Recover Copper from Oxides using Iron and Steel Scrap
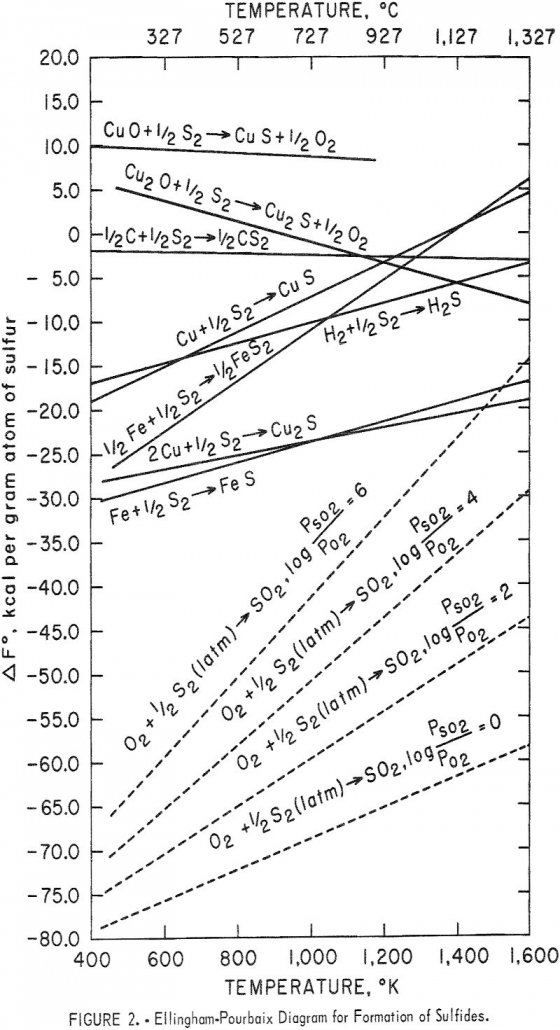
For the past two decades, about one-third of the copper consumed in the United States has been imported. In order to meet the Nation’s demand, new and improved methods of copper extraction must be found. Ferrothermic extraction is one possibility; the Bureau of Mines undertook this investigation to determine the principles and optimum conditions of […]
Amalgam Electrorefining of Zinc & Tin
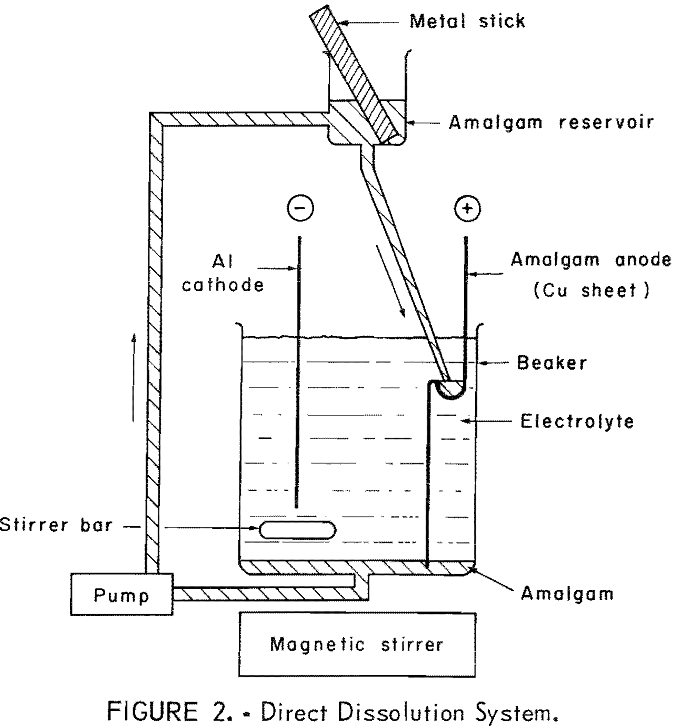
The following conclusions are drawn from the results of the laboratory tests of amalgam electrorefining of zinc and tin: Amalgam electrorefining is a method by which these metals may be refined to total metal impurity concentrations of less than 5 ppm in zinc and 9 ppm in tin. The suitability of metal for amalgam refining […]
