Table of Contents
For the first time in a gas fluxer, the G-Series offers a reliable temperature monitoring of the fusion process (patent pending). Nothing has been left aside, from perfect monitoring to perfect fusion: this will lead you to premium analytical results.
Instruments are available in 4 or 8-positions units:
- preparation of glass disk for XRF analysis
- preparation of solutions for ICP or AA analysis
- hybrid version for disk and solution preparation
- peroxide fusion version
The best systems for the sample preparation by fusion:
- With a very small footprint, the G-Series instruments allow the fully automated preparation of samples by fusion.
The instrument self-calibrates and communicate its status in real-time over a network.
Using only low-pressure propane or natural gas, we achieve the perfect fusion conditions. - The proprietary temperature monitoring system insures a perfect fusion every time.
The gas high-resolution gas control allows better repeatability, increasing your analytical precision.
The mechanical system has been carefully crafted for better stirring and faster sample dissolution. - The G-Series is designed for the most demanding environment.
The mechanical components are oversized and easily maintained on-site.
With long-lasting components forming the backbone of the instrument, the operating cost is extremely low.
A superior control of the fusion process is the starting point of first-class analytical results
At Nieka, we used our strong experience from the fusion industry and forged an instrument that is the perfect fit for the most demanding high-throughput fusion laboratories. Downtime is your enemy and using the best tool is your only way to remain on top and deliver results on time.
For the last years, we spent thousands of hours creating just what you need: a high-throughput instrument that creates perfectly homogenous samples for analysis with no surprise. Thanks to the Nieka exclusive monitoring features, you avoid the unpredictable, even if you are off-site.
Features
- High Productivity:
Produces 4 to 8 glass disks or solutions per cycle (up to 48 samples per hour). - Automated Operation:
Multilingual touchscreen controller with easy to access controls, import and export fusion method from USB or network, easy to follow fusion program execution through the instrument’s display or PC. All fusion parameters can be fully customized for optimal sample preparation. - Monitoring:
Temperature monitoring of the fusion process (patent pending), real-time monitoring through the Nieka data management system. - Efficiency and Repeatability:
Proprietary heating chambers (patent pending) allow a high thermal efficiency and higher fusion temperatures for difficult samples. Each chamber is well separated from the surroundings, allowing a perfect repeatability. - Easy Installation:
Only a low-pressure gas line and a standard electrical outlet are required. The G-Series runs on propane, any other liquid petroleum gas (LPG) or natural gas. No compressed air or oxygen is required. - Options:
The G-Series fluxers are available in 2 versions: 4 and 8 positions. Each unit can be delivered to make glass disks or solutions only or both (hybrid). - Safety:
Integrated locking safety door, real-time flame monitoring and automatic shut-off features, regulatory shutdown button. - Connectivity:
USB ports, TCP/IP Ethernet port. - Requirements:
100-240V (50/60Hz) electrical supply, propane/ LPG (37 mbar – 0.5psi) or natural gas (20 mbar – 0.3 psi) line.
Built-in safety cabinet
You can see the entire fusion process and a locked door, that opens only when the cooling step is over, protects you. From the real-time flame monitoring to ultimate user safety, nothing has been left aside to provide you with the safest operation.
Sturdy mechanical systems
Nothing lasts forever but we’re getting pretty close with the G-Series: every component is oversized and built to outlast anything else in the industry.
Fusion temperature measurement
Our proprietary fusion enclosure allows the instrument to run on low energy while achieving the required high fusion temperature for difficult samples. For the first time on a gas fluxer, the G-Series reports an accurate temperature measurement of the fusion process (patent pending).
Huge built-in touchscreen
Use the built-in touchscreen display to edit your methods easily and follow the fusion process in real-time.
Connectivity
USB or Internet, your fusion recipe can be uploaded to your instrument in a breeze. Manage your methods using our customized computer and tablet interface.
Advanced self-monitoring
Thanks to its self-monitoring feature, the G-Series fluxer analyzes all instrument functionality and logs all the cycles so we can handle the maintenance schedule remotely. That’s one more thing off your shoulders.
Dedicated mold heating
G-Series fluxers have separate burners for the molds. You can pre-heat any size of mold while reducing your overall fusion process time. The hybrid includes a snap-in module to prepare solutions for AA or ICP sample preparation.
We used our strong experience from the fusion industry and forged an instrument that is the perfect fit for the most demanding high-throughput fusion laboratories. Stay tuned for some of the key features of the G-Series automatic fusion machine.
The huge built-in touchscreen allows for an easy to follow program execution through the instrument’s display. You can easily edit your methods and follow the fusion process in real time. The G-Series produces 4-8 disks or solutions per cycle and up to 48 samples per hour.
You can manage your methods using our customized computer and tablet interface. While importing and exporting fusion methods via USB key or your network. All fusion parameters can be fully customized within seconds for optimal sample preparation. The G-Series fusion instruments run on low energy while achieving the required high fusion temperature for difficult samples. And the fusion temperature measurement allows for accurate temperature measurement of the entire fusion process.
Separating heated chambers allow for a high thermal efficiency, higher fusion temperatures for difficult samples and perfect repeatability. The built-in safety cabinet features an integrated locking safety door that only opens when the cooling step is over. The real-time flame monitoring and automatic shutoff features provide added safety.
