Use of Cryogens Liquid Nitrogen to Recycle Scrap Metals
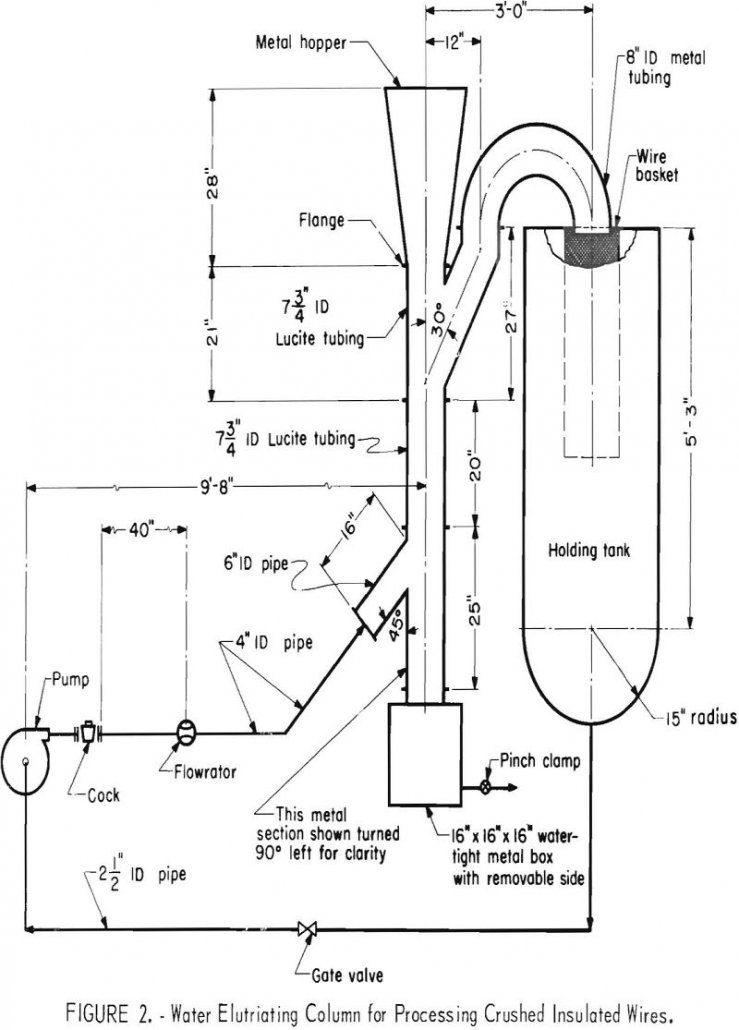
Scrap such as insulated copper wire, small motors, automobile tires, and nonferrous concentrates from automobile shredders contains materials that become brittle at low temperatures and other materials that remain malleable. Crushing of the chilled materials to shatter the embrittled portion followed by magnetic separation, screening, and/or gravity separation was studied for recovering the individual components. […]
Mica Beneficiation
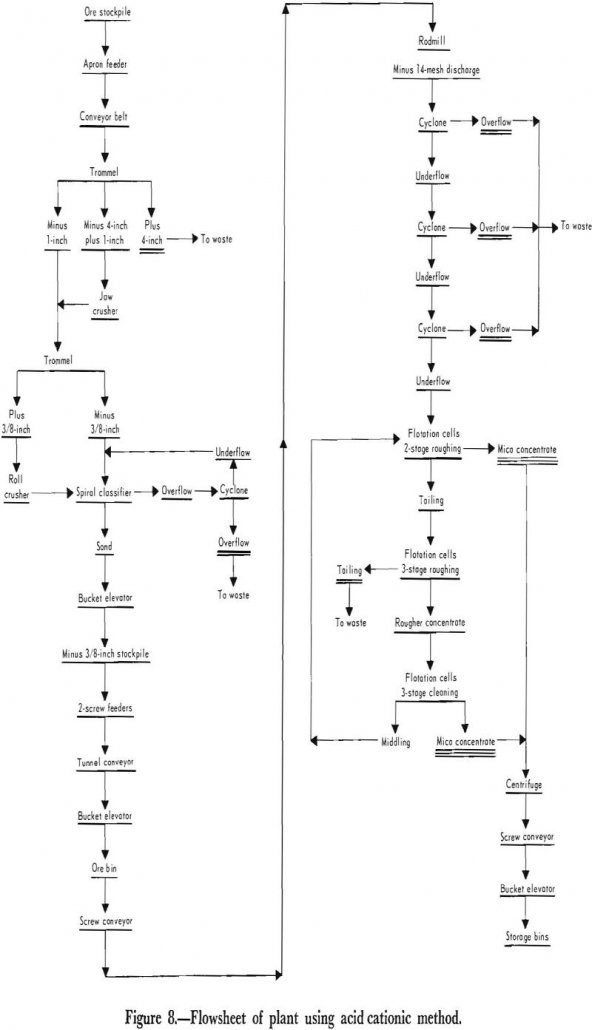
In recent years, more than 99 percent of the domestic mica produced has been scrap and flake mica (mica which does not meet specifications for sheet mica and which is used for producing fine-ground mica). There has been a continued increase in mica production for several years. The 1969 production of scrap and flake mica […]