High Temperature Electrostatic Precipitator
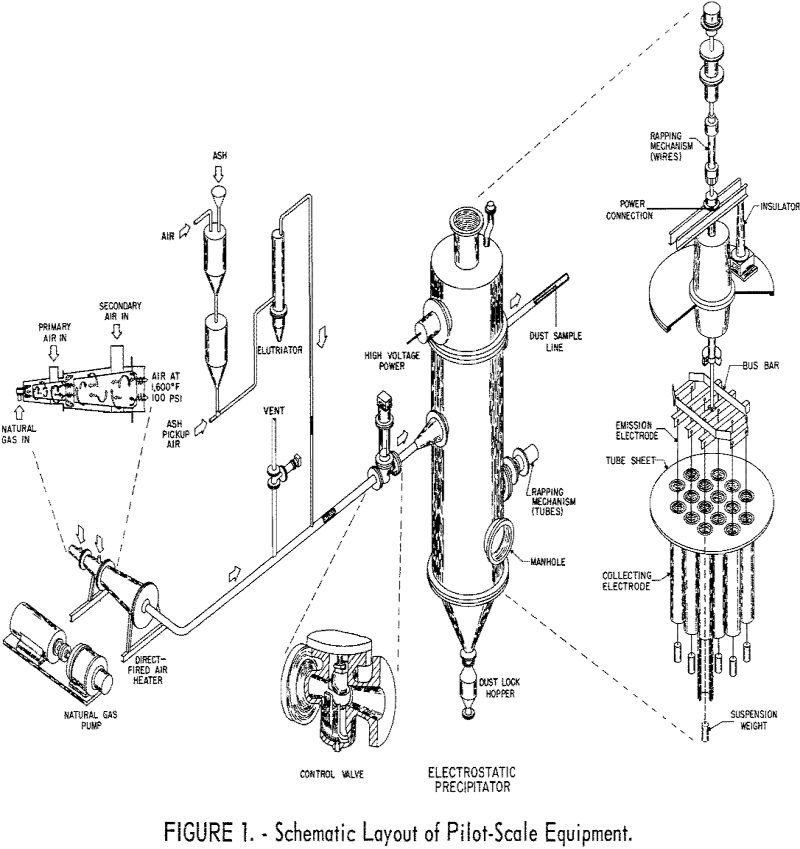
Industrial precipitators utilizing negative corona operate at maximum voltage to attain highest efficiency in removing finely divided particles from gas streams. Usage, however, is limited to applications at temperatures to about 1,000° F. Therefore, in conjunction with other work for processing coal at high temperatures, the Bureau of Mines sought to extend the applicability of […]
Small Particle Size Minerals Magnetic Separation
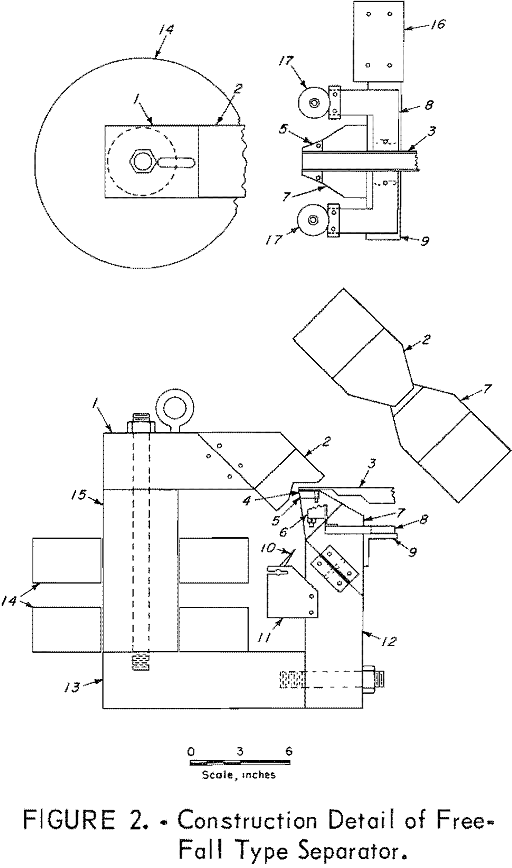