Installation of the G-Series borate fusion machine is easy, as the instruments do not require compressed air or oxygen.
Follow us now as we demonstrate a cement sample fusion process. The unique labware clips allow easy manipulation of the crucibles. You can select the number of samples to be processed simultaneously. The very efficient mixing process allows shorter fusion times through faster sample dissolution.
You can mix clockwise, counterclockwise or alternate between the two. The mold preheating can be fully customized in the fusion program. Very efficient blowers allow for faster cooling of the fused beads and the lab wear at the end of the program. You can process most samples in under 10 minutes.
For optimal results, contact us today to discuss how one of our G-Series fusion instruments can help you take your fusion process further, faster. We are here to deliver first-class analytical results every time.
Borate Fusion Applications
Shown is the application fields of XRF analysis and of fusion beads method (underlined). Wide application range for oxide powder can be seen.
The fusion bead method is an advanced analysis method having advantages shown below and registered as an international standard analysis method for refractory and iron ore.method having advantages shown below and registered as an international standard analysis method for refractory and iron ore.
- Chemical analysis of refractory products by XRF—fused cast bead method
- Determination of various elements by X-ray fluorescence spectrometry
- Eliminate the mineralogical effect and grain size effect
- Reduce coexisting component effect by dilution effect
- Possible to make standard samples from synthetic oxides.
The fusion bead method is an effective sample preparation technique for accurate XRF analysis results of ores, rocks and refractory materials since the technique eliminates heterogeneity due to grain size and mineralogical effect.
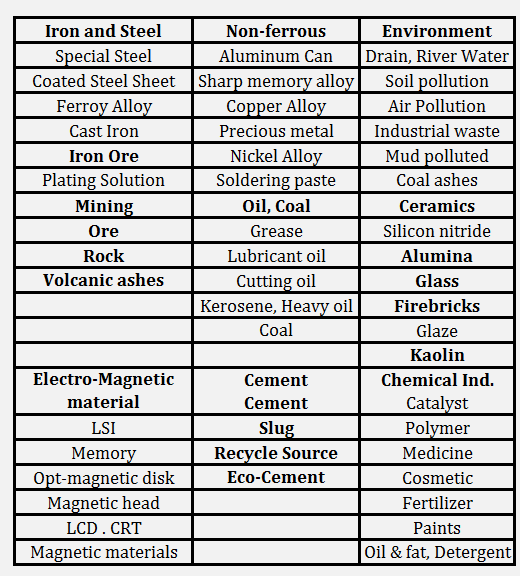
Iron and Steel
Iron Ore Plating Solution |
Non-ferrous
|
Environment
|
Mining
Ore Rock Volcanic ashes |
Oil, Coal
|
Ceramics
Silicon nitride Alumina Glass Firebricks Glaze Kaolin |
Electro-Magnetic material
LSI
|
Cement
Cement Slug Recycle Source Eco-Cement |
Chemical Ind.
|
—
XRF is a really great technique
- XRF is the only technique for elemental analysis that allows the direct measurement of a sample without vaporization and prior digestion.
- XRF is generally non-destructive for the sample
- Handheld or mobile systems offer direct approach
Direct XRF analysis without any contact!
Can we always measure directly?
Direct measurement of the sample is possible, but:
- Size limits applicability
- Physical effects and homogeneity limit application
- Sample needs to be representative
How do we get a sample?
From sample to specimen
Requirements for a prepared XRF Sample
- Representative of the material to be analyzed
- Homogeneous
- Consist of particles small enough so that several particle layers will be measured
- Smooth flat surface without irregularities
- Fit the sample holder being used
- Completely cover the opening in the sample holder
- Thick enough to be infinitely thick for the X-rays to be measured
The advantage of XRF analysis: easy, fast sample preparation
Please use your mouse to answer the question to the right of your screen:
What sample preparation techniques do you use?
□ Pressed Pellets
□ Fused Beads
□ Metal (polished/surfaced)
□ Liquid sample prep
□ Loose Powders
□ Other
While we wait for the results
Hands-on seminars for sample preparation:
- ½-day seminar during Denver X-ray Conference (July 27th 2009), Denver, CO, USA
- 3-day seminar during ICDD Sample Prep Workshop (Oct 13th 2009) at Newton Square, PA, USA
- 1-day seminar during 5-day XRF Summer School (May 30th – June 4th 2010) University Western Ontario, London, ON, Canada
Definition of Terms Accuracy and Precision
Precision:
closeness or agreement among replicate results
Accuracy:
the nearness of a result to the “true result”
Definition of Terms Quantification
In XRF quantification is based on :
Ci = Ki . Ii . Mi . S
where Ci = weight fraction of element ‘i’, i.e. Ci = C%/100
Ki = the calibration constant for element ‘i’ (%/kcps)
Ii = net peak intensity for analyte element ‘i’ (kcps)
Mi = matrix correction term for element ‘i’
[∑n(µnCn)] or [1 + ∑j(αij Cj)]
S = specimen preparation term, equal to Ss/SStd
Definition of Terms Analyzed layer on the sample surface
- No excitation within upper part of the sample (white)
- Center part of the sample will be excited, but the emitted radiation will be absorbed within the sample (light pink)
- Measured radiation comes from a layer near the sample surface (dark pink)
Analyzed layer in different matrices
Analyzed layer controlled by:
- Energy of line being measured
- Average atomic number of sample (density)
0.01µm = 10 nm = 100 A
What do we need to do?