Chlorine Leaching Copper
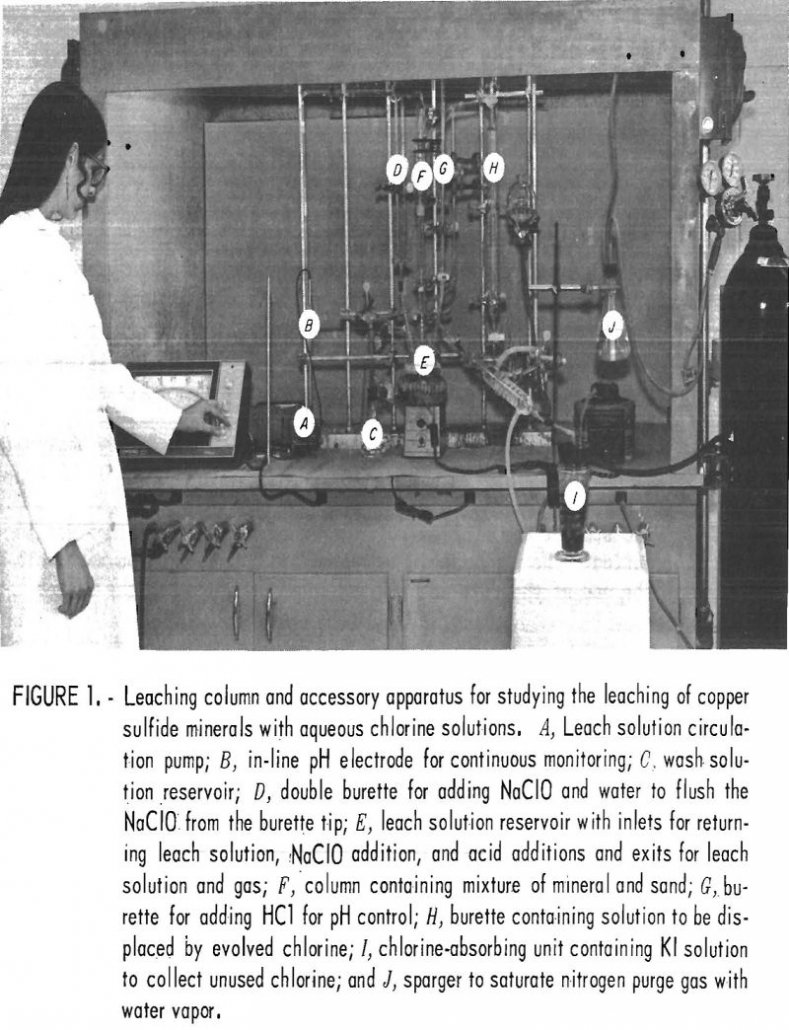
The high reactivity of chlorine as an oxidizing agent in leaching ore has long been recognized, but chlorine has not been extensively used because of high costs and because of the corrosiveness of acid chlorine solutions. As early as 1848, the use of aqueous chlorine solution was proposed for extracting values from gold ores, and […]
Rare Earth & Hydrogen Oxygen Fuel Cell
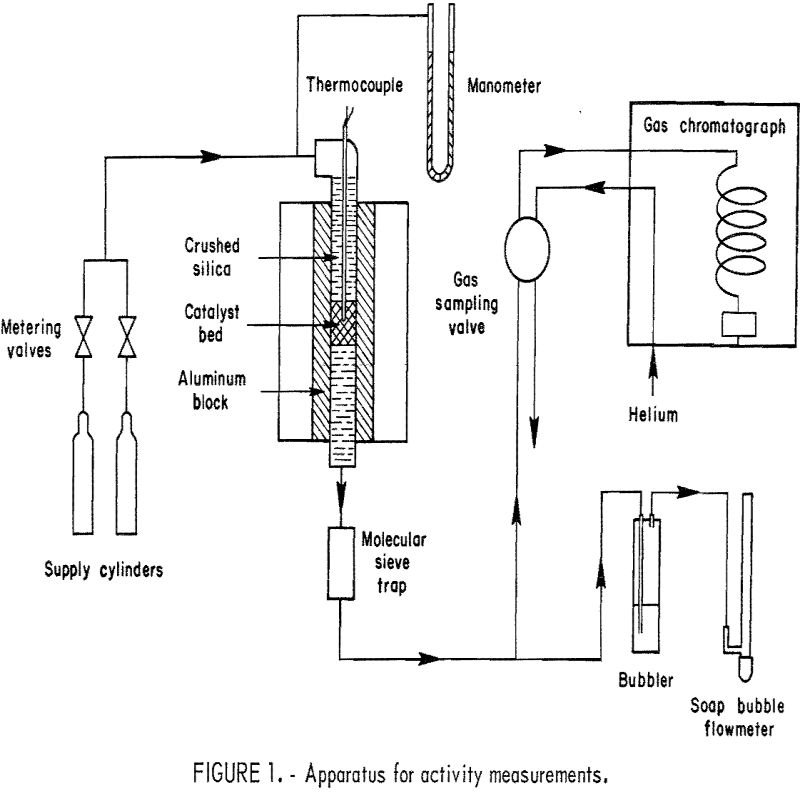
The activity of rare-earth compounds for catalysis of the hydrogen-oxygen reaction is of interest because of their possible use for electrocatalysis of the cathode reaction of a hydrogen-oxygen fuel cell. Although platinum metal has been widely used as a fuel cell catalyst, its high price and relatively limited supply prohibit its use in truly large-scale […]
