Table of Contents
Size reduction is the most expensive operation in most mills. Crushing and grinding usually require the greatest portion of capital costs and often make up 60-70 percent of total mill operating costs as shown in Figure 1. Selection of the proper crushing and grinding method must, therefore, be done with great care to be sure that the best circuit is chosen.
Autogenous grinding is favored when the ore is quite competent and a fine grind is required. Semi-autogenous grinding is applied when fine crushing could cause severe problems or when ore is variable in hardness or competency.
Figure 2 shows a typical conventional crushing-grinding circuit with three stages of crushing followed by ball mills or rod mill-ball mill combination. This flowsheet is typical of many mills that have been built throughout the world. Figure 3 shows a typical semi-autogenous (SAG) circuit with feed coming directly from a primary crusher, and the semi-autogenous mill product going to the separation process. Many similar semiautogenous circuits are built today because they are simple and flexible, lend themselves readily to high tonnages and usually are lower in capital cost and lower in operating cost. With some ores, it is possible to send mine-run ore directly to the semiautogenous mill so that the primary crusher can be eliminated.
An autogenous or semiautogenous circuit, as the name implies, uses the ore itself to assist in the grinding process. In this type of circuit, the ore must be competent so large chunks of ore can be used to grind smaller chunks of ore.
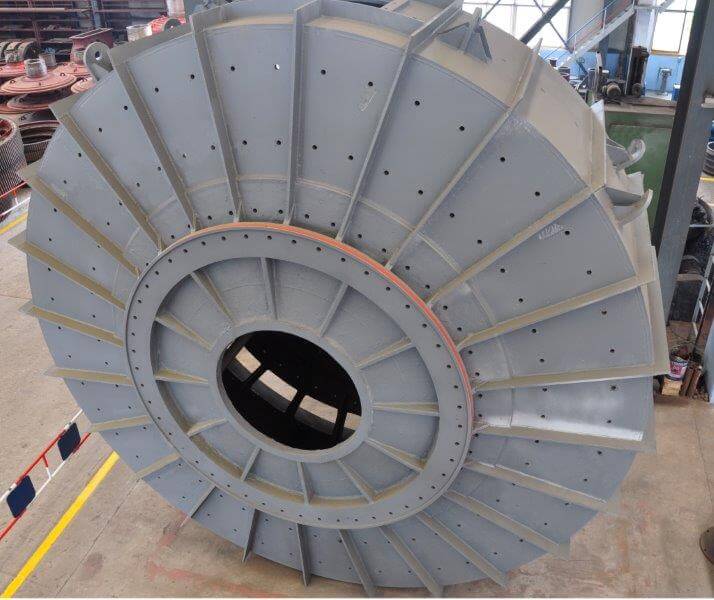
If ore alone is used then the circuit is autogenous but if balls are added to supplement the charge, then the circuit is termed semiautogenous . Ore competency is not always a binding criterion to break up large pieces and wash away cementing material. Autogenous and semi-autogenous mills have been very successful on relatively soft uranium ores where the values are frequently found in the material that cements the sandstone grains together.
Autogenous Grinding Circuits
When an ore is hard and competent, there is always the possibility that it would make good “pebbles” which could be used for fine grinding media. Different methods that have been tried using combinations of autogenous, semi-autogenous, pebble and/or ball mills. The flowsheets shown are typical of the properties listed but a specific property may be using a slight modification of the method depicted.
- Autogenous-single stage, has not had wide acceptance because it requires a very competent ore that must be ground to a relatively fine size. An autogenous circuit is difficult to control final grind.
- Autogenous plus crusher. This circuit was difficult to control and resulted in low tonnage.
- ABC closed circuit, Autogenous-Ball-Mill-Crusher. Another similar technique is the ABC open circuit where the crusher product feeds the ball mill rather than the autogenous mill. Crusher product is typical feed to a ball mill using large diameter balls but not much grinding of 20-25 mm ore can be accomplished in an autogenous mill.
- Autogenous plus Pebble Mill are an excellent technique if the ore is uniformly hard and competent but it has not been popular because the porphry copper orebodies do not consistently produce sufficient hard, competent pebbles for the secondary grind.
- Autogenous plus Ball Mill has been used very infrequently. When hard ores are encountered for extensive periods, 100 mm balls are added to the primary mill (#7).