- Sample preparation needs to be FIT for purpose.
- We need to provide the requested information
as fast
as precisely
as economically (cost)
as easily
as repeatably (by different operators)
as accurately
as needed.
Grinding
All samples need to be ground.
- Grind the sample to desired/required fineness!
Grinding From sample to specimen
Pressed Pellet
- How does it work?
- What do we need to consider?
- Pitfalls?
- Universal?
- Automatic?
- Useful?
Principles Pressed Pellet Preparation 1
Pressed Pellet Preparation 3 Issues to consider
- Standards (reference) available from same matrix?
- Desired accuracy?
- Desired precision?
- Cost/sample
- Speed → How fast do you need the result?
- Trace element analysis
Accuracy and precision are limited by sample prep and reference samples
Can we use pressed pellets?
How long do we need to grind?
Do we need an additive to help with the grinding?
Do we need an additive to keep the pellet together?
What pressure do we need to form the pellet?
Can we prepare the standards the same way as the unknowns?
Can we get the precision needed for production?
Analyzed layer/homogeneity
- Sample should be ground to uniform particle size
- Ideally the particle size should be much smaller than the analyzed layer depth
Analyzed layer / homogeneity
We need to grind long enough to get enough particles!
Pressed pellet preparation
- Optimize grinding time to ensure that sample fineness is reached
- Sieve, granulometric determination or “flour feel”
- Parameters to adjust to match reference to samples and analyzed layer!
- Measure I of characteristic emission line for the element and plot vs. grinding time to assess fineness of material
- Vary parameters of grinder (impact, time)
Issues with grinding (selection of additive, heat, time)
- Caking
Issues with pressing (pressure, binder, fineness)
- Disking
- Cracking
- Dusting
- “Reactions”
Universal pellet preparation method
Advantages
No caking in vessel
- Vessel can be cleaned by brush and compressed air
- Keeps sample homogeneous
- Minimizes cross contamination (except from vessel)
Slurry grind
- Reduces sample size more effectively since larger area of ring and puck is used and avoids caking
- Keeps sample homogeneous
- Reduces heat → caking
Dilutes samples 10% with micro cellulose
- The finer the particle size, the greater the effect of the diluent
Stable pellet. No cracking. No dust (when used with Al cup or ring)
Universal pellet preparation method
Recipe
- 5.0X grams sample (100cc vessel) max 20g
- 0.5X grams Cellulose (1 micron Whatman) max 2g
- 5 ml DuPont Vertrel XF
- 90 sec grind in ring and puck mill (WC 100cc vessel )
- Depends on matrix and can be 45 to 120 sec (max!)
- 15 sec press at 40,000 lbs (20t) in 40mm die mold (integrated)
- Cellulose backing if needed (based on volume of sample and desired prep (e.g. pressed into cup or “sandwich” )
Caking is Bad Boric Acid – 90 sec – after brushing
Cellulose/Vertrel XF – 90 sec – after brushing
Cellulose/Vertrel XF after grinding
Pressed and cleaned
- Universal!
- Easy!
- Fast!
- Low Cost/Sample
XRF Analysis (Cement)
Precision versus Accuracy
prepared as pressed powders
XRF Analysis (Slag)
Precision: 10 samples from “same”
Best counting statistics due to high signal!
- Fast measurement
- Ideal for process control
Good precision!
- Ideal for process control
Tricky Samples Salt
Tricky Samples Car Catalysts
Tricky Samples PetCoke – EDXRF: 210 sec!
Application precision (preparation n=10)
S +/- 0.07 %
V +/- 35 ppm
Ni +/- 5 ppm
Tricky Samples Low F in Cement
- Low dilution best for traces!
- No loss of volatile elements
- Works on coals, catalysts, salts.
- Precious metals or crucible toxins can be prepared
Automate Your Preparation Integrated Mill and Press
Automation: Unattended Analysis Drop and Go!
- Easy, compact automation!
- Completely unattended operation
- Belt driven
- Rugged and proven
Pressed pellets work great!
When to use the pressed pellet preparation?
- Reference material is available with same matrix and mineralogy
- Secondary reference materials from same location (quarry)
- “Acceptable” bias from non-mineralogical references
- Reference (standards) and sample can be ground fine enough to be “homogeneous” for the analyzed layer
- Fineness of standards can be matched to unknowns
- Speed is of importance (>5 minutes)
- Low cost/sample
- Ease of use / ease of training (operator skill)
- Potential automation capabilities (unattended preparation)
- Tricky samples
- Trace elements are of interest
The Other Way?
- What if there are no matrix-matched standards available or none at all?
- What if there are no mineralogical matched samples?
- Bad sample homogeneity in pellets
- Higher accuracy needed
- Larger “calibration ranges” needed for materials and flexibility
- Traceable analysis to International Reference Materials
- “Defendable” analysis
Fusion solves all of these problems !
Benefits of Borate Fusion Method of Sample Preparation for XRF Analysis
Definition of Terms Accuracy and Precision
Precision:
closeness or agreement among replicate results
Accuracy:
the nearness of a result to the “true result”
Accuracy vs. Precision
Basics of XRF Spectrometry
- XRF is a comparative technique
- The signal intensity generated by an element of the specimen must be compared with that in a standard of known composition in order to determine the concentration of the element
- The signal of an element is proportional to its concentration in the specimen
- Interference, absorption and enhancement, grain size and mineralogy change the measured signal intensity of the element
The Golden Rule for Accuracy with XRF
Since the highest accuracy in XRF is achieved by comparing unknowns with standards, the standards and unknowns must be as similar as possible in mineralogy, particle size, particle homogeneity and matrix characteristics.