Silver Barite Treatment Method
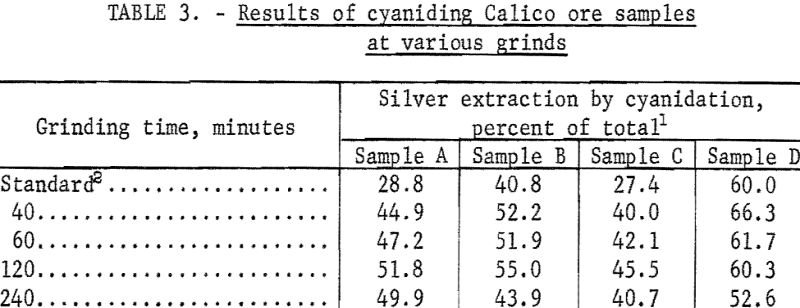
The Calico mining district in California contains extensive deposits of low-grade silver ore. The deposits cover a large area and constitute an important silver reserve if difficult concentration problems can be solved. The deposits also contain barite, which, if recovered as a byproduct during treatment of the silver ores, might contribute to the economic returns […]
Synthetic Zeolites Properties and Applications
Zeolites were first recognized as a new group of minerals by Cronstedt with the discovery of stilbite in 1756. The word zeolite was coined from the two Greek words meaning “to boil” and “a stone” because of the loss of water when heated in the mineralogist’s blow pipe. In 1845 it was discovered that certain […]