- Semiautogenous-single stage. These circuits are not a good choice for many orebodies because it is not logical to expect one machine to be as efficient on 150 mm ore as it is on 100 micron ore.
- Semi-autogenous plus ball mill has been the “work horse” of mills.
SAG vs Ball Mill Advantages
AG & SAG Mill Grinding Compared – Which is Best
Grinding rods and balls can be obtained in uniform sizes, weights and of a specified quality. Their action in a mill can be reasonably predicted.
In autogenous and semi-autogenous grinding, where all or most of the grinding media is also the material to be ground, those fixed conditions do not exist, so the media itself becomes a variable that must be evaluated.
The first question that we at Allis-Chalmers ask about the feasible application of primary autogenous or semi-autogenous grinding mills concerns the quantity and the competency to be media of media-sized ore in the feed. These are the first factors to be appraised, since if there is not enough media-sized ore and/or if the media-sized ore will not perform as media in an autogenous or semi-autogenous mill, autogonous grinding probably would not be feasible.
To study the competency of ore as media, Allis-Chalmers developed a test procedure and a device in which to run the test, which were described in 1963. The test charge consists of ten pieces of dry ore in each ½” size fraction, weighed, beginning with 6-½” x 6″- ending with 4-½” x 4″. This total of fifty pieces of ore are put into a 6′ x 1′ closed drum tester as shown in Figure 1. The tester is then run for 500 revolutions after which it is emptied. The number of survivors in each ½” size fraction down to 2-½” x 2″ are counted and weighed. A screen analysis down to 3 mesh is also made. Bond Impact, grindability tests, and abrasion index tests are also run on the sample. Rod mill grindability tests for Work Index are run at 10 or 14 mesh, and ball mill Work Index tests are run at the desired grind if finer than 28 mesh. All the data obtained is evaluated and one or more of the following recommendations made:
- The ore makes good autogenous media and pilot plant testing should be carried out, since the possibilities for autogenous grinding are very good.
- Ore makes questionable media; however, if economics, location, costs or other factors justify further study, pilot plant autogenous and/or semi-autogenous pilot plant tests should be run to further explore the possibility for this type of grinding.
- Media competency is marginal and the possibility for “critical size” buildup exists; however, ore structure is such that semi-autogenous grinding appears to be a good possibility and pilot plant testing of semi-autogenous grinding is warranted.
- Further testing is not warranted. Conventional crushing and grinding should be used.
a. Media size fraction does not make any good media which would survive as media in a mill.
b. This recommendation might also apply to non-abrasive ores which, while making good media, would show that there would be very little savings, if any, in operating costs by using autogenous grinding. - Media size fraction does not make good media but the ore is a conglomerate that breaks readily to the natural grain size. Further pilot plant testing is warranted.
To date, Allis-Chalmers has not made a recommendation to use primary autogenous or semi-autogenous mills based upon media competency test results alone. The most frequent recommendation, based on tests made to date, has been to proceed to pilot plant testing.
A media competency test for secondary autogenous (pebble) milling has also been developed to evaluate the media for secondary autogenous milling.
Testing for Product Size
Professor Marcus Digre in his book on autogenous grinding discusses grinding action in autogenous mills as different from the action in rod and ball mills. He confirms the observation that in autogenous grinding the breakage is principally along grain boundaries and around hard size fractions with little trans-granular breakage. In autogenous grinding, there appears to be more abrasion or attrition grinding and less impact grinding than in rod and ball milling.
Many of the early autogenous grinding installations in the United States and Canada were used to grind iron ores. Generally the results showed the final product contained less fines (the screen analysis as plotted on log-log paper had a steeper slope) than the products from circuits using more conventional media. This led to the statement that autogenous grinding produces less extreme fines than conventional grinding.
More and more autogenous grinding installations have been made for non-ferrous ores, particularly low grade copper ores. These ores usually do not have well-defined grain structure as found in many iron ores, and this statement has not proven correct. Some of these non-ferrous ores, when ground in autogenous mills, have produced an excess of fines and a greater surface area than with conventional grinding. An explanation for this could be that the production of fines is a function of the grain structure of the ore being ground.
The fact that the product from autogenous grinding is different from that produced by conventional grinding is the second major factor requiring testing, when studying the feasibility of using autogenous grinding. (There are few, if any, ores that will not grind in an autogenous mill.) The key questions are:
- (1) will the product produced be suitable for the next processing step,
- (2) will the power consumption be economical, and
- (3) what other considerations such as abrasiveness of the ore, metal wear reduction and material handling, are significant?