Definitions Quantification
In XRF quantification is based on :
Ci = Ki . Ii . Mi . S
where Ci = weight fraction of element ‘i’, i.e. Ci = C%/100
Ki = the calibration constant for element ‘i’ (%/kcps)
Ii = net peak intensity for analyte element ‘i’ (kcps)
Mi = matrix correction term for element ‘i’
[∑n(µn Cn)] or [1 + ∑j(αij Cj)]
S = specimen preparation term, equal to Ss/SStd
Definitions: Quantification When does S = 1?
When can we eliminate the sample preparation term?
- Standards and samples are MATRIX MATCHED
- Standards and samples are “grain” SIZE MATCHED
- Analyzed layer same for standards and samples
When standards and samples are prepared the “SAME” way
Only then can the relationship be expressed as
Ci = Ki. Ii. Mi
If the specimen is poorly prepared, NO amount of correction can improve the quality of the analytical result.
Basics of XRF Spectrometry
- There is no substitute for good sample preparation
- If the sample specimen is poorly prepared NO AMOUNT OF CORRECTION can improve the analytical result
- If S≠1, your results are not accurate
- Time and resources should be devoted to sample preparation to benefit fully from an XRF spectrometer
Pressed Powder Method of XRF Sample Preparation
Advantages
- Speed
- Inexpensive
- Easy to learn/execute
- Highest count rate (precision)
- Lowest limit of detection
Disadvantages
- Particle size effects
- Surface roughness
- Homogeneity effects
- Matrix matching problems
- Mineralogical effect (accuracy problems)
Problems with Pressed Pellet and Powder Techniques
Particle Size Effect Pressed Powders for XRF
- Grinding of different mineralogical phases and compositions produces particles of different sizes and shapes
- The particular shape and size of a particle influence its reaction to an applied pressure
- The surface flatness is also affected by the particle size and shape distribution
- A pressed pellet is not a homogenous specimen
Particle Size Effect Pressed Powders for XRF
- The analyzed layer thickness is affected by the particle size and shape distribution (density)
- The particle’s size, shape and the effect on flatness cannot be predicted and will vary with the type of matrix
- Since the signal only comes from a few atomic layers, it is not always representative of the whole specimen
Particle Size Effect Pressed Powders for XRF
Comparison of analyses of two aliquots of the same sample milled to different particle sizes
- Removes particle size effect
- Removes roughness effect
Mineralogical Effect on Fe Intensities Using Pressed Pellets
Typical Fe line intensities for Fe when present in same concentration, in same size particles, but as different minerals in a sample.
Pressed Powder Technique Mineralogical Effect on Raw Mix
Eliminate the Mineralogical Effect From the Crystal Structure to
Eliminate the Mineralogical Effect To a Glassy Matrix
Fusion for XRF
Accuracy of Fusion – Comparison of Pressed Pellets to Fused Beads
SiO2 in Raw Mix
- Before Fusion
- After Fusion
- After Fusion and Corrections
- Removes mineralogical effect for highest accuracy by XRF
- Allows for application of matrix corrections where previously not applicable
- Allows selection of unmatched matrix standards
- Allows creation of synthetic standards
What is Fusion ?
Typical Fusion Procedure
Fusion Steps
Fusion Bead Examples
- Soils
- Clays/Geological
- Catalysts
- Glass
- Ores
- What about the volatiles in the sample?
- For example: S, Cl, F, Br?
- What about ores, such as sulfide ores or sulfide minerals?
Sulfide ores as well
It can be fused too
Automated Fusion Machine Claisse “M4” Fluxer
Claisse “rFusion” Modular Automation
The Other Way? Knockout Punch!
- What if there are no matrix matched standards available or none at all –
This is the case most of the time - What if there are no mineralogical matched samples –
You won’t even know when this happens - “Defendable analysis” –
NOW you know the samples and standards weren’t matrix matched! - Bad sample homogeneity in pellets –
Happens often in spite of lengthy grinding - Higher accuracy needed –
This is why you bought and paid so much money for an XRF spectrometer in the first place - Larger “calibration ranges” needed for materials and flexibility –
This happens when your process goes out of control - Traceable analysis to International Reference Materials –
Is the norm in today’s ISO/ROHS/WEEE driven world. see “defendable analysis” - Eliminates particle size effects
- Eliminates mineralogical effects
- Eliminates roughness effects
- Provides excellent homogeneity and flatness
- Creates perfectly matrix matched standards and unknowns
- Allows for matrix corrections where previously not possible
- Provides highest accuracy
- Provides defendable analysis (without worry)
- Provides high precision
- Provides universal calibration capability
- Allows for use of matrix-unmatched standards
- Allows for creation of synthetic standards
- Allows for traceable analysis to International Reference Materials
- Easy to use – unattended operation
- Automation ready
Comparison – Pressed Powder vs Fused Beads
https://www.bruker.com/fileadmin/user_upload/8-PDF-Docs/X-rayDiffraction_ElementalAnalysis/XRF/Webinars/Bruker_AXS_Industrial_Minerals_EDXRF_Webinar.pdf
How to Prepare XRF Fusion Disk
The sample is placed directly into the crucible, on the scale to be weighed. The flux is added to the sample. A lithium-borate flux is used because it is better suited to slag samples.