By using the magnetization delay factor and the acquired momentum of the particle, minerals may be separated with magnetic susceptibilities within the diamagnetic susceptibility range. Unlike the rotating drum of the induced roll separators , and the feed belt of the cross-belt separators, which feed the particles in close packed moving layers, the vibrating feeder […]
Method for removing aluminum from diecast scrap
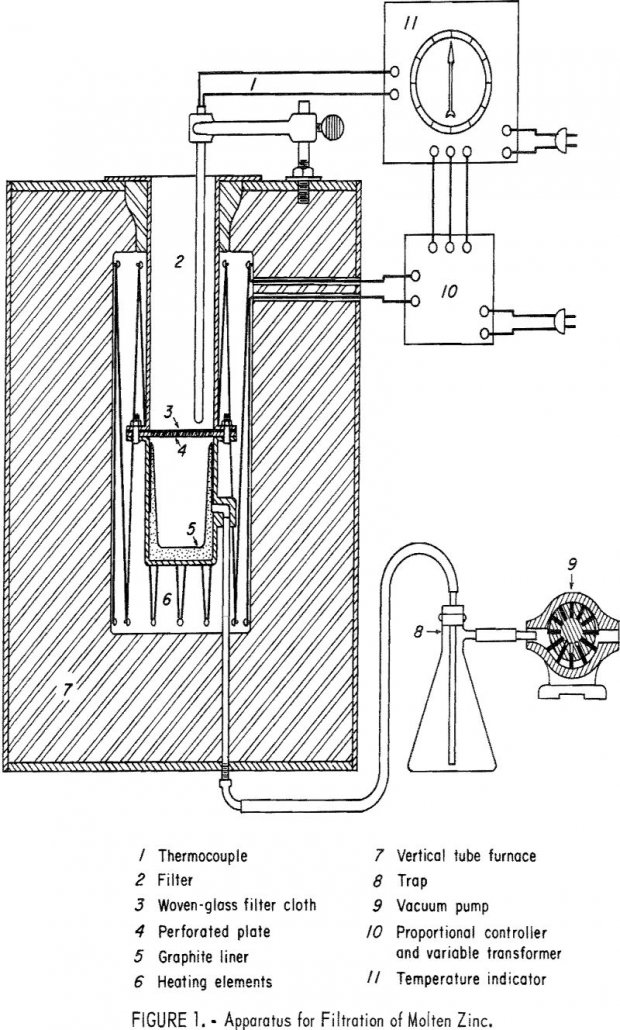
Zinc-base die-cast scrap represents the largest single source of secondary zinc. A large part of the die-cast scrap originates from grills, fuel pumps, carburetors, trim, and hardware from scrapped automobiles and other machinery, or from punchings or factory rejects of these components. A typical mixture of die-cast scrap contains from 3 to 5 percent aluminum […]
