did not recommend much oil: only “a thin layer.” In his later instructions to the Minerals Separation company, which bought his British patent in 1903, he specified that the oil was to be from 1 to 3½% on the ore.
The next method was that invented by Arthur E. Cattermole, also in 1902. It was to buy his patents that the Minerals Separation company was organized in 1903 by John Ballot, J. H. Curle, W. W. Webster, S. Gregory, H. L. Sulman, and H. F. K. Picard. Cattermole departed from the prior art. Instead of floating the sulphides, he sank them, while the gangue was assisted to rise in an upward current of water. He added oil in the proportion of 4 to 6% “of the weight of metalliferous mineral present in the ore,” together with 2% of soap, so as to obtain an agglomeration of flocculent sulphide particles, which, being heavily oiled, stuck to each other, in groups or granules that sank to the bottom. He used a Gabbett, or cone-mixer, to obtain a violent agitation of the pulp, and followed it by a gentler stirring during which the separation into “shotty granules” was effected in the presence of as little air as possible.
This process was only put to work in one mill, on the Central mine at Broken Hill, where it must have seemed a metallurgical abortion during the very short time it was in use. The oil was emulsified with soft soap and then fed into the mixers, where the crushed ore underwent agitation with acidulated water. From the very start a considerable proportion of mineral was floated on the froth incidental to violent mixing in the presence of air. Apparently only a part of the sulphides was ‘granulated,’ so as to sink according to program. The remainder was floated unintentionally. The description given by the manager, James Hebbard, indicates that he and his staff stumbled upon the so-called agitation-froth process almost immediately. He records how he discovered that more froth was made by using less oil, and that the frothing and floating proved a better method than the granulating and sinking of the sulphide particles. He also states that the discovery was made concurrently by the metallurgist of the Minerals Separation company in the London laboratory. They hit upon the same idea by varying the quantity of oil, in March 1905, so we are told. Yet the plant at the Central mine was allowed to start on the Cattermole process in July. Successful tests with the frothing process were not made until September, the proportion of oil being reduced from 3% when granulating to between 0.15 and 0.2% when frothing. The plant was gradually changed until granulation was completely ousted, by decreasing the quantity of oil and increasing the violence of agitation. The ore from the mixers was passed with “a good splash” into spitzkasten, thereby accentuating the need for aeration.
So the failure of the Cattermole method is stated to have led to the Minerals Separation process of today, the proprietary rights to which are based primarily on U. S. patent No. 835,120, dated May 29, 1905. This is a process “wherein, by the use of a frothing agent, and in the presence of such agitation as will maintain or produce distribution of the ore particles through the pulp, and dissemination of bubbles of air through the pulp and into contact with the metallic particles through the pulp, the air bubbles will seize the metallic particles and will carry them to and through the surface of the pulp, so as to permit of their delivery at or above the surface of the pulp separate from the gangue particles.” This description is taken from the complainant’s brief in the suit of Minerals Separation, Limited, v. Miami Copper Company, 1915. It is further explained that in this process “the frothing agent is an oil or immiscible liquid, and the discovery was that this mode of operation in the concentration of ores was attainable with small quantities of oil, quantities so small that although the oil coated the metallic particles in the exercise of the well known preferential affinity of oils for metallic substances, the coating was so minute, so nearly infinitesimal, that the oil disappeared from sight and sense. In this process the oil coats the metallic particles, modifies the water so as to produce minute and persistent air-bubbles, and increases the attraction of the metallic particles for the air- bubbles; and the persistence of the air-bubbles is such that the air- bubbles cling to the metallic particles and carry them to and through the surface of the pulp, and when the air-bubbles escape from their water environment in the body of the pulp and are exposed at or above the surface of the pulp, their water-films carrying a mineral load are maintained intact until at least their separation from the body of the pulp has been effected, by overflowing or otherwise. The air-bubbles with their mineral load form a froth floating upon the surface of the pulp, which, if allowed to remain there in a quiescent condition will float for days and weeks. This froth has therefore been properly called a persistent or permanent froth. It will always form a coherent mass of bubbles pressed against each other and frequently several inches in thickness.”
This description, lacking adequate punctuation, as is usual in legal statements, may be accepted as official, being the product of a joint effort on the part of counsel and experts representing Minerals Separation in the lawsuit at “Wilmington. In the basic patent, No. 835,120. the proportion of oil is given as “a fraction of 1% on the ore.” W. H. Ballantyne, patent lawyer for Minerals Separation, testified, in the Hyde suit, that “an ideal standard for the agitation-froth process is 1½ to 2 lb. oil per ton of ore.” Much less is used now in the big mills of the copper mining companies.
