POWER REQUIREMENTS
25 kVA Generator – 220v/1ph/50-60Hz – 90 amps (not including water pump) All machines are controlled by VFD’s mounted in a control console with start/stop buttons.
WATER REQUIREMENTS
20 – 35 m3/hr (2” Pump recommended) Note: Clean water required for iCON. Separate water source may be required for iCON’s
FEEDING THIS WASH PLANT
This Gold Wash Plant’ Scrubber/Trommel and Screen capacity are 10 tph but iCONS are limited to 2 tph each of -2mm. For example if the feed gradation is 40% passing 2mm, the plant can be fed a maximum of 10 tph. If the feed gradation is 100% passing 2mm, then the plant can be fed 4 tph.
ABOUT USING YOUR ICON FOR THE FIRST TIME
It is important to become familiar with your new concentrator before beginning to process your mineral. The entire installation and familiarization process should take less than ½ day.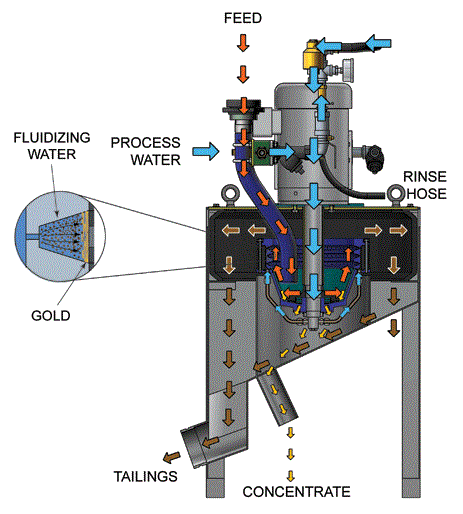
Before turning on the power, look into the bowl using a flashlight.
Here you can see the end of the feed tube.
You can see the three concentrate riffles at the top of the bowl.
In the back of the concentrate riffles, you can see the holes/water jets.
Where the bottom of the bowl joins the wall, you see the narrow gap where the concentrate will exit the bowl. It is important to notice the size of this gap. If you feed your concentrator material larger than this gap it will plug up.
Next, hold your fingers of one hand in this gap and gently rotate the bowl with your other hand. The gap will be smooth all the way around the bowl. In the future, you may notice that the concentrate is not draining and you may feel that this gap is packed with oversized material. If this is the case you will have to form a wire into a hook and remove these oversize pebbles to allow the concentrate to flush easily.
Open the process water valve slowly while looking into the bowl. Slowly turn the bowl with one hand. Notice that all of the holes are spraying water. If, in the future, these holes are not spraying water, you will have to clean the filter or clean these holes.
Now, hold your fingers gently into these 3 concentrate riffles. Gently rotate to bowl to become accustomed to the location and feel of these riffles.
With the water supply turned on, close the process water valve and record the pressure. Now, open the process valve fully and observe the pressure – be careful not to allow this pressure to exceed 50 psi.
Spin the bowl electronically. Using the VFD control, spin the bowl at 2 hertz and then at max (i150 50 hz, i350 37 hz). Now turn on the process water and spin the bowl at min (2 hertz ) and max (i150 50 hz, i350 37 hz) while observing the jets inside of the bowl. At low rpm, the jets will spray to the center of the bowl. At high rpm, water will flow, but not in the form of jets.
While the bowl is spinning and the process water is flowing, note that the water is exiting the machine through the tails outlet. Assure that that fluid is satisfactorily flowing away from your machine and work area.
Now feed water into the slurry inlet. Again ramp the rpm up and down and observe where the water flows.
Once you are satisfied with the concentrator’s electrical function and satisfied with the plumbing inlets and outlets, it is time for a complete wet run. Follow the process: Standard operating procedure.
Once you have conducted a few complete wet cycles and are familiar with the entire process, it is time to feed slurry to your concentrator.
STANDARD OPERATING PROCEDURE
Each Day
- Check the filter to make to make sure it is not blocked.
- Visually inspect inside the bowl to assure water is spraying from each hole.

Starting Procedure
- Spin the motor to desired frequency.
a. i150, usually 50hz
b. i350, usually 37 hz
- Open the process water valve to desired pressure.
a. i150, 5 to 10 psi for milled ore, 15 psi for alluvial
b. i350, 10 to 15 psi for milled ore, 20 psi for alluvial
- Begin to feed the slurry to the concentrator.
Rinsing Procedure (typically requires 1.5 minutes)
- Stop the feed.
- Close the process water valve.
- Spin the concentrator at 2 hz.
- Wait until the motor is at minimum rpm.
- Gently rinse the riffles to drain the concentrate.
General Operating Comments
If the concentrator vibrates, feed it faster and more consistently.
Small diameter concentrators require nearly no maintenance. For equal g’s larger concentrators will have sand exiting the bowl faster and the areas contacted by this high velocity sand will wear out quickly. In both iCONs, this wear part is a used tire, available anywhere in the world.
iCONs also have higher reliability than larger concentrators. The bowls are connected directly to the motor shafts leading to a dramatic reduction in the count of moving parts to service and replace. This leads to higher reliability.