The sample and flux are mixed to accelerate the fusion process. A non-wetting agent is added to allow the glass disks to be easily removed from the platinum molds. Alkaline bromides or iodides are the non-wetting agents normally used in fusion. We also offer fluxes with non-wetting agents integrated.
The crucibles and molds are placed on the Fluxer. The burners are ignited and crucibles heated at a simple touch of a button. Agitation, speed and temperature progressively increase until all the flux has melted. The sample then dissolves into the molten flux. Fusion does not consist of heating the flux and samples to the sample’s melting temperature, but rather to having the oxidized sample dissolve into the flux. Therefore, the temperature required for preparing all samples should be limited to the melting temperature of the flux. If the temperature in the crucible exceeds 11,000 degrees Celsius, there is a risk of losing volatile sample elements, the non-wetting agent and even the flux. It is best to prepare the sample at a lower temperature to avoid losing any material, thus ensuring high analytical accuracy.
When the melt is ready, the molds are raised into the flame to prepare for casting. The arm holding the crucibles quickly rotates to pour the contents of the crucibles into the molds. The molds are left at room temperature for a few seconds before fans are activated to cool the melt. The fusion cycle lasts approximately 15 minutes. The three glass disks are now ready for XRF analysis.
The new standard in sample preparation by Fusion. The Fluxer allows the preparation of a wide variety of samples by Fusion for XRF analysis with one button operation. Because of its versatility, the fusion machine can perform fusions for cement, silica, slags, lime, catalysts, feral alloys, pure metals, refractory materials, mining samples and other samples as well. Automatic ignition, agitation by rotation, no oxygen and compressed air needed for operation, stable and oxidizing flame at both high and low temperatures. This 3-position fluxion provides great repeatability and retention of volatile elements.
It can also be controlled by computer for efficient development of fusion procedures. The operations you have just seen can be performed with equal ease to prepare solutions for analysis by atomic absorption, AA, or by inductively coupled plasma – ICP. In glass disks mode or in solution mode, the Fluxer astonishes with its ease of operation, versatility and repeatability.
The Benefits and Basics of Sample Preparation by Fusion
The first part of this presentation will be an introduction on the benefits of Fusion for both ICP and XRF analysis. This will be followed by the review of the key factors that should be taken into consideration to be successful in our sample preparation by Fusion.
Let’s start by talking about sample preparation for XRF analysis. Depending on the state of the sample, whether it is liquid or solid, as well as on the requested degree of precision and accuracy, there are many different ways to prepare these samples. In this presentation we will focus on the preparation of solid samples such as minerals, concentrate, ashes or on the preparation of manufacturing materials such as cement, catalysts and many others. We will compare the two following preparation methods: pressed pellet and fusion. As illustrated in the figure, these samples need to be previously grounded for all those three preparation methods: loose powder, pressed pellet and fusion.
Now, what do you need to prepare your samples by fusion? Here is the most commonly requested equipment. To start, you need know the reagent in which the sample will be dissolved. Depending on the application, you might need other chemicals called additives such as oxidizers, non-weighting agents, fluidizer or internal standards. You will also need platinum ware. A few different alloys can be used, but the most common is the 95% platinum, 5% gold which is well-known for its durability and stability. It is also not wet by the molten mixture during the fusion process. And automated fusion instruments should be used in order to enhance your safety and higher productivity. This instrument can be heated by gas and electricity.
Some will offer resistance heating fusion instruments which can prepare one sample at a time. Some Fusion machine can be used to prepare 2 samples at a time and the Deluxe Fusion Instrument which can prepare up to 6 samples at a time for higher productivity. There is also fusion instruments which is heated by gas, liquid petroleum or a natural gas. It can prepare 3 samples at a time.
There are also many ways to prepare your sample for ICP analysis. Let’s divide them in two categories: the first category is acid digestion that include hot plate acid digestion, block digestion, bomb acid and finally microwave. These techniques use strong acid like nitric acid or hydrofluoric acid. The second category is sample preparation by Fusion. Either lithium-borate fusion or peroxide fusion. These techniques allow you to dissolve metals and other non-oxide sample quickly and rapidly. You can then get rocks, catalysts, serum mix, line products and many more in solution without HF or other strong acids.
The only change regarding equipment when comparing borate solution with sample preparation for XRF is that you change the platinum mold for a Teflon beaker. For peroxide fusion, you need sodium peroxide which is the most common solvent used for this application. But sodium carbonate can also be used for some applications. The crucibles that are the most recently used are made of zirconium or nickel. As for the two previous methods it is possible to use gas or electric fusion instruments. Also, we offer the peroxide fluxer instrument which is powered by gas and fully dedicated to peroxide fusion.
Sample preparation by fusion is a very simple technique. If you want to do a borate fusion, you must weight your sample in the 95% platinum, 5% gold crucible in which you also add the borate flux. The borate flux can be a lithium borate, a lithium metal borate or a mixture of both. Also, you might need to add an additive such as a non-wetting agent or an oxidizer. You heat up this mixture to melt the borate flux and add the sample dissolved into it. Note that only oxide samples can be dissolved into the borate flux. However, any sample can be oxidized using an oxidizer or an oxidizing technique.
