Table of Contents
During the past few years the requirements of manufacturers have increased to the extent that demand for sulphur has almost doubled. New uses, too, are continually being discovered; all of which has thrown more and more burden on Gulf Coast producers. It is apparent that new sources must be found to meet the increased demand, a fact which has called attention to low grade deposits containing approximately 25% sulphur.
Sulphur existing in these deposits must, of course, be up-graded to meet existing standards. It has been proved in recent developments that these low-grade deposits can be successfully and profitably treated by flotation to produce an 85-90% grade sulphur concentrate. This concentrate can be further treated by melting in Heavy Duty Agitators equipped with steam coils and then processing through pressure filters similar to those now used on the Gulf Coast for production of 99% elemental sulphur.
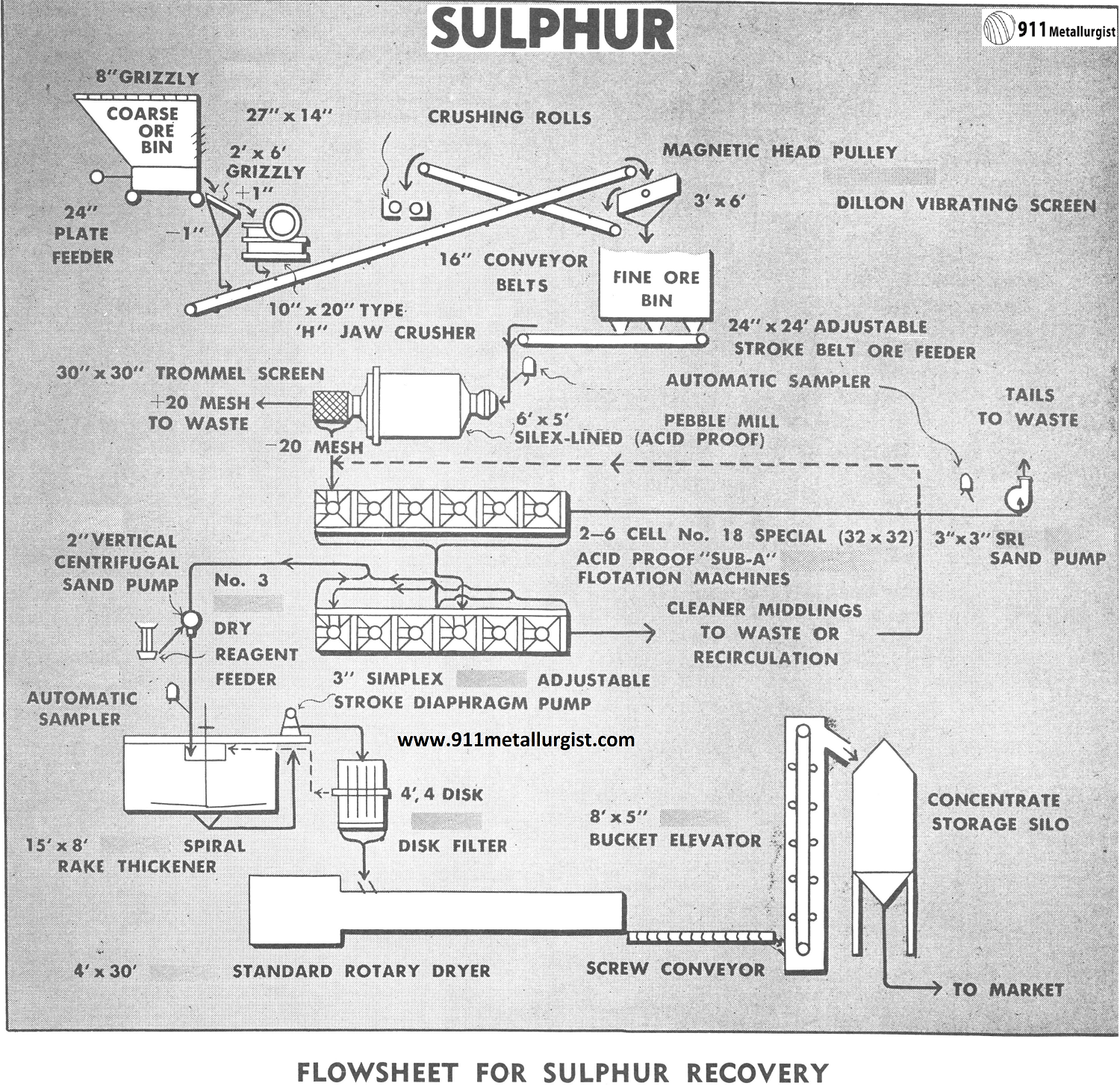
THE Sulfur Recovery FLOWSHEET
The flowsheet above is a typical example of economical treatment of low-grade sulphur by flotation. Due to the variable nature of the sulphur in these deposits, testwork, such as is offered by the 911metallurgy Equipment Company and Laboratories, is recommended to determine the exact flowsheet requirements. Information obtained from these tests will determine the basis for future development.