Joining Refractory Metal Compounds by Hot Pressing
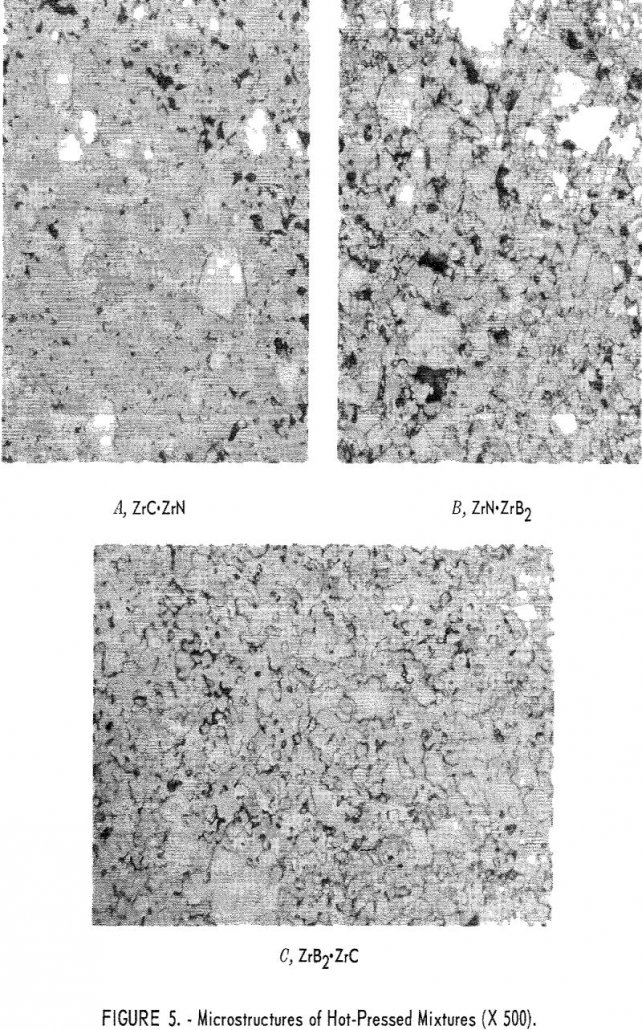
The results of this research indicate that diffusion bonding of refractory metal compounds is a promising method for joining dissimilar materials. Fabrication of graded joins by vacuum hot pressing a mixture layer between two end materials proved to be very satisfactory for the joining of nitrides, carbides, and diborides of zirconium and titanium. Joint evaluation […]
Induction Melting of Titanium
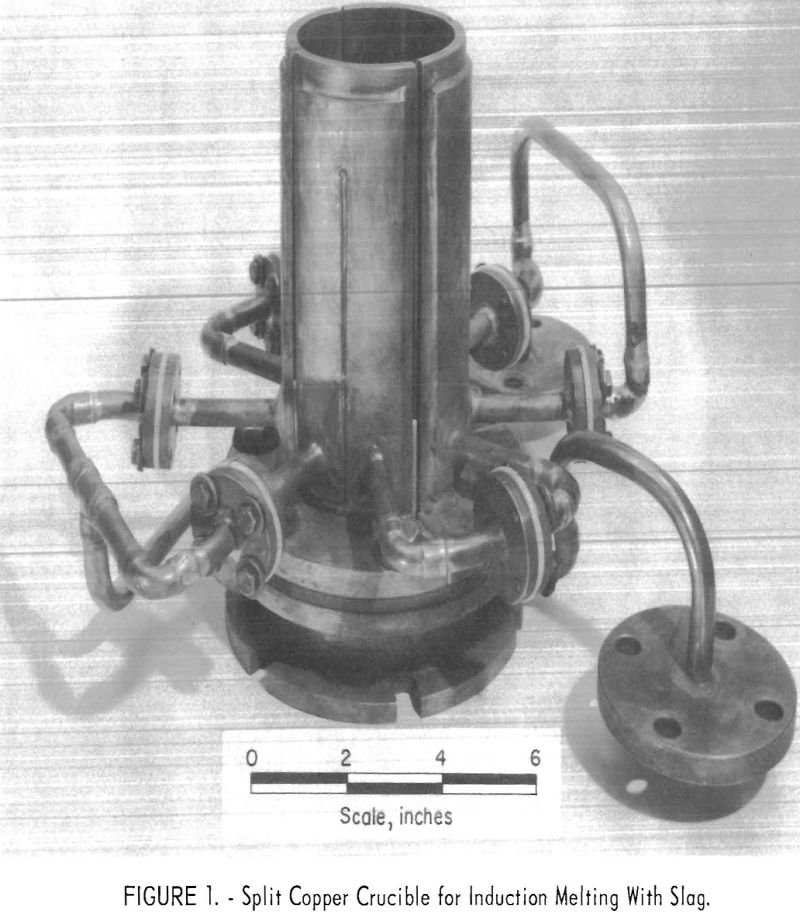
The primary purpose of the research covered by this report was the development of a method for induction melting titanium in a water-cooled copper crucible. The results reported represent findings obtained during the melting