Now, once your sample is dissolved into the molten borate flux you have two options: you either pour the mixture into the platinum gold casting mold or into a diluted acid solution. For peroxide fusion, once the sample has reacted with the peroxide in the zirconium or nickel crucible, the mixture is dissolved using ultra-pure water. Diluted acid is then added volumetrically to get the same acid concentration as used on the ICP.
Now, let’s talk about the benefits of using sample preparation by Fusion for XRF analysis. This sentence summarizes and clearly identifies what are the requirements for high-accuracy results. In fact, as mentioned in this article, XRF is a comparative technique and the closer the standards used to prepare the calibration are to the minerality particles homogenate, particles size and matrix characteristics of the unknown, the more accurate the analysis will be.
Having said that, we have to keep in mind that the standards used when preparing XRF calibration should be similar to the unknown samples that need to be analyzed. When preparing natural samples such as minerals, clay, ore geology, soil, it is practically impossible to know if the standards and unknown will be matrix matched. It is also the case with other products that can be mixed together with natural samples such as blended cement, polymers with different additives, catalyst, electronic and composite materials. Fusion is the solution to this issue and we’ll prove it in the next slide.
If we were to look at a graphic to demonstrates the mineralogical effect. We can see here how the XRF intensities are affected by the different mineralogy of iron. Also a natural material, the composition of mineral deposits varies from one location to another. There are also substitutions of various elements as contaminants in the crystal structures. Consequently it is almost impossible to closely imagine a matrix of standard to unknown using this technique, therefore highly accurate analyzers at high concentration level are difficult or simply impossible to obtain for many natural materials.
Now, if we look closely at the pressed pellet surface, that’s what we see: roughness and inhomogeneity of the specimen. The grinding of different mineralogical phases and composition produces particles that have different sizes and shapes. And which will react differently when the pressure is applied to produce the pellet. This probably leads to segregation of different materials of the sample with different density distribution. This will affect the penetration depth of the X-ray for a given wavelength of interest. This illustration shows that the effective layer is not homogenous and not representative of the overall sample composition.
Sample preparation by Fusion is the perfect method to eliminate these mineralogical and particle-size effects. The first pellet contains different crystal structures, however as illustrated here while the components to be analyzed are homogenously distributed in the glassy matrix. Using fusion makes the calibration easier. The particle size and minerology effects lead to calibration spread and to poor accuracy if you compare the fused glass disk. As a matter of fact, the calibration is no longer limited. It can be applied to a larger end of composition. A calibration can also be made with synthetic standards and it allows the application of matrix correction where it was previously not applicable.
You can see here calibrations made by pressed pellets and by fusion for 3 different production sample types which are A, B and C. We see that with pressed pellets you will need 3 different calibration curves in order to fit with all the mineralogical effects for the 3 different samples which contains the same component here: silicone dioxide. With fusion, a second calibration curve is needed, thus reducing time to calibrate and lowering the costs.
A table could summarize the benefits of sample preparation by fusion compared to pressed pellet. As we discussed, using fusion eliminates the particle side and mineralogical effect. It leads to the following benefits: less grinding prior to sample preparation, increased accuracy, possibility of using synthetic standards for calibration, a wider calibration range and application of matrix correction. It is important to know that within a webinar timeframe we mainly discuss the concept of XRF analysis. If you wish to have more information on these concepts, you can register to workshops offered by your XRF supplier or other organizations in your local area.
We will now cover the benefits of using the sample preparation by Fusion for ICP analysis. We will start with peroxide fusion. We will show you a quick video of how to perform such method. First of all, in a zirconium or nickel crucible you weigh the sodium peroxide or carbonate that will be used to oxidize your sample. Then you add your sample in the crucible. Place your crucible on the sample preparation equipment as you can see in the video that shows a peroxide fusion instrument. You heat up the mixture at a temperature of approximate 500 Celsius degrees to let the sample react with the peroxide. You let the mixture cool down when the reaction is completed. Once everything is cool, you either put the crucible into ultra-pure water, or rinse it over a funnel with the water used to rinse the crucible with the sample so everything gets transferred into a volumetric glass. Finally, you add just the volume so you get the exact dilution you are looking for.
You can notice that even though there’s a manual dissolution step, the fact that the fusion itself takes only 5 minutes still makes it with a very fast turnaround. You can count about 10 minutes from the start to the end where the sample is fully dissolved. The manual dissolution step can be processed as batches for saving even more time. This is very simple and doesn’t require any strong acids such as perchloric acid or hydrofluoric acid. The waste management is then facilitated and fusion is a clean method to prepare your sample. The heat needed to have the peroxide react with the sample is controlled by the instrument in a very fashionable and reputable way, making it stable and safe. Also, peroxide fusion is performed in a zirconium or nickel crucible which are rather cheap compared to platinum.
Now, when you use borate fusion as a sample preparation method for ICP analyzers you simply mix the borate flux – 2-3 grams usually – the sample and any additives such as an oxidizer or a non-wetting agent, all within the platinum-gold crucible. Place the crucible on the fusion instrument. Instead of pouring the fuse melt into a platinum disk as seen in the sample preparation for XRF, the fused melt is automatically poured into a diluted acid. And the agitation is automatically started. Once the sample is completely diluted, transfer into a volumetric flask and add just the final volume and acid concentration needed.
