Holman Table – Operating & Maintenance Manual
The mill enthusiasts at first hailed it as the cure for all the ills that flesh is heir to in the milling line. A little later it was found to make losses which were serious, and on this account, the table succeeded only to a limited extent in displacing the vanners of the gold-mills. Still later, mill-men in a number of districts throughout the country made special studies of the faults of the machine and devised a number of ways of grouping supplementary machines to overcome as far as possible the losses, and at the same time retain the benefit of the extraordinarily large capacity accompanied by the production of clean concentrates for which the machine has become so justly famous.
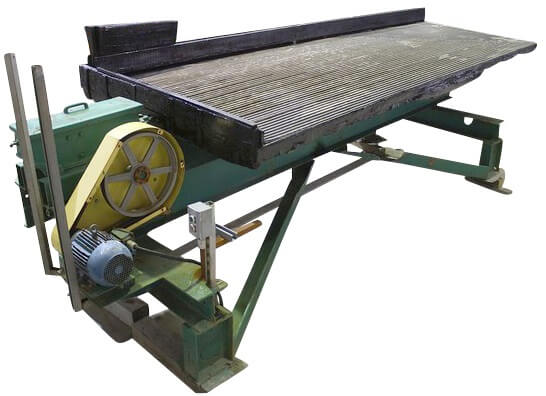
I hope to make an exhibit of some of these methods in an appendix to my book on ore-dressing which is now in preparation. These experimenters have not written up the subject, and if they possess all the facts they have not given them out for the benefit of the mining profession at large.
The object of this paper is to obtain the facts and to present them so clearly that their bearing can be seen by all. To this end, two complete series of tests have been planned. One (the present paper), to study the concentration of galena in presence of quartz; the other (to follow shortly), to study the concentration of chalcopyrite in presence of quartz.
Some authorities claim that the table does its best work when treating natural products; by this phrase, I mean products which have been crushed to pass through a limiting sieve, but have had no other preparation whatever; in consequence, they have all sizes of grains of both the heavy valuable mineral and the light waste gangue, ranging from the largest grains that can pass through the sieve down to the finest dust.
Others claim that the ore fed to a Wilfley table should be closely sized before it is fed. That is to say, it should be divided by a series of sieves ranging from coarse to fine into a series of products with sizes of grain ranging from coarse grains to fine grains; and that each of these products, in which the grains of the heavy mineral are of approximately the same diameter as the grains of the light mineral, should be fed to the Wilfley table.
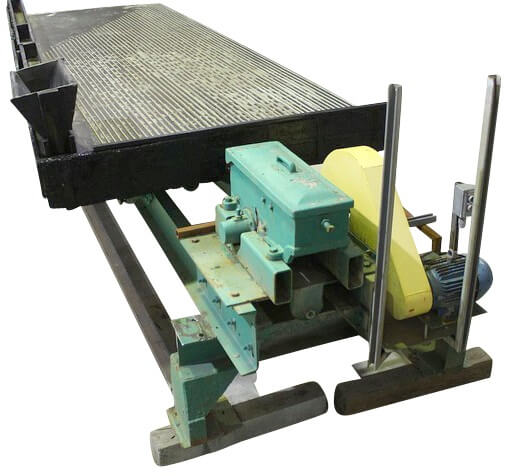
Still, the third group of authorities claims that the ore before being fed to a Wilfley table should be classified by a hydraulic classifier, which divides the crushed ore into a series of products ranging, like the sized products, from coarse grains to fine grains, by carrying it in a water-current over a series of apertures or vertical pipes, called sorting-columns, up through which water-currents are passing. These currents are graded from faster to slower, and therefore allow only the heaviest grains to settle down through the first sorting column and out through the spigot, while lighter smaller grains settle in the second, and still lighter in the third, and so on, diminishing until the last sorting-column and spigot give very small grains, and the overflow has the finest grains of all. The classified products differ greatly from the sized products in that the grains of the heavy mineral is much smaller in diameter than the light grains with which they settle, and therefore behave in a somewhat different way upon the Wilfley table from the sized products. It should be said that the first spigot-product of a classifier differs from the others in having coarse grains of the heavy mineral present also.
The usual division of products upon a Wilfley table is easily and naturally made, as shown in Fig. 1, A being concentrates; B, middlings; C, tailings, and D, slimes. Of these, when natural products are fed, the concentrates, A, are nearly clean heavy mineral, slight contamination of small grains of quartz being present. The middlings, B, carry some large grains and also some small grains of heavy mineral. The tailings, C, carry some very small grains of heavy mineral, and the slimes, D, carry very minute grains of heavy mineral.
I believe that the small grains of heavy mineral in middlings, B, and tailings, C, is of less diameter than the smallest in the concentrates, A, and of greater diameter than the majority in the slimes, D and that they belong in middlings and tailings from the law of their existence. The re-running of such middlings upon the same table is therefore not a wise proceeding, and only admissible as an expedient in small establishments when the quantity of middlings is not sufficient to warrant other provision. So much for the speculation before the investigation was made.
A lower-cost table than an original Wilfley is the RP 4 Shaker Table.
The materials for this test were pure white massive quartz for the light mineral, and crystalline galena, nearly free from blende and other impurities, from Joplin, Mo., for the heavy mineral. The quantities of these impurities were so small as to have little effect on the results. Both minerals were broken down to 2-mm. size, and mixed so as to have approximately 10 percent, of galena and 90 percent, of quartz.