Shaft Kiln for Lime Production
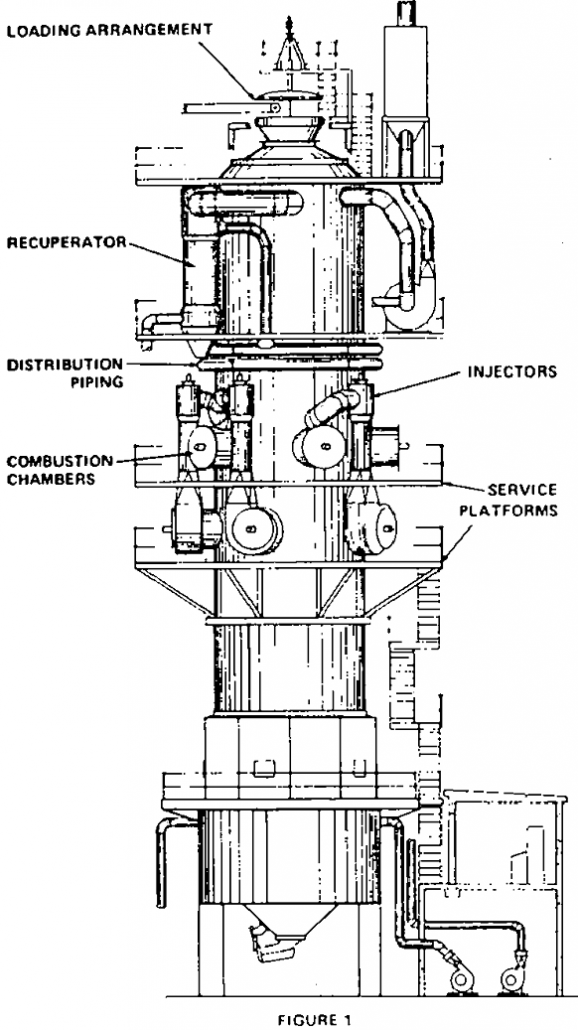
New is a relative term, and when used with reference to a concept as old as shaft kilns can be applied to a number of designs. In this case the design that is the subject of this paper, is known as the ring or annular shaft kiln as developed by Mr. Karl Beckenbach of West […]
Semi-Autogenous Liners
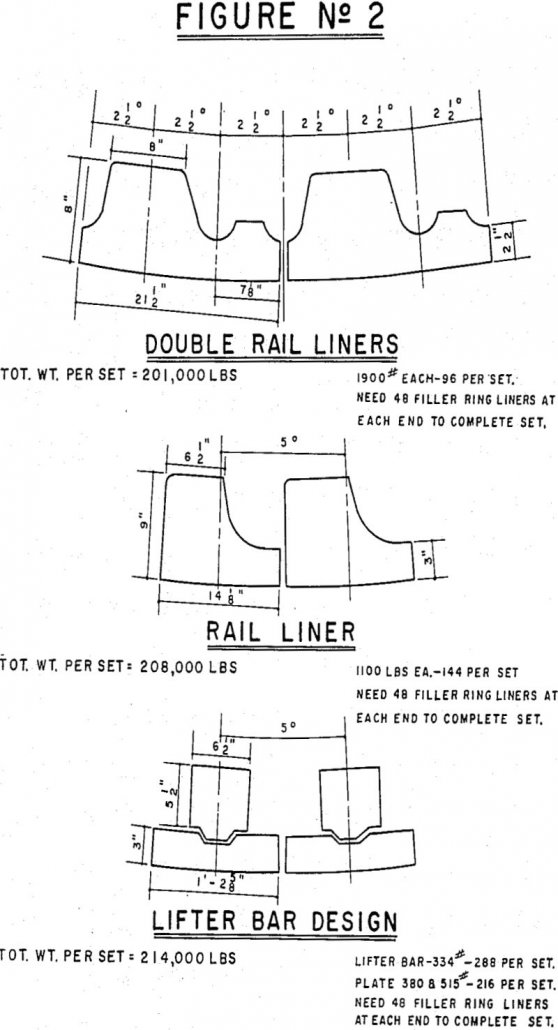
The never ending search for lower unit costs led Pima Mining Company’s management to study various alternatives shortly after Expansion III was completed. It soon became apparent that a considerable amount of ore assaying 0.35% copper had to be moved in order to maintain mill feed at the desired 0.54% copper content. New Mill Flowsheet […]
Remove Sulfur Dioxide from Off Gases of Coal Burning
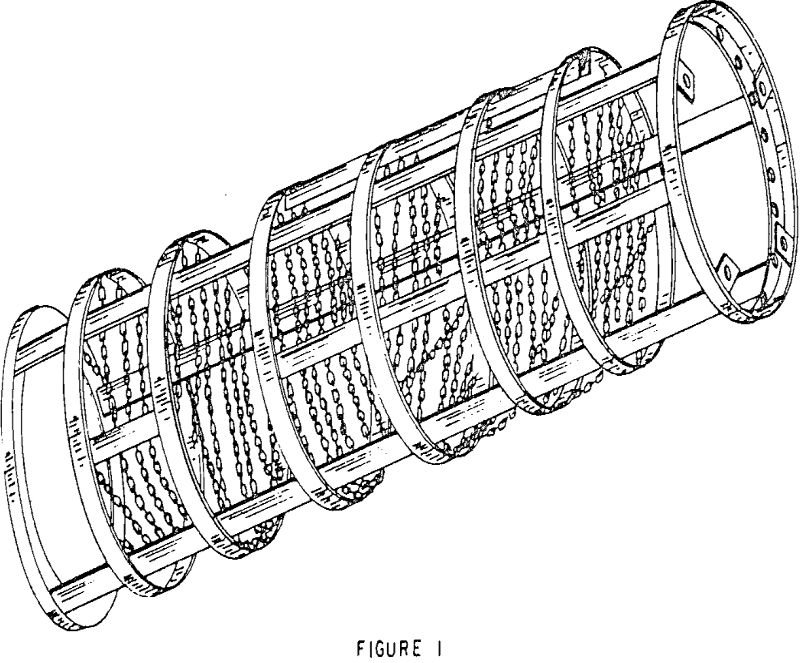