One of the great advantages of using borate fusion and peroxide fusion is that you don’t have to use strong acids such as perchloric, nitric, or fluoric acids. There is no need to heat strong acids for a long period of time in your lab. With borate fusion you can dissolve any samples within a few minutes using diluted acids. The borate fusion method is very simple. You only need a borate flux sample and, if needed, an oxidizer.
There’s also other benefits of using borate fusion. Since it’s automatic, there’s no need for supervision during the process. Technicians can then perform other tasks. Remember that this method allows you to dissolve your sample within 10-12 minutes. We can then say it’s emitted with a very quick turnaround leading to low labor cost. In addition, the fact that all labware needed for preparation by borate fusion can be reused or recycled, it gives you a fast return on your investment. Temperature, speed of agitation and the duration of the fusion being automated makes it very user-friendly and safe. Heat being distributed evenly from one sample to the other, the methods are predictable and gives you repeatable results. Once again, only diluted perchloric or nitric acid is used. There is no use of hydrofluoric acid and perchloric acid to deal with, therefore no larger waste quantities of acid.
Boric fusion dissolve even the most refractory samples such as chromite, silica, zircon and titanium oxide within those 12 minutes which makes it versatile and rapid. Finally, as a mean of summarizing all of this, we have selected a key feature and decided to compare boride and peroxide fusion with acid digestion methods. Taking into account that industries are usually motivated by profitability and quality, here is how we categorize both fusion technique. Fast throughput, low labor cost, low waste production, high analytical capabilities, ease of use, complete dissolution. That, even though the initial cost may be higher in the beginning, the real cost in the long run is often lower than all acid digestion techniques.
Now that you know how sample preparation by fusion be beneficial to your laboratory, let’s discuss about the 8 factors to consider if you want to perform successful sample preparation by Fusion. These factors are sample isolation, the borate flux choice, flux/sample ratio, the particle size, the fusion temperature, the quality of the platinum-ware surface, the cooling rate and other special keys for ICP analysis. As mentioned at the beginning of this presentation, all the oxides dissolve in the molten lithium-borate flux. However, semi-oxidized samples or non-oxidized samples can also be prepared by fusion. They only require proper oxidation steps prior to fusion. The fastest and easiest way to perform this oxidation is to do it directly on the fusion instrument. The most commonly used oxidizers for the solid dry oxidation on the Fluxer are lithium, sodium and ammonium nitrate. Carbonates and other oxidizers can also be used.
The key to perform the solid dry oxidation on the fusion instrument is to control the fusion temperature and agitation at the beginning of the fusion program. As a matter of fact, we have to first melt the oxidizer which will oxidize the sample. This step is performed at a lower temperature than the requested temperature used for the fusion process. If the fusion temperature is too high, the oxidizer can volatilize or decompose before the end of the oxidation reaction. By the way, the oxidation is a very important step because in addition to not being dissolved in the borate flux, a not fully oxidized sample could react with the platinum-ware and cause its deterioration. You really want the samples to be fully oxidized for the fusion process.
Like any analytical chemistry method, you need to select the best dissolvent for your analyzer in order to have the highest possible concentration of sample in your solution. The lithium-borate flux acidity is the best flux for your borate fusion method. From a few common elements being analyzed, we see each element has its own dissolution ratio based on the flux type. An element with a low oxygen content such as calcium oxide, magnesium oxide where there’s one oxygen per element will get the higher and better the solution in a flux mainly composed of lithium-tetraboride. On the other hand, an element with a higher ratio of oxygen such as silicone dioxide, aluminum oxide, where there’s more oxygen than the element will get a better dissolution in a flux mainly composed of lithium metaborate. However, if you are looking for universal solution for many different sample, then a 50/50 mix of lithium tetraborane, lithium metaborate is probably the best option. However, you may have to decrease the amount of simple diluted per amount of flux. It means that if you go for something universal you will probably have to reduce the sample flux ratio.
An example illustrates the importance of choosing the right flux. In this light, you can see a borate fusion made with iron oxide. In each of the 3 disks we used the same amount of sample and same method. The only thing that changed is the type of flux. In the first disk on the top we made a fusion using only lithium tetraborane. You can see we have a pane of disk with bubbles and vectors showing different oxidation state of the sample. In the middle we have used a mixture of 50% lithium tetraborane and 50% lithium metaborate. We have obtained a clean disk without any imperfection. Finally, at the bottom, the iron sample was fused with pure lithium metaborate. You can clearly see the disk is impossible to analyze since it has crystalized. Keep in mind that the proper flux will give you the best result as for the solution.
In this second example we repeat the second experiment but using a sample made of pure calcium oxide. Once again the only thing that has changed is the type of flux. In the first disk on the left, we use lithium tetraborane to fuse the sample. You can see that we have obtained a perfect disk that is ready to be analyzed. In the middle, we have used a mixture of 50% tetraborane, 50% lithium metaborate. We obtained a disk that is cracked and that is shows some undissolved particle leading to partial crystallization. This disk can’t be used for analytical purposes. Finally, on the right, the calcium sample was fused with pure lithium metaborate. You can clearly see that the disk has crystalized. It is impossible to analyze it. So you can see that the right flux to dissolve an iron or a calcium sample isn’t the same. In an ideal world, each sample type will have its own flux to obtain the best possible results regarding the dissolution of the sample. This principle also applies to borate fusion for solution; if your sample isn’t dissolving in your flux before you pour it into the diluted acid, then you won’t get a complete dissolution.