In conventional grinding, the size of product can be changed by changing media size, feed size, feed rate, classifier cut size, etc. The grinding circuit responds to these changes. In autogenous grinding, the ore “says” how it wants to be ground and the product size that it will produce, and does not change in response to the same factors. With some ores there are two possible products from an autogenous grinding circuit — a coarse product or a fine product. With other ores, there may only be one product. In autogenous grinding, one way to change the product size is to switch to semi-autogenous grinding which will give a coarser product than autogenous grinding and usually at less power consumption per ton. The Cleveland-Cliffs Iron Company referred to this in their paper on autogenous grinding. The Union Corporation in a paper on the reduction works at the Kinross Mine gives some data on grinding mill performance with and without grinding balls being used as supplemental media.
Pilot plant testing is required to determine how the ore wants to grind and the effect on the product size and power requirements by using autogenous and/or semi-autogenous grinding. To date it is only through continuous flow pilot plant testing that these factors can be established. In studying the breakage characteristics of the ore, the possibility of stage grinding using either secondary autogenous mills, such as used by The Cleveland-Cliffs Iron Company at the Empire and Sherman Mines and Pickands Mather at the Griffith Mine, or secondary ball mills such as used by Pickands Mather’s Savage River Mine, Cyprus Pima Mines, Island Copper, Boliden’s Aitik Mine, and Lornex, can also be investigated in a pilot plant test. Another possibility to be tested is the use of a cone crusher in the primary mill closed circuit arrangement. Crushing the coarse circulating load, which can be a critical size, as described by Pickands Mather and Newmont Mining, can also be tested in the pilot plant.
In conjunction with pilot plant testing, there should be either pilot plant facilities or at least bench scale facilities to test the suitability of the product for the next processing step. Either test facilities or data should be available to compare this with the product from a conventional grinding circuit.
McDermott, Lipovetz and Peterson of Pickands Mather in their paper “The Dollars and Sense of Autogenous Grinding” describe the testing they did to develop an autogenous grinding circuit for a taconite ore processing plant. Bassarear and Sorstokke of Cyprus Pima reviewed the test work they performed to develop their semi-autogenous ball mill grinding circuit. Many other papers on autogenous and semi-autogenous grinding also discuss the pilot plant and bench scale testing done to prove grinding circuits.
Primary Autogenous Grinding Concentrators Recent Trends and Developments
Recent developments in the design of concentration plants have reflected the increased recognition that has been given to the economic and metallurgical advantages of autogenous grinding. This has manifested itself in the increasing adoption of primary autogenous grinding in iron ore beneficiation plants in North America.
Autogenous Mill Types
There are basically three general types of autogenous grinding mills:
a. Primary autogenous mills which process directly the total discharge of primary crushers (usually set at 6″ to 10″ open side setting). Under some circumstances and for certain types of ore, small ball charges (usually less than 5% of the mill volume, but sometimes up to 10%) may be used with advantage to complement the natural rock grinding media forming inside the mills.
b. Intermediate autogenous mills (or intermediate pebble mills) which process a fine crushed product (minus 5/8″ to minus 1″) obtained from an intermediate crushing plant. The grinding media in these mills are rock pebbles of suitable size (3″ to 6″) screened out of the intermediate crushing circuit.
c. Secondary autogenous mills (or secondary pebble mills) which process a coarse ground product. (4 to 14 mesh; or, finer) obtained from rod mills or from primary or intermediate autogenous mills. Grinding media in these mills are rock pebbles of suitable size (1-½” to 3-½”) bled off from primary autogenous mills or screened out of intermediate crushing circuits.
Primary Autogenous Mills
It is interesting to note that mill configurations vary between wide limits. In South Africa wet grate discharge mills having a nominal ratio of length to diameter slightly larger than 1 (16/12 = 1. 33 and 14/12 = 1.17.
In North America, with wet primary mills, the practice has been to use low or high level grate discharge or peripheral discharge and a nominal ratio of length to diameter relatively close to 1/3. Ores ground have ranged in power requirements from 2-3 Hph/lt for an 8 – 14 mesh grind up to 20 – 30 Hph/lt for a 48 – 65 mesh grind.