CRUSHING
Ore is hauled to the coarse ore bin where it is broken through an 8″ grizzly. An inexpensive reciprocating plate feeder provides positive feed to a primary (Type H) Jaw Crusher. In order to keep wear on the jaw crusher to a minimum, a 2′ x 6′ Grizzly bar with 1″ spacings is recommended ahead of the jaw crusher.
Since grinding in this case will be done in an acid circuit using pebbles or balls, a secondary closed circuit arrangement using a Dillon Vibrating Screen and set of Crushing Rolls reduces the ore to approximately This makes ideal pebble mill feed, since pebble charges, due to their light weight, have difficulty breaking down coarse ore. It is usually more economical to make this reduction in the crushing circuit, rather than the grinding circuit.
Rolls equipped with special welded strips across the faces may be used in place of other types of secondary crushers, since the ores usually come from open pit mines and contain a considerable amount of moisture which would tend to clog gyratory type units. A permanent magnetic head pulley protects the rolls from tramp iron.
Moisture may cause trouble too, when ore is discharged from the fine ore bin. The use of several feed hoppers with individual discharge openings has proved to be successful, since the flow can be switched in the event of one opening bridging over.
GRINDING
Grinding, as it is normally thought of, is not required. Since the sulphur values .appear as cementing material or filler between the gangue particles, a scrubbing or polishing action is sufficient to free the sulphur after the gangue has been reduced to grain size. An open circuit pebble mill is recommended to reduce the ore to minus 20 mesh, usually fine enough to free the sulphur from waste. The acid conditions present in the ore necessitates the use of a silica or porcelain-lined Pebble Mill. If large lime deposits are readily available, grinding may be carried on in a neutral circuit using steel balls and a conventional ball mill by adding the required amount of lime rock to neutralize the ore.
An oversize Spiral Screen fitted with 20 mesh outer stainless steel cloth and ¼” stainless backing cloth provides efficient classification of pebble mill discharge. The oversize from this 20 mesh screening operation usually consists of quartz and other gangue material and is sufficiently low in sulphur content that it may normally be considered as waste.
SULFUR FLOTATION
The superior cell-to-cell design and the principles of “Sub-Aeration” incorporated in “Sub-A” Flotation Machines enable the operator to produce the highest possible grade concentrate with excellent recovery.
A rougher concentrate is first produced, averaging 65% sulphur. This is then subjected to two stages of cleaning with the final product assaying 85-90% sulphur. The only reagent usually required is a light alcohol frother.
In view of the low pH of the circuit, usually between 2 and 3, acid-proof “Sub-A” cells with rubber-covered shafts and wearing parts and wood tanks are recommended. This is far more economical than acid resistant alloys and has proved to be more than satisfactory.
To avoid the expense of acid proof thickening and filtration equipment for dewatering the concentrates, a Cone-type Dry Reagent Feeder is used. Four to five pounds of lime per ton are sufficient to neutralize the flotation concentrates. Complete neutralization and thorough mixing are assured by introducing the lime with the flotation concentrate to a Vertical Centrifugal Sand Pump.
THICKENING AND FILTRATION
Neutralized flotation concentrates enter a Spiral Rake Thickener at 30% solids and are discharged at 60% solids by a 3″ Simplex Adjustable- Stroke Diaphragm Pump. Positive control of the pulp density may be made while this pump is in operation.
Thickened concentrates then flow by gravity to a Disk Filter which produces a filter cake of 15% moisture content. The filter is located in such a position that overflow will return to the thickener by gravity.
The filter cake drops by gravity into the feed chute of a 4′ x 30′ Standard Dryer where the remaining moisture is removed. Automatic controls are required to maintain correct temperatures, due to the low melting point of sulphur. Ball strikers should be used with the dryer to prevent adhesion of the material to the shell.
STORAGE
From the dryer, concentrate is taken by a Screw-type Conveyor to an 8″ x 5″ Bucket Elevator which lifts it to a concentrate storage silo. Here it is stored prior to discharge into box cars for shipment.
A Standard, 6-Cell No. 18 Special “Sub-A” Flotation Machine.
Elemental Sulphur Flotation Plant
Elemental Sulphur Market Specifications
The largest single use of sulphur is for the production of sulphuric acid. Other uses are in the paper, rubber, and fertilizer industries.
Ordinary lump sulphur should have a guaranteed sulphur content of 99.5 per cent and be practically free of arsenic, selenium, lead, copper, zinc, iron, and moisture.
Production Problems
Flotation concentration of crude native sulphur does not usually produce a finished grade of sulphur but does make a much higher recovery than treatment by autoclave. The flotation product can then be retreated by autoclave, with much higher recovery of pure sulphur. The lower grade of the flotation concentrate is due to the presence of a sulphur coating on particles of gangue, rendering them floatable.
Reagent Combinations
Usually, the use of an alcohol frother is sufficient, as sulphur is self-promoted. In some cases, slight promotion with xanthate is beneficial.
Sulphur: Acid-proof 8-cell No. 18 Special “Sub-A” Flotation Machine averages 90% sulphur recovery in this western mill.
Source: This article is a reproduction of an excerpt of “In the Public Domain” documents held in 911Metallurgy Corp’s private library.