Table of Contents
The term “secondary crushing” has become well established and familiar through long usage; it applies to the crushing stage, either single or multiple, which follows immediately after the primary crusher, taking all or a portion of the product of the primary crushing stage as its feed. The term should not be used, as it sometimes is, to designate a particular type or size of crusher because any type and size might conceivably be used for secondary crushing. A very large number of secondary crushers in our present-day plants were originally primary crushers in those same plants. “Secondary” and “second-stage” are synonymous, and are equally good and descriptive definitions.
The term “tertiary” has been used rather extensively in recent years to cover not only third-stage crushers, but in a more general sense to delineate any and all crushers in the reduction and fine-reduction classes; a use which certainly takes liberties with the intent of the word. It is a legitimate term as applied strictly to a third stage of reduction, just as “quaternary” may be used to designate a fourth stage. Our own preference is to designate these successive reductions as “third-stage,” “fourth-stage,” and so on, and to identify the crushers themselves by the titles which usage has conferred upon them.
“Reduction-crushers” and “reduction-crushing,” through the same authority of common usage, have been narrowed from the broad scope of their definitions to delineate reductions in the intermediate sizes of product, loosely in the range between 3″ and 1″ screen sizes. “Fine-reduction,” in the same fashion, has come to cover the production of sizes in the range below 1″, approximately. More recently still, the “fine crusher” has been introduced to extend the application of the gyratory type down into that borderland between crushing and grinding formerly monopolized by the crushing rolls and the hammermill.
Secondary Crushing Stage
The simplest form of secondary crushing stage involves a single crusher, taking its feed by gravity flow direct from the primary with no interposed scalping separation. This is tantamount to making the over-all reduction in one machine, except of course that there will always be a certain amount of surge capacity between the two crushers. This type of installation has been used in a number of plants, starting with the advent of the power shovel and the large primary crusher, many of which were “tacked on” to existing plants during the conversion from hand-loading to shovel-loading operation. Probably the most notable of such installations were those of the first jaw crushers of the 84″ class. These big machines were designed to operate at rather coarse discharge settings, usually from 10 to 12″, and the usual practice was to follow them with gyratory crushers such as the No. 9 (21″)’ or No. 10 (24″), the over-all ratio-of-reduction for the two machines being 14 or 15 to 1.
The simple two-crusher, screenless arrangement works out fairly well for the large sizes of primary jaw crushers if the quarry-run rock is reasonably clean, or if any fine material which may be present in the feed is free flowing. The arrangement is not advisable under any circumstances if the setting of the secondary crusher is to be less than about 5 in.; for finer settings than this the fines produced through the two stages are apt to promote a sluggish action in the secondary machine, which might under certain conditions build up to a complete choke in this stage.
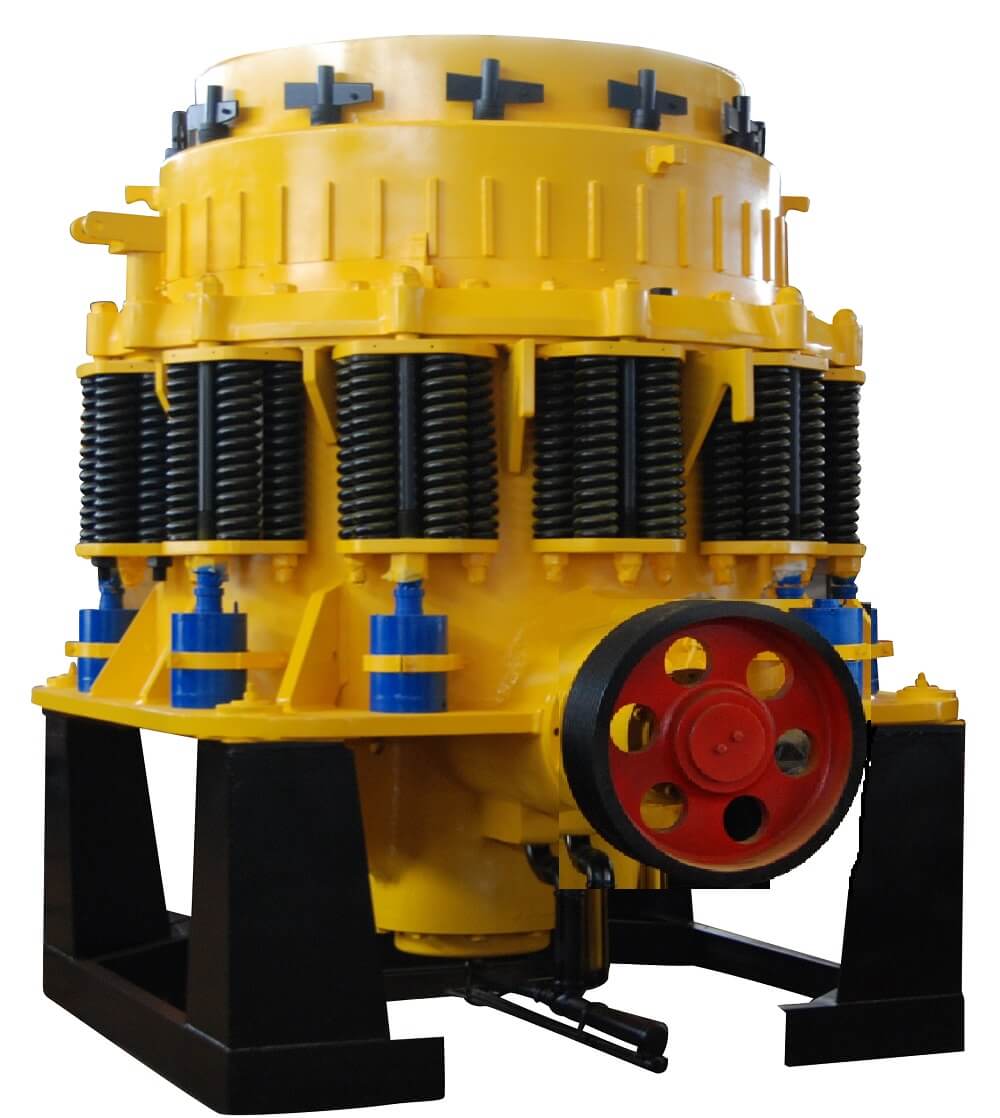
So far as the commercial crushed stone plant is concerned the method violates the well established and very desirable principle of scalping off fines between all crushing stages in order to minimize further production of fines by attrition. The safest practice in all cases is to scalp between the primary and secondary stages regardless of the sizes of crushers used or their discharge settings. A plain grizzly is better than nothing; a modern heavy- duty vibrating screen is the ideal heavy-duty scalper.