The flux to sample ratio is also an important factor to take into consideration during the borate fusion procedure. You can see here an example with aluminum. When we changed the sample to flux ratio and we keep all the other factors identical, we can see that we don’t obtain a homogenous glass disk when going from one gram of samples to two gram of sample which is over the aluminum oxide solubility in the 50/50 lithium tetraborane into metaborate flux. As expected, the quantity of undissolved particles is even larger when using 3 gram of sample in the same quantity of borate flux.
As we can see in this example, the particle size of the sample also has an impact on its solubility into the flux. By keeping all the other factors identical, like the flux type, flux to sample ratio, the fusion temperature and all the others, we can see here that for the same sample just by decreasing the particle phase we have been able to obtain a homogenous glass disk without undissolved particles.
It is very important to understand that melting and dissolving are two different phenomena. In fusion, you must melt the flux in order to dissolve the sample into it. So the temperature of the fusion process has to be high enough to melt the flux, but not the sample. Usually a temperature around 1000 degrees Celsius is enough. Repeatability is also a key to success for any analytical method. More important than the temperature used for your fusion shall give you precise and repeatable temperature control fusion after fusion. You also have to keep in mind the analytes when you are selecting your fusion temperature. High temperature may make you lose more volatile elements and it will quickly deteriorate your platinum-ware.
The quality of the platinum-ware surface also has an impact on the final dissolution and then analytical results. If the internal surface of the platinum crucible is tarnished or damaged, the molten mixture will stick on its sides. The consequences will be less melt homogenate and an incomplete transfer of the molten mixture from the crucible to the mold or the Teflon beaker. In case of sample preparation for XRF, it is important to remember that the perfect mirror image of the final glass disk surface. Any scratches, dents, holes convexity of bumps on the mold surface will appear on the glass disk surface. It will influence the distance travelled by the X-ray and affect the elemental intensities. Also, tarnished or scratched molds will decrease then increase the tendency of the glass disk to stick to the mold surface. This could lead to cracked disks.
It is also possible that you may need to use a non-wetting agent in your fusion mixture, depending on the application. The non-wetting agents which are usually alloys, create the tendency to stick to platinumware. The most common non-wetting agents are lithium bromate or lithium iodate.
In order to obtain a stable glass disk, your cooling step must be well controlled. Remember than when preparing a sample by borate fusion for XRF application, the temperature of the lithium-borate mold with your simple dissolve into it is around 1000-1100 Celsius degrees. You cast it then into a preheated platinum-gold mold and you cool it down. If you cool it too rapidly, you will enter stress in the glass, thus making it crack into the mold. On the other end, if you cool it too slowly, you will allow the molecules to reorganize in their lowest energy state which is crystal, so you will get a crystalized disk. The appropriate cooling step of the glass disk is somewhere in-between too fast and too slow. Ideally you should start to cool the sample slowly, then increase the cooling rate gradually.
When running a sample prepared by fusion on an ICP, a few tricks may help you ease your analytical process. Un an ICP OES, it is best to keep the TDS under 1% and below 0.2% for an ICPMS. So appropriate dilution may be necessary. In order to avoid deposit on the ICP torch, reduce the sample resin in the plasma and use high-energy glass flow. Also, decreasing the sample flow rate will allow to decrease the amount of salt in the ICP chamber. By experimenting in our lab we found that the two best components to use are a cyclonic spray chamber and a Meinhardt nebulizer.
Please bring your attention to the fact that sample preparation by fusion is a fast and reliable method for both ICP and XRF. The equipment used for fusion is sample and the automation of the process leads to repeatable results. It also allows you to prepare a wide range of samples with a single method and ease up the preparation of your calibration curves since metric and mineralogical effect are not taken into account.
You can expect a quick return on investment, since fusion makes the analytical process in your lab easier and because it facilitates the sample preparation and calibration. Ok, this finished the presentation. We have now only a few minutes left to answer your questions. You can still use the chat box located at the left of the screen to submit your questions.
I recently obtained a cracked disk with chromium oxide samples. How can I solve this?
So if all the other factors are the same, which means same flux, same particle size, cooling rate and you’re just having this problem the first thing to check is the quality of the mold surface, especially because chromium has a high tendency to stick to the platinumware, so it will be more easily be affected by scratched mold, depending on how the mold is damaged, it can be replenished or replaced. Also you could look at the glass fragment and try to see if there is any undissolved particles in this. The undissolved particles also lead to cracked disks, and if the crucibles you use are tarnished as explained in the presentation, it means that the molten mixture might stick to it and this will affect the melt homogeneity and the dissolution that could explain the cracked disks. So the platinumware would be the first thing to check.
When preparing borate solution, do you directly pour the hot borate melt into the diluted acid solution?
Yes, in fact yes we do. The important thing to know is that when you do borate fusion for ICP solution, we only use 2-3 gram of borate flux maximum. This way the heat transfer and the heat shock when you pour your melt into the solution isn’t big, and also it’s important that your diluted acid solution is stirring, so there’s an agitation when you pour so this will reduce the heat transfer and also help to accelerate the dissolution after.