Table of Contents
The problem a Small Gold Processing Plant can solve is for the need to to provide a small, relatively simple and inexpensive gold mill that will operate at a reasonable profit with a minimum of supervision. The limited availability of skilled operating personnel, availability of water and local power, high cost of transporting ore and expense of building, operating and maintaining such a mill have been taken into consideration in developing the flowsheet. A primary objective is to provide a mill having sufficiently low power and water requirements as to be supplied locally.
The flowsheet was developed for a siliceous ore with a high percentage of the gold present in a “free milling” state. In addition some gold bearing sulphides are present which require the inclusion of flotation in order to obtain maximum recovery. Most of the gold is, however, recoverable in bullion form for shipment to the mint. The gold tied up in the flotation concentrate is shipped to a smelter, although in remote areas a small batch cyanide plant may be used to extract the values and thereby eliminate the shipping and smelter charges.
Crushing and Grinding
Single stage crushing for the average small mill (100 tons or less) is adequate. The crushed ore at approximately minus 1 inch is wet ground in a Ball Mill to free the gold and sulfide values. Grinding is in closed circuit with a classifier and in this case a 48 mesh grind was necessary.
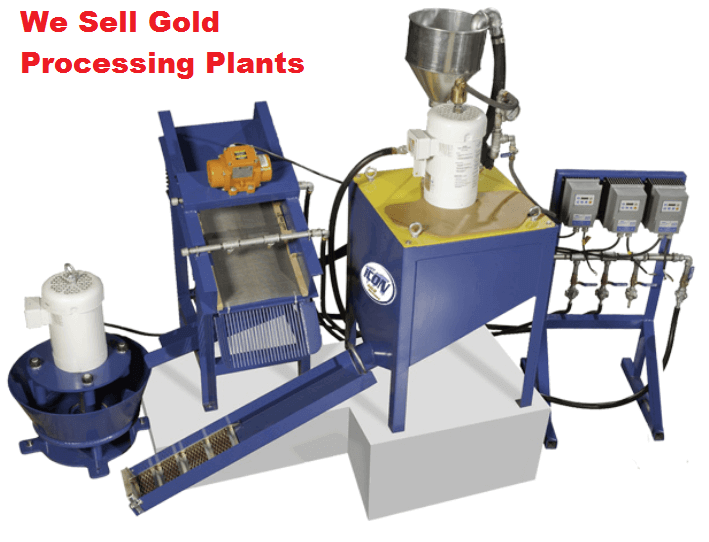
The Crushing plant is designed to crush the ore in one shift (8-10 hours). The Ball Mill and Classifier and the balance of the plant runs 24 hours per day.
Jigging and Amalgamation
To trap the heavy free gold in the grinding circuit a Mineral Jig is placed between the ball mill and classifier. This recovers the gold just as soon as released and avoids its accumulation in the bottom of the Classifier or Ball Mill scoop box. The high grade gold concentrate from the jig is ground in batches and amalgamated in a Amalgamation Unit. The residue from the unit is collected, dewatered, and saved as it usually contains sufficient value for retreatment or shipment to a smelter.
Amalgamation plates are shown in this flowsheet to recover the very fine gold which may escape the jig and overflow the classifier. Amalgam from the silvered copper plates is collected periodically and retorted along with the amalgam recovered from the amalgamated Jig concentrate. Corduroy blankets may be used in place of the plates. The heavy mineral concentrate is ground and amalgamated with the jig product.
Flotation in a Small Gold Processing Plant
The ground pulp after jigging and amalgamation will usually contain 20 to 25% solids which is ideal for flotation feed. This pulp passes to a Conditioner where reagents are added to activate the sulphides and possible tarnished gold values. After conditioning the pulp flows through a “Sub-A” Flotation Machine of the cell to cell type. The flow arrangement is typical for small plants where the ratio of concentration is high. If more cleaning is necessary, the feed may be introduced into the second cell and the final concentrate taken off Cell No. 1. Reagents for gold flotation are simple and usually consist of soda ash, a xanthate, and a frother.
All concentrates including the amalgamation residue are pumped to a Disc Filter for dewatering. Filtering may be direct without thickening. If the quantity of concentrate is appreciable and filtration rates low, a Thickener ahead of the filter is advisable.
Flotation tailings are finally tabled for recovery of oxidized values. This product may be added to the flotation concentrates, or if some free gold is present, it may be amalgamated along with the Mineral Jig concentrate. The Table also serves as a pilot control of the mill circuit both as to grind and recovery.
In this example the concentrates from the Mineral Jig and Table were combined and amalgamated to give the above recovery in amalgam form. With amalgamation plates in the circuit as shown, the recovery of gold in bullion form should approach 80%. The balance of the recoverable gold is in concentrate form for shipment to the smelter. In the example shown the combined shipping product (residue plus flotation concentrate) assays 6.45 oz. gold per ton. From 50 tons milled, 2.88 tons of concentrates are produced.
Preliminary work is recommended on all gold ores such as is available from the 911metallurgist.com Mineral Dressing Laboratory at before establishing the flowsheet and selecting equipment sizes.
CONCLUSIONS: Small Gold Processing Plant for Sale!
The developed flowsheet provides a Small Gold Processing Plant which can be efficiently operated by one operator per shift or with a helper if local requirements so dictate. Power requirements are such as to be available from a portable generator and water requirements are held to a minimum.
For cost data on the flowsheet, reference is made here.