Three factors are of prime importance in selecting the size and type of the secondary crusher, or crushers:
- capacity;
- size of feed,
- size of product.
You add to these the item of product characteristic, which embraces shape characteristic, and gradation. These are not always important, but they are sometimes very much so.
Capacity of Secondary Stage
The capacity of the secondary crushing stage need not necessarily match that of the primary crusher; more often than not it can be substantially less, for reasons outlined in the preceding section. It must of course be adequate to handle its share of the total plant capacity. How much its capacity should exceed the average plant capacity will depend upon how the job is engineered.
If the installation is of the simple “one-two” variety we have just described, and very little surge capacity is provided between the two stages, the capacity of the secondary stage should at least equal that of the primary; otherwise the quarry equipment may be held up at times, waiting on the secondary crushing stage to clear itself. If, on the other hand, an adequate surge is provided to take care of the inevitable fluctuations in feed-rate to the primary, the capacity of the secondary stage may he predicated on requirements of the succeeding stages. This presupposes that the secondary machine or machines will be large enough to eliminate delays due to bridging or blocking of the feed from the primary.
If scalping between the two stages .is resorted to, the rating of the secondary stage may be reduced by whatever amount of undersize material is to be removed from the product of the primary. This can be determined within reasonably close limits by means of the product-gradation curves we have presented. In making this calculation it should be remembered that the scalping screen, regardless of type or size, will not remove all of the undersize. From 85 to 90% efficiency is the usual range, therefore the 10 or 15% undersize which will be carried over must be added to the theoretical tonnage, as figured from the curves, in arriving at the estimated feed to the secondary stage.
Once the required capacity for the secondary stage has been determined, it may be checked against tabulated ratings, at the desired discharge setting, for the type of crusher being considered for the stage. In making this check it should be remembered that capacity tables, while they are prepared on a conservative basis, are predicated upon a uniform rate of feed; and upon the’ assumption that the crusher is in first-class condition.
If for any reason it is expected that the feed rate will not be uniform, adequate allowance should be made for whatever degree of fluctuation is anticipated, just as was suggested for the primary crusher. Also, inasmuch as it is to be expected that some drop in efficiency of the crushers will occur from time to time because of mechanical conditions, some allowance should be made for this, regardless of whether or not the feed rate will be uniform. From 10 to 15% will be sufficient for this in a properly maintained plant.
Surge storage between the primary and secondary stages, while always theoretically desirable, may not always be practicable or economical. The product of the very large sizes of jaw crusher, for example, may be so coarse and slabby that it would be exceedingly difficult to handle through a surge bin or on mechanical feeders of reasonable size and cost. Therefore, where these large jaw crushers comprise the primary stage, it is generally best to consider the two stages as a unit and to match their capacities closely enough so that the material can be kept on the move; providing only a small open surge space between them. Then, if surge storage is desired it may be incorporated in the flow line after the secondary stage. The product of the largest sizes of gyratory crushers can be handled satisfactorily through storage.
Crushing Plant Design and Layout Considerations: Ken Boyd, Manager, Material Handling, AMEC Mining & Metals , Vancouver, BC