The purpose of this article is to present design information and operating data on a pilot gas scrubber which is believed to be a new approach for removing noxious gases and particulate matter from the off gases of coal burning power plants and smelters. In addition, gas scrubbers on stream or being developed for coal […]
Open Pit Equipment Selection and Maintenance
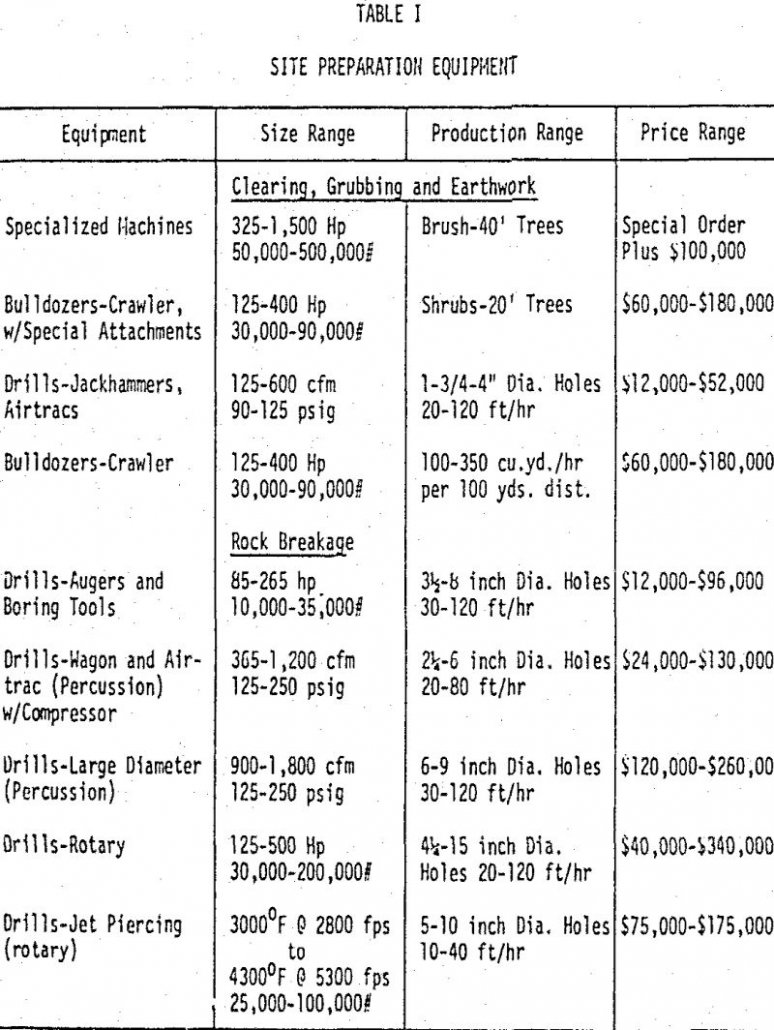
Principal factors influencing equipment selection can be grouped into five basic categories. Tonnage Requirements, Ore and Waste, Topography and Property Line Considerations, Ore Control Requirements, Physical Characteristics of Ore and Waste, and Climatic Conditions. Site Preparation Specialized Machines: This type of equipment generally operates on the principle of leverage uprooting and mechanical breakage of fallen vegetation. It is used in […]