Curved pulp lifters have been incorporated in SAG and AG mills in Australia. The aims have been to ensure complete discharge, at high throughput, of both slurry and coarse solids, especially at high mill rotational speeds. Curved pulp lifters can overcome incomplete discharge and back-flow of solids down the pulp lifter that can occur in straight-radial pulp lifters (and is a major cause of wear). They can be designed to prevent reverse flow of pulp via grates back into the mill. Experience with curved pulp lifters now extends to three years over three mills, in one mill as an installation from new and two as retrofitted installations. Curved pulp lifters, relative to conventional designs, offer improved discharge and wear performance and well as high impact-resistance and wear life of the curved pulp lifter grates.
Discharge of solids from straight radial pulp lifters is commonly incomplete and results in the back-flow of solids down the pulp lifter. This back-flow is the major source of wear in the base and head-side corners in pulp lifters. Curved pulp lifters initiate the motion of solids earlier in the rotation of the mill resulting in essentially complete discharge of the pulp lifter contents in one rotation of the mill.
DESIGN AND PERFORMANCE OF CURVED SAG MILL PULP LIFTERS
The Kambalda 26 ft AG Mill curved pulp lifters were installed from new. The principal objective in this design was to provide pumping capacity for very high recirculating loads anticipated in that mill. This mill has curved pulp lifters fitted to a curved drilling pattern. It uses bridging grates.
A curved pulp lifter and curved composite cantilever grate system was retro-fitted to the Northparkes 24 ft SAG Mill (the Bradken “Vortex” design). The principal process objective with this mill was to provide a capability “to pump rocks”. Up to 30% of oversize is being recirculated to the mills via recycle crushers.
A similar pulp lifter system has been retro-fitted to the 28 ft SAG Mill at Northparkes. The main driver in this case was to improve the life of grates and pulp lifters compared with the straight radial system then in use.
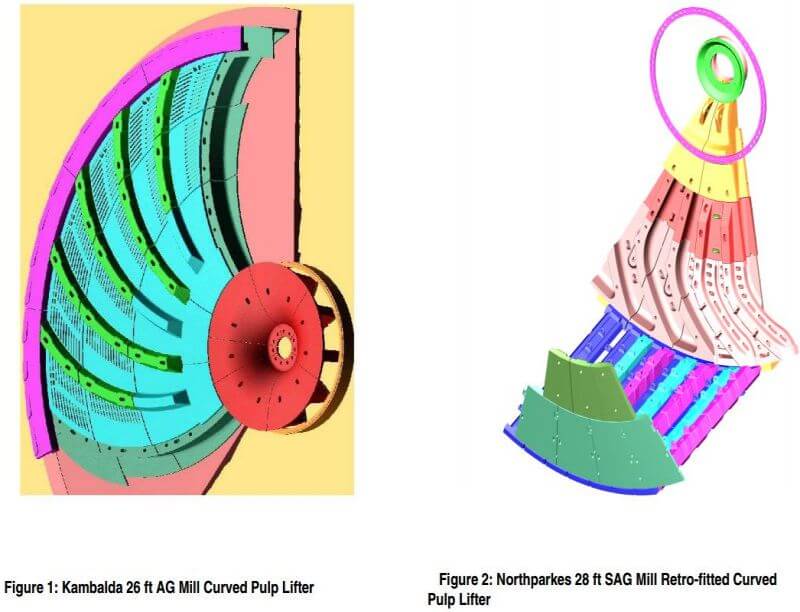