The process was first introduced on a working scale in the Central mill of the Sulphide Corporation, at Broken Hill, as already mentioned. Two years later, in 1907, it was adopted by the Zinc Corporation, to be discarded during 1909 in favor of the Elmore vacuum process, and to be restored again to favor in 1911. See Fig. 9.
The next important application was made in 1912 at the Braden Copper mine, in Chile, where a 200-ton plant was erected. The extraction of copper (as concentrate) was 80 to 85%. But when a larger mill of two 600-ton units was built the recovery became poor, being no better than it had been in the old water-concentration mill, namely, about 65%. Whereupon the oil was added to the ore in the tube-mill and the extraction improved at once. The mill has now been enlarged to seven 600-ton units, treating 3500 tons per day. The extraction last year was 77 per cent.
In February 1915 the Anaconda Copper Mining Company took a license from Minerals Separation, and at that time also the Inspiration Consolidated Copper Company made an agreement for the same purpose. Both companies built large mills for the operation of the process during last year. The Anaconda now treats 12,000 tons and the Inspiration 8000 tons of ore daily by flotation.
The first mining company in America to ignore the Minerals Separation patents was the Butte & Superior, in Montana. Under the technical guidance of James M. Hyde, this company built a 150-ton unit in their mill during 1912. This provoked the first test case, which is now before the Supreme Court of the United States.
Other companies charged with infringement are the Utah Copper, Nevada Consolidated, Magma Copper, and the Miami. The first three use the Janney machine and the last one the Callow pneumatic launder. In each case it is stated that the Minerals Separation machine—in which violent agitation is effected by blade-impellers—was tried first and then discarded as ineffective. The pneumatic flotation plant at Miami was commenced in August 1914 and remodeled in the early part of 1915. Suit for infringement was brought at once by Minerals Separation, the trial commencing on March 29 and ending on May 27, 1915. The decision of the Court is not yet known.
As applied at Miami the flotation process is simplified by the use of a launder having a canvas bottom through which air is forced under pressure. This gives the gas required for the generation of bubbles in a pulp previously modified by the addition of oil, which is mixed with the ore while being pumped into a Pachuca tank, or Brown agitator, where it undergoes further emulsification before entering the Callow launder constituting the flotation-cell. It is claimed that the froth produced in this way is different from that made in the mechanical mixer of the Minerals Separation machine. In the one case, according to R. C. Canby, the froth consists of a mass of delicate, fragile, and evanescent bubbles, which rise to the surface in rapid succession and maintain a froth only because they are being generated slightly faster than they break, so that the uppermost layer overflows, with its burden of mineral, over the lip of the vessel. In the other case the froth is said to be “thick, coherent, and persistent,” as Mr. Picard phrased it. “It appears as if the minerals were protecting the tender air-bubble like an armor, and instead of destroying it, were actually guarding it. The froth has a long life. I have myself seen a froth standing for 24 hours without the least change having taken place.” So testified Dr. Adolf Liebmann. Mr. Ballantyne stated that this agitation-froth of the Minerals Separation machine was so dense that it would support a spade. Mr. Canby showed that the air- froth of the Callow machine would not support a match-stem.
From the foregoing summary it is clear that three processes are covered by the general term ‘flotation,’ and that to clarify the discussion of the subject it will be well to distinguish between
- Film-suspension, as in the Wood and Macquisten methods.
- Oil-flotation, as in the Robson and Elmore bulk-oil methods.
- Bubble-levitation, as in the Elmore vacuum, Delprat, Froment, and Sulman-Picard methods.
The third class can be further sub-divided according as carbon dioxide or air is the principal gas utilized for making bubbles.
Finally, the air-bubble methods can be classified according to the way in which the air is introduced:
- From the bottom of the vessel, as in the Callow and Owen cells.
- By being entrained or dragged into the pulp by the beating of paddles or some other form of impeller, as in the Gabbett and Hoover mixers.
- By escape from solution in water, as in the Elmore vacuum machine and the Norris apparatus.
It remains to emphasize the fact that from the high ratio of 3 tons of oil per ton of ore, the proportion of oil used in flotation has decreased, by reason of the recognition of the part played by air, to one-third of a pound per ton of ore; that is, one eighteen-thousandths of the quantity used by Robson. Concurrently the acid used has decreased to a minus quantity, namely, alkalinity.
https://archive.org/stream/flotationproces00unkngoog#page/n48/mode/2up