Longer cycle times will lead to richer concentrates. Most hard rock miners use 30 minute cycles while most alluvial miners choose 1 hour cycles.
The most common complication with concentrators is when there is no gold in the feed.
The process water should be fed from a dedicated supply line and pump. Connection to a manifold where other people may be using this same supply may cause wild fluctuation in the pressure and lead to unpredictable gold recovery.
In the case of running multiple icons in series, it is recommended to use a pressure regulator at each icon. Stopping the process water at 1 concentrator may cause a pressure spike at neighboring concentrators. Use of a pressure regulator will limit the effect of this spike.
OPTIMIZATION
The concentrators are very forgiving. They do not need much fine tuning. Usually a new concentrator can be setup in ½ day and generally will not need fine tuning. An operator can be trained in ½ hour.
The operating parameters to consider include:
- Size distribution of feed
- Density of slurry
- Feed rate
- RPM
- Weight of ore/sand
- Cycle time
The water pressure and cycle time are really the only parameters to consider to optimize the iCON operation. From time to time, the operator can gently place his fingers in the riffles of the spinning bowl – at reduced rpm. If the riffles are loosely packed and the material rinses easily from the riffles, pressure is good. If the riffles are so densely packed that it is difficult to rinse them, then increase the water pressure.
For a heavy feed with considerable black sand and/or if using the iCON to upgrade a concentrate you may choose higher process water pressure: possibly 2 times the standard listed above.
Standard cycle times are 30 minutes for the hard rock ore and 60 minutes for alluvial. The simple way to assess the cycle time is to pan the tails every 5 minutes. The time at which you begin to find an increase of gold in the tails will determine your cycle time.
If your riffles are packed with other heavy minerals such as magnetite or galena, you may choose to shorten the cycle time or increase your water pressure.
If the Water Jets are Not Spraying
The y-strainer filter can be cleaned in less than 1 minute. Simply remove the drain plug, rinse the screen and reinstall the plug.
If you see that only a portion of the holes are spraying, the easiest solution is to cut a short piece of wire and ‘poke’ each hole to clear the blockage. This may take up to 10 minutes.
If ‘poking’ out the holes does not allow all the jets to spray, you will have to dis-assemble the bowl to clean out the water jacket. The bowl does not have to be removed from the shaft. You only need to remove the 16 long bolts that hold the 2 part bowl together. With these bolts removed, the bowl can separate into 2 pieces allowing you to rinse the inside of the water jacket and poke the holes from the inside out. This can be done in less than 60 minutes.
WARRANTY
iCON Gold Recovery equipment is backed by IGR’s reputation as a quality manufacturer, and by many years of experience in the design of reliable equipment.
Equipment manufactured and sold by IGR and paid for in full is backed by the following warranty:
For the benefit of the original user, IGR warrants all new equipment manufactured by IGR to be free from defects in material and workmanship; and will replace or repair, FOB at its factories or other location designated by it, any part or parts returned to it which IGR’s examination shall show to have failed under normal use and service by the original user within one (1) year following initial start-up or eighteen (18) months from shipment to the purchaser, whichever occurs first. Such repair or replacement shall be free of charge for all items except for those items that are consumable and normally replaced during maintenance with respect to which repair or replacement shall be subject to pro-rata charge based upon IGR’s estimate of the percentage of normal service life realized from the part. IGR’s obligation under this warranty is conditioned upon its receiving prompt notice of claimed defects which shall in no event be later than thirty (30) days following expiration of the warranty period and is limited to repair and replacement as aforesaid.
THIS WARRANTY IS EXPRESSLY MADE BY IGR AND ACCEPTED BY THE PURCHASER IN LIEU OF ALL OTHER WARRANTIES, INCLUDING WARRANTIES OF MERCHANTABILITY AND FITNESS FOR A PARTICULAR PURPOSE, WHETHER WRITTEN, ORAL, EXPRESS, IMPLIED, OR STATUTORY. IGR NEITHER ASSUMES NOR AUTHORIZES ANY OTHER PERSON TO ASSUME FOR IT ANY OTHER LIABILITY WITH RESPECT TO ITS EQUIPMENT. IGR SHALL NOT BE LIABLE FOR NORMAL WEAR AND TEAR, NOR FOR ANY CONTINGENT, INCIDENTAL, OR CONSEQUENTIAL DAMAGE OR EXPENSE DUE TO PARTIAL OR COMPLETE INOPERABILITY OF ITS EQUIPMENT FOR ANY REASON WHATSOEVER.
This warranty shall not apply to equipment or parts thereof which have been altered or repaired outside of a IGR factory, or damaged by improper installation or application, or subjected to misuse, abuse, neglect or accident.
This warranty applies only to equipment made or sold by iCON Gold Recovery Corp. IGR makes no warranty with respect to parts, accessories, or components manufactured by others. The warranty, which applies to such items is that offered by their respective manufacturers.