of a minimum number of ingots; therefore, only tentative conclusions can be drawn regarding the effects on metal quality of many […]
Recycle & Recover Titanium Chlorination Residues
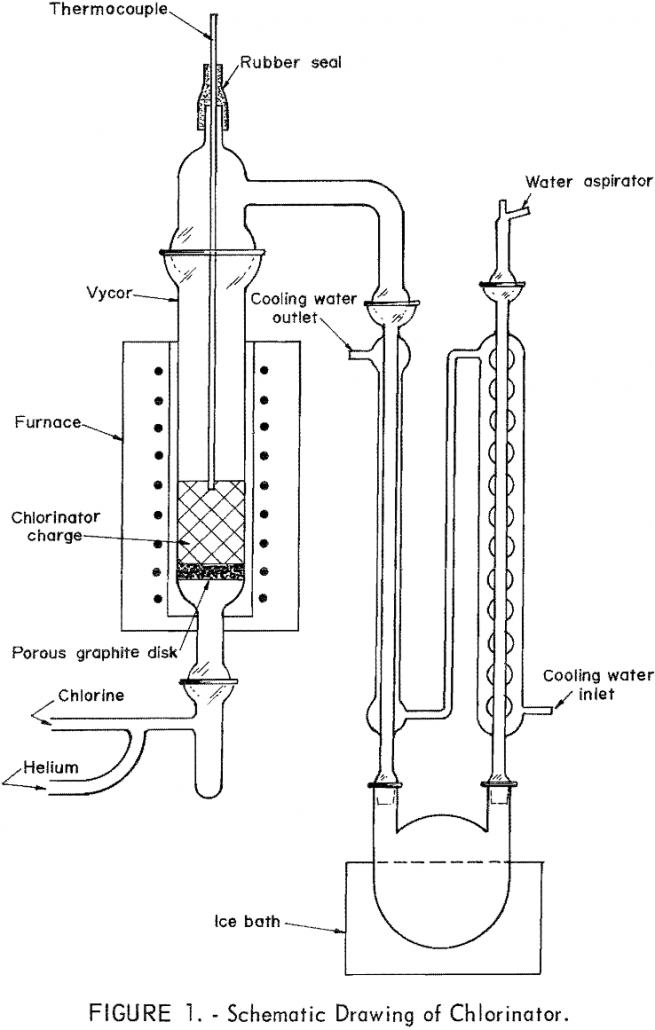
Approximately one-half of the weight of the sludge generated in the commercial production of purified TiCl4 from rutile can be recycled with a coincident diminution of waste disposal problems and the more efficient utilization of TiO2 and carbon in the processing operation. The sludge can be separated into soluble and insoluble fractions by water leaching, […]
Drillability – Percussion Drilling
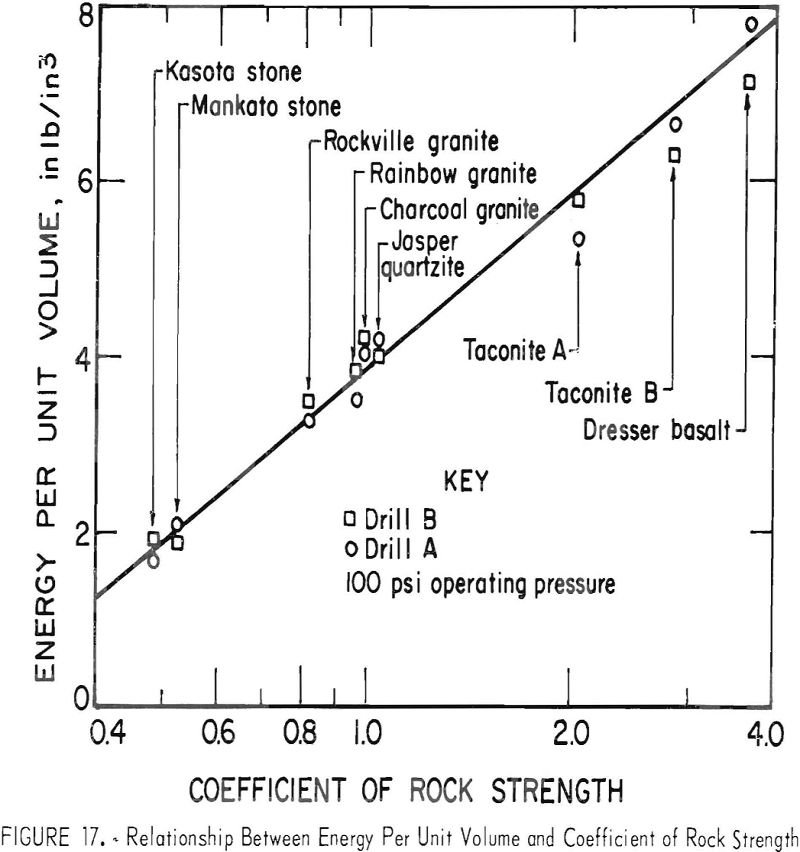