Where dry grinding has been adopted, Aerofall Mills have been exclusively used. They are characterized by a length that varies little, ranging from nearly 5′ 6″ for 17′ mills and not exceeding 6′ for the largest ones. This corresponds to nominal ratios of length to diameter that decrease from around 1/3 for the smaller mills to less than ¼ for the larger mills. The grinding characteristics of the ores processed have varied from 2-3 Hph/lt for a 10 – 20 mesh grind up to 15 – 20 Hph/lt for a 65 mesh grind.
Wet Versus Dry Primary Grinding
From the standpoint of operating costs, it is to be expected that liner wear, and, where a small ball charge is used, ball wear would be higher in wet grinding than in dry grinding. On the other hand, the frequent necessity to dry the mill feed and to provide adequate dust collection would weigh against dry grinding. Moreover, it is to be expected that the cost of dry classification would be higher than for wet classification.
In most cases as matters stand today, only adequate testing and comprehensive cost and metallurgical comparisons can establish a sound and reliable basis for the determination of the most efficient and economic method of primary grinding.
As a matter of fact, there is evidence that for some types of ores, dry and wet autogenous grinding are characterized by differences that may, in certain cases, represent an essential consideration from a metallurgical standpoint. The major points of difference that seem to have been established in this respect are:
a. For fine grained ores, a finer product can be obtained in a single stage of wet primary grinding than in a dry grinding circuit.
b. Wet primary grinding has a tendency to produce more slimes than dry grinding.
c. Dry primary grinding gives the, possibility of obtaining higher grade concentrates at a coarser size than wet grinding.
d. With dry grinding, it is easier and less costly to provide for storage of the primary ground product prior to subsequent processing, in cases where it is important to do so.
e. Wet autogenous mills can have their grates fitted with slots of suitable size making it possible to set, as desired, the top size of the product discharged from the mill.
Basic Plant Flowsheet
One major characteristic of primary autogenous concentrators is the relative simplicity of their overall plant flowsheet. Where in conventional rod and ball mill plants there are usually 3 to 4 stages of crushing followed by 1 to 3 stages of grinding, depending on ore fineness and hardness, primary autogenous plants require only one stage of crushing followed by 1 to 2 stages of grinding. It is even reasonable to expect that with the development of suitable designs for primary grinding mills of increasing diameters, these mills will be able to directly process run of mine ore, suitably fragmented to keep the size of the largest pieces within reasonable limits.
As matters stand now, a primary autogenous concentration plant will consist of the following major facilities:
a. A single stage crushing plant.
b. Conveying and storage facilities for the primary crushed ore.
c. A single or two stage grinding and concentration mill. .
There is no basic difference in the design and layout of a primary crushing plant, whether it delivers ore to an autogenous or a conventional concentrator, except in the fact that in the former case it need not include more than a single stage of crushing.
With the size of ore to be handled and the capacities involved, which are usually of the order of 2000 ltph or more, primary gyratory crushers are mostly used, with mantle diameters of 7 feet or more and feed openings of 54″ or more. In these sizes, no grizzlies are required ahead of the gyratory crusher, and very compact and economic layouts can be adopted for the crushing plant, incorporating a dumping pocket above the crusher, a discharge box underneath it feeding an apron feeder which delivers the crushed ore to the primary conveyor belt. For the capacities considered, 72″ or 84″ apron feeders and 48″ to 60″ belt conveyors are usually used.
Basic Primary Grinding Flowsheets
Primary grinding mills almost always operate in closed circuit. Even when they are used for coarse grinding, the fineness of the primary ground product is seldom coarser than 8-10 mesh. The discharge of wet primary mills, as determined by the openings in their grates may contain fractions as coarse as 3/8″ to ½”, if no pebble slots are provided, and as coarse as 2-½” to 3-½” if pebbles are extracted. Consequently, trommels and vibrating screens are used on the discharge of wet primary mills to separate oversize fractions which are almost always recirculated back to the mill feed end. The screen undersize constitutes the primary circuit final product when the grind required is not finer than 10 to 14 mesh.
In coarse grinding primary circuits (10 – 14 mesh) the product of the first two collectors is screened. The screen oversize is returned to the mill and its under size, with the underflows of the third stage cyclone and dust collector constitute the primary circuit product. In fine grinding flowsheets, no screening is necessary. Depending on the fineness of grind required, both the vertical separator and intermediate collector underflows or the former only are returned to the mill.