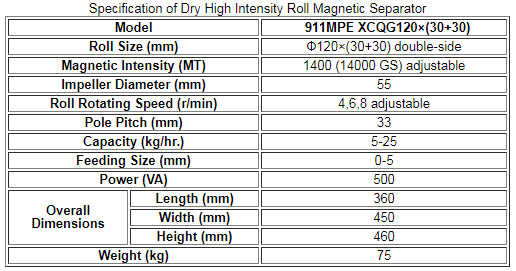
A splitter arrangement is used to segregate the two streams. This separator has a roll width up to 60 inches. The schematic diagram shown in Figure 7 illustrates the magnetic circuit arrangement for a typical rare-earth roll magnetic separator.
The rare-earth roll magnetic separator can effectively treat a wide variety of industrial minerals resulting in high purity products. In fact, it is the separator of choice for upgrading the raw materials for glass production such as silica, quartzite, feldspar, and fluorspar.
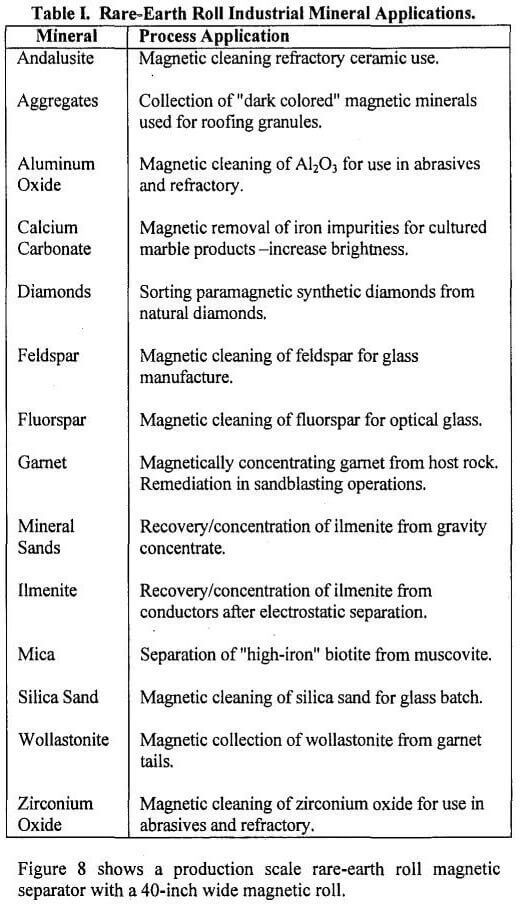
The roll separator is capable of processing 100 kg/hr/cm of roll width of 20 by 200 mesh material resulting in capacities up to 10 TPH on a 1.5-meter wide separator. Typically iron levels are reduced to 0.02 to 0.05 percent. This separator is also used in many specialty and value-added type applications, such as high-purity quartz, as well as many ceramic feedstocks such as alumina, kyanite, mullite, and zircon.
It is typically the case that a double-stage separation is required with the magnetic cleaning of industrial minerals. The non-magnetic product from the first stage separation is repassed to a second stage to further remove any residual iron-bearing components. Generally, between 60 and 75 percent of the magnetics removed in a two-stage separation are removed in the first separation stage. Table I provides a listing of various industrial applications currently using rare-earth roll separators.
Separation Variables
With any type of rotating separator, the magnetic attractive force is opposed by centrifugal force. The primary variables affecting separation efficiency are the magnetic field strength, feed rate, linear speed of the separator surface, and particle mass. An effective separation requires an equilibrium among these variables. In assessing the feed rate, a balance must be struck between an economic feed rate, product specifications, and recovery. As the feed rate increases, the burden depth on the separator surface increases resulting in a loss of efficiency. The increase in burden depth can be offset by increasing the drum speed, resulting in an improved collection of magnetic particles. A practical limit exists, however, due to the centrifugal force acting on the particles. The centrifugal force exerted by the drum or roll surface is the critical factor affecting separation. Beyond the critical speed, the centrifugal force overcomes the magnetic attractive force and the separation efficiency deteriorates.
Particle size also affects separation efficiency. Coarse particles provide a high burden depth on the separator surface and respond with a relatively high magnetic attractive force. Coarse particles typically provide high unit capacities with high separation efficiencies. Fine particles demonstrate a lower magnetic attractive force. As a consequence, lower burden depths must be maintained resulting in lower process capacities.
Locked particles consisting of a magnetic portion and a non-magnetic portion are usually collected with a magnetic separator. In some applications the collection of these particles can be problematic. A locked particle reporting to a magnetic concentrate will in many cases account for any trace contamination, such as the case of silica in hematite or ilmenite concentrates.