Penetration rate is increased by an increase in applied thrust up to an optimum point after which penetration decreases until the drill eventually stalls. Higher operating pressures result in increased penetration rates with the only apparent limitations being the design characteristics of the drill and bit and the ability to remove the cuttings produced. Rock […]
Ferrous Iron Oxidation by Activated Carbon
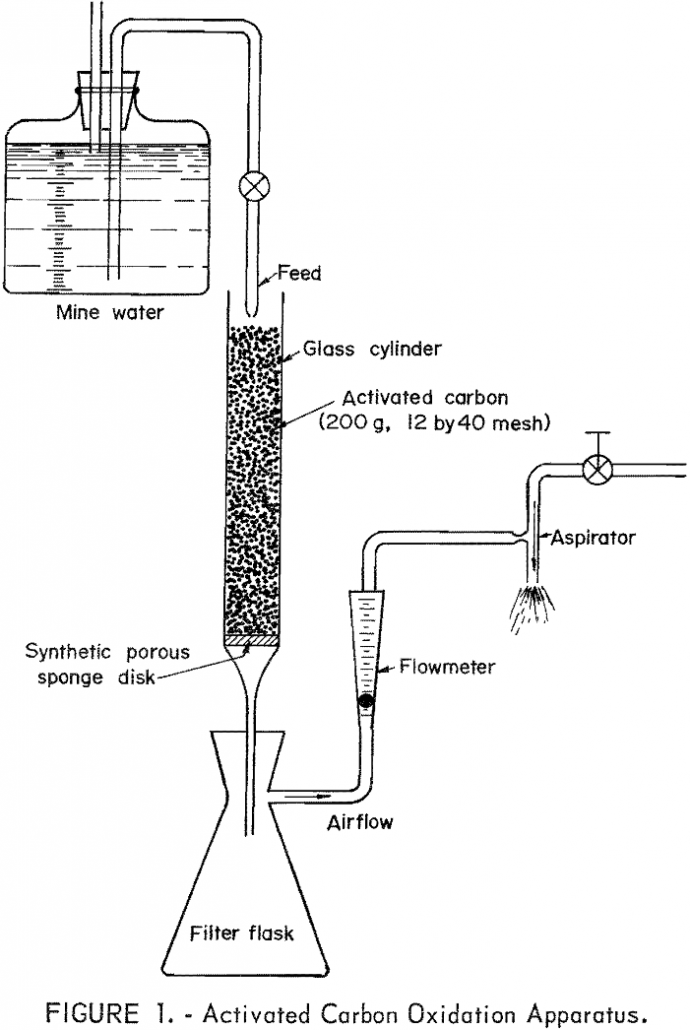
The exploratory tests conducted with activated carbon and a ferruginous acid mine water indicate that ferrous iron oxidation takes place catalytically at an extremely rapid rate. The brevity of this study did not allow defining the reaction kinetics, or resolving the various factors affecting the activated carbon-air-acid mine water system. The favorable preliminary results warrant […]